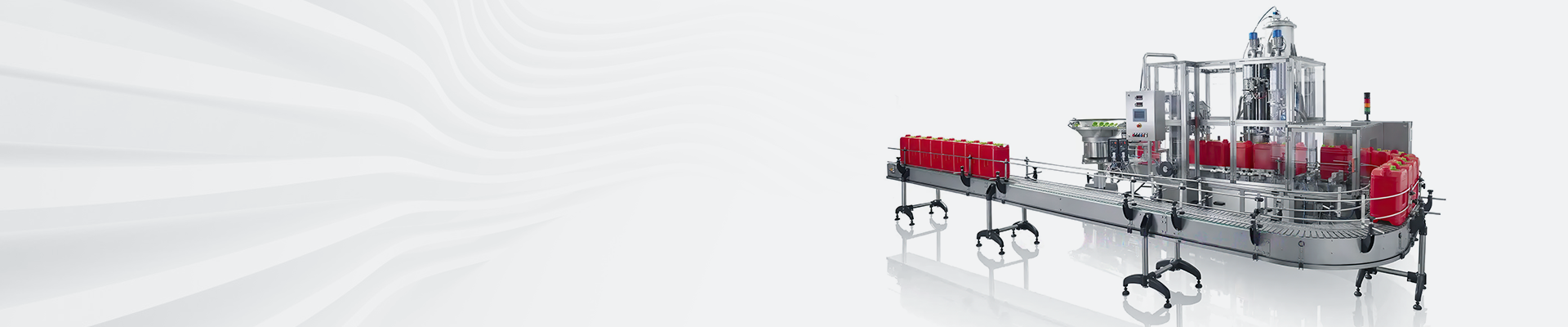
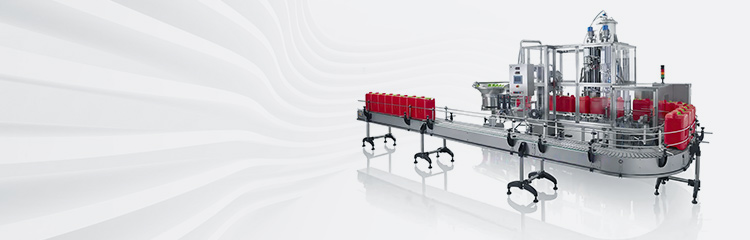

Summary:The batching system communicates with the host computer through the spiral frequency conversion control through the weighing instrument, and is connected to form an on-site communication control system.Calculate the ingredients of the mixed raw materials according to the mixing requirements of the reactor and the chemical composition of each material, determine the proportion of each material, and implement the ingredients through weight detection.
Adopting the centralized control mode based on the communication of on-site weighing instrument.
The screw, plate flowmeter, radar level meter, intelligent regulator, etc. are connected with the upper computer through the weighing instrument with field communication function, forming a centralized system based on field communication.
The on-site weighing instrument communication adopts the HART communication protocol based on the principle of master-slave protocol. The communication is characterized by only two commands for reading and writing, the upper computer software is easy to write, and the PC can be used as the upper computer, applying its rich software resources, and the advantage of very fast development. Compared with analog transmission, it has the advantages of easy debugging and maintenance and higher accuracy.
The dosage has the following advantages:
High reliability
The automatic dosage system adopts photoelectric isolation technology to isolate the communication interface from other parts of the weighing instrument line. When the communication interface or line fails, the screw and regulator can still work normally. Due to the use of low-level digital signals and phase continuous average value is zero, anti-interference ability is strong. Simple wiring, easy maintenance, accurate data transmission. Failure between single machine detection and control does not spread, failure between the upper and lower computer does not spread, the impact of failure on the entire dosage is minimized, greatly improving the reliability of dosage. Manual and automatic conversion methods are flexible and diversified. It can be converted in the upper computer, in the basic regulator, and also in the frequency converter and operation box, which solves the problem of slow emergency response in case of failure.
Strong data processing capability of the upper computer and richer monitoring program functions
As the data is collected by communication, and some statistical data of the stand-alone machine is completed by the lower computer, the upper computer mainly processes the dosage data, which frees up more time and memory to process the application programs with richer functions.
Investment saving
The upper computer does not need analog input/output modules and corresponding panel cabinets, and also eliminates the need for a hot standby upper computer. At the same time, when adding a single machine, there is no need to add a public part of the hardware, saving expansion costs. In addition, save signal cable and installation and commissioning costs. Also on the use and maintenance of low quality requirements of personnel, saving training costs.
