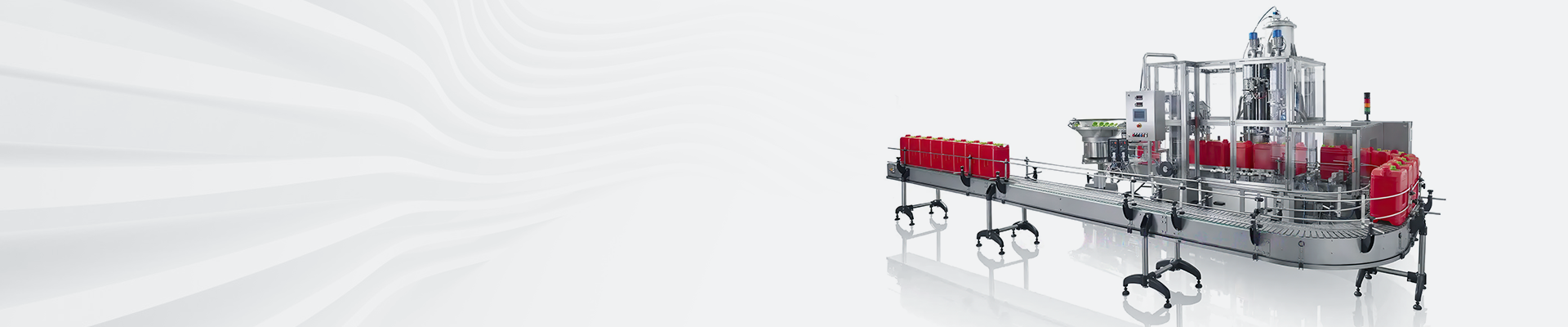
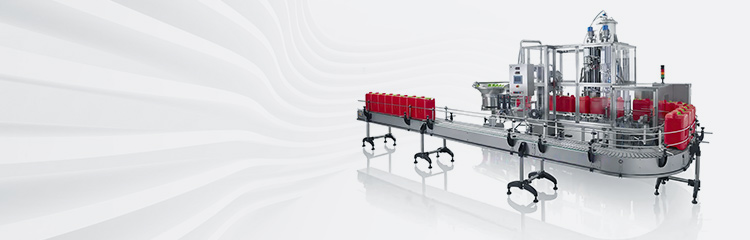
摘要:配料系统其功能是对配料液体进行升温、混配成分微调、稀释、分解、混调、夹杂物控制及均匀温度等处理以提高钛白粉品质。
1引言
反应釜也称搅拌计量反应罐配料系统其功能是对配料液体进行升温、混配成分微调、稀释、分解、混调、夹杂物控制及均匀温度等处理以提高钛白粉品质,是树脂与配料工艺间的重要生产环节,能协调转反应釜称重与配料机的生产节奏等,目前已被越来越多的聚酯广泛应用。而其中向配料液体中投入可控量的钛白粉配及混调料,以精确的控制配料液体的化学成分,对聚酯的质量有着至关重要的调控作用。本文以反应釜为背景,对反应釜钛白粉配自动配料系统的控制作简单介绍。
2反应釜钛白粉配料工艺简述
反应釜钛白粉配料工艺过程包括钛白粉配装料、配料、排料以及投料。
2.1装料:钛白粉配或杂料分品种装入2m3体积大小的底开式料罐中,用汽车运至反应釜,通过反应釜的航吊将钛白粉配或杂料料罐吊起,吊装到10m3钛白粉配高位料仓上。
2.2配料:从树脂转反应釜送来的每一罐配料液体,由于成分有一些差异和产品聚酯不同,所以需要加入不同数量和种类的混配料。混配和杂料按操作人员确认了的配料单进行称量,经振动给料机从高位料仓卸到料斗秤。
1号料斗秤按料单顺序完成1#~6#料仓的称量,2号料斗秤按料单顺序完成7#~10#料仓的称量,3号料斗秤按料单顺序完成11#~15#料仓的称量。
2.3排料:排料包括正常排料和事故排料。正常排料,是将已配好的料从各料斗秤向反应釜的中间料斗的运输过程,在配料及生产正常情况下,正常排料按逆物料方向依次启动设备。事故排料,是在配料或生产异常时,将各料斗秤物料向事故料斗排空。
2.4投料:投料就是通过对反应釜盖混配加料门上的球阀、中间料斗的振动给料机的控制将中间料斗的物料输送到反应釜中。
3系统设计
投料系统由基础自动化系统(L1)和二级过程计算机系统(L2)组成。基础自动化系统包括自动配料系统和HMI监控系统,完成现场数据采集、过程回路控制、参数设定、设备顺序控制、设备运转操作监视及报警等基本控制功能;二级计算机完成设计计划、设计模型计算、配料模型计算、配料液体成分物流跟踪等过程控制功能,两级配料共同完成反应釜钛白粉配自动加料的控制,实现准确配料、自动上料功能,适时掌控所添加物料的品种和数量。
自动化喂料机控制站采用德国西门子公司的S7-400,CPU板为CPU414-2DP,采用以太网与L2及以上系统进行通讯。控制站共有5个ET200远程I/O站,采用PROFIBUS-DP接口通讯。系统编程软件采用STEP7,软件平台基于MicrosoftWindows2000/XP操作系统,安装方便,界面友好。监控软件采用WonderwareINTOUCH,画面图形编制、数据读写、通讯组态、趋势记录、报警记录等都极为方便。系统布局合理,网络运行稳定、通讯畅通。
计量混合机过程控制计算机系统由1台服务器、1台开发维护终端、1台操作站及相应的以太网组成;服务器采用磁盘阵列技术,以保证系统数据的可靠性;服务器、开发维护终端和操作站安装在反应釜操作室内,它们之间通过星型以太网连接;二级计算机通过服务器与基础自动化通讯;服务器通过以太网实现与上位计算机系统之间的数据通信。
4控制功能
自动混料机的控制包括上料系统的控制、配料的控制、排料系统的控制以及投料系统的控制。
4.1上料控制
1)手动上料,根据操作画面上的钛白粉配及杂料高位料仓的低料位报警信号或凭借操作人员的经验定期上料。采用超声波料位计通过超声波回声定位检测料仓内混配的存量,当料位低于15%时,在操作站上有报警显示,提醒操作人员及时补充混配。
