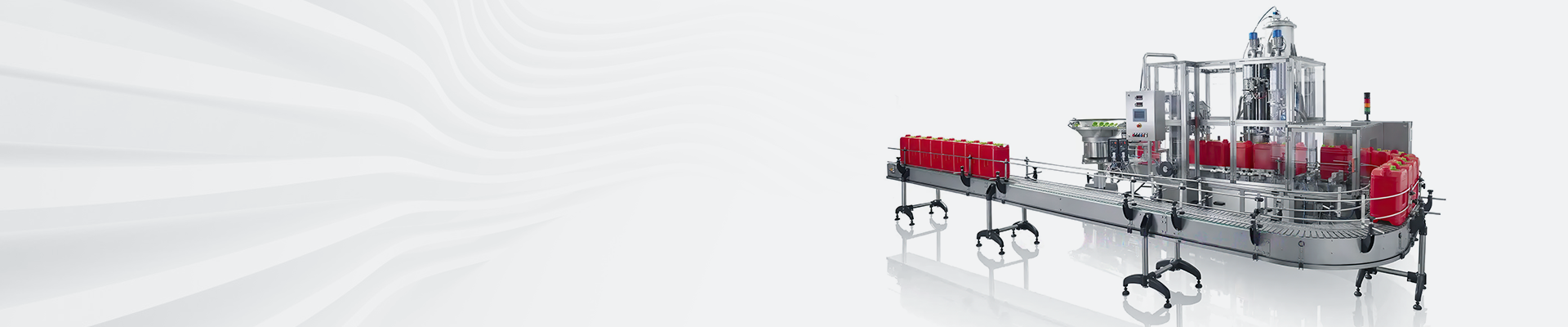
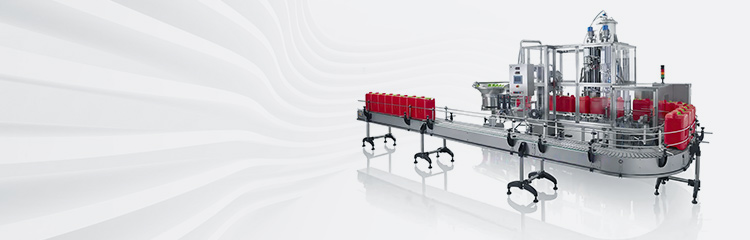

Summary:The batching system sets process parameters (output, thickness, extraction speed), relies on the measurement of parameters by the weighing module and speed measurement module, and automatically adjusts the actual process parameters through intelligent software analysis and calculation, thereby controlling process quality. .
Overview of the resin industry
With the rapid development of the resin industry, the supply of raw materials in the material process rely solely on manual weighing, mixing and dosing this way is difficult to ensure the quality of its work and work efficiency, especially with the rapid development of multilayer co-extrusion technology, resin weighing process of raw material supply has gradually evolved into a collection of raw materials mixing, storage, conveying, mixing and weighing control in the integration of the automated dosage system engineering; on the other hand, today's On the other hand, today's resin processing industry is facing increasingly serious competition and continuous market changes, on how to ensure product quality and competitive position in the market, a high degree of flexibility in production is very and absolutely necessary, and to reduce the cost of the product has become more and more important. Dosing control technology is a new technology that has been rapidly developed to meet the growing demand in the resin weighing industry and has attracted a great deal of attention.
In the resin weighing and molding process, automatic feeding system raw material supply is usually divided into three steps: first of all, the dosage of each component required for weighing, followed by each dosage scale a total of components required for mixing, and finally, the mixed material is supplied to the hopper through the screw plasticizing and mixing weighing. The conventional practice is to weigh offline, that is, how many barrels of the main material (25 kilograms) with how many barrels of auxiliary materials, and then manually stirred into the dosage hopper. Such a practice often produces a series of problems: such as inaccurate weighing; uneven mixing, especially in multi-component dosage additives are not sufficiently dispersed; sometimes due to excessive manual dosage caused by the waste of raw materials and increase in labor costs; can not provide real-time dosage of the weighing of the amount of production, the lack of monitoring of the quality, and so on. Therefore, the use of on-line continuous weighing and mixing is of great significance, which can effectively ensure that the components are weighed according to the predetermined weight percentage and achieve the purpose of mixing uniformity.
On the other hand, the conventional weighing control in the resin weighing process requires the operator to set the speed of the dosage and to make manual adjustments, which does not guarantee a constant weighing output, and over time, due to fluctuations in temperature and pressure, the condition of the filter and other related process changes, the weighing production volume tends to change cyclically, due to the relatively constant speed of the screw and the traction machine, so the The products produced in the meter weight, i.e., the longitudinal direction of the product will be thick and thin deviation, which seriously affects the quality of the product. The following figure shows the change of the meter weight of the product with the fluctuation of the weighing production volume.
