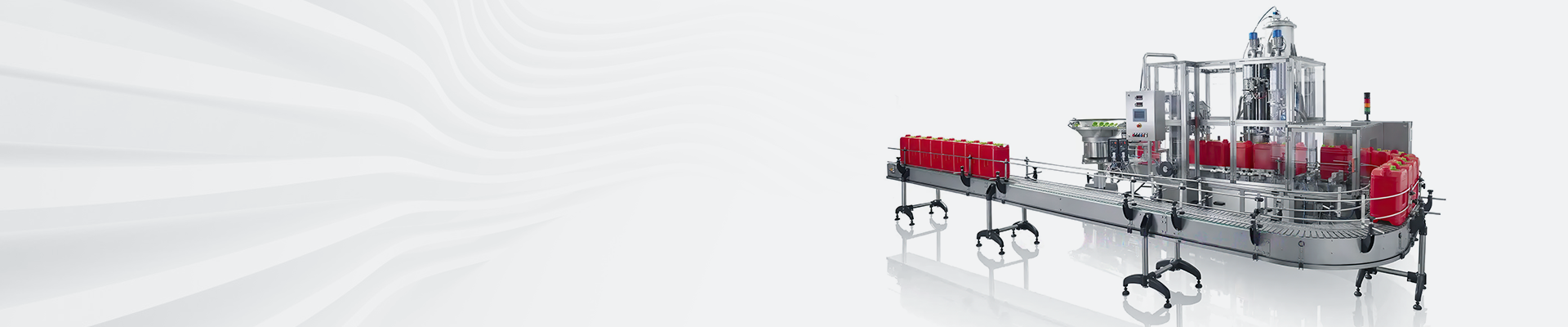
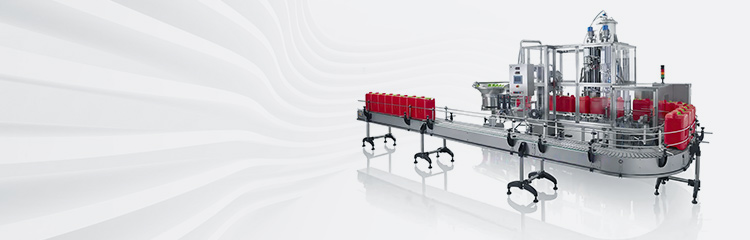

Summary:The weighing and dosage system accepts the information from the switching input module, the analog input module and the high counting module, processes the received information according to the program flow and activates the corresponding output module. After processing the received information according to the programmed compensation algorithm, the corresponding values are output.
With the current social and economic progress, the energy issue has become the focus of more attention, for the oil refining industry in the lubricant industry, how to ensure its efficient production, energy saving has become the key to determine the development of the entire automotive and machinery industries, and the application of the blending reactor in the lubricating oil ingredients to promote the quality of lubricating oil production and use of the benefits of the environmental protection and energy efficiency of the band to effectively enhance. Lubricant dosage on the blending reactor in the lubricant production in the application of certain analysis to explore, and combined with the actual to do the corresponding collation and summary in recent years with the intensification of the energy consumption problem, the lubricant industry has been gradually to the long life, energy saving, environmental protection direction, for the lubricant has oxidation resistance, oxidation stability, viscosity index, volatility and other qualities of the further set higher standard requirements. Combined with the practical point of view, most of the current mechanical equipment, automobile manufacturing and other industrial industries on the lubricant demand and quality standards gradually improved, according to the traditional way of separating the base oil lubricant effect has been unable to meet the needs of industry development. The application of blending kettle in the production of lubricants, to realize the lubricant itself a comprehensive enhancement of the nature of performance, but also according to the specific needs of the product to make the production of lubricant efficacy is more targeted and diversified; this process through the selection of one or more kinds of lubricant base oil to do the corresponding reagents added by a specific blending kettle to do the corresponding processing to achieve to meet the current needs of the various industrial sectors of the performance of the lubricant requirements. It can be seen that the application of the blending reactor in the lubricant production, the development of China's industries and energy industry has an extremely important significance to promote. At present, China's blending reactor in the production of lubricant ingredients in the application, mainly to the reaction tank blending and pipeline blending two ways to reflect, which can be regarded as a physical reaction process, the reaction tank blending and pipeline blending two blending methods, characteristics, subsequent use of a certain degree of variability. Oil storage and transportation process, online blending and batching production and delivery of key links, the use of imported special equipment weighing controller program, high cost, can not be freely expanded, the controller in the field of high security risks. The automatic dosage system adopts pc+plc mode, utilizing common plc controller as the control machine, taking pc as the management machine, the control machine and the management machine are in the non-explosion-proof area of the solution, which is a better solution to the above problems.
0Introduction
With the dwindling of oil, and China's increasing demand for oil and oil combustion pollution of the environment has also caused concern. The production of lubricating oil can reduce the consumption of lubricating oil, lubricating oil combustion more fully, improve the utilization rate of lubricating oil, can effectively reduce oil consumption, protect the environment, reduce the cost of users. The calorific value of the lubricant is 61%, but the oxygen content is higher than the lubricant up to 35%, the emission of co and hc compounds produced by combustion is lower than the lubricant, which is more environmentally friendly than the direct use of the lubricant. The octane number of 111, evaporation, its mixed oxygen calorific value is close to the lubricating oil, in the lubricating oil added not more than 10% of the engine used now do not need to transform, and does not reduce the power nor corrosion of the metal, the engine life has no effect. Manufacturing for sugar crops, starch-containing crops and fibrous fuels, renewable resources and such resources are abundant in our country, China's annual oil demand is now over 100 million tons, so the use of lubricants can reduce dependence on petroleum resources, conducive to energy security. Lubricants are easy to stratify, static storage can not be more than 4 days, ready to use is the best choice. Previously blended lubricants mainly used imported equipment, high cost, free expansion is limited, to expand production, construction difficulties. On-site single circuit failure to maintain, other circuits need to stop operation. Not conducive to continuous production. Controller in the blending site, for the explosion-proof area, high security risk. With pc+plc mode, the controller is located in the non-explosion-proof area, and the indexes of blending ratio, dosing accuracy and weighing accuracy are in line with the standard, and the safety risk is lower in the existing blending and weighing and dosing system. It has been popularized and used.