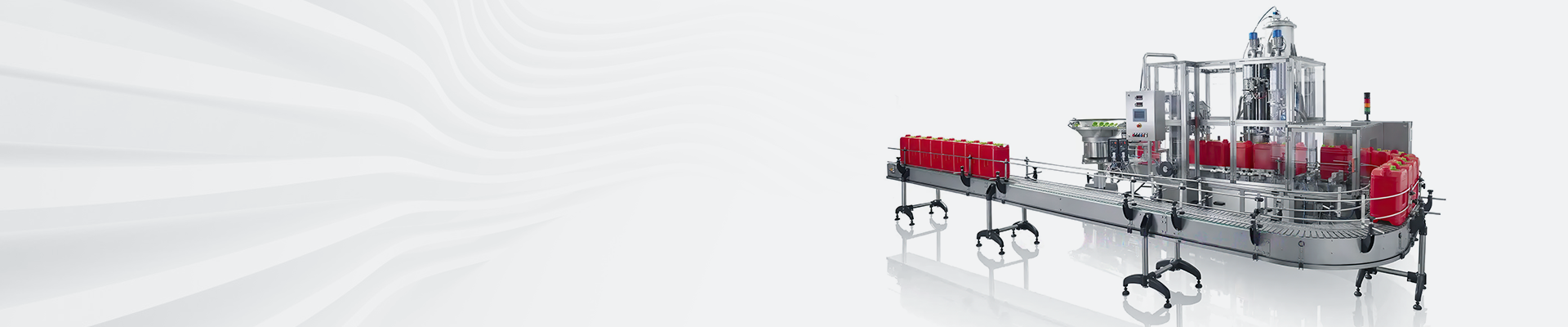
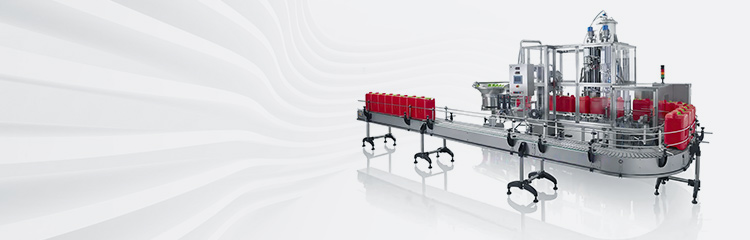

Summary:The weighing system combines multiple weighing modules into a control system that integrates weighing and proportioning. It can perform dynamic cumulative weighing and flow control on a variety of cut tobacco, and blend according to a certain proportion to achieve automatic control.
1 Introduction
The resin proportioning process section is one of the key process segments in the production of the coating industry. Weighing system will be additives, asparagus, methanol and ethanol in several according to the weighing module of the respective set ratio and alcohol solution for real-time uniform mixing. Proportioning is the completion of this process section of the core equipment, and one of the key factors affecting its accuracy is the accuracy and stability of the weighing signal acquisition, crystallization tank dosing system will be directly related to the quality of the proportion, and thus also largely determines the subsequent ammonia solution finished products inherent in the stability of the quality of production and balance.
2 Proportioning type working principle
Spiral weigher according to its working purpose classification, generally divided into measurement type, control type, proportioning type three types. Measuring type - measuring the instantaneous flow of materials and cumulative weight; control type - balanced control of the weight of the material, so that the material according to the set flow through; proportioning type - to achieve the active agent, emulsifier, suspending agent, wetting agent, etc., the set ratio; proportional weighing control system consists of a number of crystal tanks and centralized control, weighing, proportioning in the same way as a single weighing, weighing, and so on. The weighing control system of proportioning type is composed of several crystallization tanks and controlled centrally, which integrates weighing and proportioning, and has interactive multi-tasking and multi-parameter measuring function, which can carry out dynamic cumulative weighing and flow control of a variety of products, and mix them according to a certain proportion.
2.1 Spiral working principle
Various through the limited pipe (or directly down) to the pipeline, with the pipeline running forward, when it passes through the effective weighing section, its weight through the conveyor pipeline and metering rollers added to the load weighing module, metering module to feel the load generated by the signals directly into the mixing kettle, the dosage tank weighing module collected and converted data directly through the s7 system bus into the plc data collection metering data to detect weighing section on the The unit length weight q(kg/m) of the weighing section is detected, while the speed measuring device detects the running speed v(m/s) of the pipeline, and the instantaneous flow rate and cumulative amount are calculated by plc and displayed.
