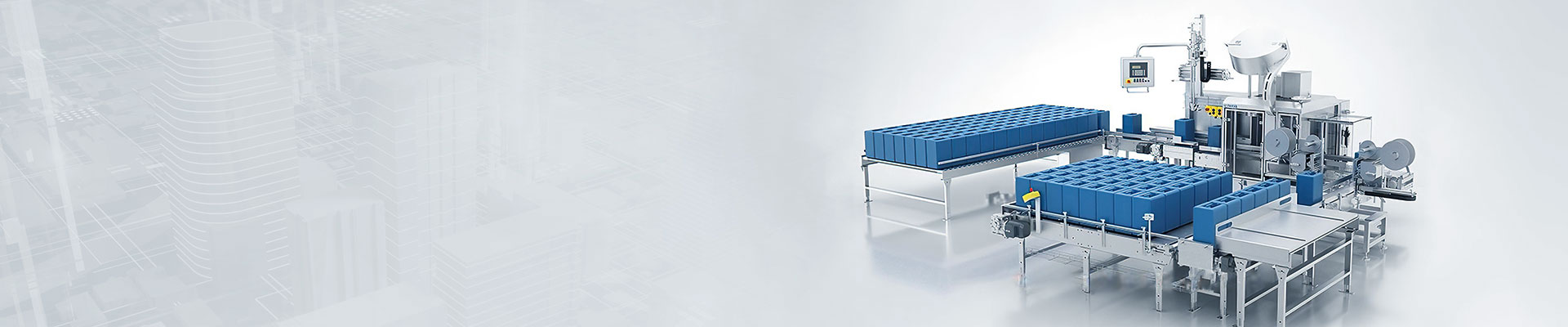
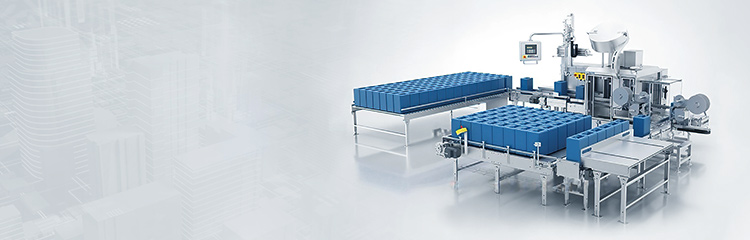
The main belt scale is composed of weighing frame, weighing sensor , bridge box, weighing control sub-, and can be equipped with printer, microcomputer management system system and other equipment according to the needs of households. Belt scales are used to ration feed bulk materials. And the weight is measured by weighing bridge. At the same time, a speed sensor mounted on the rear wheel detects the speed of the belt and controls the constant feed flow.

Belt scale converts the measured weight parameters into analog voltage or analog current by analog weighing module, and transmits them together with the instantaneous speed detected by the velocity sensor to the digital transmitter. After the conversion of the digital transmitter, the output digital signal is sent to the intelligent weighing controller of the belt scale, and the instantaneous flow and accumulated weight of the material are displayed by microcomputer conversion based on the integration principle. The measurement signal is transmitted to the control system through the current isolation module to complete the dynamic process of remote display and production flow control. The electronic control system is composed of main control console, variable frequency cabinet, PLC host, testing device and driving device. The main control console adopts advanced technology and reliable performance programmable controller equipped with weighing module position sensing and other testing devices, driving drum, cleaner, etc. The driving component adopts high-performance vector control inverter to control the motor. Complete various functions such as stacking, blanking, soft start, soft stop and speed regulation during the operation of the belt conveyor. Equipped with the status display, each belt is installed under a weighing sensor, when the coal on a belt exceeds the limit value, the corresponding pressure switch is closed to provide PLC signals for stacking through program analysis, and display the overload state. The position switch is installed on the left and right side of the belt, and once the belt runs off, the position switch will be triggered to close, and the correction device of the driving drum will be automatically corrected by PLC analysis. Install a certain height of coal level detection device on the ground, as long as the coal falls to this height, the height position switch is closed, and the PLC drives the cleaner to clean up.
System control can start and stop independently, with pressure overload and alarm function, power frequency conversion switching function, belt deviation processing function, abnormal can automatically trip to power frequency function and automatic blanking cleaning function. The main circuit of the belt electromechanical control system has two independent 10kV power supply lines, which are divided into two transformer channels through the bus bar, and the 1# transformer is 10kV/380V type, which supplies power to the frequency converter, and each frequency converter has the power frequency/frequency conversion switching function (such as frequency converter 1). KM11 K12 control frequency conversion work KM13 switch to power frequency operation), and then connected to the motor respectively for control, 2# transformer 10kV/380V type, through low-voltage distribution to the PLC cabinet power supply, or process control power supply.
The main technical indicators are as follows:
◇ Case: "S" type seal protection
◇ Nonlinear: <0.03%FS
◇ Non-repeatability: <0.01%FS
◇ Creep: <0.02%FS
◇ Zero output: ±1%
◇ Under the maximum flow rate, the displacement of the pressure point of the sensor elastomer is not more than 0.2mm
◇ Temperature sensitivity: Interval: 0.0008%FS/oF
Zero point: 0.0015%FS/oF
◇ Lag error: 0.02%
◇ Sensitivity error: ± 0.1%
◇ Overload capacity: 150% of sensor capacity
Speed sensor 12C,12B
The speed sensor is installed on the tail drum, the speed measuring large diameter drum or the speed measuring roller, and the speed measuring drum/roller is installed on the upper surface of the return belt, eliminating the influence caused by the belt slip. The speed sensor is a digital brushless pulse generator. When the belt is running, the speed sensor emits a series of speed pulses, each pulse represents a unit length of the belt travel, and the pulse frequency is proportional to the speed of the belt.
The shell material is cast aluminum, which can be adapted to the open-air working environment
Ac pulse generators do not require adjustment or change of brush
No carbon brush type AC pulse generator, no adjustment, calibration, maintenance free
The latest soft connection technology ensures the speed measurement accuracy more effectively, and greatly improves the service life of the equipment.
CI2001 weighing control instrument
◆ Adopt 32-bit CPU and 24-bit A/D to speed up the running speed and improve the measurement accuracy;
◆ All the data of the belt scale are displayed on the high-brightness four-row vacuum screen;
◆ Menu panel operation mode, in line with people's computer operation habits;
◆ When the relevant data of the belt scale is changed, the original data can be retained for query to reduce human error;
◆ Provide multi-level password protection to facilitate different users; Provides linear compensation so that the belt scale has the same accuracy at 25% to 100% of the rated load;
◆ Optional analog output for material flow, weight or speed display;
◆ Optional analog output delay for actual control;
◆ Optional analog input and output board (one or two voltage and current input and output) for control or compensation use;
◆ Optional RS-232/RS-485 communication board, from the hardware Settings can choose one of the two ways;
◆ CI2000 series instrument has CI2001 type, CI2105 type for users to choose;
Type CI201 weighing instrument
◆ The display is dual screen digital display, the upper screen shows the cumulative amount, the lower screen shows the instantaneous flow;
◆ The number input and output adopts the key to call out in the form of command code, such as: 01P represents the zero value;
◆ Remote counting using contact and no contact two ways to choose, no contact output for DC 24V signal;
◆ The optional communication board is used when the upper computer is communicating, and the communication mode is RS-485 standard port;
◆ Optional current output board, output for standard 0-20mA or 4-20mA signal;
◆ Optional print expansion board, output interface can be connected to mp or pp series parallel port printer.