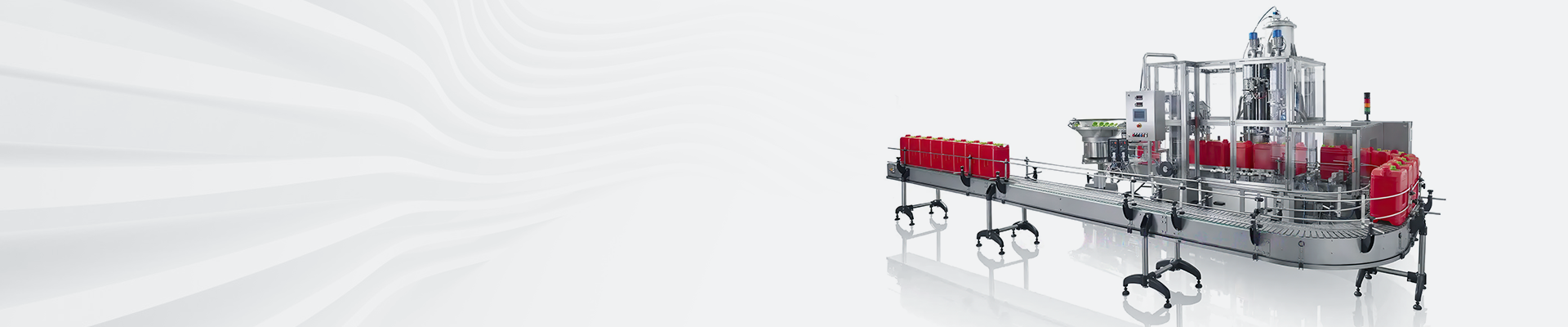
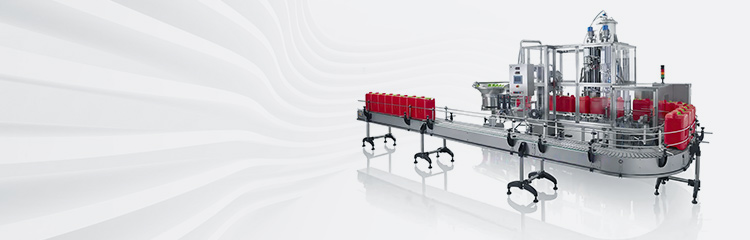

Summary:Aiming at the problems of large errors and instability in the aggregate weighing and batching machines of asphalt equipment, a double-opening aggregate weighing and batching machine with two cylinders and two solenoid valves was proposed. Practice has shown that this system has high accuracy, good stability, and simple structure.
January 1, 2005 began to implement the "highway asphalt pavement construction specifications" (JTGF40-2004, hereinafter referred to as the new specification) provides for intermittent asphalt mixer mineral gradation allowable deviation: sieve 0075mm for 2% of the sieve hole, sieve hole ≤ 2.36mm for 5% of the sieve hole > 4.75mm for 6% of the sieve hole. From the current domestic use of asphalt mixer, due to the improvement of the new specification requirements, the early 3000 series asphalt mixer in the aggregate weighing can not adapt to the new requirements, the later 4000 series of asphalt mixer has been improved, but in the stability of the system and the use of the maintenance of the system is not ideal. Therefore, the 3000 series asphalt mixer aggregate weighing batching machine to improve to adapt to the new specification requirements, but also for the 4000 type asphalt batching plant weighing control system for reference.
2 early 3000 series asphalt mixer aggregate weighing mixer of the basic structure and problems
Early 3000 series asphalt mixer aggregate weighing mixer basic structure, in this structure, due to the cylinder door closing process and aggregates fall to the weighing hopper on the existence of a certain delay, so it must be not weighed to the set value before a certain amount of advance to close the door of the hot material silo, after a certain time delay and then take the value of the weighing results. Early 3000 series asphalt mixer off the value of the warehouse in advance is generally used in the impulse automatic correction method 2, according to the last weighing of the warehouse off the value of the warehouse in advance and weighing error value to adjust the next weighing of the warehouse off the value of the value of the warehouse in advance, adjust the formula is as follows: the next weighing of the warehouse off the value of the warehouse in advance = the last weighing of the value of the value of the value of the value of the warehouse off the value of the value of the value of the value of the value of the last weighing of the value of the value of error.
Application practice shows that the general intermittent asphalt mixer must be completed in about 30s aggregate weighing time, in order to complete the weighing task in a certain period of time, the hot bin door must be opened large enough. But the larger the hot material silo door open, the ability to adapt to the hot material storage material changes and other destabilizing factors, the worse the ability, especially when there is a lack of material waiting, feeding fast and slow changes in production conditions, according to the last weighing error adjusted to the value of the closing position in advance of the next weighing conditions have been changed greatly and can not be applied at all, the system stability is very poor, the error is very large.
3 double cylinder double solenoid valve double opening degree aggregate weighing and batching machine basic structure, algorithm and advantages
Double cylinder double solenoid valve double open degree aggregate weighing batching machine two cylinders of the same diameter of a group of cylinders to control a silo door, cylinder stroke according to the characteristics of the silo and aggregates to choose, hook by a separate two-position five-way solenoid valve control. Two cylinders all open for the large degree of opening, a cylinder to open a cylinder closed for the small degree of opening, two cylinders all closed when the silo door closed. This system first to ensure that the weighing speed of large openings, and then turned to small openings to ensure weighing accuracy and system stability, while taking into account the weighing speed, weighing accuracy and system stability requirements, the system does not require high component, simple structure, easy maintenance.
4 double cylinder double solenoid valve double opening degree aggregate weighing and batching machine application effect actual production data sampling, from the record data can be seen in the bin closure advance value of most of the material in the waiting state of the ultra-low value, from the record after the bin material also appeared when more and less phenomenon, this situation at the same time affects the bin closure advance value of the larger fluctuations in the record of the weighing results are more stable, the error in the norms allowable range, indicating that the structure for the lack of material waiting, feeding and weighing, the system stability. Structure of the lack of material waiting, feeding fast and slow changes in production conditions such as strong adaptability.
Production applications show that the double cylinder double solenoid valve double opening degree batching machine can take into account the requirements of weighing speed and weighing accuracy. And the system stability is good.
5Summary
From the improvement process, the single degree weighing mechanism can not adapt to the complexity of the working conditions caused by the poor stability of the system is the root cause of the error, double cylinders and double solenoid valve double degree aggregate weighing and batching machine from the structure of the actuator and the algorithm of the control process of the two aspects of the simple and feasible way to improve the solution to the plagued asphalt equipment weighing and batching system design problem provides a new way of thinking. From the improved application point of view, the size of the opening of the conversion value selection is more critical, the opening of the conversion value is too large to affect the weighing speed, too small may not have a large opening to a small opening of the process into the original single-opening weighing structure, the current improvement of the system's opening of the conversion value is still based on the process of the field manually set up for further improvement can be considered to design a certain algorithm to automatically correct. From the above experience of aggregate weighing and batching machine improvement, it is also relatively easy to understand the filler and asphalt weighing errors and the reasons for instability. First of all, filler weighing screw conveyors are commonly used such as asynchronous motors, or asynchronous motors plus butterfly valves, or brake motors are subject to large errors and instability, the reason is that the filler due to moisture and other reasons caused by the transmission instability leads to the final stop weighing advance value can not be adapted to the