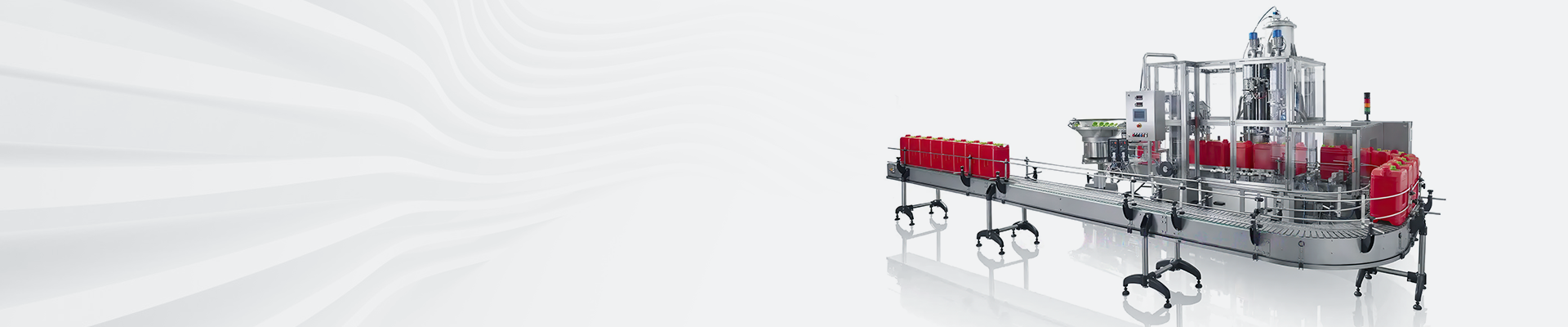
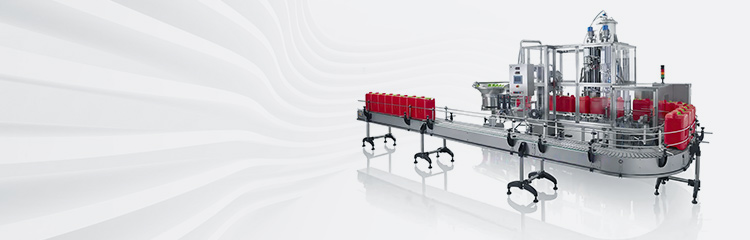

Summary:In lubricant petrochemical production, lubricant dosing process has large inertia, time-varying parameters, multivariate coupling, strong nonlinearity and other comprehensive and complex characteristics, therefore, the traditional manual dosing production method leads to large energy consumption in the dosing process, low qualification rate of lubricant process indexes, and low production efficiency. In view of the above problems, a comprehensive automation system of dosing process based on the optimization of lubricant process indexes is proposed. The system consists of process management, intelligent optimization setting control and process control, and discusses the structure, function and intelligent optimization setting control strategy of the system. The system is successfully applied in the lubricant dosing process of a large domestic petrochemical plant, which stabilizes the production process, improves the qualification rate of lubricant process indexes, and realizes optimized control, optimized management and optimized operation, and achieves remarkable application results.
Introduction
In the lubricant production process, the lubricant dosing process is to include a variety of hydrocarbons, aromatic hydrocarbons, fatty acids and their esters, phenols, amines and other raw materials are transported to the reactor for mixing and stirring to form lubricants. The good or bad of lubricant process indexes directly affects the operation and quality of the downstream dosing process, thus influencing the quality of the final petrochemical products. Due to the lubricant dosing process itself has a large inertia, multi-variable coupling, non-linear, boundary conditions fluctuations and process indicators and other key parameters are difficult to measure online and other complex characteristics, so the current lubricant dosing process automation is low, basically stays in the level of manual operation, resulting in low productivity, energy consumption, lubricating oil of the various process indicators of the qualification rate is low, to become a constraint on the petrochemical production of lubricants. Bottleneck. Petrochemical industry technology development guide pointed out: "Reduce production costs, improve product quality, reduce environmental pollution and resource consumption can only be achieved through the optimal design of the whole process automatic control system. Comprehensive automation is the key to solve the above problems. Wen puts forward a comprehensive automation system composed of process control, process optimization, production scheduling, enterprise management and economic decision-making five-layer structure.
Wen proposed a production process automation system composed of process stabilization, process optimization and process management. The paper proposes a comprehensive automation system composed of enterprise resource planning (ERP)/manufacturing execution system (MES)/process control system (PCS) three-layer structure, which is successfully applied in Sinopec and has achieved remarkable results.
This paper combines the technical requirements and process characteristics of the lubricant dosing process, the use of reasoning and other intelligent technologies, proposed by the process management, intelligent optimization of the setting control, process control of the three-layer structure composed of lubricant dosing process integrated automation system, and the system was successfully applied to a large petrochemical plant in the lubricant dosage process, to achieve the optimization of the control of the integrated production indexes, and achieved significant results in the application of the results.
1 lubricating oil dosage process introduction
Lubricant dosage process, first of all, including a variety of hydrocarbons, aromatic hydrocarbons, fatty acids and their esters, phenols, amines, etc. into the reactor mixed to form lubricants. The base oil, additives and filler of the required formula are mixed and stirred evenly according to the proportion; the mixed raw materials are put into the reactor for heating or pressurization to make them react and produce precipitation; the precipitation produced after reaction is mechanically filtered to remove the impurities; the filtered lubricant is centrifuged and dewatered to make its quality more pure. The lubricating oil from the reaction kettle enters into the B tank to store and conduct the index test. The qualified lubricating oil enters the K tank for storage, and then transported to the downstream filling process.
Base oils and additives are mainly determined by the amount of feed indicators, so the key to the dosage process is to determine the amount of each feed material according to the requirements of the process indicators of the lubricant. Traditional manual dosage by the operator according to the target value of the process indicators of the range of empirical information on the changes in judgment and decision-making, to give the base oil, additives, raw materials, flow control circuit settings, but due to the strong coupling of the dosage process, non-linear, as well as a variety of raw materials and the complexity of the chemical composition of the complex and often fluctuating, the key parameters of the process detection lag and other complex characteristics, it is difficult for operators to determine a reasonable feedstock according to the requirements of the process indicators. It is difficult for the operator to determine the reasonable quantity of raw materials to be fed according to the requirements of process indexes, which leads to large energy consumption in the dosing process, low productivity and low qualification rate of various process indexes of lubricants.