There are many factors that cause changes in production, such as: fluctuations in the weighing motor, the characteristics of the resin material added, the structure of the barrel screw and the above process changes in the weighing process, etc., the following from the characteristics of the material briefly talk about the impact of weighing production. Generally speaking, the material added to the dosage according to its size and shape is divided into: powder, granules, trimmings and recycled materials. Powder size is generally less than 0.1mm, finer between 10-100μm called fine powder, between 1-10μm called fine powder, between 0.1-1μm called ultra-fine powder. The size of granule is between 0.5-5mm. Between 0.1-1mm is called pellet, between 1-5mm is called pellet. Edge and recycled materials its size is generally larger than 5mm and its shape is flaky, filamentary or irregularly shaped pellets. Therefore, these different shapes and sizes of materials due to density and bulkiness changes when added to the automatic batching system its fluidity and processability is not the same, in the total weighing often cause weighing instability and lead to product quality decline. Therefore, how to effectively control the material flow (i.e., production volume) of the stability of the weighing process is very important, in relation to the metric weight of the product as well as the quality of the weighed product, reflecting the functionality of the production line. If the flow of material is not stabilized during the production process, in addition to other process parameters, the result is bound to have a great impact on the quality of the product. This is why, in terms of the economic efficiency of the production line and the quality of the product, the accurate recording and detection of the product material flow, as well as the corresponding control to control the meter weight of the product becomes the decisive factor, that is, why the automatic weighing and batching control is used.
The results of the weighing and dosage system in terms of the accuracy of the control were satisfactory, with an accuracy of <±0.5% for different forms of control of the set values and the particular chosen process. The process of change in the accuracy of the product of the automatic dosage system from no meter weight control to the adoption of meter weight control.
Batching in the weighing control that is, meter weight control, usually divided into traction meter weight control mode, dosage meter weight control mode and traction automatic dosage system synchronized meter weight control and so on three kinds of ways.
(1) The traction meter weight control means that the meter weight of the product can be set in advance, and the deviation between the set value and the actual value occurs in the automatic mode and is eliminated by the speed adjustment of the traction machine;
(2) The dosage meter weight control method means that the meter weight of the product can be set in advance, and the deviation between the set value and the actual value occurring in the automatic mode is eliminated by adjusting the speed of the dosage screw. If the dosage is dosed by a dosage unit, the screw speed of this dosage unit will be adjusted.
(3) Dosage meter weight control and traction dosage synchronized meter weight control means that the output of the product can be set in advance and new working points can be adjusted separately, and the controller synchronizes the adjustment of the dosage screw speed and the traction machine speed, so as to keep the meter weight of the product constant. It is mainly used in the production process of recycled materials.
In terms of return on investment, the approach to installing a dosage system focuses on those factors that have a direct impact on the use of raw materials and the quality of the product. Over the years, proven methods abound in terms of raw material and energy savings, in terms of increased productivity and reduced labor and material and scrap costs. Maximum potential savings are achieved by minimizing errors in arm thicknesses, lengths and diameters, and by reducing the metric weight of the product as well as the use of expensive additives. In some cases, savings even average more than 2-5%.
In summary, the use of dosage systems is divided into two main areas, dosage mixing and weighing control (meter weight control). The purpose of batching and mixing is to ensure that the components are mixed homogeneously at the correct weight percentage; weighing control is to ensure that the dosage rate is consistent and that the thickness of the product, or the ratio of each layer, is maintained. The factors for evaluating batching ingredients are categorized into three areas, namely accuracy of batching, homogeneity of mixing, and precision of weighing control. Accuracy of batching refers to the difference between the actual value of the weight percentage of each raw material ingredient and the set value; uniformity of mixing refers to whether the various ingredients are completely dispersed into the mixture; and precision of control refers to the precision of control of meter weight and the ratio between co-extruded layers.
Types of dosing and mixing equipment
Due to the use of volumetric system it exists:
1, must rely on time to adjust the dosage precision;
2、The setting of equipment data needs to be operated by specialized personnel;
3、The formula and processing data need to be converted and corrected;
4, the uniformity of the volume and density of the raw material particles required to teach high. Therefore, the current application in the resin weighing process is relatively rare.
