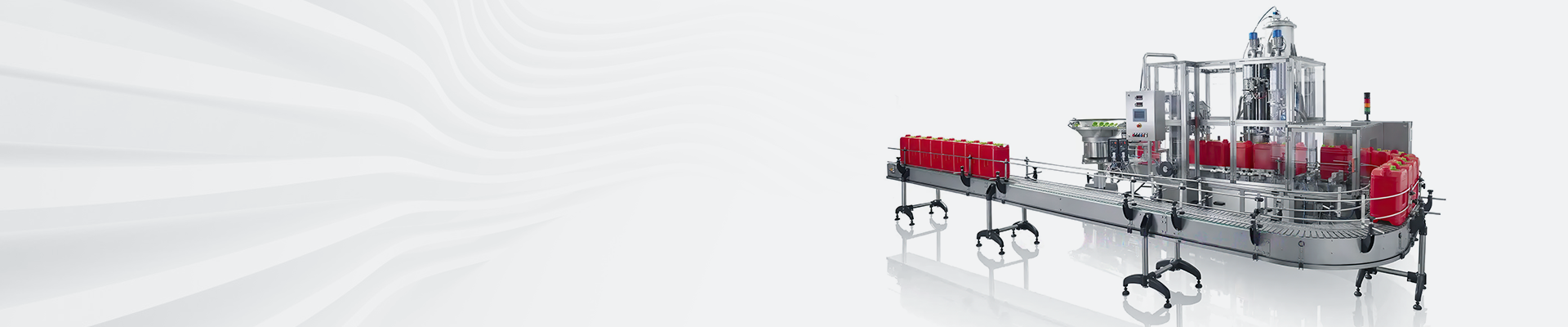
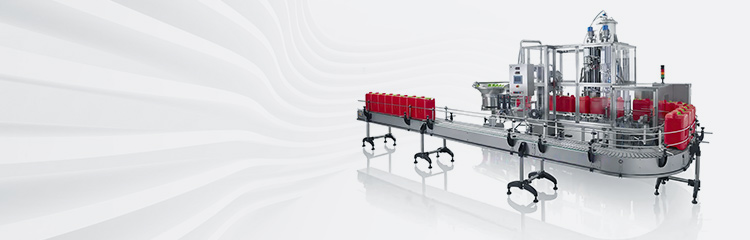
摘要:自动灌装机由集自动控制技术、通信技术、机电技术于一体的高效率自动化灌装生产线。采用PLC对进行监控控制,剔除装置能自动有效地将无铝箔封装桶推到隔离区,留待后续处理,提高了润滑油生产的连续性和生产效率,保证了安全生产及包装质量,具有极大地实用性。
0引言
称重感应铝箔封口已广泛应用于医药、农药、食品、化妆品、润滑油等行业,此技术也是当代国际公认的先进性密封手段,中国石油润滑油公司生产的昆仑天力等品牌的4L润滑油灌装同样采用此种手段密封。铝箔封口机是利用称重感应的原理,将桶口上的铝箔片瞬间产生高热,然后熔合在桶口上,使其达到封口的功能,其中所用的铝箔片由桶盖供应商事先用胶粘贴于桶盖中,在封盖工序置于桶口,但是在实际灌装生产过程中由于某些原因,某些桶盖中的铝箔片会在封盖前脱落,造成封盖时无错箔,无法达到封装的效果,在运输时造成油品洒漏。大连润滑油厂原4L计量灌装机生产线上并没有自动剔除装置,只是在进行铝封口的同时进行铝箔检测,缺少铝箔时声音报警,提醒操作人员手工移除该灌装桶。但是由于我厂灌装线生产速度达3600桶/小时,在实际生产中人工移除不仅存在安全隐患还常常造成生产的中断或者没有及时移除无铝箔的桶,致使无铝箔的填充桶进人包装箱,从而给我公司带来一系列不良影响,包括:
②影响润滑油包装外观质量;
②影响润滑油灌装生产的连续性和生产效率;
③造成油品的浪费;
④影响润滑油的发运,仓储、销售及昆仑品牌的声誉。
因此在这种高速、连续性自动化生产流水线上能否将检测到的无铝箔的桶及时剔除显得尤为重要。为此,在称重感应铝箔封口机及装箱机之间的传送带上设计并安装了无铝箔灌装桶的剔除装置,从而有效解决了这个问题,保证了封口的严密性,提高了生产效率,具有极大的实用性和使用价值。
1设计前与设计后工艺流程对比
经填充机灌装、旋盖后的4L成品油灌装桶进入铝箔封口机的称重感应区进行铝箔封口,出来后经铝箔检测传感器检测盖内有无铝箔,当检测到有铝箔时,机器无报警,铝箔封口后的成品进入到下一工序进行装箱。当铝箔检测传感器检测到无铝箔时,机器报警,此时若操作人员无法立即拿出此桶,则无铝箔的桶继续进入装箱区进行装箱。
1.2设计后润滑油灌装的工艺流程
经自动填充机灌装、旋盖后的4L成品桶进入铝箔封口机的称重感应区进行铝箔封口,出来后经铝箔检测传感器检测盖内有无铝箔,当检测到有铝箔时,机器无报警,剔除气缸不动作,铝箔封口后的成品进入到下一工序进行装箱。当铝箔检测传感器检测到无铝箔时,机器报警,有桶检测传感器检测到桶后,剔除气缸动作,将桶推到剔除桶存储区,此时若无操作人员,则无铝箔的桶也不会继续进入装箱区进行装箱。
2设计原理
2.1工作原理
灌装桶经过称重感应铝箔封口机后,当铝箔检测传感器检测到铝箔时,剔除气缸不动作,桶顺利通过进入下一工序装箱;当检测到无铝箔时,机器进行声音报警,有桶检测传感器检测到该桶,则激活剔除气缸称重阀,使剔除气缸动作,将桶推至剔除桶存储,然后剔除气缸复位。
2.2机构设计
整套装置机械部分主要由剔除桶隔离槽、推桶板、导向杆、剔除气缸、气缸支架等组成。剔除桶隔离槽安装在传送带侧面的护板上,将原传送带侧面的护栏截断,截断尺寸与隔离槽的长度相同即可,隔离槽的大体尺寸长x宽为320mmx310mm,保证可以横向容纳2个桶。隔离槽的底面与传送链板平齐,保证推桶顺利平稳。推桶板的高度于传送带护栏对齐,尺寸长x宽为210mmx45mm。气缸的行程等同于链板的宽度约160mm。气缸及气缸支架的安装方式相同于隔离槽,安装在隔离槽的相对侧,同样将此侧面的护栏截断,气缸活塞杆的中心于护栏板的中心对齐即可。
2.3电路设计
