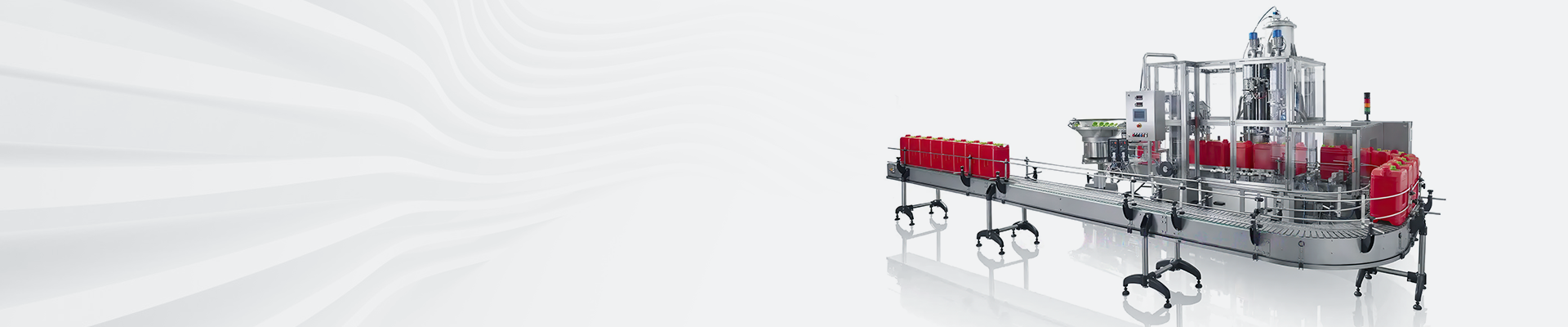
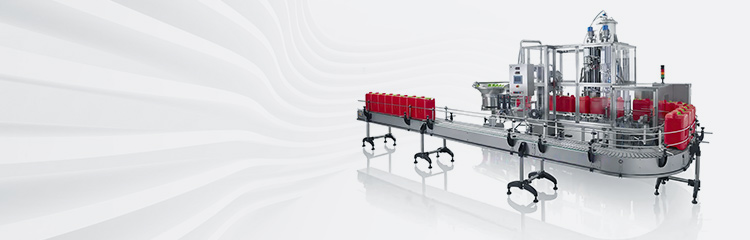

Summary:Batching system to achieve multi-level control and automatic control, according to the process areas in a certain proportion of mixed materials, batch processing joint network, more open (strengthen the division of labor), standardization, productization, integration.
1 System Overview
Batching system to promote the optimization and upgrading of industrial structure, information technology to change the traditional industry, is to promote the integration of the basic cause, widely known. With the leaping development of ICT technology, the industrial automatic dosage system and electronic scale technology is developing rapidly, presenting the characteristics of miniaturization, digitalization, intelligence, network, integration and so on. The system consists of two DEIL dual-core computers, a set of Siemens S7-300 series programmable controllers, as well as five dosage (weighing) instrumentation and four temperature control instrumentation, external printer. See the system configuration diagram (four temperature-controlled meter in the figure is not drawn). The temperature control meter is connected to the analog input module of PLC, the weighing meter is connected to the analog input module of PLC, the computer communicates with PLC through the MPI port of PLC, and the data sharing between two computers is realized through HUB (8D-LINK). In addition, the PLC has a total of 224 points of switching inputs, 288 points of switching outputs, 24 analog inputs and outputs to achieve and the first floor of the outdoor raw material field control box remote I0 terminal data exchange). Two DELL computers running Siemens WINCC monitoring software, through their respective communication ports and programmable controllers communicate with the two communication ports, can be run independently, play the role of mutual backup, greatly improving the reliability of the system. The monitoring software can dynamically display the process flow of the whole production process, display the operation, fault and alarm status of each equipment, display process parameters such as temperature, pressure, etc., and set the alarm value, timing parameters, dosage (weighing) instrument parameters, etc. The monitoring software can also switch the system's manual control. The monitoring software can also switch the manual and automatic operation mode of the system, and in the manual mode, it can manually operate the main motors and valves of the system. All operations and parameter settings are password-protected and have operator records (manual mode of operation must be entered with the appropriate access rights).
