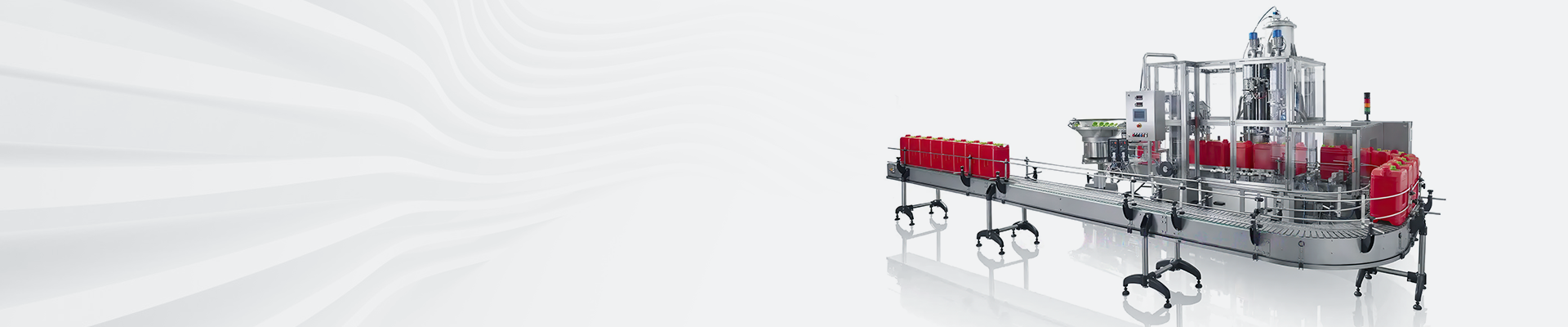
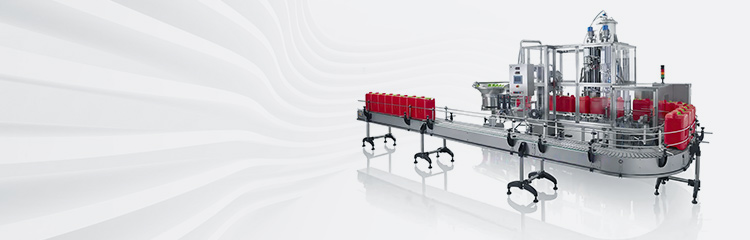
摘要:配料系统通过工艺参数(产量,厚度,引取速度)的设定,依靠称重模块和测速模块对参数的测量,通过智能的软件分析计算,对实际的工艺参数进行自动调整,从而达到控制工艺质量。
概述
随着树脂工业的迅猛发展,物料过程中的原料供给单纯靠人工称重、混合加料这种方式很难保证其工作质量和工作效率,特别是随着多层共挤技术的快速发展,树脂称重过程的原料供给已经逐步演变为集原料的搅拌、储存、输送、混料和称重控制于一体的自动配料系统工程;另一方面,当今的树脂加工行业正面临日趋严重的竞争和持续不断的市场变化,对如何确保产品的品质和市场的竞争地位,在生产中具有高度的灵活性是非常和绝对必要的,而且降低产品的成本也就变得越来越重要了。配料控制技术正是为满足人们在树脂称重行业日益增长的需求而迅速发展起来的一项新技术,引起了人们的广泛关注。
在树脂称重成型过程中,自动投料系统原料供给通常分为三个步骤:首先是对配料所需的每个组分进行称重,其次是将每台配料秤共需的组分进行混合,最后是将混合均匀的物料供给料斗通过螺杆塑化搅拌称重。常规的做法是离线进行配重,即主料多少桶(25公斤装)配辅料多少桶,然后人工搅拌装入配料斗。这样的做法往往会产生一系列的问题:诸如称重不准确;混料不均匀,特别是多组分配料中添加剂分散不充分;有时由于人工配料过多造成原料的浪费和人工成本的增加;无法提供配料实时的称重生产量,对品质缺乏监控等等。因此采用在线连续称重混料具有极其重要的意义,能有效确保各组分按预定的重量百分比配料称重,达到混合均一的目的。
另一方面,在树脂称重过程中常规的称重控制需要操作人员设定配料的转速和进行手动调节,而这并不能保证称重产量的恒定,并且随着时间的推移,由于温度和压力的波动、过滤网的状况及其他相关工艺的变化,称重生产量往往会发生周期性的变化,由于螺杆和牵引机的速度相对恒定,因此,生产的制品在米重上即产品的纵向就发生厚薄偏差,严重影响产品的质量,下图显示了制品米重随称重生产量的波动而变化的情况。
而引起产量变化的因素往往有很多,诸如:称重电机的波动、加入的树脂物料的特性、机筒螺杆的结构和上述中称重过程中的工艺变化等等,下面从物料的特性简单谈谈对称重产量的影响。一般来讲加入到配料中的物料按照其尺寸与形状分为:粉料、粒料、边角料和回收料等。粉料其尺寸一般小于0.1mm。更细的在10-100μm之间的称为细粉料,在1-10μm之间的称为精粉料,在0.1-1μm之间的称为超细粉料。粒料它的尺寸在0.5-5mm之间。在0.1-1mm之间称为颗粒,在1-5mm之间称为丸粒。边角料和回收料其尺寸一般大于5mm,形状有片状、丝状或形状不规则的颗粒等。因此,这些不同形状和尺寸的物料由于密度和松散度变化当加入到自动配料系统中其流动性和加工性就不一样,在共称重时往往会引起称重不稳定而导致产品质量下降。因此,如何有效控制物料流量(即生产量)的稳定在称重过程中非常重要,在涉及到产品的米重以及称重产品的质量方面,体现了生产线的功能性。在生产过程中,除了其他工艺参数外,若物料的流量不能够保持稳定的话,其结果必然对产品的质量产生很大的影响。这就是为何就生产线的经济效益和产品质量方面而言,精确记录并检测产品物料流量,同时做好相应的控制以控制产品的米重成为决定性的因素,也即为何要采用自动称重配料控制的原因。
