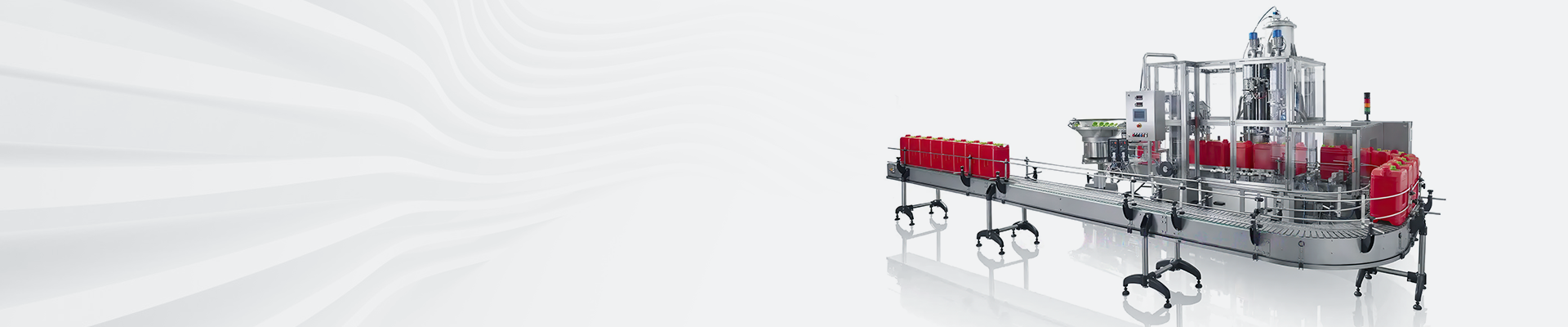
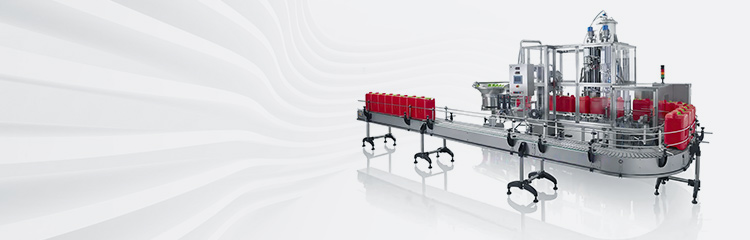

Summary:The online sorting machine completes the collection of weight signals and sends the weight signals to the controller for processing. The infeed conveyor ensures sufficient spacing between the products mainly by increasing the speed. The outfeed conveyor is used to transport the inspected products away from the weighing area.
At present, packaging, filling automatic production line to prevent the filling weight is not enough level detection, packing lack of bottles and other positions, still following the old method of manual testing, requiring employees to stare at tens of thousands of bottles of products per hour from the eyes of the eyes, the eyes are very easy to fatigue; or packaging bottles should be stationed in the packaging machine, to prevent the lack of bottles. In order to reduce the enterprise's labor input, improve production efficiency, the development of automatic online monitoring of the sorting device is essential. Developed a system of dynamic weighing module of Keating ADuC7026, the design greatly improves the system response speed, can be quickly weighed, but need the configuration of the upper and lower machines to realize, the more equipment required, the system independence is poor". The dynamic weighing system developed by utilizing PID sampling and using ARM embedded system, but its weighing efficiency and speed is slower than the designed system, and all of them are upper and lower machine configurations, which can't be directly connected with other equipments of the production line. Therefore, the development of an automatic production line online dynamic weighing control system, real-time product sorting, grading screening and rejection, direct communication with the front and rear of the filling machine and labeling machine, reduce human labor intensity and reduce production costs is very important.
1 system function introduction, hardware design
1.1 Structure design
Checkweigher requirements for automatic weighing is the system can flow through the weighing part of the continuous or discrete materials for real-time weighing, according to different requirements for display, storage, and to achieve the necessary control. The flow rate of discrete materials is different according to different applications and system accuracy, generally 60~200 pcs/min. For example, this system is designed for on-line weighing and sorting of filled beer in the beer production line, the proposed maximum weighing capacity is 5kg, the product size is <120mm in width and <120mm in length, and the accuracy of the flow rate of 240 pcs/min is required to reach 0.05%. Weighing module row in the back of the labeling machine, packaging machine in front of the position, placed in the middle of the conveyor chain from left to right for weighing, the interval between the sensor and the weighing platform is just the width of a product, when the weighing of the product is almost over, the next product just to arrive at the population position, the last product arrived at the position of the sorting cylinder, so that the data are recorded in turn.
1.2 System hardware design
Hardware design mainly includes programmable controller, weighing module, transmitter and analog module.
Programmable controller selection of a company's F series of FX2n-32MR-001, the PLC has 16 input points and 16 points of relay outputs, to meet the requirements of the control port, and lower prices, stable performance. Coupled with the FX2n-4AD analog input module, the module has four channels from CH1 to CH4, each channel can be AD converted, with 12-bit resolution and 1-bit sign, the collected signal voltage is -10V to +10V, with a resolution of 5mV. current input is 4~20mA, with a resolution of 20uA, and the FX2n-4AD has 32 internal 16-bit buffer registers BMF for exchanging data with the host. the FX2n-4AD occupies 8 points of the FX2n expansion bus.
The weighing module and transmitter adopt a company's JHBT weighing module, which is a molded box series load cell that uses foil strain gauges affixed to an elastomer made of alloy steel, featuring high precision, small temperature contamination, and strong overload capacity. The transmitter selects the matching HSO2 amplifier (digital display instrument can be selected). Standard signal 0~10mA, 4~20mA or 0~10V output.
Analog weighing module composed of elastic measuring elements and strain gauges collects the analog signal of the measured weight, the transmitter amplifies and converts the weak analog signal (mV level signal) into standard analog signal (0~10V), the standard signal is sent to the voltage input of the analog module, and samples the signal by using the 12-bit ADC with a sampling rate of up to 1MSPS integrated inside the CPU CPU samples the sampled The signal is filtered and processed by the CPU, and the processed data is sent to the superior control PLC via RS-485.PLC can send instantaneous data or average value data commands to the CPU at any time, and read/write the parameters inside the CPU; PLC can carry out further subsequent processing by judging the values delivered by the sensors.