The system also records the weight data of various materials, which are saved in the data, and produces reports such as shift reports, daily reports and monthly reports based on these data. Moreover, the system also carries out real-time monitoring of the mixing temperature of the high-cooling mixing machine and the temperature of the pot wall, and has real-time curve tracking to monitor the real-time temperature of the material and the pot wall as well as historical curve querying the historical temperature.
Programmable controller in addition to complete the logic control of the entire production line, but also with six weighing instruments and ten temperature control instrument for communication, in addition to reading each time the weight of the data, but also to set the working parameters of each instrument to achieve remote monitoring. Due to the use of Siemens S7-300 programmable controller, the PLC is not only very fast (the fastest instruction 0.75 microseconds), but also supports structured programming, according to the process can be compiled as many as 254 programs, and support for more than one person at the same time debugging, is very convenient for system development and operation and maintenance.
2 process
The dosing system mainly consists of a computer (server, engineer workstation, each production workstation), the main module (including digital and analog modules), electronic scales, control station, field measurement module, field touch screen button box. The equipment is an optimized combination of advanced control concepts that effectively ensures computerized data management, dynamometer weight marking, control of production modes, management of the metering automatic dosage system software using HPS, comprehensive production testing and safety management, as well as safe operation of the equipment. When starting dosage, the automatic dosage system supplies the dosage according to the set recipe parameters and production sequence. The host computer displays the dosage status which can be viewed on the computer in a number of interfaces, including the main interface, the main reaction sub-interface, the temperature profile interface and so on. After running, the dosage supplies materials according to the target weight and material sequence set on the host computer, and the corresponding valves will be opened automatically when measuring. After reaching the set target quantity, the valves will be closed automatically. In order to better control the metering accuracy, the low rotation value can be set on the computer and the discharge valve can be closed beforehand, so as to reduce the influence of the discharge weight on the metering. The electronic scale is transmitted to the main control module at the same time, to the host computer, and the electronic scale automatically enters the next measurement. Electrical automatic dosage system mainly consists of weighing device and control device. In the measurement unit, most of the weight stabilized by the weight, debugging is relatively complex, low cost, simple function of the measurement of the sensor and controller electrical components control.
Users have direct access to the PLC system, the final system for multi-level control and automation. In dosage jobs, one goal is to eliminate errors and accurate historical data from the workflow, and another is to utilize the data more efficiently. Batching operations and collection of information are automatically logged to minimize user error and maintain actual results. This comprehensive and complete information management monitoring platform enables fast and efficient tracking of material processes, from raw material inputs, to automated material control, to supply chain-wide management, thus maximizing the elimination of safety risks.
3 Monitoring Software
The system uses the world's most famous industrial control software provider Siemens MMI software WINCC, the software is powerful, easy to learn, stable and reliable, the computer is on, the monitoring software runs automatically, and automatically into the main menu screen, from the main menu can be seen, the system is divided into four main screens: process flow screen, parameter settings, centralized control, trend curve and reports, in addition, in the clock In addition, above the clock, there is the total pressure of the gas circuit and the cooling water temperature of the digital plant display. In addition, in the process flow screen there are: the main material feeding unit, dosage unit, vacuum feeding unit, mixing unit, finished material unit, program, pulse valve parameter setting, weighing instrument parameter setting, temperature alarm limit setting, motor current display, valve summary control, temperature alarm curve, 3 performance features
WINCC software after a complete test and run the test, high reliability and stability, maximum openness, WINCC's operating environment is WIN98/2000/XP, so many WIN9812000/XP run under the software can be directly communicated with the WINCC, the network function, WINCC support for a variety of Microsoft's network, the network is very simple, the database function, WINCC in addition to its own parameters of the pulse valve set, the motor current display, the valve summary control, temperature alarm curve. Database function, WINCC in addition to its own database, but also supports the SOL language, you can easily connect with other databases, WINCC provides a variety of powerful features, through the configuration can meet the user in the operation, display, record a variety of special requirements. Through the transformation, this system can upload the industrial process parameters, cost parameters, repair parameters, etc. to the management platform and auxiliary decision-making platform in real time through the Tianye informatization bus, and at the same time, it improves the level of enterprise automation and control, enhances the stability and reliability of the production, and greatly improves the competitiveness of the enterprise in the market.