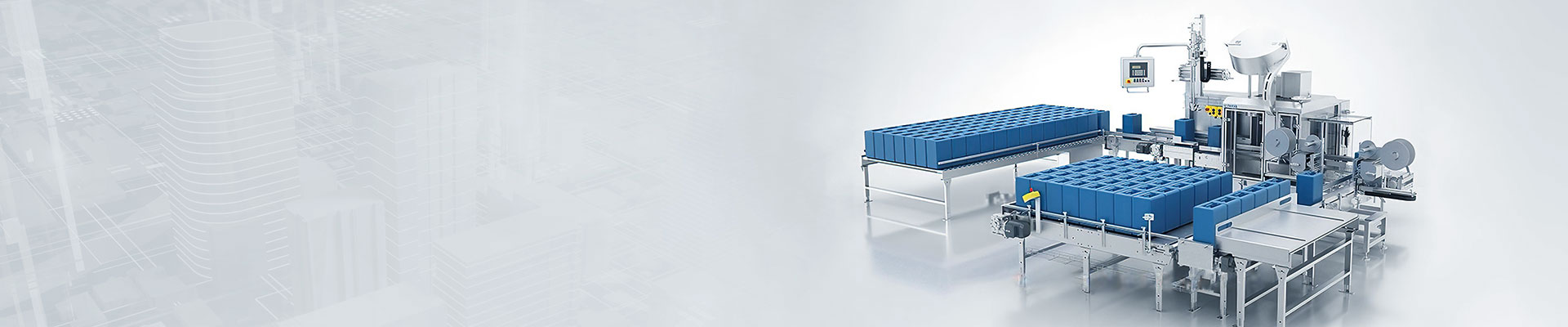
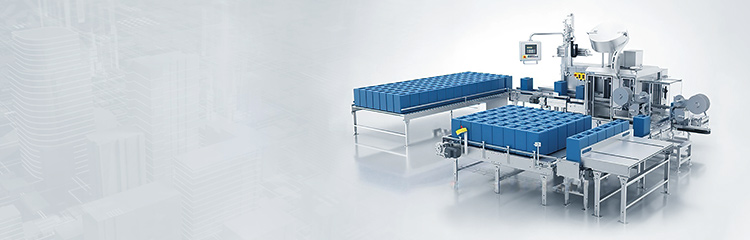
The core part of the weighing module is CPU, which communicates with the modules installed on the rack by using the backplane bus of the rack. On the premise of hardware self-inspection, the module installation inspection and program scanning are carried out, and the I/O module values are stored and updated regularly. The analog module is used to poll each module of the equipment and constantly update each channel, and the results are directly input and output after the program execution. Even if the HMI fails, the normal operation of the system will not be affected. At the same time, the weighing sensor has the functions of interlocking control of itself and the surrounding system, controlling the running state of the motor, various feeders, baffles, charging doors, measuring hoppers and other components in the control system, detecting the running state of the state sensor, monitoring the field situation in real time and giving an alarm at any time, transmitting the running state of the system to the upper computer in time and accepting the supervision of the upper computer all the time.

The metering module adopts a full-bridge measurement circuit to make the system produce less error and more accurate output data. The role of the three operation amplifier circuit is to amplify the weak analog signal output from the sensor by a certain number of times to meet the requirements of the input signal level of the A/D converter.The role of the A/D converter is to convert the analog signal into a digital signal, analog-to-digital conversion, and then the digital signal is delivered to the display road, and finally the measurement results are displayed by the display circuit.
The weighing module can be composed of a combination of PLC hardware, weighing equipment and HMI. The core part of the module is the CPU, which utilizes the rack backplane bus to communicate with the modules mounted on the rack, and performs module installation check and program scanning under the premise of self-testing of the hardware, storing and updating the I/O module values on a regular basis, polling the various modules of the equipment through the analog module and constantly updating the channels, and directly inputting and outputting the results after program execution. The analog module polls each module of the device and constantly updates each channel, and inputs and outputs the results directly after the program execution, so that the normal operation of the system will not be affected even if the HMI fails.
At the same time, the load cell has the functions of interlocking control of itself and peripheral systems, controlling the operating status of motors, various Feeders, baffles, gates, measuring hoppers and other components within the control system, detecting the operating status of status sensors, carrying out real-time supervision of the scene and alarming at any time, and transmitting the operating status of the system to the upper computer in a timely manner, as well as accepting the upper computer to supervise the whole process.
Product Features
* Installation of load cells in accordance with OIML R60
*Use of struts and anti-pullout design
*Reaction pots are compact and low in height
* Maintenance-free
* Easy to install reaction tanks
*Electroplated alloy or stainless steel available
*Pendulum structure with automatic reset function
*In accordance with OIML R60 Class C1 (Ex ib Ⅱ CT4)
*Explosion-proof (Ex ib Ⅱ CT4)
Technical Parameters
*Rated load (R.C.): 0.25,0.5,1,2,3,5,10T
*Rated Output (R.O.): 2±0.005mV/V
*Zero Balance:±0.030mV/V
*Integrated error:±0.03%R.O.
*Nonlinearity:±0.03%R.O.
*Hysteresis:±0.03%R.O.
*Repeatability ±0.02% R.O.
*Creep (30 minutes): ±0.03%R.O.
*Normal operating temperature range:-10... +40°C
*Allowable working temperature range:-20... +70°C
*Temperature effect on sensitivity:±0.02%R.O./10 °C
*Temperature effect on zero point: ±0.02%R.O./10 °C
*Recommended excitation voltage:10V(DC/AC)
*Maximum excitation voltage:15V(DC/AC)
*Input Impedance:385±10Ω
*Output impedance:350±3Ω
*Insulation impedance:>5000MΩ
*Safety overload: 150% R.C.
*Limit overload:300%R.C.
*Elastic element material: alloy steel
*Protection class:IP67
*Cable length: 4m (0.25t...2t), 6m (3t...10t)