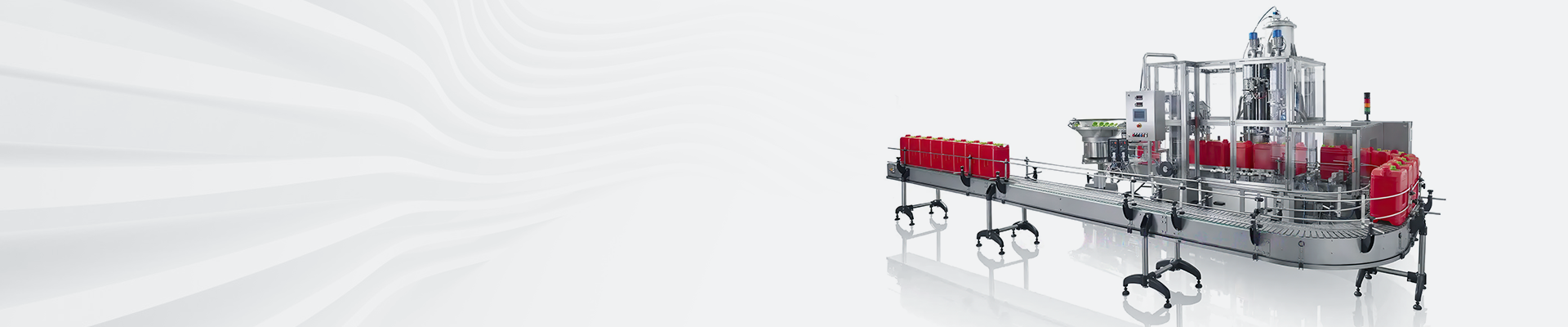
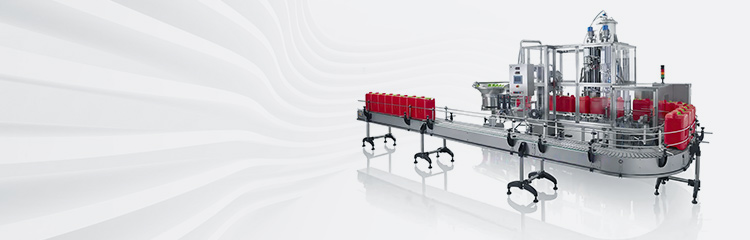

Summary:The batching system provides access to the PROFIBUS system based on the PB-B-RS232 weighing instrument, and the proportion of auxiliary raw materials set manually and computer-set. The auxiliary raw materials entering the reactor are weighed by the hopper scale and then automatically loaded according to the amount.
Weighing instruments are used in all walks of life, unfortunately most of the weighing indicators only with serial port or 485 port, which and it was originally designed to be connected to the computer's serial port, with the use of fieldbus in various fields, how to weigh the instrument access to the field weighing and dosage system will be a matter of concern, the automatic loading system will be through the PB-B-RS232 bus bridge will EDI-800A intervene in the Siemens 400 PLC to briefly explain the process of realization and some of the issues to be aware of. RS232 bus bridge will be EDI-800A intervene Siemens 400PLC to briefly explain the process of realization and some of the issues to be noted.
Second, the system architecture
Feeding system here in order to tell the simplicity of the weighing system will be the other from the station are omitted, such as Siemens ET200 and so on. This weighing and feeding system uses Siemens 400 PLC as the master station, the configuration software used is STEP7, PLC from the first bus bridge distance of about 200 meters, PROFIBUS baud rate of 1.5M, so the use of Siemens repeaters, after the first bus bridge PROFIBUS will be connected to the second bus bridge in the 48-meter-high platform, due to the 48-meter-high platform, four buses on the platform. 48-meter-high platform on the four bus bridges and 42-meter-high platform on the one bus bridge between the total distance of nearly 100 meters, plus the distance up and down, so that the next 20-meter-high platform on the bus bridge distance from the first close to the distance of 200 meters, so in both sides are added to the repeater. All the devices connected under the 11 bus bridges are EDI-800A weighing controllers.
The equipment connected under EDI-800A is the weighing hopper in the bulk weighing and batching machine of the conveying reactor and batching reactor, which mainly feeds back the weight data of the batching and conveying process to the master station in time.
Third, the realization of the process and function
The function of this project is relatively simple, EDI-800A periodically and automatically sends out telegrams containing weight information, and PB-B-RS232 is in the state of automatic reception, it is necessary to write a program in the OB module, i.e., the lowest bit of the status word of the PB-B-RS232 (ready to send after receiving) is used to control the sixth bit of the control word (forcible reception). Also need to pay attention to a place is the explosion-proof electronic scales and bus bridge serial interface between the communication, the first point of the communication interface should be set correctly, including baud rate, data bits, stop bits, parity; the second point is to be wired correctly, pay attention to check the manual on the description of the TXD (transmit), RXD (receive) and GND (ground) are the pins, select the appropriate serial line or to make their own.
The following briefly mentions the role of the weighing system in the resin weighing feeder. Resin is the process of removing the carbon content of the raw powder to a specified range and reducing or increasing the content of other elements to a specified range according to the requirements of the ingredient being dosed. Weighing errors and compositional errors in the main raw materials (methanol and resin) and secondary raw materials (additives, ethanol, propanol, solution, polyester, etc.) of the rotary reactor directly affect the resin end-point dosing ratio and the quality of the resin. This weighing and dosing system is used to ensure accurate weighing of the primary and secondary raw materials. There is a lot of weight information that needs to be transmitted back to the main station in a timely manner, including three parts. ①Electronic scale: it is used to weigh methanol, resin, polyurethane and resin, and can be automatically tared; ②Sub-ingredients weighing and feeding control: when the sub-ingredients in the high-level silo are used up, the sub-ingredients from the underground silo can be automatically fed into the high-level silo, which adopts a material level detector to check out the silo level signals, and is weighed on a belt scale, and the feeding is controlled by an electronic logic or a micro-computer; ③Sub-ingredients auto-dosage control: the sub-ingredients are automatically dosed and controlled according to the manually set and computer-set sub-ingredients dosage ratio and the quality of resin. ③ automatic batching control of secondary raw materials: according to the proportion of secondary raw materials set manually and by computer, the secondary raw materials into the reactor are automatically loaded according to the quantity after weighing by hopper scale. There are also conveying to the reactor bulk material weighing and batching system silo and batching tank to the reactor bulk material silo used in a lot of weighing hopper.
IV. Conclusion
The PB-B-RS232 weighing instrument for dosage systems provides a solution for accessing PROFIBUS to provide timely feedback of weight data from the dosage and conveying process to the master station. All other weighing devices can be easily connected. That is to say, any weighing device with a communication interface (or any other device such as a weight indicator) can be connected to the PROFIBUS weighing and dosage system by means of a technological bus bridge of the corresponding type.