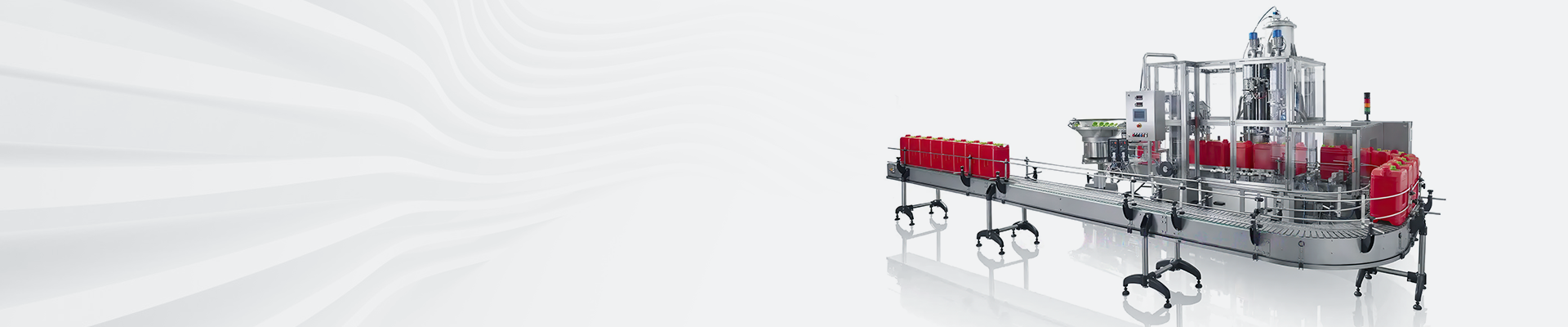
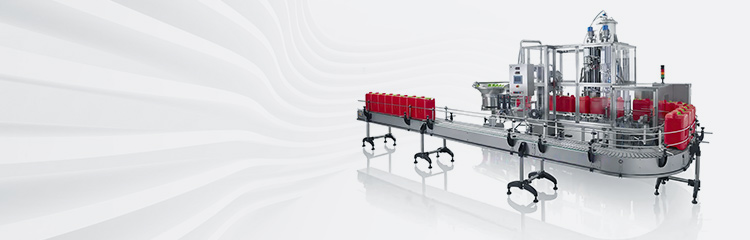

Summary:The semi-continuous polyester batching system adopts the hardware structure of ARCNET industrial standard network and multiple central processing units, and is equipped with 2 industrial-grade computers as operating stations.
Semi-continuous polyester batching process
The weighing and batching system is a production process of direct esterification intermittent polycondensation with PTA and EG as the main raw materials. The direct esterification method is to leave a certain amount of oligomer of BHET in the reactor V-201 in advance, and first add a certain molar ratio of PTA and EG slurry to the esterification reactor V-201 continuously with a certain flow rate, and the reaction is carried out under the clear point. After the end of the esterification reaction, the material is moved into the polycondensation reactor V-401 for polycondensation reaction.
1、Control of slurry preparation
As the slurry from the company's CP (continuous polyester) line, not subject to control of this device, and the molar ratio (mol) is not the same as the process, there is a contradiction, coupled with the device has the characteristics of intermittent production (esterification to polycondensation needs to be guided), the control of slurry with the addition of EG (ethylene glycol) must be articulated so that in the actual control, the metering of the EG is set to be the total amount of slurry for a PID control loop, the speed of the slurry is controlled by the CP (because the CP line needs to adjust the parameters according to the production), the flow direction of the slurry is controlled by the feeding system according to the total amount of the relevant control using a combination of sequential and interlocking, the preparation of slurry and the preparation of EG is fully automatic.
2、Control of esterification internal temperature TI-201 and column top temperature TI-202
In the polyester production process, the control of esterification internal temperature TI-201 and column top temperature TI-202 has been more difficult to deal with, coupled with the inherent shortcomings of some auxiliary processes, many manufacturers tend to use the method of human eyes, but just can't achieve the desired results, this time in the device to make full use of the advantages of the dosage system, the sequence of control, interlock control and complex loop algorithms are perfectly combined together, the program will be According to the current state (some important parameters such as internal temperature, water reception, liquid level, etc.) to know the esterification reaction to the first few steps, and then the implementation of the latest control scheme, which not only makes the process parameters tend to be stable, but also improves the quality of the product.
