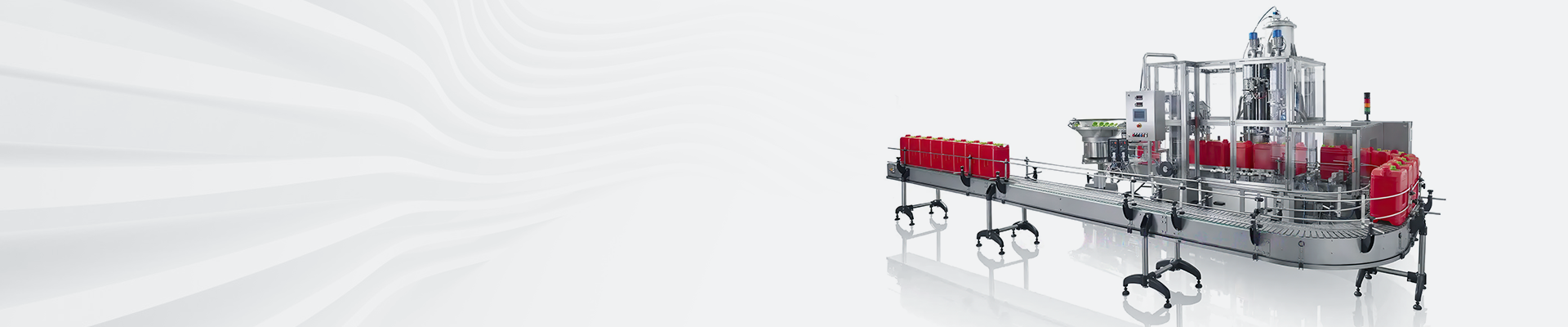
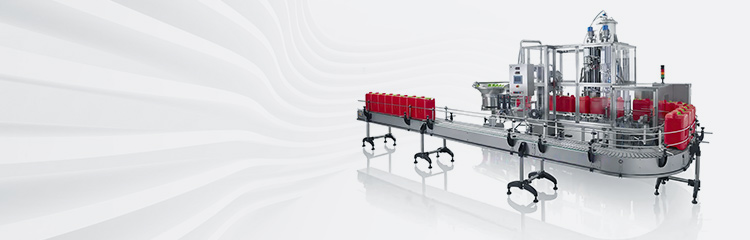
摘要:干法氟化铝工艺相比其他工艺的产品,具有流程短、见效快,且产品主含量高、水分低、堆积比重大等优势,近年来新增的产能也较大。但各厂家控制水平差异较大,其主要关键设备反应炉的工艺控制是主要核心影响因素。本文主要分析反应炉的配料进行理论计算,并对反应炉炉温分布提出下步控制及改进的建议。
干氟化铝主要用于电解铝行业,是铝电解的助溶剂,用于调节电解槽中电解质的分子比。在干燥氟化铝的生产过程中,反应炉主要用于萤石粉(97%以上的氟化钙和硫酸)的反应。硫酸与萤石粉之间的反应是吸热反应,反应所需的热量由天然气燃烧间接提供。
目前干法氟化铝行业使用的反应器规格为3.3m*33m,物料在反应器中的反应分为三个阶段。第一阶段,混合和预反应,是从反应器的进料端到反应器中7米的间隔。该区间的物料密度为60分钟,萤石粉分解率达到78%左右。在第二阶段中,距离反应器7-25m的反应段称为反应段。物料在该段停留时间为62分钟,萤石粉分解率达到18%。在反应器中25-33米处的第三阶段的干燥段在该阶段已经停止了萤石粉末和硫酸的反应。
配料控制系统的主要控制指标是副产品氟石膏中氟化钙的含量。反应炉中的物料经历三种不同的物理状态,即糊状、粘稠状和颗粒状。根据某厂的实际生产情况,分析了影响尾矿的控制因素,如下图1所示。图1中的鱼骨图从人、机、料、法、环境等方面分析了影响尾矿的因素,其中人、机、料等因素可以及时排除,但过程控制中的温度和配料是一个复杂的交互系统。本文主要讨论影响尾矿控制指标的工艺因素中的关键环节,即反应炉的配料和温度控制。
1.反应炉配料计算
干法氟化铝反应器主要是硫酸和氟化钙的反应,反应方程式为CaF,+H,s0,=Cas0,++2HFt干法氟化铝反应器主要是硫酸和氟化钙的反应,反应方程式为CaF,+H,S0,=Cas0,++2hft一般在生产干法氟化铝时,先设定萤石粉的投料量,然后根据上式计算氟化钙与硫酸的比例,干法系统中使用的硫酸为98%和105%的酸,通过计算得到它们各自的理论用量,为了保证进入反应炉的酸浓度能够达到100%,提高反应效率,减少反应炉的腐蚀,在配料系统中,反应器的配料非常重要,这不仅影响反应器的反应效率和现场环境,也影响设备的使用寿命。反应器的配料主要是指萤石粉和硫酸的配料,硫酸和烟酸的配料需要根据萤石粉原料的组成来计算
基于年产30,000吨的干法生产线,干法配料按65吨/小时萤石进行理论计算。计算中使用的数据基于工厂生产的实验室测试的实际数据。萤石粉中各组分的指标见下表1,计算所需的其他指标见下表2
表1萤石中各种成分的含量
项目:caf2;二氧化硅;Cac0B0
含量:97.40%;1.0%;0.50%;0.2%
表2其他指标
硫酸/%:烟酸/%;烟酸中游离S0,/%;尾矿中硫酸含量/%;尾矿氟化钙含量/%
98%:97.40%;23%;0.80%;0.2%
(1)萤石中各成分消耗的硫酸量
假设萤石中氟化钙消耗的硫酸总量为X1,碳酸钙消耗的硫酸总量为X2。
①萤石中氟化钙消耗的硫酸总量CaF+H,S0=CaS01+2HFt7898
6500*97.4%-1.7*6500*2%X1根据方程式解得氟化钙消耗的硫酸总量为:X1=7677kg。
②萤石中碳酸钙消耗的硫酸总量Cac0+Hs0-CaS04+C0+H0
100986500*0.5%X2根据方程式解得碳酸钙消耗的硫酸总量为:X2=318.5Kg。
(2)尾渣中未反应完的硫酸总量尾渣中未反应完的硫酸总量:1.7*6500*0.8%=88.4Kg。因此,进入反应炉系统需消耗的硫酸总量为:7677+318.5+88.4=8083.9Kg,(1.7为反应炉物料衡算的理论数据)。
(3)硫酸总量的计算
硫酸配料的原则是在保证100%硫酸总量为8083.9Kg的前提下,烟酸中游离的S0,与进入系统中的98%酸、萤石原料带入的水分以及反应产生的水结合。
