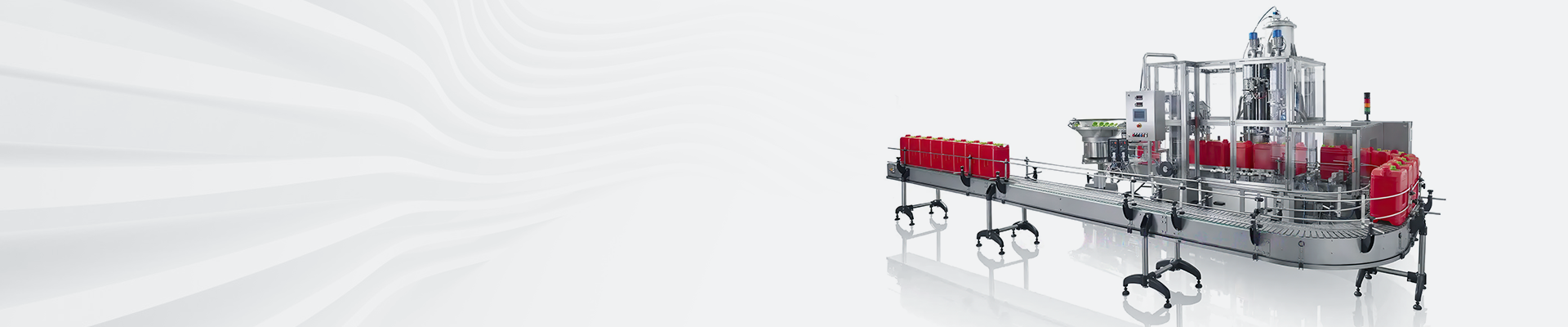
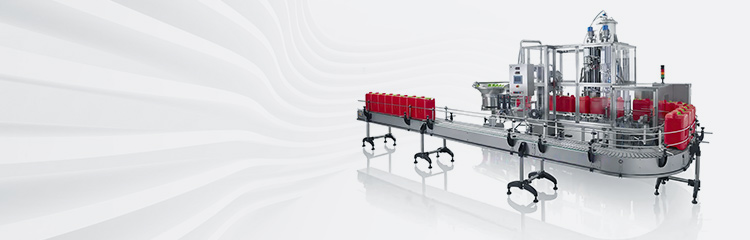

Summary:Liquid filling machine in turn to complete: barrel, barrel, feeding, feeding, filling, barrel, capping, sealing, palletizing and other steps, the use of PLC to do the main control elements, photoelectric and proximity switches and other detection of the load cell as an external input signal, servo motors, action cylinders and so on, as the output components.
1 System program design
Filling machine in the automatic control system hardware including microcontroller, weight detection circuit, linear amplification circuit, A/D conversion circuit, display, keyboard and some other circuits and other components. Filling machine is usually an automatic weighing and dosing system as the main control unit is through the microcontroller filling system design. Generally speaking, the filling equipment selection of single-chip control from the cost of the product, filling machinery occupies space and other aspects of this is the best choice. Liquid filling machine through the investigation of the market variety of microcontrollers have a variety of microcontrollers can complete the required functions. Filling device selected by the microcontroller is a new generation of microcontroller STC90C516RD launched by Hongjing Technology. Quantitative filling machine this microcontroller low cost, excellent performance, liquid filling machine with the same has a super anti-static, quantitative filling machine super anti-jamming ability, low power consumption, high speed and reliable operation. Automatic filling machine system requirements with the production data (industrial output capacity, production batch number, etc.) uploaded to the PC function, automatic filling machine at the same time you can view the instantaneous production rate, the number of filled and so on.
1.1 Process Flow
After the liquid filling machine is turned on for automatic filling, the filling conveyor starts to run. The main control system of the weighing and filling machine adopts PLC as the main control element, the photoelectric and proximity switches and other detection load cells of the quantitative weighing and filling machine as the external input signals, and servo motors and action cylinders as the output elements. At the same time, the automatic filling machine production line has a product online real-time monitoring function, and has the product information entry function, the computer is connected to the PLC liquid quantitative filling machine through serial communication, explosion-proof filling machine can collect data in real time and can carry out the production line data processing and data entry, preservation. Multi-mixed explosion-proof liquid filling machine control functions are realized with hardware relays. Quantitative liquid filling machine relays are connected in series in the control circuit according to the main circuit in the voltage, current, speed, time and temperature and other parametric changes in action, multi-mixed weighing liquid filling machine to realize the automatic control and protection of electric power dragging device. The system is complex, in the control process, mixing tank weighing automatic filling machine if a relay is damaged, will affect the normal operation of the entire liquid automatic filling machine weighing system weighing module, find and troubleshooting is often very difficult, although the price of the relay itself is not too expensive, but the installation of the control cabinet wiring workload is large, so the entire control cabinet is very high, poor flexibility, slow response time. Automatic liquid filling machine filling packaging barrels in the filling machine in order to complete: on the barrel, into the barrel, feeding, feeding, filling, out of the barrel, capping, sealing, palletizing and other 9 steps. Normal operation, liquid filling equipment to meet the interlock switch closure, air pressure conditions, liquid level conditions, such as external transmission number normal, the equipment in the press start switch, automatic filling equipment should be in automatic operation mode, filling line of each station will be in accordance with the liquid filling system PLC programmed in the cycle of scanning execution.
1.2 Basic configuration
According to the automatic filling system design program selected Siemens S7-300 supporting products, including power modules, CPU modules, input modules, output modules, FM354 positioning module. This liquid filling device selected PS307 power supply module, CPU selection 315-2DP, due to the need to achieve nearly 70 external input detection action, nearly 50 external output action, the automatic filling device design uses a number of DI/DO.AI/AO modules, including two SM321 digital input module, one SM322 digital output module, one SM323 AI/AO modules include 2 SM321 digital input modules, 1 SM322 digital output module, 1 SM323 digital input/output module, 1 SM331 analog input module, and 1 SM332 analog output module for input and output command operations. When there is an input signal from the external sensor of the liquid filling machine, the input module will immediately transfer the instruction to the module, and when processed by the CPU of the automatic filling machine, the action of the corresponding point of the output module is required. The main circuit of the automatic filling machine in the design of the motor load, AC to DC switching power supply location and power distribution cabinet specifications, so that it meets the production needs, weighing and filling equipment control cabinet of the total power switch should be installed in the control cabinet panel, automatic filling scale so that when you use it does not have to open the door of the control cabinet, the cabinet is reserved for a certain amount of space, easy to adjust. The control cabinet is equipped with automatic lighting, internal cooling fan and spare sockets, PLC transmission and control panel.