Gravimetric dosage is divided into loss-in-weight and gain-in-weight two dosage methods, due to the use of gravity dosage system approach, it has the following advantages:
1, stable and accurate control;
2, can use a variety of different raw materials;
Automatic calibration function;
4. Simple setup - only takes a very short time;
5, with weight dosage system - not with volume dosage system;
6, Elimination of fuzzy operations;
7. Fast return on investment.
The loss-in-weight dosage method is suitable for weighing high output volumes and providing auxiliary control of multiple blenders used in multi-layer co-extrusion plants, while the weight-in-weight dosage method is suitable for all raw materials with weight dosage having:
1. Extremely high accuracy;
2. Automatic calibration;
3, direct setting of the percentage of each component;
4、Direct setting with dial wheel;
5, operating the machine is simple and so on.
Several typical weighing equipment shao integrated continuous weighing and dosing systems provide the user with high precision dosing using the loss-in-weight dosing function. The principle of operation is to convey the raw materials to the various gravity hoppers by means of a vacuum transfer device, using the principle of loss-in-weight measurement to determine the amount of the various raw material components to be fed. The dosage calculates the percentage of the main ingredient from the gravity dosage to the automatic dosage, which is also measured by its own hopper. In automatic mode, the dosage calculates and controls the rotational speed of the weighing screw by comparing the measured feed quantity with the target value set by the process. When the weighing quantity is changed due to a production target or a process change, the dosage recalculates the percentage of feed speed at the same time, thus guaranteeing the feed quantity.
The GT3, GDC3X00 and ACS5X00/6X00 dosage control systems are available to the customer according to the requirements of the plant.
(1) The GT3 is the smallest dosage system, capable of controlling up to 3 co-extruded dosages and single automatic weighing dosages with 2 additive feeding units;
(2) The GDC3X00 is a moderate control system, capable of controlling up to 1 single weighing line with 1 main ingredient and up to 6 additive feeding units, or a combined co-extrusion line with up to 5 dosage points and up to 9 weighing points (main hopper and additive);
3) The ACS 5X00/6X00 is a complete weighing and feeding control system for lines with 1-10 ingredients and up to 35 feed hoppers.
Its advantages are:
1. No limitation of dosing components;
2. Highly stable dosing by mechanical means;
3, Unaffected by the density of the material;
4, no premixing device is required, no material overflow during operation;
5, dosing system resolution of about 0.1% of the maximum screw feed volume, the minimum feed volume is 250 grams / hour;
6, high stability, fast cleanup, no mixing of raw materials when changing products; 7, can be extremely effective in controlling the proportion of layer thickness of products, as far as possible to reduce the consumption of valuable raw materials.
Continuous loss-in-weight gravity blending dosage
Continuous Loss-in-Weight Gravimetric Blending is used to produce an accurate, homogeneous blend by weighing that quickly compensates for changes in the material due to changes in bulk density. The operator enters the desired blend ratio at the operator's console. Hopper scales for each material are equipped with integral feed screws, and a dosage computer monitors the actual feed rate of each ingredient and maintains the pre-determined blend weight ratios by cyclically adjusting the feed rate of each ingredient. All materials flow into a waterfall mixing chamber for very thorough homogenization. The dosage uses the latest microprocessor technology to fully automate recipe entry, storage and printing, material control and process control, providing excellent stability and ease of use. At the same time the dosage can accurately control the resin weighing process material mixing uniformity, its high precision gravity weighing dosage makes those expensive additives to minimize the amount, and has unsurpassed material mixing uniformity and precision, can adapt to the needs of different applications.
Guardian Batch Gravimetric Dosing Systems
The Guardian Batch Gravimetric Blender is designed for resin processors who want simple operation, high dosage accuracy, uniformity and low cost of ownership, based on the principle of gravity dosage for precise blending of raw materials. The blender is designed to proportionally weigh each component into a main hopper scale, each batch can achieve ±0.02% accuracy through the gravity dosage system and control, after weighing, all the material enters into a stirring mixture chamber to make it fully mixed before resin processing. Therefore, the dosage system has the following characteristics:
(1) Advanced dosing and weighing allows precise control of the amount of each component to be placed in each batch according to preset quantities; instead of averaging multiple feeds to reach a set value, as is usually the case with other batch-type mixing and dosing systems in the industry, each component is dosed with an accuracy of +/-0.02%, according to the highest accuracy settings for mixing and dosing.
2) In addition to precise batch dosing, PCC USA has developed the most completely uniform mixing chamber in the industry. Inadequate mixing can lead to inconsistencies in product performance, such as color changes or other defects.
3) The Guardian® series of mixing dosage is equipped with a built-in cleanout dosage. With a movable discharge chute and separate manual control valve, the mixing dosage can be quickly and easily emptied during material changes.
