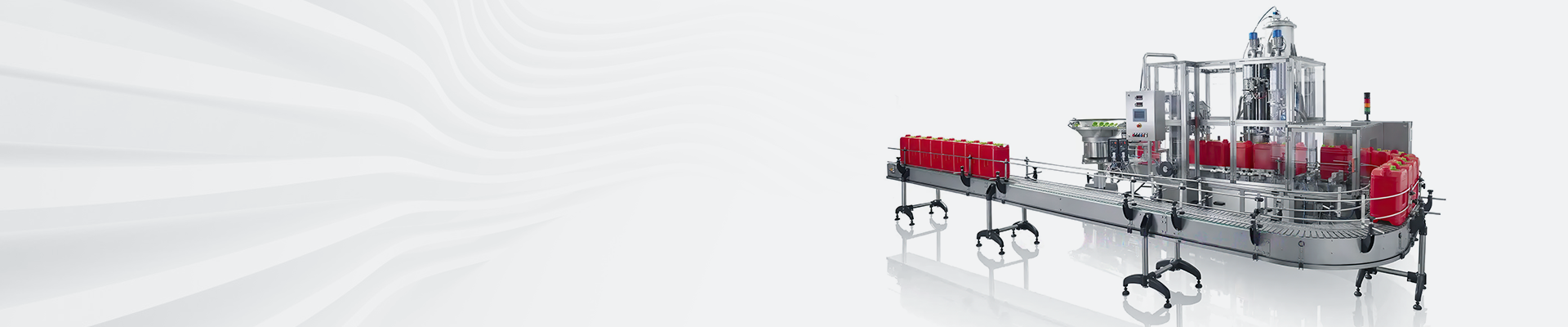
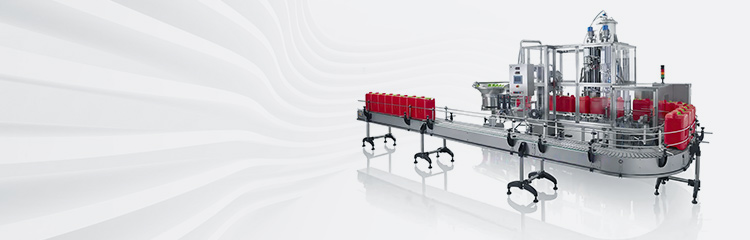

Summary:The automatic batching system organically combines computer technology with traditional relay control, and outputs various control signals to control contactors, relays, solenoid valves and other components to perform corresponding actions.The PLC jog control mode is used for jog blanking to ensure the material measurement accuracy requirements.
Different production process, the automatic feeding system dosage accuracy and working speed has different requirements, automatic dosage system has the following three kinds of control computer, plc, and weighing instrumentation three types of control.
1、Automatic batching system adopts computer for control.
This kind of control is under the control of computer, according to the user's pre-set dosage program automatically weigh all kinds of materials, automatic dosage of all aspects of control, complete the dosage process. The key to accurate dosage of batching machine is to control the rotating speed and start/stop of the motor. In the process of dosage, the rotating speed of the motor is controlled according to the amount of material to be dosed, and it is divided into different modes such as high-speed dosage and low-speed dosage, which can not only improve the working efficiency of the system, but also enhance the accuracy of the dosage. When the difference between the actual feeding and the set value is large, the high speed feeding mode is adopted, which can improve the working efficiency of the system. When the value of already discharged material is close to the set value, low-speed discharging mode is adopted, and the motor stops rotating when the control advance quantity is reached due to the air stagnant material between the discharging port and the material disk. When the actual dosing process reaches the control lead time, due to the difference in material density, the quality of the material in the air retained after the motor stops rotating is different, so the system should be able to set the lead time for the motor to stop according to the actual operating conditions. Determine the end moment of feeding according to the fall compensation coefficient of each material, read the final weight of the material in the hopper after the weighing hopper is stabilized and compare it with the set value, which will be used as the basis for choosing the correction coefficient of the fall of dosage for the next time. That is to say, the current dosage adopts the average value of the measured fallout value and the fallout compensation value of the last dosage to compensate the fallout, and this way can make the dosage accuracy of the dosage system improve with the increase of dosage times.
2、Weighing control system adopts PLC for control.
PLC can realize highly flexible and reliable industrial control by combining computer technology with traditional relay control system. In the automatic dosage system, PLC is mainly responsible for receiving external switching signals to determine the current operating state of the system, and output a variety of control signals to control contactors, relays, solenoid valves and other components to carry out the corresponding action. According to the specific dosage process, at the beginning of the dosage, the motor runs normally, the feeding system discharges the material at high speed, and when the material weight is close to the target value, the PLC adopts the pointing control mode to discharges the material, so as to ensure the requirement of material measuring accuracy. In addition, it is also responsible for receiving the control commands from the upper computer to complete the control of automatic batching.
3、Weighing and batching is controlled by special weighing instrument.
Weighing instrument is generally for quantitative packaging, sorting and automatic dosage and other applications specifically tailored to the instrument has a collection of weight signals and processing, the corresponding control signal issued by the function, easy to install and debugging, is currently more common in the feeder in a way to control. The use of weighing instruments to detect and control the materials allocated, can better overcome the shortcomings of low dosage accuracy, but also has a direct realization of the quality of the ratio, high reliability and superiority. Weighing instrument generally have fast, slow two kinds of charging speed, in the dosage of the beginning of fast charging, fast charging advance is for the slow charging process to determine the amount of charging, after reaching the set value of the use of slow charging, slow charging advance is to compensate for the impact of the air flying material, so that the weighing value is as close as possible to the set value. Therefore, according to the actual production process of weighing instrumentation settings, reasonable setting of fast plus advance and slow plus advance, can be better control of dosage accuracy. Through the test on the dosage process, for different materials, according to the error situation of multiple measurements, set the control advance amount. This control method is suitable for the production process with uniform feeding speed, if the feeding speed fluctuates greatly, it will cause large quantitative deviation and affect the dosing accuracy.
At present, the introduction of automatic control methods in the dosage process, for the uncertainty of the factors can be well controlled, reduce the dosage error and speed up the weighing speed, is the dosage system for high precision requirements of the more commonly used control methods.