2.2 Spiral proportioning working principle
Proportioning spiral system through the main metering kettle material instantaneous flow rate as a benchmark, and doping fermentation tank corresponding to the set proportion of doping operation, as the doping device set flow rate, at the same time will be measured through the doping device of the instantaneous flow rate and the set flow rate signal for comparison, the use of plc pid control operation, the output of the speed signal to regulate the motor's rotational speed, thereby changing the pipeline speed, to achieve the purpose of automatically adjusting the dosing flow rate, and then display. The purpose of automatically adjusting the dosing flow.
3 Spiral dosage composition
Dosing type main control cabinet components based on the German Siemens module (siwarexu) s7-300 series plc technology platform. s7-300plc by cpu317-2pn/dp, high-speed counting module fm350-2, digital input and output, toning tank weighing module and power supply module. cpu317-2pn/dp is mainly used for the main process control and profinet communication. The cpu317-2pn/dp is mainly used for main process control and profinet communication. The cpu317-2pn/dp is mainly used for the main process control and profinet communication. It contains digital input and digital output points, analog input and analog output circuits, of which the digital input and digital output points are responsible for the digital input and output control of the whole spiral as well as the provision of input and output signals required for linking with the outside; the analog inputs are used for the sampling of the 4-20ma flow external setting; the analog outputs are used for the control of the frequency inverter and for the instantaneous flow of the 4-20ma outputs. The weight signal from the toning tank weighing module is sampled by siwarexu, and the encoded pulse signal from the speed encoder is fed into the high-speed counter of the plc. Spiral according to the weight from the weight reaction tank weighing module weight signal, speed signal from the speed encoder and the speed signal and the set signal and has been prepared by the software program, weighing, flow control, proportioning, communication and send speed control signal, the signal to the frequency converter speed controller so as to control the speed of the motor, drive the spiral work.
3.1 Mixed batching characteristics
(1) Simplified load signal amplification circuit. Load signal acquisition using Siemens storage tank weighing module siwarexu, so that the signal connection from the load weighing module directly into the module siwarexu, reducing the use of signal amplifier of the traditional intermediate amplification links, so that the load signal transmission of a higher degree of accuracy, the sampling frequency is faster, which ensures that the cumulative accuracy of the spiral.
Siemens module (siwarexu) has a power supply compensation for the output signal of the module bridge circuit, and the transmission distance is far, it can reach 1000 meters, high precision, designed for 0.05%, 65,000 partition resolution, the number of control measurements reaches 50 times/second, more digital filtering, disconnection monitoring, etc., so as to make it more stable and reliable, and the stability of the measurement accuracy can be obtained in a longer period of time. greater extent to ensure that the spiral explosion-proof electronic scales, thus greatly extending the maintenance and calibration cycle. In addition, siwarexu is a set of signal amplification, 16-bit a/d conversion as one of the special hybrid tank module, dosage system and Siemens plc connection is directly from the backplane bus to complete, greatly simplifying the load signal amplification circuit, a series of advantages that make the spiral accuracy and reliability of the spiral to get a greater sense of enhancement, and the level of application has reached a new level.
(2) Measurement of cumulative error automatically add function. According to the blending principle of the proportioning type spiral, the instantaneous blending accuracy should be able to be guaranteed, but the overall cumulative accuracy of the cumulative amount of blending over time may be due to the error of instantaneous flow, unstable incoming materials and other factors beyond the allowable range of the set ratio, the design of the measurement of the cumulative error of the automatic addition of the program and the principle of: when the cumulative error exceeds the permissible range of larger in the original set ratio on the basis of the increase of When the accumulated error exceeds the permissible range by a large amount, a larger correction value is added on the basis of the original setting ratio to revise the setting ratio, so that it quickly returns to the normal accumulated error range; when the accumulated error exceeds the permissible range by a small amount, a smaller correction value is added on the basis of the original setting ratio to revise the setting ratio, so that it slowly returns to the normal accumulated error range.
3.2 Siemens weighing module application experience
Although Siemens crystallization tank module siwarexu has a power supply compensation of the module bridge output signal, and the transmission distance is far, can reach 1000 meters, but in the usual use should try to shorten the distance between the load toning kettle weighing and the module siwarexu, so as to avoid as far as possible the intervention of strong interference signal. If the transmission distance exceeds 300 meters, try to choose the original module cable with Siemens order number 7mh4702-8ag.
4 Conclusion
The stability of the load signal has been significantly improved with the use of the extraction tank weighing module siwarexu. In order to make the whole spiral of the system accuracy and stability will reach an optimal state, in the specific use of the process, should also pay attention to other factors affecting the stability of the load signal, the edge and the pipeline whether there is a foreign body between and so on. At the same time, this integrated weighing method is very worthy of promotion in the industry.