假设给料酸中98%酸量为X,烟酸量为Y,得到以下方程
98%*X+105%*Y=8083.9原料带入的水分需消耗烟酸总量计算:
①硫酸带入系统中的水分:(1-98%)X=0.02*X;
②萤石带入系统中的水分:6500*0.2%=13;
③反应产生的水分,假设二氧化硅反应产生的水为H1。
为反应中二氧化硅的转化率,解得H=31.2Kg。
解方程式得H2=5.85Kg。
反应产生的总水分量为:H1+H2=37.05Kg。
系统中的总水分为:0.02X+13+37.05=0.02X+50.05。
进入反应炉投料系统中的总水分与进入系统中的烟酸中的S03,正好结合为100%的硫酸。
按理论计算,理论配料比应为:(2.773+1.530)*1840/6500=1.22,硫酸与烟酸的酸比为:2.773/1.530=1.81:1。但实际上因系统的密封性及其他因素,且因预净化酸水分在15%-19%之间,在计算时未计入,校核上述两部分消耗烟酸用量后,因此实际配料中烟酸的用量比理论计算的要偏大,一般实际生产中硫酸与萤石粉的配料比在1.22-1.25之间。
2.反应炉炉温控制
除了配料的影响外,反应器的反应效率还有一个重要因素,即反应器的温度分布控制。除了配料的影响外,反应器的反应效率还有一个重要因素,即反应器的温度分布控制。燃气热风系统由燃气燃烧装置、热风炉、高温风道、回风风道、高温风机组成,空气调节阀等设备和结构部件以及电器和自动调温系统煤气在热风炉内充分燃烧后,在热风炉尾部的混合箱内与高温风机送来的400-450℃的热空气混合,形成650℃的热空气,其在高温风道的正压下通过四个进风口进入反应炉的热风进口,与炉壁和物料进行间接热交换后,通过回风道进入高温风机的进风口循环使用由于物料在反应炉中的反应分为四个阶段,每个阶段的反应要求和机理不同,反应炉每个阶段的炉温要求也不同。反应炉的反应和控制可以直接通过副产品氟石膏的排渣指标和性能来反映。
某厂针对干法氟化铝反应炉炉温梯度的控制,进行了阶段性的实验。为消除其他因素影响实验的准确性,实验阶段始终稳定了以下因素:
(1)一直保持98%酸和105%酸比不变。
(2)萤石粉与硫酸的配料比不变。
(3)萤石粉使用单一同一厂家、并且成分含量尽量接
(4)萤石粉投料量始终保持5.2吨/小时。
(5)其他相关影响反应效率的设备运行均正常。
从阶段性实验结果看,2号实验方案的参数运行效果良好,且尾渣性状及现场环境也较好,但在实际运行控制中,因不同厂家的原料指标及粒度不一,炉温可进行适当上下调节。
3.气体预处理控制
在干法氟化铝生产过程的配料中,气体预处理后的洗涤酸需要与烟酸和硫酸混合,然后进入反应炉与萤石参与反应。因此,气体预处理系统的工艺系统对投料系统的配料环节尤为重要。气体预处理系统主要由净化、换热器和除雾器组成。净化塔的主要功能是除尘、冷却和吸收,主要控制参数是净化塔喷淋流量、出口温度和洗涤酸水分;换热器主要冷却净化塔的洗涤酸;除雾器是过滤气体中的酸雾、元素硫和少量粉尘的一部分,其主要控制指标是除雾器的压差。这个加料系统最关键的控制是洗酸的含水量,它不仅影响加药机配料,还影响产品质量。酸洗水分控制要点:
(1)硫酸、烟酸的浓度要符合工艺要求,即确保硫酸的浓度大于98%、烟酸的的浓度大于105%;
(2)由于洗涤酸循环使用过程中,洗涤酸的水分会逐渐增加,在工艺控制中,要根据洗涤槽液位增加量和洗涤酸水分的趋势变化,要及时将洗涤酸少量、稳定的排入系统中;
(3)时刻关注洗涤槽的液位变化,正常控制中,洗涤槽的液位是稳定均匀的增加,当其液位和温度出现较大浮动的上涨时,要及时检查换热器,检查水是否进入系统中;
(4)原料萤石粉的指标要符合工艺要求,萤石粉中水分和碳酸钙含量也是系统水来源之一,因此在配料环节要做到均匀、稳定搭配。
4.结束语
随着国家对安全环保的要求越来越严格,对无机氟化盐工业的尾气排放和现场环境控制要求也愈加严格,再加上当前严峻的市场环境,氟化盐生产企业必须追求精益的生产工艺控制,才能达到企业受益、员工受益双丰收。