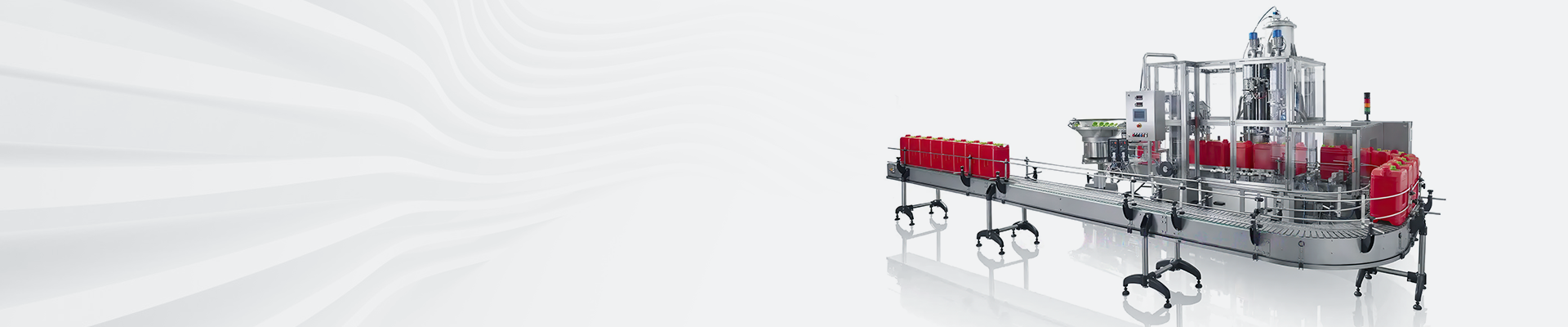
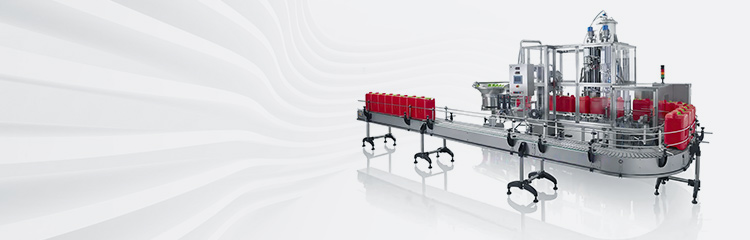

Summary:Compared with the products of other processes, dry process aluminum fluoride process has the advantages of short process, quick effect, and high main content of the product, low moisture, and high stacking ratio, and the new production capacity has been larger in recent years. However, the control level of each manufacturer varies greatly, and the process control of its main key equipment reactor is the main core influence factor. This paper mainly analyzes the dosing of the reactor for theoretical calculations, and the temperature distribution of the reactor furnace to put forward the next step in the control and improvement of the proposal.
Dry aluminum fluoride is mainly used in the aluminum electrolysis industry, is a kind of aluminum electrolysis co-solvent, used to adjust the molecular ratio of electrolyte in the electrolysis tank. In the dry aluminum fluoride production process, the reactor is mainly used for fluorite powder (more than 97% of calcium fluoride and sulfuric acid reaction. The reaction between sulfuric acid and fluorite powder is a heat-absorbing reaction, and the heat required for the reaction is provided indirectly through natural gas combustion.
At present, the specifications of the reactor used in the dry process aluminum fluoride industry are 3.3m*33m, and the reaction of materials in the reactor is divided into three stages. The first stage of mixing and pre-reaction section, is counted from the feed end of the reactor to the reactor 7 meters of the interval, the material in this interval of the stopping time of 60 minutes, fluorite powder decomposition rate of 78%; the second stage of the reaction section, is the reactor 7-25 meters of the interval, known as the reaction section, the material in this section of the stopping time of 62 minutes, fluorite powder decomposition rate of 18%; the third stage of the drying section, is 25-33 meters of the reactor, the reaction section is called the reaction section, the material in the section of 62 minutes, fluorite powder decomposition rate of 18%; the third stage of the drying section. The third stage of drying section is the interval of 25-33 meters in the reactor, the reaction of fluorite powder and sulfuric acid in this stage has been stopped.
The most important control index of the dosing control system is the content of calcium fluoride in the by-product fluorine gypsum, and the materials in the reactor go through three different physical states, i.e. paste, thick material and granular. A plant according to the actual production situation, analyzed the impact of the tailing control factors are shown in the following figure 1. Figure 1 of the fishbone diagram from the human, machine, material, law, the environment factors analyzed the impact of the tailing factors, which can be excluded from the human, machine, material and other factors in a timely manner, but the process control of the temperature and dosage is a complex interplay between the system, the main focus of this paper is to explore the impact of the tailing control indicators of the key links in the process factors, that is, the reactor dosing and Temperature control.