称重配料系统在控制的精度方面,其结果是令人满意的,对于设定值和特定所选用的工艺的不同控制形式来说,其精度为<±0.5%。自动配料系统从无米重控制到采用米重控制后制品精度的变化过程。
配料在称重控制即米重控制方面,通常分为牵引米重控制方式、配料米重控制方式和牵引自动配料系统同步米重控制等三种方式。
1)牵引米重控制方式是指对产品的米重可预先设定,在自动模式中发生在设定数值与实际数值之间的偏离,通过牵引机的速度调整予以消除;
2)配料米重控制方式是指对产品的米重可预先设定,在自动模式中发生在设定数值与实际数值之间的偏离,通过配料螺杆速度的调整予以消除。如果配料由一个配料装置来配料,则将对这个配料装置的螺杆速度进行调整。
3)配料米重控制和牵引配料同步米重控制方式是指对产品的产量可预先设定,并可分别调整新的工作点,控制器同步调整配料螺杆速度和牵引机的速度,从而使产品的米重保持恒定。主要应用在回收料的生产过程中。
在投资回报上,对于安装一套配料系统其考虑方法主要集中在这些直接对原材料的使用和产品质量直接产生影响的因素。多年来,在原料和能源节约方面,在增加生产率方面和降低人力物力以及和碎料成本方面,已经证明了的方法比比皆是。最大潜能的节约就是使臂厚、长度和直径的误差最小化,并减少产品的米重以及使用昂贵的添加剂。在有些情况下,节约甚至平均超过2-5%。
综上所述,配料系统其用途主要分为两个方面,即配料混合与称重控制(米重控制)。配料混合目的是确保各组分按正确的重量百分比,达到混合均一的目的;称重控制是保证配料速率一致,保持产品的厚度或每层的比例。评估配料配料的因素分为三个方面,即配料的准确性、混合的均匀性以及称重控制的精确性。配料的准确性是指每种原料成分的重量百分比实际值与设定值的差异;混合均匀性是指各种成分是否完全分散到混合物中;控制的精确性是指米重和共挤层间比例的控制精度。
配料混合设备的种类
由于采用体积系统它存在着:
1、必须依靠时间调整配料精度;
2、设备数据的设置需专业人员操作;
3、配方和加工数据需要进行转换和矫正;
4、对原料颗粒的体积和密度的均匀度要求教高。因此目前在树脂称重过程中应用较为少见。
重力式配料分为失重式和增重式两种配料方法, 由于采用重力配料系统方式,它存在着以下优点:
1、稳定的准确控制;
2、可使用各种不同的原料;
3、自动校准功能;
4、设置简单-仅需极短的时间;
5、用重量配料系统-不是用体积配料系统;
6、消除模糊作业;
7、快速的投资回报率。
其中失重式配料方式适用于高产出量的称重生产和提供对用于多层共挤设备的多台混料机的辅助控制;而增重式配料方式适用于所有原料用重量配料具有:
1、极高的准确率;
2、自动校正;
3、直接设置各组分的百分比;
4、直接用拨轮设置;
5、操作机器简单等特点。
几种典型的称重设备绍集成的连续称重定量上料系统为用户提供了使用失重配料功能的高精度配料。其工作原理是将原料通过真空传送装置输送到各个重力料斗,采用减重测量原理,确定各种原料组份的给料量。该配料计算由重力配料到自动配料的主要原料的百分比,该主要原料给料量同时也被其自有的料斗测量出重量。在自动模式下,通过给料量测量值和工艺设定的目标值比较,配料计算和控制称重螺杆的转速。当称重量由于生产目标或工艺改变时,配料同时重新计算给料速度百分比,从而保证给料量。
根据设备的要求为用户提供GT3、GDC3X00和ACS5X00/6X00配料控制系统。