Advanced and practical, small maintenance workload
For the general spiral maintenance workload, anti-interference ability is poor, the choice of maintenance-free, weighing millivolt signal on-site digitization and become 4-20mA signal.
Selection of advanced and practical punching plate detection
General spiral detection, two spiral detection of a material point, are unstable, maintenance workload, low precision, high investment. Choose the advanced and practical punching plate detection. The differential amplifier is replaced by high-precision stainless steel weighing module, which not only improves the stability and detection accuracy, but also reduces the maintenance workload and technical requirements. At the same time, the use of ceramic wear-resistant punch plate to solve the problem of short life of steel punch plate. In addition, its flow signal is processed by spiral alloy steel weighing module, which solves the problem of matching with the upper computer.
Selection of advanced intelligent regulator
Whether it can realize high-precision automatic adjustment, the correct choice of regulator is the key. This system uses an intelligent regulator with on-site communication function and fuzzy rules for PID regulation. The improved PID algorithm is used for regulation. It has a variety of setting methods, which can be set manually and digitally directly on its panel buttons, and can also be set analogically on its external given terminals. In order to prevent abnormal overshooting, it also has the function of presetting the upper and lower control limits. At the same time, debugging is simple and has little impact on normal production. The structure type is hot-drawing and inserting type, which is convenient and quick to replace.
Selection of advanced radar level meter detection bin material level
The traditional ways of detecting the material level of the warehouse are weighing type, heavy hammer type and manual measuring tape, which are difficult to maintain and the maintenance workload is large and unreliable. Choose accurate, reliable, maintenance-free radar level meter detection.
The application program is novel, practical and rich in functions
The system application program is written in VB6.0 with good visualization performance. Compared with the general dosage monitoring program, this dosage monitoring program has more novel, practical and rich functions, and has strong man-machine dialogue ability, which is highlighted as follows:
Alarm mode adopts over-difference and inverse time limit voice alarm
Most of the traditional alarms are sound and light alarms for instantaneous quantity or long-term continuous accumulation quantity. Due to the limitations of the feeding method (uneven feeding) instantaneous amount of alarm either frequent false alarms (too late to deal with the recovery); or overshooting the alarm (large deviation) and leakage alarm. Continuous cumulative amount of alarm, but also due to the accumulation of time is too short or too long and false alarms and missed alarms. At the same time, the alarm object should be confirmed with the monitor screen. Adoption of over-difference inverse time alarm. That is, a certain amount of accumulation (absolute error) and time interval (minimum processing time) for the alarm conditions, the instantaneous amount of error continuously accumulated and transmitted to the host computer in a communication mode, the greater the cumulative amount of time per unit of time, the shorter the alarm time limit, and vice versa, the longer the alarm time limit. At the same time, the instantaneous amount of deviation is too large when the direct alarm. This is neither false alarm nor omission. In addition, the use of voice broadcasting dosage system, automatic direct reporting of the alarm object and prompt the reason and processing measures. This not only shortens the alarm confirmation and processing time, but also reduces the fatigue of operators by eliminating the need for them to stare at the screen.
Solve the problem of batch control
In order to realize the batch control of variable materials in traditional metering and batching, the upper computer and the regulator are analog setting, and the hardware structure is complicated. We use in the host computer preset variable material value, to field communication to change the regulator set value, according to the principle of material head material tail alignment automatically sent, variable material time is short, the longest time is only 90 seconds (only by the mixing material screw machine speed and bin spacing decision), regulator does not overshooting, reduce due to variable material fluctuations brought about by the malignant material change and production instability problems. There is also no need to interlock with the electrics when slowing down the material.
Realization of manual and automatic rapid switching without disturbance
The traditional hand and automatic non-disturbance fast switching refers to the instantaneous output value of hand and automatic is equal at the switching moment. And in the dosage automatic regulation, hand, automatic non-disturbance fast switching requirements are switching before and after the average value of the control quantity or controlled quantity is equal, which must be calculated before switching the average value of the control quantity or controlled quantity, and then switching, in order to achieve the smallest possible impact on the process, the real realization of the hand, automatic non-disturbance switching. Obviously, the traditional sense of the instantaneous amount of manual and automatic non-perturbative fast switching does not apply to this. Therefore, the use of on-site communication in the manual to automatic switching, the first in the host computer tracking calculation of the average value of the amount of controlled per minute at that time; this value as a given value at the beginning of the automatic; in the automatic to manual switching, the first in the host computer tracking calculation of the average value of the amount of control per minute at that time, this value as a manual control value at the beginning of the control value. Then set to the artificial intelligence regulator, and finally carry out the average value of the hand, automatic non-perturbative fast switching. Realize a conversion success, solved the previous hand ﹑ automatic switching, must be carried out many times to modify the control volume or set value, is still difficult to achieve the switching requirements of the value, resulting in production fluctuations and prolong the time to reach stability of the problem.
