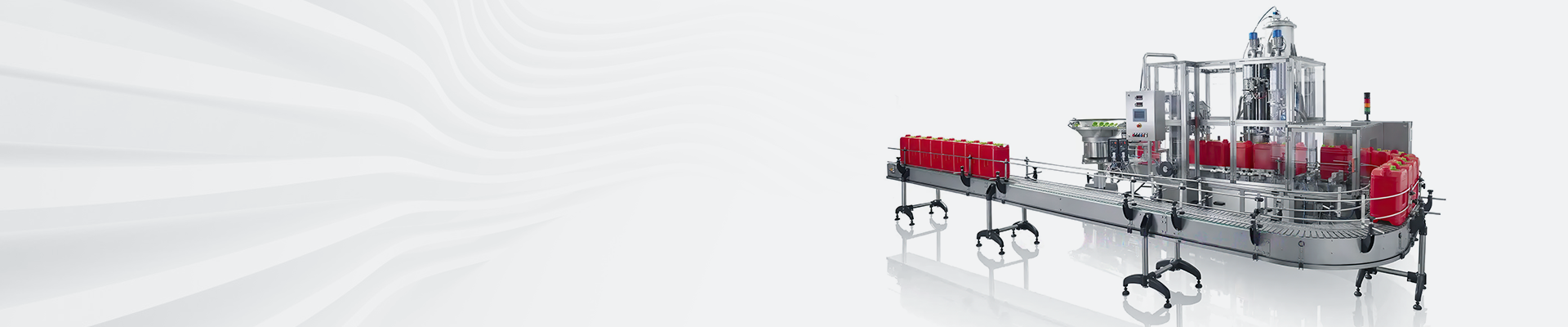
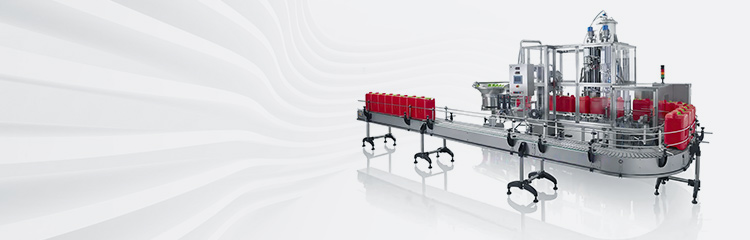
摘要:在线分选机完成重量信号的采集工作,并将重量信号送至控制器进行处理。进料输送机主要通过提高速度来保证产品间具有足够的间距。出料输送机用来将完成检测的产品输送离开称重区域。
目前包装、灌装自动生产线为防止灌装重量不够的液位检测、装箱缺瓶等岗位上,仍然沿用人工检测的老办法,要求员工每小时盯住几万瓶产品从眼前晃过,眼睛非常容易疲劳;或包装装瓶时要驻守包装机,防止缺瓶。为了减少企业的人力投入,提高生产效率,开发自动在线监测分拣装置的是必不可少的。开发了基丁ADuC7026的动态称重模块的系统,该设计大大提高了系统响应速度,能快速称重,但需要上下机的配置才能实现,所需要的设备较多,系统独立性较差“。利用PID采样、采用ARM嵌人式系统来研制的动态称重系统,但其称重效率和速度要比设计的系统要慢,并且都是上下位机配置,与生产线的其他设备不能直接连接。因此,开发出自动生产线的在线动态称重了控制系统,实时对产品进行分拣、分级筛选和剔除,直接与前后的灌装机和贴标机通信,减少人的劳动强度和降低生产成本就显得非常重要。
1系统功能介绍、硬件设计
1.1结构设计
检重机对自动称重的要求是系统能对流经称重部件的连续或者离散物料进行实时的称量,根据不同的要求显示、存储,并实现必要的控制。对于离散物料的流速则根据不同的应用场合和系统精度而不同,一般60~200个/min。如本系统针对啤酒生产线上灌装好的啤酒进行在线称重分拣,拟定最大称重量为5kg,产品尺寸为宽<120mm,长<120mm,按照流速240个/min情况下精度要求达到0.05%。称量模块排在贴标机后面,包装机前面的位置上,安放在输送链中间从左到右进行称重,传感器与称重平台之间的间隔刚好是一个产品的宽度,当该个产品称重快结束时,下一个产品刚好到达人口位置,上一个产品到达分拣气缸位置,以此依次记录数据。
1.2系统硬件设计
硬件设计主要包括可编程控制器、称重模块、变送器和模拟量模块。
可编程控制器选用某公司的F系列的FX2n-32MR-001,该PLC具有16输入点和16点继电器输出端,能满足控制端口要求,而且价格较低,性能稳定。再配以FX2n-4AD模拟量输人模块,该模块有CH1至CH4四个通道,每个通道都可进行AD转换,分辨率为12位,符号1位,采集信号电压为-10V到+10V,分辨率为5mV。电流输人时为4~20mA,分辨率为20uA,FX2n-4AD内部有32个16位的缓冲寄存器BMF,用于与主机交换数据。FX2n-4AD占用FX2n扩展总线的8个点。
计量模块和变送器采用某公司的JHBT称重模块,其为模盒系列称重传感器,采用了箔式应变片贴在合金钢做的弹性体上,具有精度高、温污小、过载能力强等特点。变送器选择配套的HSO2放大器(可以选择数字显示仪器)。标准信号0~10mA、4~20mA或0~10V输出。
