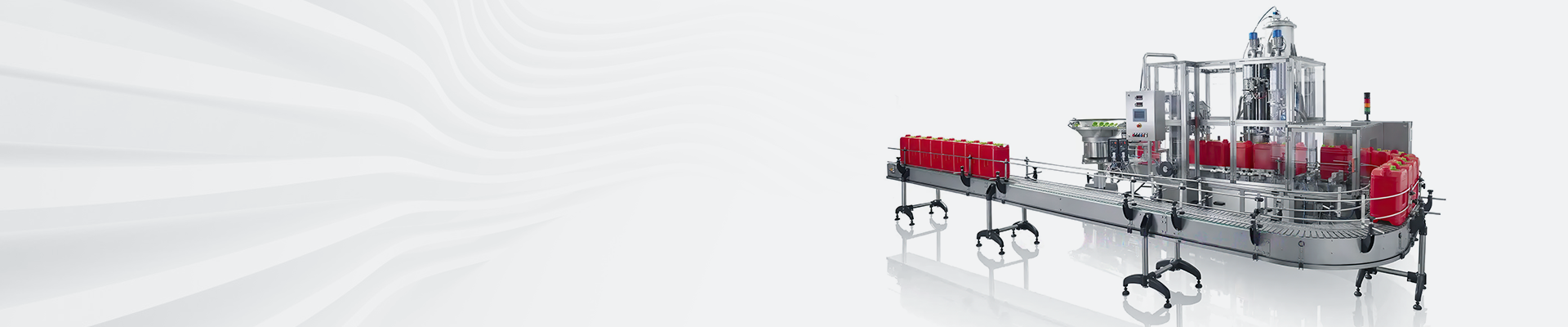
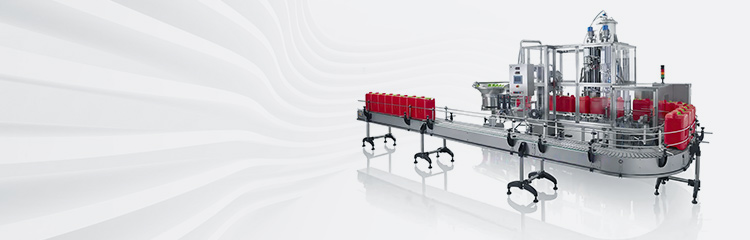

Summary:The dosing control system slowly adds solid reactants under constant stirring and mixing to keep them reacting or dissolving so as to avoid precipitation. Completion of the chemical reaction process, accompanied by mixing, heat transfer, and drive device made of the original. By Siemenss7-400PLC, Simaticwincc6.0 configuration monitoring software, to realize the automatic control of the sintering production line, since the commissioning of the system, the system has been running stably.
1 Introduction
The batching production line is completed and put into operation, which consists of batching system, sintering machine, screening system, ignition furnace, belt conveyor and finished ore bin. The whole sintering production line adopts Siemens S7-400 to form a control system, which meets the requirements of the production process and realizes automatic computer control.
2 Hardware composition
The network structure of the feeding system adopts Advantech upper SiemensS7-400PLC two-stage control system, the PLC system CPU adopts CPU414-2DP, each sub-station and the master station adopts Profibus-DP, the communication template selects CP443-1 communication module, and the remote I/0 station adopts ET200M, which is stable and cost-saving. The upper monitoring software selects Wincc6.0 of Siemens. PLC realizes the control requirements through PROFIBUS-DP network with remote I/0 station and frequency converter.
3.Network structure
This feeding system is a distributed control based on Profibus field bus. The lowest layer of the system is the equipment control layer, which mainly completes the on-site control and monitoring of the equipment, and the second layer is the monitoring layer, which mainly completes the on-line monitoring of the sintering system and sends control commands to the control layer. The master station communicates with the ET200M remote racks of batching, mixing and screening through the PROFIBUS-DP network, which is one of the international common fieldbus standards recently, and has become the most important fieldbus standard with its unique technical characteristics, strict certification specifications, open standards, the support of many vendors, and the evolving application line rules. Stability of communication is guaranteed. In the main control room, there are TV monitoring station and operator workstation, through the operator station to give production instructions to realize the automatic control of the sintering system.
4 Control Functions
The main control functions of the feeding system include the setting of the main process parameters, chain start/stop of the equipment, browsing and inquiry of the main process parameters, etc. The PLC sends the collected status of the equipment, material flow rate, and bin level to the ICP via Ethernet to be displayed, which is convenient for the control of the production process. At the same time, Simaticwincc6.0 will save the actual speed of each motor, current signals, the amount of material in the dosage bin, bin level signals of the data to save the history, which is conducive to the equipment, the cause of production failure query.
4.1 Automatic batching system
Measuring and batching system is the core part of producing sintered ore, which requires high precision reliability and confidentiality of batching. The automatic batching system adopts the mass batching method, where all kinds of iron-containing, carbon and silicon are dosed by weighing equipment according to the ratios inputted by the operator. The accuracy of batching directly affects the stability of sinter content, so it puts high requirements on the control system.
The batching control system is mainly composed of PLC, feeding device, weighing device, frequency converter and so on. The operator inputs the chemical composition and proportion of various raw materials through the operator station, and the flow signal is converted into 4~20mA signal by weighing equipment and weight indicator, which is input to the function module, compared with the set value, and then transmitted to the frequency converter through Profibus-DP bus through the PID operation of FB41 continuous control block, and the resulting control word is transmitted to the frequency converter, and the frequency converter controls the rotational speed of the motor of the feeding device according to the signal, so as to make the feeding device motors rotate at the same time, and then make the feeder motors rotate at the same speed. According to this signal, the frequency converter controls the rotating speed of the motor of the feeding device, so that the feeding quantity of each feeding device fluctuates slightly above and below the set value, realizing the function of automatic dosage. The PID algorithm is as follows: Y(t) is the set value of the feeding quantity at the moment of t, Y(t) is the deviation of the feeding quantity at the moment of t, and the control output of the control system at this time is u(t), u(t)=Kpfe(t)+I/]ife(t)dt+Td[de(t)/dt]}, of which K "Ti, 1ld, are the proportionality coefficients, the integral time constant, the differential time constant, the three coefficients can be adjusted to change the control time constant, and the control time constant can be changed by adjusting these three factors. The control output can be changed by adjusting these three coefficients to achieve a better control effect.