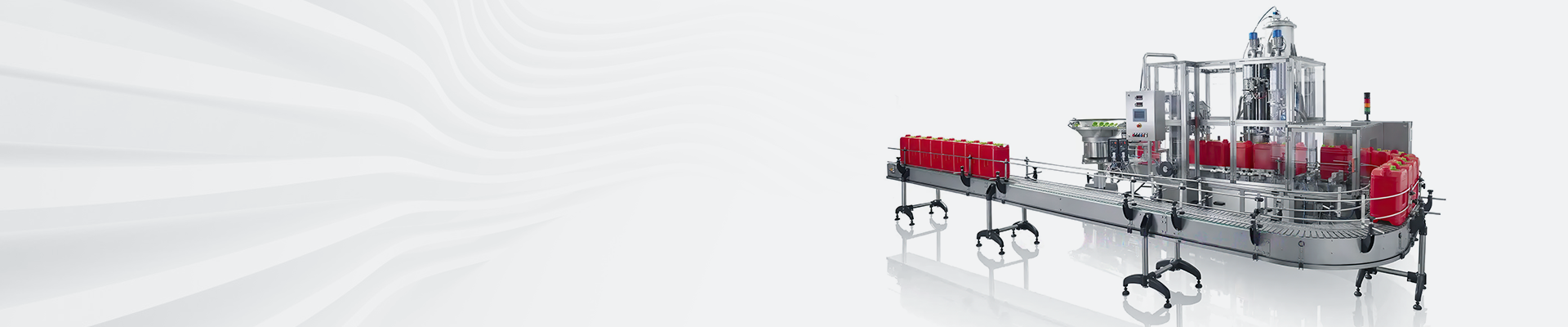
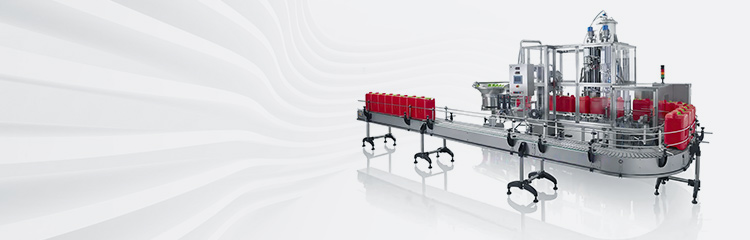
摘要:液体灌装机依次完成:上桶,进桶,上料,进料,灌装,出桶,旋盖,封箱,码垛等步骤,采用PLC做的主控制元件,光电和接近开关等检测称重传感器作为外部输入信号,伺服电机、动作气缸等作为输出元件。
1系统方案设计
灌装机在自动控制系统的硬件包括单片机、重量检测电路、线性放大电路、A/D转换电路、显示器、键盘和其它一些电路等组成。灌装机通常以自动称重配料系统为主控单元是通过单片机灌装系统设计。一般来说,灌装设备选用单片机控制从产品的成本,灌装机械占用空间等方面来说这是最好的选择。液体灌装机通过对市场上的单片机品种的调查有多种单片机都可以完成所需功能。灌装装置选用的单片机是宏晶科技推出的新一代单片机STC90C516RD+。定量灌装机这款单片机成本低,性能优良,液体灌装机同上拥有超强的抗静电,定量灌装机超强的抗干扰能力,功耗较低,运作高速可靠。自动灌装机系统要求具有将生产数据(工业产出能力、生产批号等)上载到PC机的功能,自动灌装机同时可以査看瞬时生产速率,已灌装数量等等。
1.1工艺流程
液体灌装机的设备开启自动灌装之后,灌装输送机开始运转。称重灌装机主控制系统采用PLC做的主控制元件,定量称重灌装机光电和接近开关等检测称重传感器作为外部输入信号,伺服电机、动作气缸等作为输出元件。同时自动灌装机生产线具有产品的在线实时监控功能,并具有产品信息的录入功能,计算机通过串行通讯与PLC液体定量灌装机相连,防爆灌装机能够实时采集数据并能进行生产线数据处理和数据录入、保存。多混合防爆液体灌装机控制功能是用硬件继电器实现的。定量液体灌装机继电器串接在控制电路中根据主电路中的电压、电流、转速、时间及温度等参量变化而动作,多混合称重液体灌装机以实现电力拖动装置的自动控制及保护。系统复杂,在控制过程中,搅拌罐称重自动灌装机如果某个继电器损坏,都会影响整个液体自动灌装机称重系统称重模块的正常运行,查找和排除故障往往非常困难,虽然继电器本身价格不太贵,但是控制柜的安装接线工作量大,因此整个控制柜价格非常高,灵活性差,响应速度慢。自动液体灌装机灌装包装桶在灌装机中依次完成:上桶,进桶,上料,进料,灌装,出桶,旋盖,封箱,码垛等9个步骤。正常操作时,液体灌装设备在满足联锁开关闭合、气压条件、液位条件等外部输号正常时,设备在按压启动开关后,自动灌装设备应处于自动运行模式,灌装线上的各个工位会按照液体灌装系统PLC中编好的程序循环扫描执行。
1.2基本配置
根据自动灌装系统设计方案选用了西门子S7-300的配套产品,包括电源模块、CPU模块、输入模块、输出模块、FM354定位模块等。本液体灌装装置选用了PS307电源模块,CPU选择315-2DP,由于需要实现近70个外部输入检测动作,近50个外部输出动作,自动灌装装置设计中使用了多个DI/DO.AI/AO模块,包括2个SM321数字量输入模块,1个SM322数字量输出模块,1个SM323数字量输入/输出模块,1个SM331模拟量输入模块,1个SM332模拟量输出模块用来进行输入、输出指令操作。