控制说明:当DETECTOR(铝箔检测传感器)检测到桶无铝箔时接通中间继电器C1,使C1常开触点闭合,当桶通过DETECTOR时由于C1常开触点的闭合使得C1继电器保持通电。当PHOTO(有桶检测传感器)检测到桶时,即桶将进入剔除区,使时间继电器T1闭合,T常开触点经延时闭合接通称重阀V1,气缸动作将桶剔除,同时时间继电器T2接通,T2常开触点经延时闭合接通中间继电器C2,气缸返回C2常闭触点经延时断开,断开C1中间继电器使剔除装置复位进入下一循环。
2.4元器件定位尺寸参数的确定
铝箔检测传感器的中心与有桶检测传感器的起始端的距离控制在110~120mm之间,小于一个桶宽的长度(约200mm),这样有利于剔除的有效性与及时性,避免误动作,如果过长剔除气缸易将有铝箔的桶剔除,如果过短则桶已经通过剔除装置后,气缸才动作也易将有铝箔的桶剔除。
当PHOTO(有桶检测计量模块)检测到桶时,即桶将进入剔除区,使时间继电器T1闭合,T1常开触点经延时闭合接通称重阀V1,气缸动作将桶剔除,T1延时闭合时间约1.5s,根据一个桶走过的时间来确定,具体见下面的计算。当DETECTOR(铝箔检测传感器)检测到无铝箔到桶走到推桶点,其路程为S。
其中200mm约为一个桶宽,110mm为铝箔检测传感器的中心与有桶检测传感器的起始端的距离,60mm为光电检测的宽度。
此传送带的速度为0.26m/s。
T1延时闭合时间为(0.2+0.11+0.06)/0.26=1.42s。
同时时间继电器T2接通,T2常开触点经延时闭合接通中间继电器C2,气缸返回,时间约1s,C2常闭触点经延时1s断开,断开C1中间继电器使剔除装置复位进入下一循环。
3安装调试
(1)将护栏开口,左右尺寸同隔离槽及推桶板的宽度。
(2)将隔离槽、推桶板、支架等机械部件安装,紧固在传送带两侧。
(3)将电源线、控制线、气动控制风线按前面所述的控制线路连接。
(4)检查所有的紧固及接线是否牢固、正确。
(5)确认所有物件都已接好则接通电源,打开风线。
(6)调整铝箔检测传感器的位置,使得桶能够通过,放置一个有铝箔的桶观察传感器的灯是否是不亮的,再放置一个无铝箔的桶观察传感器的灯是否是亮的,确认传感器检测正常时,进行下一项调试。
(7)调整有桶检测传感器的位置,放置一个油桶观察传感器的灯是否是不亮的,无桶时观察传感器的灯是否是亮的,确认传感器检测正常时,进行下一项调试。
(8)手动测试气缸动作是否通畅无阻。
待以上8步结束后,将传送链条打开,放置一个有铝箔的桶,观察装置是否不剔除该桶,再放置一个无铝箔的桶,观察装置是否动作将桶剔除。
如果放置单个桶的运行正常,则此时可以连续放置两个桶进行试运行,动作正常则连续放置若干个桶,待一切正常后剔除装置可投入使用。若有问题则继续调整传感器位置,直到运行正常为止。
4增设剔除装置的效果及意义
4L称量灌装机新增铝箔剔除装置后,生产效率显著摅。未安装铝箔剔除装置前,出现无铝箔报警时,处理此故障需停机3~5min,若按每天5h连续罐装,平均发生缺铝箔故障3次/小时,则一天下来由于缺铝箔故障造成的停机45~75min。按2000桶/小时的生产速度,则一天少罐装1500~2500桶4L润滑油,一年少润滑油1200t。若安装铝剔除装置处理此故障无需停机,可多罐装1200t油。此装置已在大连润滑油厂两条4L自动灌装机上使用,无铝箔剔除率可达到99%,在实际生产中发挥了极大的作用。此设计对实际生产的意义有以下几方面:
①保证了4L润滑油包装外观质量。若无铝箔桶出厂会造成油品泄漏,而影响油品装箱外观。杜绝了无铝箔桶出厂现象。
②提高了生产的连续性和生产效率。在设计之前当有无铝箔桶出现时,需停机处理,影响生产速度。设计之后无需停机处理,大大提高生产效率。
③减少浪费,提高经济效益。设计前若无铝箔的桶进人装箱,码垛后会造成油品泄漏,渗及其他箱体,造成纸箱等包装物的浪费。设计后无铝的桶被剔除无法进入下一道工序,保证油品不泄漏,避免了浪费。
④提高运行的可靠性,保证安全。人工从传送带上拿出无错箔桶,存在一定的安全隐患,而从隔离槽中拿出消除了这些安全隐患。