1)GT3属最小配置的配料系统,最多能控制3个共挤配料和带2个添加剂喂物料单元的单自动称重配料;
2)GDC3X00适中控制系统,最多能控制1个主原料和最多6个添加剂喂物料单元的单称重生产线,也可控制最多5个配料和最多9个称重点(主料斗和添加剂)的组合共挤生产线;
3)ACS5X00/6X00属全面的称重上料控制系统,能适用于1-10个配料和最多35个进料斗的生产线。
其优势在于:
1、定量给料组份没有限制;
2、通过机械方法高度稳定定量给料;
3、不受材料密度影响;
4、无需预混料装置,运行中无原料溢出;
5、配料系统分辨率约为最大螺杆给料量的0.1%,最小给料量是250克/小时;
6、稳定性高,清理快速,改变产品时没有混合原料;7、能够极其有效地控制制品的层间厚度比例,尽可能降低贵重原料的消耗。
连续失重式重力混料配料
连续失重式重力混料是用于通过称重生产出精确、均匀的混料,能快速补偿物料因容积密度改变而产生的变化。操作人员在操作台上输入期望的混合比例,每种物料的料斗秤都配有完整的进料螺杆,配料计算机监控每种成分的实际进料速度并通过周期性调节每种成分的进料速度来维持事先设定的混料重量比例。所有物料都流入瀑布式的混合室进行十分彻底的均匀混合。该配料使用最新的微处理技术,配方的输入、储存及打印,物料控制及过程控制全部实现完全自动控制,具有卓越的稳定性和易用性。同时该配料能精确地控制树脂称重过程物料混合均一性,其高精度的重力称重配料使得那些昂贵的添加剂用量减少到最少,并且具有无法超越的物料混合均一性和精度,能适应不同应用的需要。
Guardian系列分批式重力混料配料
Guardian系列分批式重力混料配料是专门为那些希望操作简单、高精度配料、混合均匀、低成本的树脂加工者设计的,其原理是通过重力配料来实现原料的精确混合。该混料机设计成可以按照比例称重每一组分进入一个主要的料斗秤,每种物料通过重力配料系统和控制,每批次可以达到±0.02%的精度,在称重过后,全部物料进入一个搅动的混合物料室使其在进行树脂加工前得到充分的混合。因此,该配料系统具有如下特点:
1)先进的配料和称重可根据预设的数量精确地控制每批次每个组份的投放量;而不是像行业内其他分批式混料配料系统那样,通常通过平均多次投料达到设定值,按混料配料最高的精度设置,每个组份以+/-0.02%的精确度来配料。
2)除了精确的分批次配料外,美国PCC公司开发出行业内最完全均匀的混料室。不够充分的混料易导致产品性能的不一致,如颜色发生变化或带来其他缺陷。
3)Guardian®系列混料配料同时配有内置的清料配料。由于配有一个活动式的排料槽和独立的手动控制阀,混料配料可在换料时快速又简易地完成清料工作。
4)使用可选的PCCWeb®软件,用户可在标配PC上通过网络浏览器远程监控Guardian®混料系统。通过每个微型操作控制面板后部的以太网接口,每台混料系统能被接入到一个局域网中,网内的每台计算机都可以访问到相关数据。
5)除结合了高精度的配料和完全均匀的混合特性外,又易于操作。目前Guardian系列分批式重力混料配料共有四种规格:1.25kg、2.5kg、5kg、12kg分批式重力混料系统。其中12kg规格分批式重力混料系统可达2-12个组份,最大产量范围:2组分为1134-2694kg/h;3组分为1051-2053kg/h;4组分为770-1685kg/h;5组分为607-1391kg/h;6组分为501-1197kg/h。
Gravitrol称重控制配料
