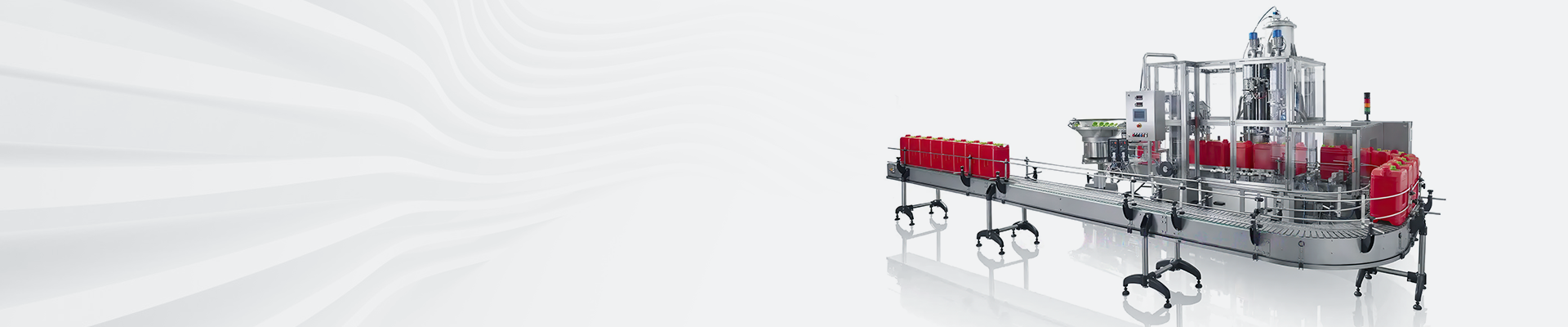
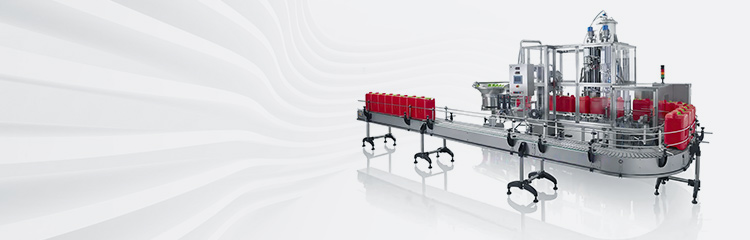

Summary:The weighing and batching system collects the signals from the weighing sensors, generates control commands for the actuators with the help of the raw material ratio given by the formula, and controls the screw feeders, valves and hot and cold mixer valves of each silo through the programmable controller. Start, stop and open and close.
The dosing system can provide dosing whole process monitoring for many kinds of complex materials at the same time.
Software functions: real-time dynamic display of a variety of processes, design recipes, weighing scales.
Batch quantity, mixing time, graphical report of production statistics, fault display, real-time and historical trend curve, optimization of formulas, display of operating status parameters of production line equipments, acousto-optic fault alarm and chain protection.
Completion of multi-bin and multi-scales to realize the complex functions of weighing, batching, mixing, heating, cooling, conveying, packaging and testing, etc., using frequency converter to realize the high precision of batching, automatic correction of the impact of the material and the error of hanging material.
Professional solid material arching control technology, liquid small material metering and filling control technology.
Multi-screen display, powerful control function, anti-interference, hand/automatic non-interference control conversion.
All the equipments of automatic batching production line can realize the whole process of start/stop chain protection control.
Distributed control system and frequency conversion speed control technology through the network to realize remote group control for multiple sets of batching equipment.
Professional production information management software, real-time detection, storage silo material level, dosage scale finished product packaging detection and other material conditions, materials into the warehouse to the finished product factory, to achieve the system management level control, to realize the factory information management network, production data sharing.
The automatic batching system collects the weighing signals from each load cell in real time. According to the weighing signals and production formula, it generates control signals for screw feeder and electronic scale valve. Dynamic detection and processing of various faults that may occur in the dosage process.
The lower computer communicates with the upper computer.
Centralized monitoring by the upper computer. When batching, the weighing instrument collects the signals from the weighing module, generates the control commands of the actuators with the help of the raw material ratios given by the formula, and controls the starting and stopping, opening and closing of the screw feeders, valves and valves of the hot and cold mixer of the silos by the programmable controller; the operation and faults of the motor and valve are obtained by detecting the motor protection device and the valve position switching status, and can be displayed on the analog display operation screen of the electrical control cabinet or monitored by the host computer. It can be displayed on the screen or on the monitor of the upper computer, and is divided into four parts: sending feeding, batching and measuring, material mixing, lifting and feeding, and each part can work independently or work automatically with each other, and it can also work normally in the case of detachment from the upper computer.
Dosing composition
I. Batching control system 1: sending feeding system. Its function is to convey the PVC resin in the sending and loading operation room on the first floor to the three storage bins on the third floor. It adopts positive pressure dense phase pneumatic conveying method. The system consists of compressed air inflatable pipeline, dust collector, positive pressure pneumatic sending tank, exhaust valve, inflatable valve, inlet valve, outlet valve, air knife valve, dust collector motor, vibration motor and so on. It adopts 1#PLC for logic control.
Second, weighing control system 2: main materials, auxiliary materials, batching machine. Its function is to measure the main material (PVC resin) and many kinds of auxiliary materials separately according to the formula of production process, and then convey them to 1# mixer. The system consists of 1# main material scale, auxiliary material scale, and trace material step feeder. It adopts 2#PLC for logic control.
Weighing Mixer 3: 2# main material and auxiliary material metering system. Its function is the main material (PVC resin) and a variety of auxiliary materials according to the production process formula were measured, and then transported to the 2 # mixer. 2 # mixer after processing the finished material with a trolley to store, supply the extruder for the production of PVC foaming pipe use. The system consists of 2# main material scale, auxiliary material manual feeder. It adopts 3#PLC for logic control.
Automatic batching machine 4: 3# main material and auxiliary material measuring system. Its function is to calculate the main material (PVC resin) and many kinds of auxiliary materials according to the formula of the production process, and then convey them to 3# mixer. 3# mixer finished processing the finished material with a trolley to store, and supply the extruder to produce PVC anisotropic material to use. The system consists of 3# main material scale, auxiliary material manual feeder. It adopts 3#PLC for logic control.
Metering Feeder Unity 5: Extruder Feeding System. Its function is to use the vacuum lifting fan to transport the finished material in the mixing bin to the extruder hopper, supplying the extruder to produce PVC foam sheet. The system consists of a gate valve at the bottom of the mixing bin, vibrating screen, transition box, extruder vacuum suction box, extruder vacuum lifting fan and other components. Adopt 3#PLC for logic control.
Weighing and mixing muscle 6: 1 # mixer control system. Its function is to mix the main materials, auxiliary materials and trace materials conveyed by system 2, stirring and mixing, warming, cooling and cooling treatment in 1# mixer, and then discharge the processed finished materials into the transition bin. The system consists of hot mixer and cold mixer in 1# mixer, as well as feed valve, discharge valve, blowback valve and so on. It adopts 4# PLC for logic control.