Automatic correction of the original set value of the corresponding regulator
According to the amount of zero change and accuracy change before and after the calibration, the new set value corresponding to the original set value is calculated automatically to ensure that the new set value and the original set value are equal in physical quantity, which avoids the additional error caused by the calibration of zero and calibration, and maintains the continuity of production. The general solvent dosage system does not have this function.
It realizes the automatic recording and time inquiry of over-difference, changing warehouse, breaking, changing and slowing material, which solves the problem of real-time supervision of process discipline in the dosage process.
When the above alarm occurs, the monitor automatically pops up a dialog box with the contents of alarm object, alarm reason, treatment method and duty person, etc., and the duty person confirms each item. It clarifies the responsibility, strengthens the self-discipline of operators, lays the foundation for correctly analyzing the cause of fluctuation, and is conducive to the stable improvement of process technology level.
Historical trend graph vertical coordinate divided into two proportional segments, to ensure that the size of the flow in the same screen are clearly distinguishable instantaneous volume change trend. In the upper computer monitor centralized view, modify the parameters of the explosion-proof weighbridge, school explosion-proof electronic weighbridge convenient. Silo level virtual indication of the initial amount of material minus the amount of material for the remaining amount, without the need for level meters can also be more accurate indication of material level. Data packaged in an error-free way to remote transmission of dosage information, and can be queried off-site, the realization of the dosage information sharing, improve the level of process management. Flexible and diversified ratio setting. It can either automatically calculate the set amount after inputting the relevant ingredients and total amount according to the formula of process batching, or manually calculate and input the set value one by one; it can be preset uniformly according to the requirements of batch control on the upper computer, or set separately on each basic regulator. The history statistics of the stand-alone machine are stored in its corresponding module, saving the time and memory of the host computer and increasing the expansion margin of the dosage system. The unit of measurement can be interchanged between t/h and kg/m, which is convenient for on-site verification. The display screen is equipped with a help menu, which is convenient for operators and maintenance personnel to learn and master.
The effect of two years of operation has shown that
The dosing work is stable and reliable, reducing the labor intensity of operators and maintenance personnel. Due to the automatic detection and adjustment, it greatly reduces the manual running plate weighing, and can spare more time for inspection, timely detection and treatment of hidden danger, which reduces the workload of sudden accidents and their treatment. At the same time, the alarm is accurate and timely, also reduces the interference and the workload of dealing with faults. In particular, the change of material and manual and automatic conversion in one place, not only to enhance the real-time control, improve the accuracy of control, but also to reduce the labor intensity of repeated weighing. The man-machine interface is intuitive, the function operation is simple, and there is also a help menu, convenient and easy to learn. The monitoring program has strong man-machine dialogue capability, which is convenient for process management, improves the responsibility of operators, reduces abnormal fluctuations and promotes the improvement of production indexes.
The dosage system realizes continuously adjustable control stability and ±1.5% accuracy of cumulative quantity control per minute under disc feeding mode. It meets the process requirements of variable and slow material, manual and automatic switching, smooth transition before and after calibration of explosion-proof weighbridge, and accurate and timely remote transmission of dosage information. The application program functions of measurement, control, management in one, to achieve the goal of high performance to investment ratio.
Problems and improvement measures
Slow communication speed. Further improve the function of the lower computer, so that the data taken by the upper computer can be counted and stored in the designated storage unit as far as possible in the lower computer. At the same time, use data compression technology to reduce the amount of data transmission and shorten the communication time. In addition, improve the communication baud rate.
The feeding system is not uniform. Further change the feeding method, the disk feeding all changed to wide screw drag material.
Difficulty of physical calibration. Add a mobile hopper at the screw machine's drop point, so that the physical calibration can be done at any time.
Separation of instrumentation control and electric control. Combine the instrumentation control with electric control and adopt A7-301M switching input/output module to realize fully automatic dosage and dosage information into the production management information network.