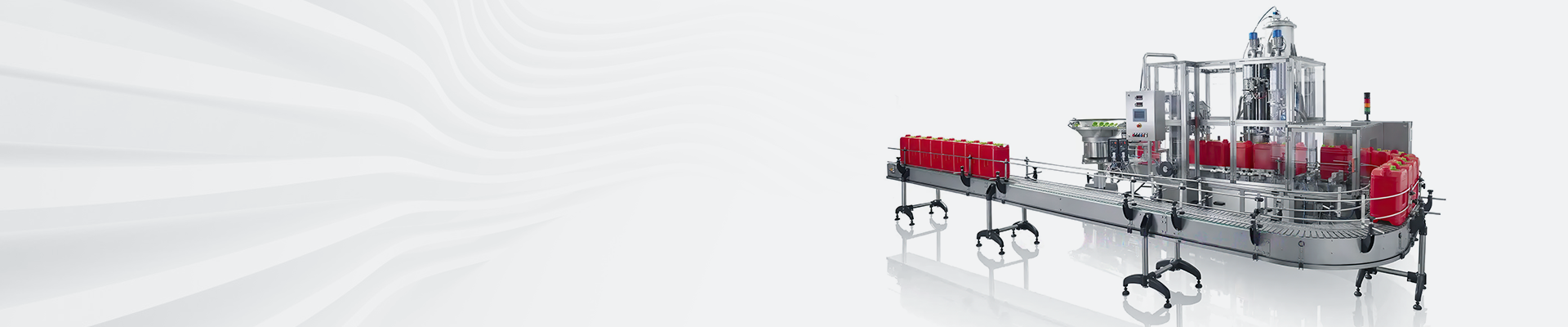
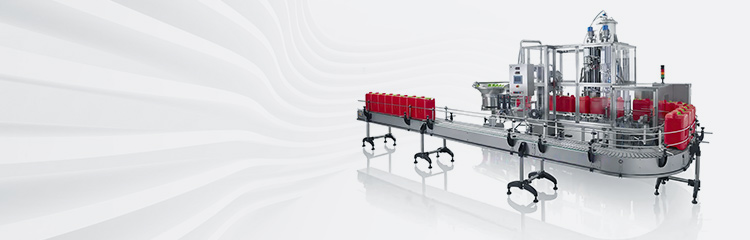

Summary:The batching system uses batching scales and spiral scales, and uses microcomputer background monitoring to change the PID adjustment parameters of the belt scale control according to the feeding situation, thereby improving the control characteristics of the batching system and keeping the feeding volume from fluctuating.The scale is calibrated using a method that combines chain code verification and physical verification.Since its inception, the system's cloud center has been stable and its ratio control has been reliable, meeting production needs.
0.Preface
The main function of the batching system is to mix 5~6 kinds of iron powder with different tastes and strengths and a certain amount of bentonite in a balanced manner according to a certain ratio to form a material with uniform composition. Electronic belt scales (mainly including metering belt scales, dosage scales, spiral scales) with its inherent characteristics are widely used in the feeding system, the current pellet dosage system is used in the dosage scales and spiral scales. As the degree of automation of the pelletizing process system increases, the requirements for the accuracy and rapidity of the feeding system are getting higher and higher, and the improvement of the pelletizing production feeding system is crucial to the improvement of the technical and economic indexes of the pellet mine. Therefore, measures must be taken to improve the automation control precision of pellet batching system.
1. Composition of electronic belt scale
1.1 Composition of dosing scale
(1) scale frame. For the whole machine-type dosing scale, the scale frame is actually a small belt conveyor, responsible for dragging the material out of the silo and conveying the purpose. When the material passes through the weighing section, the weighing frame and the sensor detect the weight of the material, so as to complete the weighing while continuously conveying the material, and the size of the material flow rate can be adjusted when changing the rotating speed of the speed-regulating motor.
(2) Load cell. When the material passes through the weighing section, the weighing frame passes the weight of the material to the weighing sensor, and the weighing module converts the weight into the corresponding millivolt voltage signal and sends it out. Weighing module adopts resistance strain type, when the sensor is subjected to force, affixed to the sensor wall of the corresponding deformation of the resistance strain gauges, resistance value also changed, resistance strain gauges connected to a bridge, when the bridge arm organization changes, you can output the corresponding electrical signal.
(3) speed sensor. To complete the weighing, must measure the speed of the belt. Speed sensor is installed on the upper surface of the lower belt, the use of self-weight pressure to make the friction wheel and belt contact, when the belt moves the friction wheel at the same time rotate, at the same time the speed sensor occurs synchronized pulse signal.
(4) Control and display. To complete this function, the module is S-301 weighing controller, which receives the weighing signal and speed signal from the signal amplifier, gets the cumulative weight and instantaneous flow rate of the material through the arithmetic processing, and sends out PID control signals according to the gap between the set flow rate and the current flow rate value, and controls the feeding equipment to reach the required flow rate.
(5) Speed control device. Used to drive the motor of the regulating equipment under the control of PID signal. Commonly used slip motor controller and frequency governor. Mining and construction of the pelletizing plant is used in the frequency converter speed regulator.
1.2 Screw scale composition
Some powdery materials (such as cement, lime powder, bentonite, etc.) should not be weighed with a batching scale, can be used spiral scale. Due to the limitation of its structural characteristics, the weighing accuracy is lower than the belt scale.
(1) Scale body. Scale body consists of spiral feeding cylinder, drive motor and pivot point. The pivot point position should be in the center of the feed opening, in the absence of material when the spiral Jane and the drive motor in the pivot point on both sides of the weight is basically equal, when transporting the material, the material from the population inlet to the outlet running, the pressure on the sensor gradually increased. The whole scale is the structure of cantilever scale.
(2) Load cell. The felt gravity is converted into an electrical signal output, and the role of the sensor in the dosage scale is the same. Due to the heavier spiral scale, the sensor range is not too large, so attention should be paid to the weight balance of the spiral feeding cylinder and the drive motor, if necessary, add counterweight to adjust. Weighing and belt scales are the same, but no speed measurement signal. The speed is considered to be constant, determined by the power supply frequency.
(3) Calculation, display, control and adjustment device. The function is the same as that of dosage scale, but the object of speed regulation is the feeding motor.
(4) Soft connection. Used to connect the scale and feeding equipment, not only to prevent material leakage, but also to make the scale and feeding equipment between the connection does not affect the weighing. Commonly used materials for chemical fiber, rubber and so on.
2. Belt scale calibration
Before production or production after a certain period of time, the need to calibrate the belt scale to ensure its accuracy, to meet production needs. Scale calibration methods are many, mining and construction of pellet plant is a combination of chain code calibration and physical calibration method. Physical calibration using known quality of the physical reproduction of the actual working process of the dosage scale, this method of calibration effect is accurate, small error, but time-consuming and laborious. Chain code calibration is a form of physical simulation, simple and labor-saving, but the accuracy is low compared with physical calibration.
3. PID control of belt scale dosage
PID control is proportional, integral, differential control, also known as PID regulation, PID regulation controller parameterization is the core of the control system design. Its purpose is to reduce and eliminate system errors, to ensure stable operation of the system, by adjusting the proportional, integral and differential coefficients so that the output signal tends to the set value.
4.Application effect
Since the batching system has been put into operation, the working condition is good, the scale frame and on-site load cell performance is stable, after calibration test, the batching control system controls the dose accurately, each disk material quantity mediates the fast reaction speed, the control accuracy reaches the expected requirements. The commissioning of this dosage system reduces the labor intensity of the post, simplifies the operation procedure, improves the production efficiency and achieves good economic benefits.