4) The optional PCCWeb® software allows the user to remotely monitor and control the Guardian® blending system via a web browser on a standard PC. Through the Ethernet interface on the rear of each miniature operator control panel, each blending system can be connected to a local area network (LAN) where each computer can access the data.
5) In addition to combining high precision dosing and complete homogeneous mixing characteristics, it is also easy to operate. Currently the Guardian series of batch gravity mix dosage is available in four sizes: 1.25kg, 2.5kg, 5kg and 12kg batch gravity mix systems. Among them, the 12kg batch gravity mixing system can be used for 2-12 components, and the maximum output range is 1134-2694kg/h for 2-component; 1051-2053kg/h for 3-component; 770-1685kg/h for 4-component; 1685kg/h for 5-component; and 770-1,685kg/h for 5-component. 1685 kg/h for 2-component; 1051-2053 kg/h for 3-component; 770-1685 kg/h for 4-component; 607-1391 kg/h for 5-component; and 501-1197 kg/h for 6-component.
Gravitrol Weigh Control Dosing
Gravitrol Weighing Control dosage allows to maintain a constant weighing output by monitoring in real time the production volume and regulating the dosage screw speed, freeing the operator from those tasks of estimation; in coextrusion lines Gravitrol Weighing Control dosage allows to regulate the output of each dosage unit, thus controlling with high precision the proportion of each layer of the final product. The central computer and operating platform, each hopper scale and the drive control module for each dosage unit. The central computer calculates the actual dosage quantity and correctly adjusts the dosage screw speed to maintain the output of each dosage within ±0.5. For applications requiring control of meter weight (weight of product per unit length), a line speed drive module is added to control the tractor speed and a pulse generator and encoder is used to accurately measure the line speed for closed-loop control.The advantages of Gravitrol's weighing and control of the dosage are:
1) Improved product quality;
2) Reduction of scrap;
3) Maintaining product tolerances and reducing material consumption;
4) Improvement of production repeatability;
5) Reducing start-up and product changeover times;
6) Generate accurate material management reports.
Gravitrol Weigh Control Dosing is one of the best raw material savings solutions in the resin weighing industry, meeting the customer's need for both product quality improvement and raw material savings. It is widely used in blown film, runners, sheets, tubes, profiles, wire/cable, sheathing and weigh coating lines.
Volumetric Mixing and Dosing
Sonner's current volumetric systems for mixing and dosing are available in three sizes: VDEX-II, VDS and VDMI volumetric mixing and dosing. These dosage systems utilize synchronized, digital technology to accurately dosage all of the system's ingredients into the resin molding machine: injection, weighing, and blow molding machines. The precise dosage of all raw materials is based on: the use of correctly sized dosage carousels, special DC motors, and precise control software; synchronized mixing of additives and raw materials in the mixing chamber in accordance with the pre-set recipe system, eliminating the need for traditional mixing devices; and consistent dosage throughputs with the output of the molding machine; in case of discrepancies between the outputs of the molding machine and the dosage setup, the mixing and dosage level modules shut down the entire unit. The entire mixing process of VDEX-II is done continuously through a specially designed static mixing chamber, which minimizes the mixing volume ratio per unit of time, thus ensuring the homogeneity of the mixing of the main raw material and the additive formula.
Gravimetric system mixing
The UM200 is Sonner's most advanced gravimetric batch mixing system. Used for granular, powdery resin raw materials or additives, it is suitable for injection, weighing and blow molding processes.UM200 can precisely control the flow of each set of dispensing valves through the weighing module, using digital technology, to ensure the accuracy of each batch of mixing formulations, with an accuracy of up to 0.1%, and at the same time, save raw material costs and improve product quality; optimized design of the agitator enables the raw materials that have been dosed to be well mixed and the mixer to be fully integrated. The optimized design of the agitator allows for the homogeneous mixing and blending of the dosed ingredients. The UM200 can produce up to 200 kg/h. The compact and modular design of the entire dosage unit ensures that maintenance or replacement of raw materials is effortless, and the raw material silos can be disassembled and removed quickly and easily, taking only a few minutes to clean the raw materials in the machine, minimizing standby time and providing a safe and reliable operation. The UM200 is mounted directly to the inlet of the molding machine and is equipped with various sizes of connecting devices to connect to any type of structural inlet molding machine.
Loss-in-Weight System Mixing
Sonner's current loss-in-weight system mixing dosage is divided into five specifications: GBL-Compact, GBL-Flex, GBL-SS20, GBL-ST22 and GraviL loss-in-weight mixing dosage.