由弹性测量元件和应变片组成的模拟称重模块采集到被测重物的模拟信号,变送器将微弱的模拟信号(mV级信号)放大转换为标准模拟信号(0~10V),标准信号被送入模拟量模块的电压输入端,利用CPU内部集成高达1MSPS采样率的12位ADC对信号进行采样CPU对采样后的信号进行滤波和数据处理,将处理后的数据通过RS-485发送至上级控制PLC。PLC可以随时向CPU发送瞬时数据或均值数据命令,并对CPU内部的参数进行读写操作;PLC可以通过判断传感器输送过来的数值进行进一步的后续处理。
本系统采用的变送器将传感器的微弱信号(mV)转换为标准模拟信号(如0~10V),变送器的外部输入电压只要将信号的+、-极分别接模块的VI+和VI-端。由于模拟量模块是12位的,其电压和数字量转换公式为:电压y-0.00049x,x为输出的数字信号,y为信号输人电压V。
1.3系统软件滤波
由于输送机生产线上瓶子的输送速度是快速并且是固定的,约为0.5ms的速度。瓶子以一个冲击形式进入和离开称重台,剩下平稳的称重时间是非常短的,在这大约20ms时间内完成测量,在软件设计上除了考虑静态因素以外,更重要的是要解决动态称重外界干扰大和测重间隔短所造成的称重误差较大的问题。对于瓶子进入和离开时对称重平台的直接和间接冲击会对系统产生一个超调量,该量处理不好会产生很大的称重误差。因此,本系统应用斜率滤波法对采样数据进行滤波。其原理为:在两个连续的固定采样时间间隔信号之间比较其数值,数值的大小即为其斜率,设置该比值的阙值点,对超过该阀值的采样数据进行过滤,对剩下斜率变化不大的数据点进行均值滤波,从而消除振动和高频所引起的干扰。
另外,为了提高系统的采样响应速度,本系统同时设置一个最低的响应阀值100,即空瓶重量的一半。当信号低于该阀值时,系统不采样,以此来减少空载高频振动对系统的负担,提高响应速度和抗干扰能力。到的点数是视传输速度而定的,因此根实验选择固定点数据作为最终数据的方式也不行。所以笔者提出斜率滤波法,有效的解决了重响应的数据处理问题,并且大大提高了系统干扰能力。
实验在系统流量是240个/min的情况下多次动态检测和静态测量的数据比较。结果表明该系统测量精度高,最大测量误差为7g,且测量一致性好,分选动作准确,达到了系统的设计初衷。
2结语
本项目基于PLC控制系统开发德国HBM高精度称重模块,实现自动生产线的在线动态检测机,称出的重量作为产品合格与否的参照值并自动剔除,统计和反馈给灌装系统作为灌装液位调整依据。整个系统设计无须再选择接口、A/D等器件,节约了成本和元器件,且通过总线直接与生产线上其他机器通信,实现全自动化生产和检测。
而且,该分选秤具有测量速度快、测量精度高,成本低,运行可靠,界面显示大方,操作简便以及拓展功能多等特点,适合大多数自动称重行业,且升级方便。不仅减少了企业的人力投入,而且效率高,不受外界干扰,可实现生产线全自动化运行和检测,符合我国国情的验瓶机的国产化具有重要的社会效益和经济效益,该技术在食品饮料、医药以及包装等其他相关行业中也具有广阔的应用市场。