2)上料过程中要与高位料仓除尘阀的进行联锁控制。
3)L2操作画面上显示各料仓名称,如果料仓对应物料品种有变化,将实际物料通过L1操作画面录入,并上传至L2系统,同时L1操作画面上料仓号与贮存物料名称的对照表也将自动作相应调整。
4.2配料控制
1)配料控制分机旁手动、远程手动、自动配料控制方式。机旁与远程的切换地点设置在机旁操作盘上,自动与远程手动控制方式的切换点在操作室画面上。
2)机旁手动。不用于生产,用于设备调试和维修,调试和维修人员可在机旁手动启、停各振动给料机。
3)手动配料
a)在操作画面上,将“操作方式”切至“手动”方式。
b)配料系统处于操作室手动控制状态,操作人员可手动分别对各振动给料机进行启、停控制;并在接近称重终点时,手动切换振动给料机到弱振状态,实现慢速加料。
c)手动配料用于配料后混配品种的微量调整或者生产要求有变化时料斗秤的混配补料。正常生产方式下,配料都采用自动配料方式。
4)自动配料
a)在操作画面上,将“操作方式”切至“自动”。
b)配料液体通过测温、取样送到检化验系统,检化验系统分析出配料液体成分通过计算机传到过程配料系统L2级,L2综合计量聚酯、配料液体温度、化学成分、设备性能等因素,通过数学模型计算得到所需添加混配数量和加热时间。按画面上“请求二级”按钮,将需加入反应釜的混配和杂料下载到基础自动化系统,显示在HMI画面上的设定值建议区,对于建议区的设定值,操作人员根据实际经验来确认,也可对过程计算机计算结果进行修改;在过程计算异常时,必须由操作人员在操作画面上人工输入设定值。
e)不同料斗秤的物料可以同时开始称量,需要下料的高位料仓料位信号不为“空”。
每一种物料的设定重量值>相应的高位料仓振动给料机停止给料后的“落差量”。
所设定的由某个料斗秤称量的所有物料的重量和体积的累计量不能超过料斗秤的称量量程和有效容积。
如设定值验证未通过,应有报警提示操作人员。设定值通过验证后,将建议区的设定值下送至接受区;接受区域内的设定值不能修改,只能接受或清除。在设定值由建议区转入接受区的之后,并自动复位清零建议区的设定值。
d)设定值验证通过后,操作人员触发“自动配料开始”按钮,配料检查“配料”前提条件是否成立。在计算机配料开始时,检查电气系统是否“准备就绪”、对应称量料斗为空、且对应料斗秤下的振动给料机处于停振状态。如检查未通过,配料过程处于停止状态并且有报警提示操作人员;如果正常,则“自动配料开始”按钮在自动配料过程中失效,且物料设定值禁止修改;配料系统立即自动启动相应料仓的振动给料机,开始进行自动称量。在自动配料过程中,“自动配料停止”按钮优先,如在自动配料过程中按下“自动配料停止”按钮,则系统立即停止。
e)不同料斗秤的物料可以同时开始称量,对同一料斗秤而言,称量采用累计称量的方法,即一个料斗秤如果有2种物料需要称量,必须按照先后顺序进行,待一种物料称量完毕,不必放空料斗秤,再马上开始第二种物料的称量,重量累计。
f)对每个料斗秤而言,称量过程就是料斗秤重量值(料斗秤压头反馈重量信号)与目标值接近的过程。当重量值与下料目标值相差一定数量(转低速值)时,即到了由高速转低速的“变速点”,振料机在弱振状态下运行。当重量值与下料目标重量相差一定数量(落差量)时,即发出停止振动信号,停止振料机,由于惯性继续落下的物料(落差量)正好使其达到设定值,一种物料称量完毕。
g)所有设定的物料全部按顺序称量完后,计算机自动配料过程自动结束。
4.3排料控制