当液体灌装机械的外部传感器有输入信号时,输入模块会立即将指令传输到模块中,当经过自动灌装机械CPU处理后,需要输出模块相应点的动作。自动灌装机的主回路在设计时充分考虑电机负荷、交流变直流的开关电源位置和配电柜规格,使之满足生产需要,称重灌装设备控制柜的总电源开关应安装在控制柜面板上,自动灌装秤以便使用时不必打开控制柜门,柜内预留有一定的空间,方便调整。控制柜加装自动照明,内部有散热风扇及备用插座。PLC输入输出各留出至少5个以上的空点,并留有单独不被其他设备占用的计算机连接接口,逐级设定管理控制权限。
1.3结构设计
称重灌装机传感器及支架要安装牢固,位置应方便维护;传感器加装外部金属防护,防止损坏。主要由储液箱、灌装机构、推桶机构、进辊筒输送机、称重机构、出辊筒输送机及控制箱等组成。
灌装PLC控制空桶送进,灌装阀灌装,称重传感器计量,成品输出,完成一次灌装过程。储液箱上设计了上料机构,储液箱内装置浮球位置设计时设定了两个值,最低值和最高值,浮球位置处于最低值时上料,浮球位置上升到最高值时停止上料。灌装阀由双工位气缸驱动,分两次灌装。当桶被送进进辊筒输送机上称量灌装机时,光电开关1检测到桶已到位,推桶气缸动作,将空桶推到称重机构上的无动力辊筒上,即位置2。光电开关2检测到桶已到液体灌装机灌装位置时,灌装阀全打开开始灌装,当灌装重量达到设定初始重量时,灌装阀半开启进行灌装;当灌装重量达到设定重量时,即需要的灌装重量时,灌装阀全关闭。推桶气缸动作,推动下一个空桶到位置2,此空桶将称量自动灌装机灌装完毕的桶从位置2推到位置3,即推到输送机上输送出去。
2硬件设计
称重仪表硬件电路主要由以STC12C5A60S2为核心的单片机最小系统、串口通信、电流转换电压电路、液晶显示电路、独立式键盘电路和HX711模块电路等组成。
电路将三个非电量信号(液体重量、液位高度和阳值)转换为三个电量信号,单片机采集这三个电量信号转换为对应数据。再通过液体重量和液位高度计算出液体比重,再配合液体P值确定最终液体成分。
3程序设计
液体灌装机生产工艺过程PLC是利用计算机技术对生产过程进行集中监控、操作、管理和分散控制的一种新型的控制技术。可以通过监管操作站对整个生产工艺,全过程中的数十至上百个监测点,进行集中监测监视控制、生产工艺参数实时记录,产生生产工艺过程管理报表、产品质量管理报表、生产过程历史报表等查阅和打印等,从而使产品生产质量稳定和产品质量等级提升,不但可以确保自动灌装机生产安全的可靠性,也使原有的生产工艺操作过程监管快步进入计算机灌机管理模式。PLC控制系统可以实现工艺过程单元全自动、半自动和手动控制的基本功能,称量灌装机生产过程关联的物料称重配比自动、半自动、手动控制及过程记录、报表等功能;生产过程中分散灌装运转状况、记录、报表等功能;生产过程中设备运转状况、记录、报表等功能;整个生产过程全程记录,上传各数据,使整个过程一目了然。
4总结
基于单片机控制的多功能液体容器可以测量20到1500公斤液体灌装信息,能自动测量液体的液位、重量、体积、比重等相关参数,并能判别液体成分,如纯涂料、胶水、油脂、溶剂和各种化工等液体,并能将相关数据显示到液晶显示屏上。根据实验检测,系统误差能达到液位测量绝对误差的绝对值小于1mm;重量测量绝对误差的绝对值小于0.5g。