(1) GBL (GraviblendingL)-Compact continuous loss-in-weight system mixing dosage for spherical, cylindrical, granular resin particles proportional mixing system. Each GBL-Compact is equipped with 1-6 precision single-screw conveyor dosage systems in each weighing line. The dosage accuracy is ±0.25%. GBL-Compact can be used in continuous weighing lines with throughputs ranging from 0.5 kg/h to 2,500 kg/h. The dosing and mixing production process is continuous. The flow of raw materials is constantly monitored and calibrated by the Sonner M250 industrial control computer.
2) The GGBL-Flex loss-in-weight system mixing and dosing is designed and manufactured for granular, flowable and non-flowable powders and is suitable for granular, flowable and non-flowable powdery materials.The GGBL-Flex has an optimized modular design in order to solve complex mixing and dosing solutions, allowing the user to maximize the variability of his/her own formulas. Especially for high viscosity, hard-to-flow powdery materials, GBL-Flex adopts the advanced anti-bridging technology "Kneading Dosing" to improve the efficiency of dosing and conveying, and the flexibility of GBL-Flex also lies in the use of advanced integration technology, which allows the user to easily realize the interchangeability of single-screw doser and twin-screw dosers in the same Flex. GBL-Flex can be used as volumetric dosage or loss-in-weight dosage system with dosage accuracy of ±0.25%.
(3) GBL(GraviblendingL)-SS20 is a continuous loss-in-weight system mixing and dosing system for micro-ratio mixing and dosing of spherical and granular resin particles and recycled materials. Each GBL-SS20 can be combined with other weighing and dosing systems. The dosage accuracy can reach ±0.25%. GBL-SS20 can produce from 0.25kg/hr to 25kg/hr, which is suitable for continuous production in weighing lines. The dosing and mixing production process is continuous. The flow of raw materials is constantly monitored and calibrated by the SONNERM 250 industrial control computer.
4) The GBL (GraviblendingL)-ST22 is a continuous loss-in-weight system for the proportional mixing of powders with easy or difficult flow. Each GBL-ST22 can be combined with any other weighing dosage. The dosage accuracy is ± 0.5%. The output of the GBL-ST22 ranges from 0.1 kg/hr to 25 kg/hr, which makes it suitable for use in continuous production weighing lines. The dosing and mixing production process is continuous. The flow of raw materials is constantly monitored and calibrated by the Sonner M250 industrial control computer.
5) GraviL (GravidosingL) is a continuous loss-in-weight dosing system for the precise dosing of liquid raw materials of various viscosities. Widely used in the weighing and molding process, granulation process, GraviL output can be from 0.2kg / h-100kg / h. Continuous dosage and mixing production process is constantly and automatically monitored and calibrated by the Sonner M250 industrial control computer; control accuracy range of ± 0.25%. GraviL dosage system relies on the selection of the correct type of dosage pumps, precision high dynamic response weighing device, and accurate dosage. The GraviL dosage system relies on the selection of the right type of dosage pumps, precise and highly dynamic response weighing devices, and accurate control software to ensure that the entire dosage is constant and accurate throughout the production process.
Gravihopper weighing and control of the dosage.
The Gravihopper weighing and control dosage system is an advanced process quality control standard based on the intelligent dosage principle. Process quality control is achieved through the setting of the process parameters (throughput, thickness, drawing speed), relying on the measurement of the parameters by the weighing module and the speed measuring module, and the automatic adjustment of the actual process parameters by means of an intelligent software analysis and calculation. The output of each layer (Kg/h or g/min) can be pre-set, and in automatic mode, by monitoring the actual speed of the motors, the deviation between the actual output and the set output is eliminated by automatically synchronizing the adjustment of the weighing motors of each layer, thus guaranteeing the same ratio of output for each layer. The Gravihopper is designed as a compact unit and can be combined with Sonner's suction unit and the mixing unit of the weight-increasing dosage system. The accuracy of the Gravihopper is controlled within ±0.5%, with a maximum output of 800 kg/h and up to 8 weighing and dosage systems can be controlled at the same time.
Conclusion
The twenty-first century is the century of environmental protection, environmental issues are increasingly important, resources, energy is becoming more tense, the resin industry has ushered in a new opportunity, but also will be subject to serious challenges, in order to adapt to the requirements of the new era, the resin barrel material in addition to requirements to meet the requirements of the market such as quality and efficiency of barrels, but also need to be further required to save energy and resources, such as barrels of film, containers, sheets to lightweight, thin-walled development, and its The key technology in addition to raw materials and equipment from the technology and precision and other aspects of the enhancement, one of the key points is the application of automatic weighing and dosing system control dosage, which can not only effectively improve the quality of the film, but also in the degree of automation, personnel costs and resource savings, etc. is playing an increasingly important role.