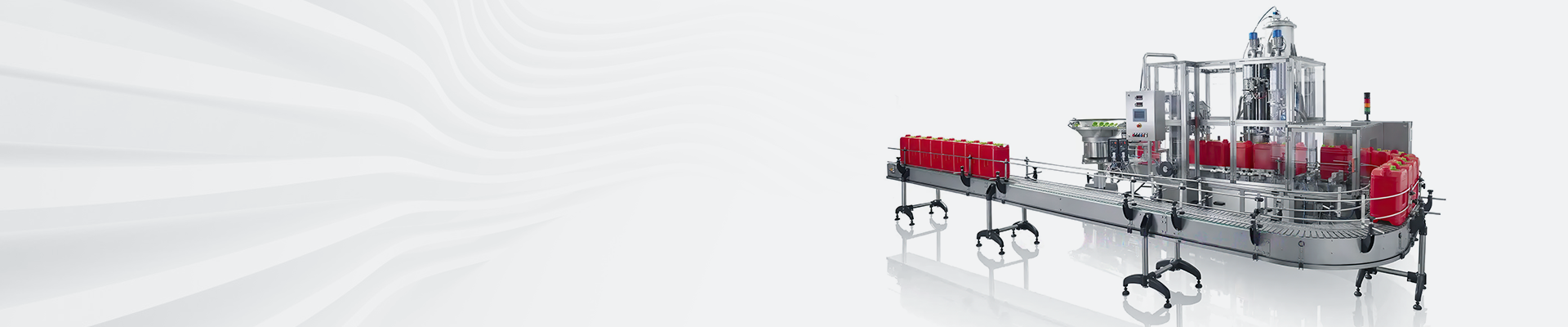
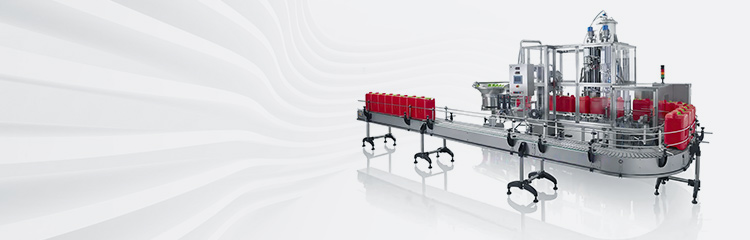

Summary:The automatic batching system can complete on-site batching control and formula weight collection through the multi-material function of the touch screen, and set the formula for multi-batch batching and transportation.Upload relevant production information to the data server ERP through the communication interface to realize information sharing.
In the field of production, the proportioning accuracy between various raw materials has an important impact on the stability of the production process and the quality and yield of the product batching machine is widely used in metallurgy, building materials, chemical and food industries. In recent years with the rapid development of computer technology and PLC technology, the configuration software at home and abroad continues to improve, and the automatic batching system control program is also improving.7 At present, in the field of automation control, PLC is an important control device.
1 Complex solid material dosage demand
Batching systems for solid materials are mostly applied to powdered materials. Powdery material uniformity is relatively good, easy to control, and most of them are in a quantitative way, this dosage system requires large hoppers or silos, and multiple crushers to pulverize the material in advance. In some small and medium-sized enterprises, due to the enterprise's capital, plant and technical conditions of the limitations of a variety of particles or small pieces of material can not be crushed separately to powder, but requires online matching, together with the crusher for crushing. This saves the crusher and reduces the investment cost of the enterprise. This paper provides a complex solid material automatic dosage system can be applied to both powdered materials, but also can be applied to particles or small pieces of material online automatic dosage.
2 complex solid material feeding system process design
The following two solid materials as an example to introduce this automatic dosage system.
The structure of the dosing system is relatively simple, mainly composed of silo, feeding control device, belt scale, conveyor belt.
The silo is filled with powdered or granular or small pieces of solid material due to the silo around the slope design, the material will automatically slide down to the feed control device. The feeding control device is actually a conveyor belt driven by a three-phase motor, with fixed baffles on both sides and one end to prevent the material from slipping. The motor drives the conveyor belt to feed the material onto the belt scale. The belt scale is an electronic belt scale, which can weigh the weight of the material on the belt scale, and the belt scale pours the material onto the conveyor belt at a certain speed. Finally, the conveyor belt sends the two materials to the crusher for crushing and mixing.
