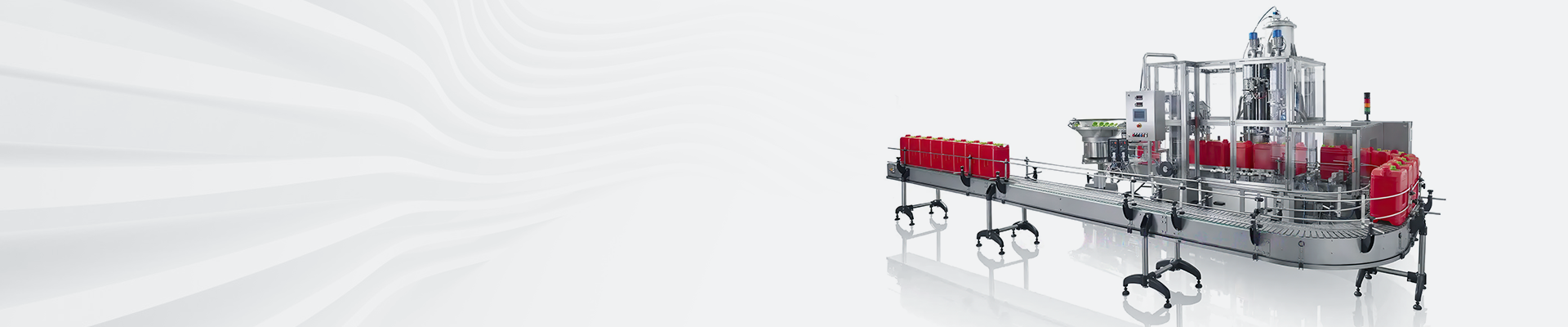
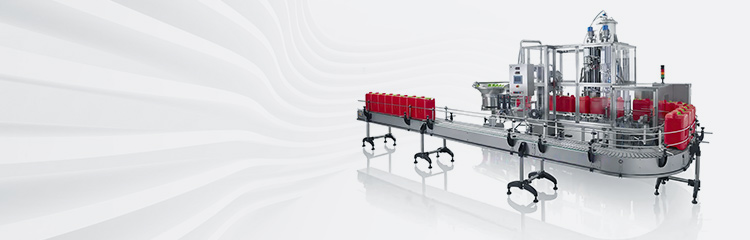

Summary:Filling machine in the low-temperature state of the use of the problems that are likely to occur and the reasons for this, on the basis of the constant temperature heating solution. Taking DM-25A filling machine as the object, the constant temperature heating device of the filling machine using DS1620 digital temperature measurement and control device as the core is designed, which improves the low-temperature adaptability of the filling machine and improves the performance of the equipment.
0 Preface.
From the control characteristics, automatic filling machine can be divided into two forms of pneumatic and electric. The so-called pneumatic refers to: weighing unit using resistance strain type weighing module to detect the weighing signal, control and display unit using a high degree of integration of weighing instrumentation and digital processing technology of the main control template, the feeding system and clamping the bag discharge system is controlled using pneumatic components; and electric is the feeding system and clamping the bag discharge system using electromagnet control. Pneumatic form of metering filling machine structure is simple, fast weighing speed, good stability, but the ambient temperature has certain requirements, theoretically speaking, the ambient temperature can not be lower than 0 ℃. Electric form of automatic filling machine, although the requirements of the ambient temperature is not very strict, but because of its more complex structure, and make its weighing speed is low. Combined with speed, stability, economic benefits and many other factors, manufacturers still prefer pneumatic form of filling machine. The vast majority of filling machines on the market today are pneumatic.
1 low-temperature pneumatic filling machine in the use of problems
Pneumatic filling machine on the use of pneumatic components, and the pneumatic system due to the presence of moisture, so its use of temperature must be above 0 ℃, but in the winter, China's northeastern region, the temperature of -5 ~ -25 ℃ between the time to reach more than 100 days, and some areas of the lowest temperature to be below -30 ℃. To use the filling machine in such a low temperature environment, manufacturers must take anti-freezing measures, otherwise the machine works abnormally or even stops working.
DM-25A type filling machine uses AD-4401 weighing instrument, which is compact, shockproof performance is good, the front panel has a splash-proof function. The internal resolution of the instrument is 0.0001%, the sampling frequency is 100 times/s, it has a dual display VFD screen, which can display tare weight, target weight, cumulative weight and so on more flexibly compared with other instruments, and the various timer functions inside the instrument and the built-in control program can be used for the PLC free silo system of the programmable controller. It also has eight weighing modes and RS-422/RS-232 communication functions, and can also be used as a filling scale, calibration scale, and loss-in-weight scale control, making it an excellent price/performance ratio weighing controller in today's world. Its working environment temperature requirement is -5~+40℃. The production workshop of the rice processing plant does not have any warming measures at all. Just into the winter, the ambient temperature of -10 ℃ or so, for the new machine, the pneumatic system in the water is very little, filler work is basically normal, weighing accuracy and speed can still meet the requirements. However, after the filling machine is used for half a year, due to more moisture in the pneumatic system, the action of the cylinder will be a little slow, thus affecting the precision and speed of weighing. On the other hand, too low a temperature will also have an effect on the electrical performance of the electronics. When the temperature is even lower to -15℃ and below, it stops working, and the filling machine cannot work normally or does not work at all. Therefore, solving the filling technology under low temperature is a problem that users and manufacturers attach great importance to. The use of constant temperature heating technology to increase the filling machine's anti-freezing warm function is an important way to solve the problem of low-temperature filling.
2 thermostatic heating device design
2.1 TDM-25A type loose material filling machine structure analysis and heating point layout
TDM-25A loose material filling machine is designed with overall structure, divided into two parts, the upper part is installed with weighing instruments, weighing modules, hopper scales, size of the feeding system, etc., its two sides and the back of the door is open for observation and loading and unloading parts; the lower part is installed with pneumatic control system (including pressure regulating valves, muffler exhaust valves, pneumatic solenoid valves), the main control board, thermostatic control device and bag clamping and discharge system. The lower part is installed with pneumatic control system (including pressure regulating valve, muffler exhaust valve, pneumatic solenoid valve group), main control board, thermostatic control system, bag clamping and discharging system, etc. There is a door at the back of the machine for installing, overhauling, and replacing the circuit boards and pneumatic devices. The upper and lower movable doors have locks for locking and relatively good sealing.