1)排料系统设置“自动”、“远程手动”和“机旁手动”3种控制方式。“机旁手动”与“远程”的切换地点设置在机旁操作盘上,“自动”与“远程手动”切换地点在HMI操作画面上。
2)远程手动排料。当操作地点为远程,并在HMI上选择了手动模式,排料系统处于远程手动控制状态,操作人员可手动启、停排料系统的设备。
3)机旁手动。不用于生产,用于设备调试和维修,调试和维修人员可在机旁手动启、停各排料系统设备。
4)操作人员判断料斗秤的称量实际情况和生产情况,决定在HMI上选择“正常排料”或“事故排料”方式。
5)自动正常排料。当在HMI上选择了“自动排料”方式;先确认料斗秤的称量作业已完成,且中间料斗振动给料机处于停振状态;操作人员在HMI上按下“正常排料”按钮,“正常排料”和“事故排料”按钮失效,实现自动正常排料。
a)自动正常排料,按垂直螺旋输送机、水平螺旋输送机的顺序逆物料方向依次延时启动皮带。
b)在收到螺旋输送机运行的信号后,有物料的料斗秤振动给料机按照料斗的编号顺序开始顺序启动,但料斗秤不能同时排料。
c)当料斗秤中的物料重量减少至“偏置值”时,延时5秒振动给料机停止。
d)最后一个料斗秤振动给料机停振后延时10秒停止水平螺旋输送机。
e)水平螺旋输送机停止后20秒停止垂直螺旋输送机,正常排料过程结束。
6)自动事故排料。当生产出现异常时,需要把料自动排到事故料斗中。先确认料斗秤的称量作业已完成,且中间料斗振动给料机处于停振状态;操作人员可以在HMI上,选择“自动排料”方式,按下“事故排料”按钮,“正常排料”和“事故排料”按钮失效,实现自动事故排料。
a)自动事故排料按开事故下料三通阀、水平螺旋输送机的顺序逆物料方向依次启动设备。
b)在收到螺旋输送机运行的信号后,有物料的料斗秤振动给料机按照料斗的编号顺序开始顺序启动,但料斗秤不能同时排料。
c)当料斗秤中的物料重量减少至“偏置值”时,延时5秒振动给料机停止。
d)最后一个料斗秤振动给料机停振后延时10秒停止水平螺旋输送机。
e)水平螺旋输送机停止后3秒关闭事故下料三通阀,事故排料过程结束。
4.4投料控制
1)电极在高位才允许混配下料。
2)投料系统设置自动、远程手动和机旁手动3种控制方式。机旁与远程的切换地点设置在机旁,自动与远程手动控制方式的切换点在HMI操作画面上。
3)远程手动投料。当操作地点为远程,并在HMI上选择了手动模式,投料系统处于远程手动控制状态,操作人员可手动启、停中间料斗振动机和加料球阀。
4)机旁手动。不用于生产,用于设备调试和维修,调试和维修人员可在机旁,手动启、停各投料系统设备。
5)自动投料。在正常排料结束后,操作人员就可根据需要,在HMI上按下“自动投料”按钮,自动开始投料控制。
a)先打开加料溜管氮封,延时2秒打开反应釜盖上方混配加料球阀。
b)混配加料打开后,延时2秒启动中间料斗下振动给料机。
c)中间料斗下振动给料机启动后,延时10秒停止中间料斗下振动给料机。
d)中间料斗下振动给料机停止后,延时2秒关闭反应釜盖混配加料门球阀,然后延时2秒关闭加料溜管氮封,自动投料结束。
4.5联锁处理
1)当某一设备发生故障时,其前面(逆物料输送方向为前面)的所有设备立即停,而后面的设备应继续运转,直到物料空为止,避免物料堆积。
2)螺旋输送机设置跑偏开关、打滑检测器和拉绳开关,其信号要与相关控制设备联锁控制。
3)操作画面及紧急操作台设“急停”按钮,在设备运行过程中出现需要紧急停止的情况下,使设备能够可靠停止,以保证设备安全。
5结束语
反应釜钛白粉配加料系统于2016年5月投入运行,目前系统运行良好,自动投运率达100%。典型的配料周期为1分30秒,精度达1.5%。