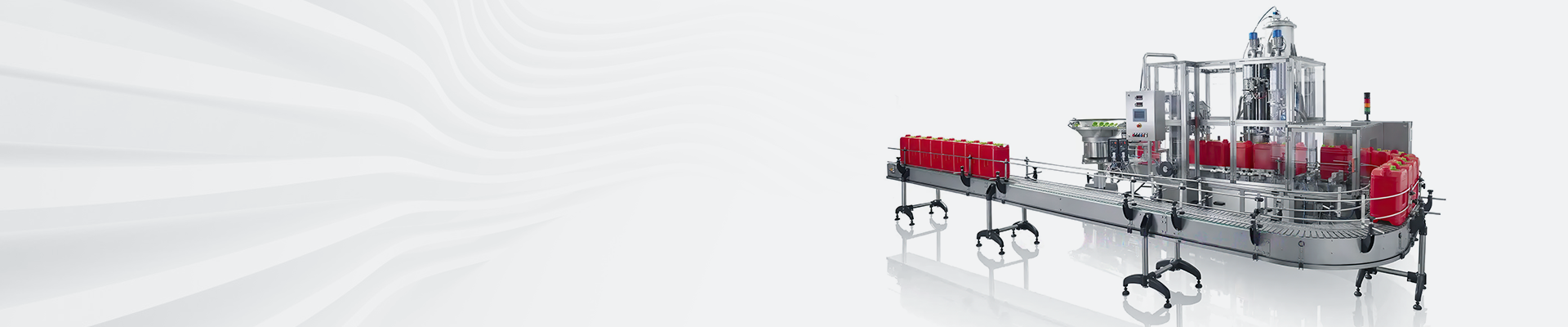
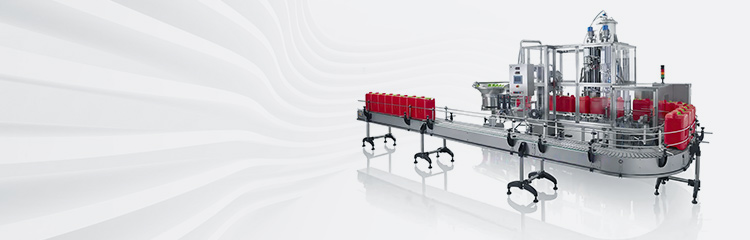
摘要:称重配料系统接受开关量输入模块、模拟量输入模块和高数计数模块的信息,按照程序流程处理接受到的信息后启动相应的输出模块。按照编制的补偿算法处理接受到的信息后输出相应的数值。
随着当前社会经济的进步,能源问题已经成为人们关注的焦点。对于炼油行业中的润滑油行业来说,如何保证其高效生产,节能降耗已成为整个汽车和机械行业发展的关键。调和反应器在润滑油配料中的应用促进了润滑油的生产质量和使用效率,有效提高了润滑油配料的环保性和能源利用率。对调和反应器在润滑油生产中的应用进行了分析和探讨,并根据近年来的实际情况进行了整理和总结。随着能源消耗的加剧,润滑油行业逐渐向长寿命、节能、环保的方向发展,对润滑油的现有特性,如抗氧化性、氧化安定性、粘度指数、挥发性等提出了更高的标准。
根据实际情况,机械设备和汽车制造等大多数工业部门对润滑油的需求和质量标准正在逐步提高,以传统方式分离基础油获得的润滑油的效率已不能满足行业的发展需求。调和反应器在润滑油生产中的应用可以全面提高润滑油本身的本质性能,并且在此过程中根据产品的具体需求,选择一种或多种润滑油基础油作为相应的试剂添加,并通过特定的调合反应器进行相应的处理,从而满足目前各行业所需润滑油的性能要求由此可见调合反应器在润滑油生产中的应用对我国各行业和能源行业的发展具有重要意义目前调合反应器在我国润滑油配料生产中的应用主要体现在反应罐调合和管道调合两种方式这两种方式均可视为物理反应过程两种调合方式的特点和后续使用存在一定差异。
在油品储运过程中,在线调合及配料生产和输送的关键环节采用进口专用设备称重控制器制作的方案,成本高且无法自由扩展,控制器在现场存在较高的安全风险。自动配料系统采用pc+plc模式,使用普通plc控制器作为控制器,pc作为管理器,控制器和管理器处于非防爆区域,很好地解决了上述问题。
0引言
随着石油的日益减少,中国对石油日益增长的需求和石油燃烧造成的环境污染也引起了人们的关注。润滑油的生产可以减少润滑油的消耗,使润滑油燃烧更充分,提高润滑油的利用率,有效降低油耗。保护环境,降低用户成本热值是润滑油的61%,但含氧量比润滑油高35%,燃烧产生的co和hc化合物排放比润滑油低,比直接使用润滑油更环保其辛烷值为111,蒸发量大,其混氧热值与润滑油接近,在润滑油中添加10%以下,现有发动机无需改造,不降低功率,不腐蚀金属,对发动机寿命无影响。它由我国可再生资源丰富的糖料作物、淀粉作物和纤维燃料制成。中国每年的石油需求超过1亿吨因此使用润滑油可以减少对石油资源的依赖并有利于能源安全润滑油很容易分层,并且静态存储不能超过4天它是现在制造它的最佳选择过去,主要用于调和润滑油的进口设备成本高且自由膨胀有限,当现场单向故障需要维修时,其他电路需要停止工作,不利于连续生产。控制器位于配料现场,这是一个安全风险较高的防爆区域。pc+plc模式的配料控制器位于非防爆区域,配料比、配料精度和称重精度符合标准,因此安全风险较低。在现有的配料称重配料系统中已得到推广使用。
在反应釜中调合配料生产中的应用主要是将润滑油基础油按一定的调合比例与相应的添加剂进行调合,在此过程中,将各种油品和试剂倒入调合罐中,并使用相应的辅助泵进行循环,然后通过电动搅拌将调和基础油和添加剂混合均匀,形成一种新型的调和油;结合实际情况,搅拌罐混合工艺在润滑油配料生产中的应用具有工艺设备简单、操作方便、投资小等显著特点。配料釜调合技术主要适用于润滑油批量小、组分多的企业,同时也是目前国内大部分润滑油配料生产中常用的调合技术,然而,搅拌罐中的调合在调和油的生产和能耗中并不占优势,整个反应过程耗时较长,耗油量相对较大。同时增加了生产风险和人工成本同时,配料种类多、数量巨大,现场人工配料难以管理,容易出现错配,不仅难以保证质量,还增加了管理成本为了保证产品质量、提高生产效率,需要精确可靠的自动配料系统整个自动配料搅拌系统由工控机、PLC、工业称重仪表、变频器、振动电机、搅拌机、称重模块、输送带等组成在PLC控制过程中,上位机使用上位机连接命令监控下位机的运行状态和数据区内容,并实时读取PLC内部状态和称重仪表的实时数据,并显示在上位机上。系统具有如下功能:
①全自动配料,在设定好配方之后,系统自动按照配方称重配料,无需操作人员干预;
②具有报表功能,可以产生日报表,实时报表和月报表、年报表等;
③动态增加和修改报表,自动配料系统通过设定权限,赋予技术人员或操作人员修改,增加配方的权利,同时记录该次修改的日期和操作人员编号;
④断电恢复功能,系统能够在突然断电的情况下,恢复断电前的测量记录;
⑤局域网共享功能,主机在局域网内可以共享数据,方便车间主管了解工程进度和其他情况。
称重配料系统主要由料仓、给料装置、称重模块、输送装置、电控柜和微机控制系统组成,可完成各种不同配方物料的自动给料和配料,广泛应用于化工、建材、医药、食品和饲料加工等行业的各种物料的称重控制。送料装置、称重模块、输送装置、电控柜和微机控制系统,可完成各种不同配方物料的自动送料和配料,广泛应用于化工、建材、医药、食品和饲料加工等行业各种物料的称重控制。自动配料系统集物料储存、定量送料、称重和密封输送于一体,全过程由微机控制,自动化程度高。每台单秤技术先进、性能优良,整个系统结构紧凑;通过终端设备的操作即可完成用户多素材、多配方环境下各种数据的输入输出;方便地在终端屏幕上输出或显示设定的数据,这是一个实现自动控制的集中监控系统,使用PLC、人机和组态软件实现自动控制;它具有现场监控、故障报警、数据采集、记录、统计、查询和打印的自动化过程。该系统长期稳定可靠地工作,消除了人工配料误差,提高了配料效率,改善了工作环境和工作条件
1配料设备配置
1.1控制部分
s7300plc主机—接受开关量输入模块、模拟量输入模块和高数计数模块的信息,按照程序流程处理接受到的信息后启动相应的输出模块。按照编制的补偿算法处理接受到的信息后输出相应的数值。
开关量输入模块—接受现场静电溢油保护器、应答器的信号。
开关量输出模块—接受主机的指令启动相应的继电器组。
高数计数模块—接受现场电子秤的计数脉冲,按照电子秤的脉冲系数折算成标准的流量数值送主机处理。
继电器组—接受开关量模块的控制启停泵及电液阀。
1.2管理部分
ipc工控机或dell机—同其他称重配料系统联网,生产管理,数据储存及历史数据管理。
1.3现场称重仪表设备
电子秤以脉冲的形式称重配料流过液体量。
数字电液阀—开、关管道通路。
温度变送器—检测液体温度并转换成电信号或其他模拟量信号。
静电溢油保护器—检测装油容器的静电泄掉,监测容器的液位。
1.4工艺设备
管道闸阀—关闭管道。
管道球阀—紧急关闭管道。
单向阀—保证液体单向流动。
过滤器—防杂质通过。
花管混合器—三通管,两种液体从两个管进入混匀一个管流出。
1.5电气部分
应答器—现场付油准备完毕,给出准备完毕信号。
电气配电柜—提供发油泵电器控制回路。
油泵—输送油品动力,dn100流量为80吨/时,扬程为30m,
2安全设置
现场设紧急停止按钮—现场突发事件发生时,及时自动关断油路。管道球阀—现场手动关断油路。管理计算机上组态画面上设紧急关断按钮—付油监控人员紧急处置突发事件关断油路。
3在线调和及发油流程
1)用户到销售业务部门交款拿到提单及提油ic卡,用户提货信息在销售业务部门和储运发油部门管理机共享。用户到现场读卡,信息在ic读卡器和发油管理机上显示出来,发油人员可以核对提单和ic读卡器传回的信息,相符后通知提货人将槽车开到指定位置装油。
2)在开始发油前,要做好下列准备:
润滑油、工艺线开通且放空管内所有气体,保证管内没有气体。两条工艺管线上的设备工作正常,防爆电子秤经检定合格,防震压力表检定合格。真空压力表检定合格。电动调节阀关闭严密不渗漏。
3)用户提单的数值,按照预定的比例自动分配,一般情况将润滑油和按89:11分配,例如提单10000公斤,润滑油为8900公斤,1100公斤,理论上分配比例可在99:1——1:99之间任意取值。实际中油品调和比例要同已经施工好的工艺线截面积之比的数值相匹配。这样,能减少调和时间、提高混匀度。
4)plc控制器同管理计算机通过网线传输信息。控制器接受管理机的启动、停止、暂停等指令,检测现场静电溢油保护器状态信号、及应答信号,并传给管理机,plc管理程序中将此双信号做成与门,双信号状态成立后,才启动发油。
付油画面信息有:发油设定值(如**公斤),发油速度值(**kg/s),实时发油值(**kg)。发油设定值是指提单上的提油数量(包括润滑油和)。发油速度值是润滑油速度值和速度值的和,实时发油值是实时发油的数量值。发油开始时,管理计算机监测到提油的容器静电已泄掉(是防止有静电的容器在填装油品时出现火花引起火灾)及应答控制器已启动后自动启动此鹤位上的润滑油、泵电机,1s~2s后启动本鹤位上的润滑油、电液阀。在发油时,流速由零开始,阶梯缓慢上升,达到防爆电子秤最高流量的80%左右时稳定发油,在油品还有近1分的发油数量值时,流速阶梯缓慢下降,对于汽车槽车,降到6kg/s左右(也叫小流量)时稳定流量,以发油设定值减去实际发油值的差值除以6kg/s,所得到的时间减去2s为启动电液阀的关阀启动时间。全部发油速度过程图像为非等腰阶梯形。
原因是:液体流速开始时应缓慢上升,对工艺线及称重仪表冲击小,这样就要求电液阀用时3s~4s缓慢打开,液体流速在dn100的工艺线由0kg/s上升到24kg/s。以此速度为正常付油工作速度,在油品还剩下1000kg时,为防止水击现象也为付油控制更准确,电液阀应缓慢关闭,到小流量时稳定付油,以电液阀关断时间为提前量启动电液阀关断信号,可保证了工艺线平稳工作、称重配料系统付油精度。
5)精度合格标准
称重配料系统精度:2.5‰,设定1000公斤,实际发油量在(997.5-1002.5)公斤为合格。称重精度:每次付油偏差3公斤为合格。
4结论
以pc+plc模式建立的润滑油在线调和配料方案,在减少了安全风险的前提下,用普通设备代替了专用设备,扩容方便,减少了投资,投入运行后操作简单,维护工作量相对减少。经检定满足油品调和配料的精度要求。是较理想的润滑油在线调和配料方案。