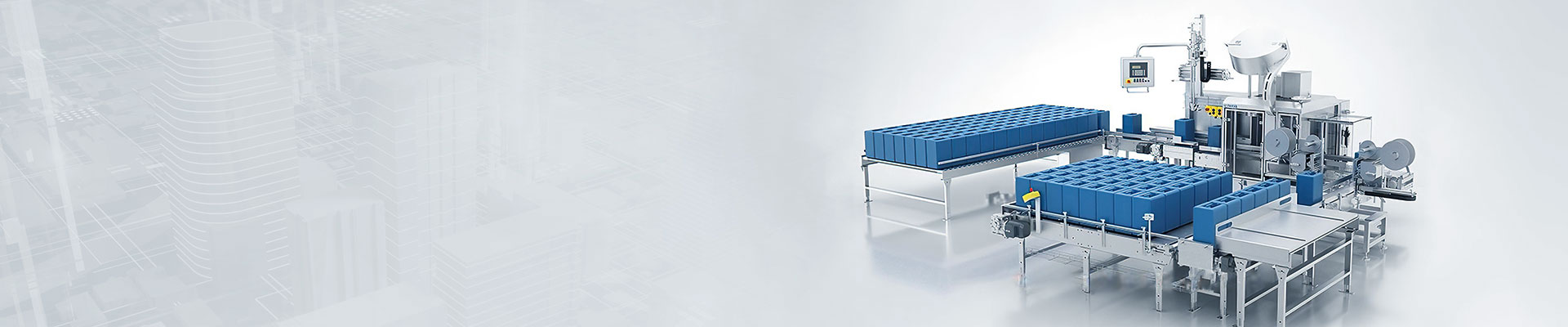
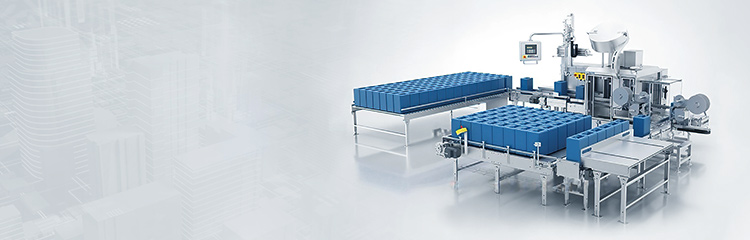
Dust-free weighing and feeding system is composed of mechanical weighing frame, feeding mechanism, stainless steel weighing module, speed sensor, weighing instrument, driving part, frequency converter, control cabinet and other main components, which is a production measurement equipment for manipulating feeding, dynamic measurement and continuous transportation of powdery materials. According to the pre-determined quality ratio, the weighing system is a balanced weighing system for dosage and measurement of several substances in the weighed material. Weighing system is divided into single tube single layer and double tube double layer, single tube single layer together with the completion of measurement and transportation, double tube double layer structure, the upper layer of the completion of flow stabilization and transportation, the grass-roots level of the completion of measurement and transportation, flow stabilization effect is better and save space.

Weighing control system is for a variety of solid silos, tanks, liquid tanks and other materials to implement continuous weighing, control of metering equipment, through the weighing and feeding, formula control, mixing and homogenization, material delivery and other processes, the use of microcomputer control and data management as one of the integrated automation system, the use of Mitsubishi or Siemens series of PLC and industrial control microcomputer to set up a high-performance control platform. For the design of a set of automation systems for production control, must achieve a stable and reliable operation, simple and practical operation, as well as superior cost-effective.
Feeding system is composed of mechanical weighing frame, feeding mechanism, stainless steel weighing module, speed sensor, weighing instrument, driving part, frequency converter, control cabinet and other main components, it is the production measurement equipment for powdery materials to manipulate feeding, dynamic measurement and continuous transportation. According to the pre-determined quality ratio, the Weighing system is a balanced weighing system for dosage and measurement of several substances in the weighed material. Weighing system is divided into single tube single layer and double tube double layer, single tube single layer together with the completion of measurement and transportation, double tube double layer structure, the upper layer of the completion of flow stabilization and transportation, the grass-roots level of the completion of measurement and transportation, flow stabilization effect is better and save space.
Adopt DCS control system, the whole system pneumatic, stop, run in the control room for control and monitoring; the overall equipment with fault detection system, the rear section of the equipment failure, the front section of the equipment with its own stop, and display the location of the fault point and the reason, with alarm lights to show the system operating status; the use of three-stage control, the weight signal from the material in the silo is transmitted to the microprocessor controller, which automatically calculates the material's actual The weight signal from the material in the silo is transmitted to the microprocessor controller, which automatically calculates the actual weight or height of the material. The weight or height of the material is converted into a 4-20MA signal. The upper and lower limit values of the material can be set to control the feeding and discharging equipments to keep the actual material within the set range.
Performance Characteristics
1、Full suspension direct weighing structure ensures accurate measurement and long-term stability.
2、Adopting high-precision digital weighing module, digital transmission, high resolution, no signal attenuation, strong anti-interference.
3, the controller adopts touch display technology, Chinese and English graphical display, intuitive display, simple operation.
4, can be connected to 485 communication, CAN communication, DCS, PLC and other interfaces.
5, GPRS wireless digital transmission function, you can SMS reports, remote diagnosis, calibration scale and other functions.
Technical indicators
Measurement accuracy: ≤ ± 0.5%
Measuring range: 0.001-1000T
Measurement method: weighing
Working mode: continuous or batch