The feeding size of the feeding control device is determined by the speed of the driving motor, which is controlled by the frequency converter, and the frequency converter is regulated by the analog signal output from the PLC. Ultimately, the feeding control device feeding size is determined by the PLC output analog signal size of the belt scale motor after the speed reducer, rotating at a fixed speed. Therefore, the material on the belt scale is basically a low-speed, uniform speed movement.
3 control system design
Dosing control system is mainly composed of PLC and touch screen and then software system development to realize the automatic dosing of materials.
Control system PLC using Siemens CPU226 plus analog input and output modules, touch screen is also used Siemens TP177B detection (or monitoring) signals: belt scale weight signal (analog) feeding control device motor status signal (digital); belt motor status signal (digital); motor overcurrent signal. Control output signals: feed control device motor speed control signal (analog); feed control device motor control signal (digital); belt scale motor control signal (digital).
The control system can detect the weight signal of the belt scale to measure the material, and at the same time, it can control the size of the feeding quantity by adjusting the output analog quantity. The system also provides an alarm function to warn and automatically process when the motor overcurrent or does not meet the dosage requirements. This system is equipped with a communication module (CP243), can be incorporated into the computer system.
4 Software system design
This system is mainly composed of PLC software and touch screen software. The PLC system is based on Siemens SIEMENS programming software STEP7MicroWIN4.0 program development, touch screen using WinCCflexible2008 for configuration PLC software program to complete all the detection and monitoring, and data calculation and processing, the use of fuzzy control to regulate the amount of feed and so on. The touch screen program is mainly image configuration, provide human-computer data exchange interface for the operator to operate, data settings, data observation.
5 Principle of operation
5.1 Weighing principle
Due to the complexity of the material, the weight of the feed is very uneven hook, coupled with the irregular impact of granular or lumpy materials falling, the belt scale data is also a messy change, no regularity. If the establishment of weight and time Li number, will be a complex multi-order function, in the calculation of instantaneous and cumulative are more complex.
Here to provide a simple measurement method, that is, in the movement of the first static measurement of the effective length of the belt scale, that is, the material falls to the belt scale to leave the belt kind of fall into the conveyor belt time, for example, 15S, feeding control device feeding time control in 13S, that is, there is a 2S interval of 2S does not feed time to ensure that each section (within 13S) to feed the material is not connected to the boundaries of a clear, at the same time in the 2S, the belt scale No feeding, no impact, relatively stationary state, the weight signal is stable, you can take the value of the measurement, so the measurement is more accurate.
5.2 Feeding control principle
Because of the use of segmental feeding, segmental weighting, can not be adjusted using PIDD, so the system's feeding control is to use fuzzy control, cycle replenishment.
First of all, according to the output requirements and the ratio of each belt, calculate the amount of each feeding, combined with the fuzzy control rule table, select the appropriate control feeding speed (feeding control device motor speed). Each time the weight counting and the required feeding volume P for comparison, if the difference value is D (positive value indicates overload negative value indicates underload), then the next required feeding value P1 = P + D. Pl value combined with the fuzzy control rule table in the selection of the appropriate control feeding speed for this feeding control.
To 5 times for a cycle, 5 times after the completion of the replenishment. That is, according to the ratio value and the actual feeding value of 5 times, to see which material is not enough. Not enough to make up for the amount of material, and enough material to stop feeding. In this way to ensure that in a cycle of various materials in accordance with the formula to realize the automatic distribution of Lou.
In addition, due to the humidity of the material and other reasons, the belt scale may stick to the material and cause the zero tare value changes, which will lead to the measurement time is not given to the material. In this way, the material of the belt scale macro is fed at intervals of 13 S, with an interval of 2 S. The system needs to clear the tare once a cycle, i.e., periodically adjusting the base value of the signal of the belt scale when the measurement is zero.
6 Conclusion
The complete set of automatic dosing system developed for complex solid materials has been successfully applied to the brick industry after a trial in a brick-making enterprise in Jiangxi, and through the improvement of the popularization and application in a number of enterprises in the country. The system solves the automatic batching of granular, especially blocky materials, and can be applied to powder materials such as cement batching, batching effect is also better.