1. Calculation of reactor dosage
Dry aluminum fluoride reactor is mainly sulfuric acid and calcium fluoride reaction, the reaction equation is: CaF, +H, S0, = Cas0, + +2HFt. Generally in the production of dry aluminum fluoride, the first to set the amount of fluorspar powder, and then calculated according to the above equation to get the calcium fluoride and sulfuric acid ratio. And the sulfuric acid used in the dry system is the concentration of 98% and 105% of the acid is calculated to get the respective theoretical dosage to ensure that the concentration of the acid entering the reactor can reach 100%, improve the reaction efficiency and reduce the corrosion of the reactor. In the dosing system, the dosing of the reactor is very important, not only affecting the reaction efficiency of the reactor, the site environment, but also affecting the length of the equipment life cycle. The dosage of the reactor mainly refers to the dosage of fluorite powder and sulfuric acid, and the dosage of sulfuric acid and nicotinic acid needs to be calculated according to the composition of the raw material fluorite powder. With an annual output of 30,000 tons of dry production line as the basis for fluorite feeding take 6.5 tons / hour, the dry dosage of theoretical calculations. Calculation of the data used in the production of a plant to the actual data of the laboratory shall prevail. Which fluorite powder in the composition of the indicators are shown in Table 1 below, the calculation of other indicators needed to see the following Table 2.
Table 1 Fluorite in the content of various components
Item: CaF2; Si02; Cac0; B0
Contents: 97.40%; 1.0%; 0.50%; 0.2%
Table 2 Other indexes
Sulfuric acid/%: nicotinic acid/%; free S0 in nicotinic acid, /%; tailing slag sulfuric acid content/%; tailing slag calcium fluoride content/%
98%: 97.40%; 23%; 0.80%; 0.2%
(1) The amount of sulfuric acid consumed by each component in fluorite
Assume that the total amount of sulfuric acid consumed by calcium fluoride in fluorite is X1 and the total amount of sulfuric acid consumed by calcium carbonate is X2.
①Total amount of sulfuric acid consumed by calcium fluoride in fluorite CaF+H, S0=CaS01+2HFt7898
6500 * 97.4% - 1.7 * 6500 * 2% X1 according to the equation to solve the total amount of sulfuric acid consumed by calcium fluoride: X1 = 7677kg.
② total amount of sulfuric acid consumed by calcium carbonate in fluorite Cac0+Hs0-CaS04+C0+H0
100986500 * 0.5% X2 according to the equation to solve the total amount of sulfuric acid consumed by calcium carbonate is: X2 = 318.5Kg.
(2)The total amount of un-reacted sulfuric acid in the tailing slag The total amount of un-reacted sulfuric acid in the tailing slag: 1.7*6500*0.8%=88.4Kg.Therefore, the total amount of sulfuric acid consumed into the reactor system is: 7677+318.5+88.4=8083.9Kg, (1.7 is the theoretical data for the reactor material accounting).
(3) Calculation of the total amount of sulfuric acid
The principle of sulfuric acid dosing is to ensure that the total amount of 100% sulfuric acid is 8083.9Kg under the premise of the free S0 in the fuming acid, combined with the 98% acid that enters the system, the water brought in by the fluorite raw material and the water produced by the reaction.
Assuming that the amount of 98% acid in the feed acid is X and the amount of nicotinic acid is Y, the following equation is obtained
98%*X+105%*Y=8083.9 The total amount of niacin to be consumed for the water brought in by the raw material is calculated:
① Moisture brought into the system by sulfuric acid: (1-98%)X=0.02*X;
② Fluorspar brought into the system of water: 6500 * 0.2% = 13;
(iii) The water produced by the reaction, assuming that the water produced by the silica reaction is H1.
For the conversion rate of silica in the reaction, solve the equation to get H=31.2Kg.
Solve the equation to get H2 = 5.85Kg.
The total amount of water produced by the reaction is: H1+H2=37.05Kg.
The total moisture in the system is: 0.02X+13+37.05=0.02X+50.05.
The total moisture in the feeding system into the reactor and the S03 in the nicotinic acid that enters the system are exactly combined into 100% sulfuric acid.
According to the theoretical calculation, the theoretical dosage ratio should be: (2.773+1.530)*1840/6500=1.22, sulfuric acid and nicotinic acid acid ratio is: 2.773/1.530=1.81:1. But in practice, due to the system's sealing and other factors, and because of the pre-purification of the acid moisture in the range of 15%-19%, in the calculation is not taken into account, the calibration of the two parts of the consumption of nicotinic acid consumption Therefore, the actual dosage of nicotinic acid than the theoretical calculation of the dosage to be on the large side, the general actual production of sulfuric acid and fluorite powder dosage ratio between 1.22-1.25.
2. Reactor temperature control
The reaction efficiency of the reactor, in addition to the impact of the dosage, there is an important factor is the temperature distribution control of the reactor. Gas hot air system consists of gas combustion device, hot air furnace, high-temperature air duct, return air duct, high-temperature fan, regulating dampers and other equipment and structural components, as well as electrical and automatic temperature control system. After the gas is fully burned in the hot air furnace, it is mixed with 400-450℃ hot air sent by high temperature fan in the mixing box at the end of the hot air furnace to form 650℃ hot air, which enters into the inlet of hot air of the reactor through 4 air inlets under the effect of positive pressure of high temperature ducts and is recycled and reutilized by the suction air inlet of the high temperature fan through the return air ducts after the indirect heat exchanging between the wall of the furnace and the materials. Because the material in the reactor is divided into four stages of reaction, each section of the reaction requirements and mechanisms are different, the furnace temperature requirements of each section of the reactor are also different, the reactor reaction and the control of the good and bad, can be directly through the by-product of fluorine gypsum slagging indicators and properties to react.
A plant for dry aluminum fluoride reaction furnace temperature gradient control, conducted a staged experiment. In order to eliminate other factors affecting the accuracy of the experiment, the following factors were always stabilized during the experimental phase: