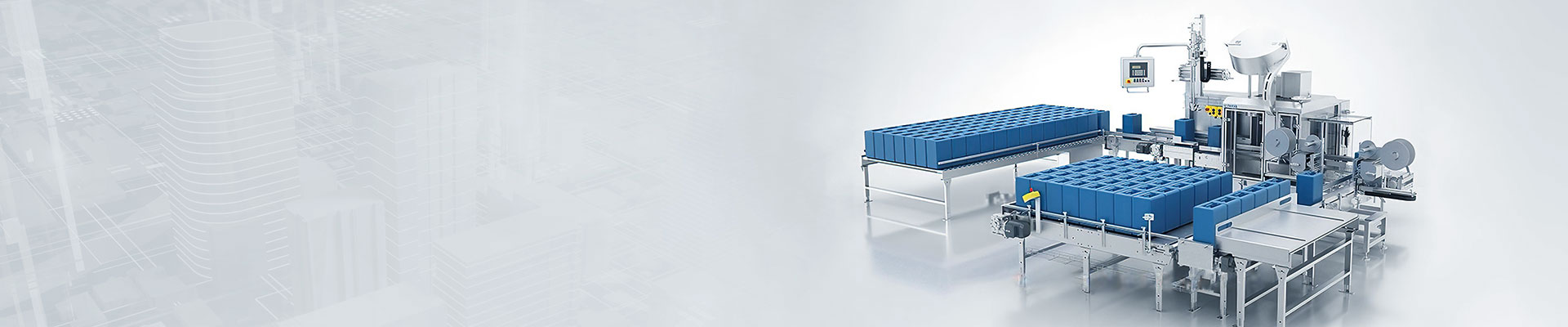
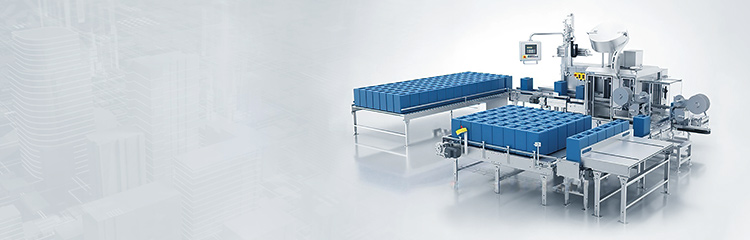
The belt scale is equipped with a load weighing module bridge, mounted on the longitudinal beam of the conveyor. The weighing rollers on the weighing bridge detect the weight of the material on the belt and produce an electrical output signal proportional to the belt load. The speed sensor is directly coupled to the follower pulley or large diameter rollers and provides a series of pulses, each pulse representing a unit of belt motion, at a frequency proportional to the belt speed. The weighing instrument receives the output signals from the weighing module and the speed sensor, electronically multiplies the belt motion and belt load, and produces an instantaneous flow value and a cumulative total by calculating the time. The cumulative total and the instantaneous flow are converted into selected engineering units and displayed on the accumulator respectively.

Belt scales are equipped with a load weighing module bridge, mounted on the longitudinal beam of the conveyor. The weighing rollers on the bridge detect the weight of the material on the belt and produce an electrical output signal proportional to the belt load. The speed sensor is directly coupled to the follower pulley or large diameter rollers and provides a series of pulses, each pulse representing a unit of belt motion, at a frequency proportional to the belt speed. The weighing instrument receives the output signals from the weighing module and the speed sensor, electronically multiplies the belt motion and belt load, and produces an instantaneous flow value and a cumulative total by calculating the time. The cumulative total and the instantaneous flow are converted into selected engineering units and displayed on the accumulator respectively.
Belt scales are mainly of four types: double-lever multi-roller type, single-roller type, cantilever type and suspended type. Double-lever multi-roller type and suspended type scales have longer conveyor metering segments, generally 2-8 groups of rollers, with high metering accuracy, and are suitable for places with larger flow rates and high metering accuracy requirements. Belt scales by the load-bearing device, weighing module, speed sensor and weighing instrumentation, weighing bridge mounted on the conveyor frame, when the material passes through, the load-bearing device will be the gravity of the material on the belt to the weighing module, the sensor that is the output is proportional to the gravity of the material voltage mV signal amplified by the amplifier sent to the analog/digital converter into a digital quantity A, sent to the operator; the speed of the material entered into the speed sensor, the speed sensor that output pulse number B is also the speed sensor, the speed sensor is the number of pulses. Speed sensor that is the output of the pulse number B is also sent to the operator, the operator on the A, B after the operation that is the amount of material to get this measurement cycle, for each measurement cycle can be totaled to get the total amount of material on the belt through the continuous.
PLC's instantaneous value are collected from the field belt scale output current signal or voltage signal, instantaneous current/voltage value collected by the analog module by the lower program calibration block calibration converted to kg/hour, and then through the calculation module is converted to grams/second instantaneous amount, through the cumulative calculation of the cumulative amount of each batch. According to the field signal configuration of the corresponding module channel configuration, the current type generally use 4 ~ 20mA signal, channel configuration InputType selection: 4-20mA. the flow data provided by the field is a voltage and current signals, the processing of analog to be converted to the flow of the corresponding data before processing, through the metering module after the calculation of the value of the actual instantaneous value of the belt site.