Gravitrol称重控制配料可通过实时监控的生产量和调节配料螺杆转速来保持称重产量的恒定,并把操作人员从那些单考估算的工作中解脱出来;在共挤生产线中Gravitrol称重控制配料可调节每台配料产量,从而对最终产品每层的比例实现高精度的控制。中央计算机及操作平台、每台料斗称和用于每台配料的驱动控制模块。中央计算机计算出实际的配料用料量,正确地调整配料螺杆转速,保持每台配料的产量维持在±0.5之内。对于那些要求控制米重(每单位长度产品的重量)的应用,需要增加一个线速度驱动模块以控制牵引机速度和一个脉冲生成器及编码器用于精确地测量生产线速度从而实现闭环控制。Gravitrol称重控制配料的优势在于:
1)提高产品的品质;
2)减少废品;
3)维持产品的公差,减少物料的消耗量;
4)提高生产的重复性;
5)缩短开机和产品更换时间;
6)生成精确的物料管理报告。
Gravitrol称重控制配料是树脂称重行业最佳的原料节省方案之一,能满足客户对产品质量提高和原材料节省的双重需求。广泛应用于吹膜、流涎、片材、管材、型材、电线/电缆、护套及称重涂覆生产线。
体积式混合配料
Sonner公司目前体积式系统混合配料分为三种规格产品:VDEX-II、VDS和VDMI体积式混合配料。该配料系统采用同步,数字式技术,能够精确的配料系统原料添加到树脂成型主机里:如注射设备,称重设备,吹塑成型设备。精确配料系统所有原料的添加量主要是依靠:使用正确尺寸的配料转盘,特殊的DC马达以及精确的控制软件;添加剂与主原料按照预设定的配方系统,在混合腔同步均匀混合,无需采用传统的搅拌装置;通过预设产量使之与成型主机产量保持一致,一旦成型主机和配料设定产量不一致,混合料位模块会关闭整个装置。VDEX-Ⅱ整个混合过程是通过特殊设计的静态混合腔连续的完成的,使得混合容积比在单位时间内最小,从而保证了主原料与添加剂配方混合的均匀性。
增重式系统混合配料
UM200增重式系统混合配料是目前Sonner最先进的重量式批次配料混合装置。用于颗粒状,粉状树脂原料或添加剂的配料混合,适合注射工艺、称重工艺、吹塑工艺。UM200通过重量式称重模块,利用数字式技术,能够精确的控制每一组分配料阀的流量,保证每一批次混料的配方的准确,精度可达0.1%,同时节约原料成本提高产品质量;优化设计的搅拌器能够使已经配料的原料得到充分的均匀搅拌和混合。UM200产量最大可达200kg/h。整个配料紧凑模块化式设计确保维修保养或原料的更换毫不费力,原料料仓可以简单快速地拆卸并移出,只需花费数分钟时间清洁设备里的原料,使待工时间减少至最低,并且安全,可靠。UM200直接安装在成型主机入料口上,并且配备各种尺寸规格的连接装置与任何一种结构入料口成型主机连接。
失重式系统混合配料
Sonner公司目前失重式系统混合配料分为五种规格产品:GBL-Compact、GBL-Flex、GBL-SS20、GBL-ST22和GraviL失重式混合配料。
1)GBL(GraviblendingL)-Compact连续失重式系统混合配料,适用于球状,圆柱状,颗粒树脂粒子比例混合系统。每一款GBL-Compact在每一条称重生产线上配置1-6个精密单螺杆输送配料系统。配料精度可达±0.25%。GBL-Compact的产量可从0.5kg/h-2,500kg/范围,可适用于连续生产的称重生产线上。配料混合生产工艺过程是连续的。原料的流量不断的被SonnerM250工业控制电脑监视和校准。