3、Control of material transfer reactor
The control of material transfer reactor mainly contains three major parts:
① Judge the process of esterification and polycondensation;
② Pressure control;
② Pressure control; ③ Material valve control order and important details.
Since the material transfer reactor adopts automatic material valve, it must be put to good use, instead of just reducing the labor intensity of workers, it should make full use of the advantages of automation. Through the use of fully automatic material guide control, saving the amount of nitrogen, saving the reaction time, to avoid misoperation. In the process, the first to determine the operating conditions of the process, and then make a judgment of the next step in the implementation of the action, the opening and closing of this valve are cumulative time, and can ensure that the material tube of the material is exhausted, thus greatly reducing the slice of the small black spots, the control of the pressure to ensure that the production of safety, but also to ensure that the material can be moved to the reactor adequately, the control of the production of a stabilizing effect.
4、Condensation system control
Previously, the polycondensation control has a lot of human factors, the reaction time of each batch is inconsistent, the vacuum with serious material, and the condenser part also appeared in the phenomenon of blocking, I think that in addition to do some articles on the equipment, the importance of the control can not be ignored. This Thailand project has adopted fully automatic control, the program process is as follows: condensation begins, the first atmospheric pressure for a certain period of time, and then enter the low-vacuum program control sub-program PC401, in the process, at the same time, the temperature TI-401 control, to ensure that the temperature to meet the requirements of the process, the program adopts the four automatic shift control condensation, shift will be based on the temperature, power, vacuum and other parameters to be calculated to find the timing of the shift, by using four automatic shift control condensation, shift will be based on the temperature, power, vacuum and other parameters. The program uses four automatic gear changes to control the polycondensation, the gear change will be based on the temperature, power, vacuum and other parameters to find the timing of the gear change, by monitoring the quality indicators of more than 100 batches of slices, it can be concluded that this program is very feasible.
5、Control of total program of main process
Through many practices and the experience of imported devices using conventional instrumentation for control, combined with the characteristics of the automatic dosage system, the actual control of the place will display colors, "STEP" indicates the specific step digital display, "M" indicates MAN, "A" indicates AUTO, the figure indicates that the first esterification reaction is divided into 11 steps, the first esterification reaction is divided into 10 steps, the polycondensation reaction is divided into 15 steps. "A" means AUTO, the figure indicates that the first esterification reaction is divided into 11 steps, the first esterification reaction is divided into 10 steps, and the polycondensation reaction is divided into 15 steps, and when the program is executed to a certain step, the place will display green, and the step control can be referred to in the "M" state. In the "M" state, the step control can be modified by reference to the reality, and in which automatic and manual control can be carried out at the same time, in full compliance with the requirements of the process operation, the key steps accordingly for a variety of conditions of different interlocking control, resulting in the system features:
1. High reliability
The measurement of the dosage system SNAP components are provided with 4000V photoelectric isolation, the main controller of the MTBF (hour) (Mean Time Between Failure ratio) is 65,500, fully able to meet the current industrial site.
2. High Maintainability
The feeding system in the module are all 5V DC power supply, the system adopts a modular design, modules and terminals are separate, easy to replace the module, digital point modules have LED status indicators, action and failure can be detected intuitively, the controller itself has a diagnostic function, the fault information exists in a fixed register. System configuration using OPTOCONTROL software, the use of flow charts for programming, control instructions using ready-made English instructions, this configuration is not only easy to understand, but also easy to modify, more convenient for users to maintain.
3. Intelligent
For SNAPI / O system, it has all the I / O points can complete the intelligent function, which is the main difference between it and PLC and DCS. For digital points, can be counted, state summing, pulse output, time proportional output, watchdog, etc.; for analog points, you can carry out PID operations, digital filtering, totalization, summing, watchdog, etc.; unit processor also has a response to the event function, interrupt control function.
4. Strong practicality
For a set of on-site automatic feeding system, the detailed control program is very necessary, but the convenience of the configuration is the first. A dosage system can run 32 utility programs at the same time, all programs are processed in parallel, all the circuit adjustment does not take up host resources, and if there is a good local control program, can be compiled into a subroutine, and the program can be transplanted to other configurations, without having to change, which is very important for engineers and technicians, can be used for other aspects of the extra time.