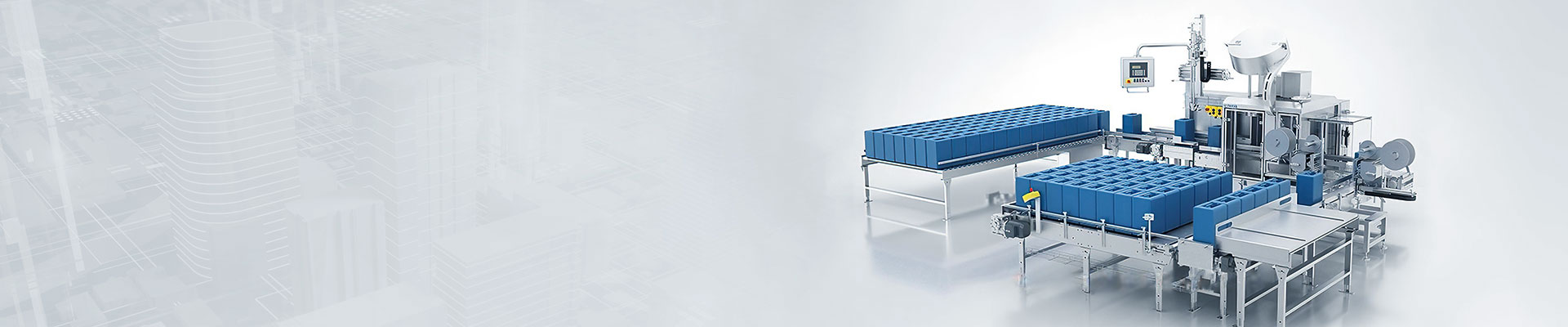
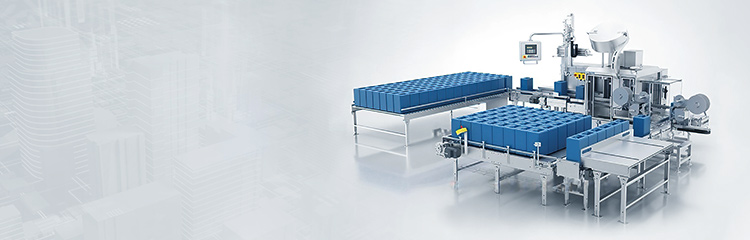
The feeding system utilizes PLC as the central control area to complete the whole process of weighing and feeding. The PLC central control area sends out a signal to start the corresponding solenoid valve to inject the liquid into the reaction kettle, and at the same time, the weighing module starts to work. When the amount of liquid in the reaction kettle increases to the same value as the weight set by the quantitative setting finger, the central control area receives the action signal from the weighing module, and immediately closes the solenoid valve for adding liquid and stops adding liquid. Automatically start the stirring switch, the control area sends out the instruction to start the corresponding solenoid valve of the mixer and the timer set by the program starts to time, the mixer stirs the solution evenly; when the timer time reaches the set value, the control area sends out the instruction to close the solenoid valve and stops the stirring.

Feeding system is a kind of production equipment used in industry for processing different powder or liquid materials in certain proportion automatically and accurately, which usually consists of Weighing system, weighing control instrument, PLC system and upper computer. Weighing system includes raw material storage body, conveying body, weighing and dosing body, dust removing body, material mixing body and other equipments; the dosing method can be reasonably selected according to the characteristics of the industry, the requirements of the production process, the specific characteristics of the material, such as "incremental" or "decremental" weighing method, with a single hopper single material, single hopper multi-materials, multi hopper multi-materials and other modes of operation.
The feeding system utilizes PLC as the central control area to complete the whole process of weighing and feeding. The PLC central control area sends out a signal to start the corresponding solenoid valve to inject the liquid into the reaction kettle, and at the same time, the weighing module starts to work. When the amount of liquid in the reaction kettle increases to the same value as the weight set by the quantitative setting finger, the central control area receives the action signal from the weighing module, and immediately closes the solenoid valve for adding liquid and stops adding liquid. Automatically start the stirring switch, the control area sends out the instruction to start the corresponding solenoid valve of the mixer and the timer set by the program starts to time, the mixer stirs the solution evenly; when the timer time reaches the set value, the control area sends out the instruction, the solenoid valve closes and the stirring stops.
Dosing equipment performance characteristics:
Reliable system, strong applicability, high weighing precision, high automation precision, stable quality, easy to manage.
Electronic weighing display design, high measuring precision, easy to calibrate and maintain.
Data processing, the Batching system can automatically operate and process the collected signals, so as to automatically control the normal operation of the equipment.
Communication function, bi-directional data communication between industrial control machine, PLC and meter.
Monitoring function, detect and monitor the instantaneous flow rate, daily totalization, monthly totalization, yearly totalization and other parameters of the batching process.
Screen display, through the computer monitor or weighing instrument can display the operation status of the relevant control parameters in the dosage process.
Professional material handling capacity, with the characteristics of the user measurement of raw materials, the use of various types of Feeder and inlet and outlet valves.
Friendly man-machine interface interface, can be connected to various types of controllers, the implementation of quantitative measurement or batching process control.
A variety of control modes can be selected, PLC, human-machine interface, microcontroller, industrial control computer and other types of control.