2)GGBL-Flex失重式系统混合配料专业为混配造粒工艺设计制造,适用于颗粒状、易流动及不易流动的粉状原料的配料系统。GBL-Flex采用优化模块化设计,以解决复杂的混配造粒工艺方案,用户可以最大限度的变化自己的工艺配方。特别在处理高粘度,不易流动的粉状原料方面,GBL-Flex采用先进的防架桥技术“揉动配料”提高配料输送的效率。GBL-Flex的灵活性还在于采用先进的整合技术,在同一台Flex里,用户可轻松的实现单螺杆配料器和双螺杆的互换,降低客户的投资成本。GBL-Flex即可以作为体积式配料使用,亦可以作为失重式配料系统,配料精度可达±0.25%。
3)GBL(GraviblendingL)-SS20是连续失重式系统混合配料适用于球状、颗粒树脂粒子、再生原料的微量比例混合配料系统。每一款GBL-SS20与其他称重配料任意组合。配料精度可达±0.25%。GBL-SS20的产量可从0.25kg/hr-25kg/hr的范围,可适用于连续生产的称重生产线上。配料混合生产工艺过程是连续的。原料的流量不断的被SONNERM250工业控制电脑监视和校准。
4)GBL(GraviblendingL)-ST22是连续失重式系统混合配料适用于易流动或不易流动粉状的比例混合配料。每一款GBL-ST22可与其他称重配料任意组合。配料精度可达±0.5%。GBL-ST22的产量可从0.1kg/hr-25kg/hr范围,可适用于连续生产的称重生产线上。配料混合生产工艺过程是连续的。原料的流量不断的被SonnerM250工业控制电脑监视和校准。
5)GraviL(GravidosingL)是连续失重式定量给料配料,适用于各种粘度液体状原料的精确配料。广泛地应用在称重成型工艺,造粒工艺。GraviL的产量可从0.2kg/h-100kg/h。连续的配料混合生产工艺过程不断的被Sonner公司M250工业控制电脑自动监视和校准;控制精度范围为±0.25%。GraviL配料系统依靠选取正确类型的配料泵,精密的高动态响应称重装置,以及精确的控制软件,保证整个配料在生产工艺中恒定和准确。
Gravihopper称重控制配料
Gravihopper称重控制配料系统是基于智能的配料原理而建立的一种先进的工艺质量控制标准。通过工艺参数(产量,厚度,引取速度)的设定,依靠称量模块和测速模块对参数的测量,通过智能的软件分析计算,对实际的工艺参数进行自动调整,从而达到控制工艺质量。对每一层产品产量(Kg/h或g/min)可预先设定,在自动模式中通过监测马达实际速度,根据实际产量与设定产量的偏差,通过自动同步调整每一层称重马达予以消除,从而保证每一层称重产量比例一致。Gravihopper的结构设计为紧凑组合式,并且可以与Sonner公司的吸料装置及增重式配料系统混合装置配合使用。其精度控制在±0.5%以内;最大产量可达800kg/h;最多可同时控制8个称重配料系统。
结束语
二十一世纪是环保世纪,环境问题日显重要,资源、能源更趋紧张,树脂行业既迎来了新的机遇,同时也将接受严峻的挑战,为适应新时代的要求,树脂桶装材料除要求满足市场桶装质量和效益等要求之外,还需进一步要求节约能源和资源,如桶装薄膜、容器、片材向轻量化、薄壁化发展,而其关键技术除了从原料和设备的技术与精度等方面提升外,其中关键的一点是自动称重配料系统控制配料的应用,它不但能有效提高薄膜的品质,而且在自动化程度、人员成本和资源节约等方面扮演着越来越重要的角色。