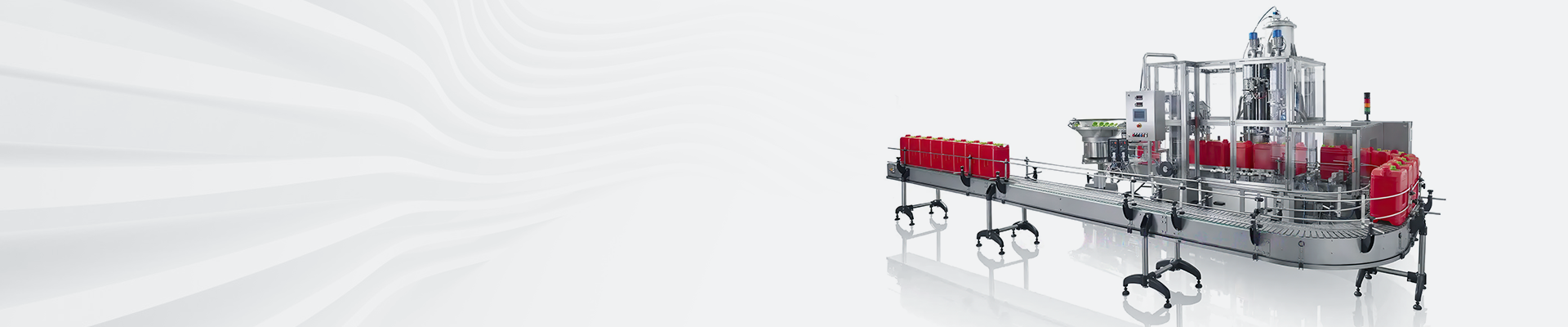
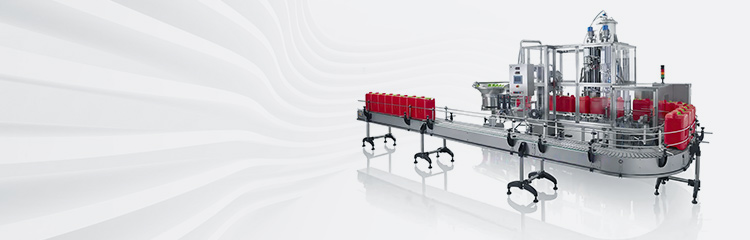

Summary:The automatic dosage system sends liquid raw materials through pipeline pump, sends powder and solid lump raw materials through conveyor belt or screw conveyor, and distributes them to each dosage port, and AGV runs automatically to receive materials between each dosage port, so that the material from the beginning of the tank to the completion of the dosage realizes the automation of the whole line.
Ink is an important material used for printing. With the rapid development of China's economy, the prosperity of the printing and packaging industry has led to the rapid growth of the ink manufacturing industry, making China in the last decade or so quickly rose to become one of the world's major ink manufacturing countries. But at the same time, ink production is also deficient, which is not a high degree of automation, production process technology innovation ability is not strong, etc. Seriously impede the development of the ink industry, mainly reflected in the following aspects:
1. Artificial formula and scheduling management is inefficient, in the face of a large number of materials and formulas, the dosage production line adopts artificial management and scheduling, which inevitably causes confusion; the operators are exposed to various kinds of dust for a long time, which jeopardizes their health.
2. Manual weighing affects the product quality, manual weighing and dosage is easy to cause mistakes or errors, affecting the effect of the formula.
3. The labor intensity of manual conveying batching bucket is high, and the phenomenon of leaking and spreading materials caused by fatigue occurs from time to time.
4. Manual batching line is difficult to respond quickly to the market demand under the new situation with low capacity and low efficiency.
Application of AGV in automatic batching system production line
In an automated feeding system production line project implemented by Kunshan, the AGV system, combined with a third-party production and batching management system, fully realizes the automatic formulation of the whole process and meets the needs of the user enterprise for continuous production operations for 8 hours on 250 working days per year.
1. AGV stand-alone design
According to the user's actual demand, AGV adopts magnetic tape guidance, two-wheel differential drive, rated load of 800 kg. AGV is mainly composed of vehicle body, weighing unit, traveling drive unit, safety protection unit, communication unit, display and operation unit, main controller and related control units.
2. Process flow and realization
AGV system combined with the third party production batching management system to realize the whole process of automatic production, process realization process is as follows:
(1) When there is a recipe task, the production batching management system generates the task and sends it to the AGV ground control system, after receiving the task, the AGV ground control system assigns the nearest idle AGV to arrive at the barrel loading station.
(2) When the AGV arrives at the barrel loading station, the AGV ground control system sends the AGV arrival information (No. x AGV arrives at x station) to the production dosage management system, at this time, the AGV maintains the stop state.
(3) After receiving the confirmation message from the AGV ground control system, the production dosage management system starts the barrel loading operation. After the barrel loading operation is completed, the batching management system sends the barrel loading completion message to the AGV ground control system.
(4) When the barrel loading is finished, the AGV ground control system commands the AGV to travel to the first feeding station, when the AGV reaches the first feeding station, the AGV ground control system sends the AGV in place information to the production dosage management system, and then the AGV keeps stopping state.
(5) After receiving the confirmation message from AGV ground control system, the batching management system will carry out the batching operation until the batching is finished, and then the batching management system will send the message of "batching finished" to AGV ground control system.
(6) The production batching management system determines whether it is the last feeding station, if not, the production batching management system sends the next feeding station information to the AGV ground control system, and the AGV ground control system directs the AGV to travel to the next feeding station, and repeats the two processes of (5) and (6); if it is the last feeding station, the production batching management system sends the next barrel station information to the AGV ground control system, and the AGV ground control system sends the "feeding completed" message to the AGV ground control system, and the AGV ground control system sends the "feeding completed" message to the AGV ground control system. The AGV ground control system commands the AGV to travel to the next barrel station.
(7) When AGV arrives at the bucket work station, AGV ground control system sends AGV in place information to the production dosage management system, at this time, AGV keeps stopping state.
(8) The batching management system receives the confirmation message from the AGV ground control system and carries out the pail operation, when it is finished, the batching management system sends the pail finished task end message to the AGV ground control system, the AGV ground control system receives the task end message and puts the AGV into the idle state, waiting for the next handling task.
In addition to the above normal workflow, the automatic operation also includes midway formula change and abnormal termination and other processes.
Application effect of AGV system
After the batching control system production line is put into use, it takes less than one shift (6 hours) to complete the same workload of two shifts (16 hours) per day, which greatly improves the working efficiency and product quality. The main performance is:
1.Informatization to improve efficiency
AGV system with the production of batching management system to achieve the informationization of the entire batching line, from the generation of the formula issued to the completion of the task implementation, eliminating a variety of human confirmation and recording links, the workflow is smooth and efficient. It provides perfect and convenient means for on-site customization and management of process formulas, automatic issuance and execution of formulas, change and re-completion of formulas, interruption of formulas, formula query, treasury and material management, etc., so that the efficiency of on-site management of formulas has been greatly improved.
2.Automatic distribution improves efficiency
Various raw materials are pre-stored in the storage tanks, when it is necessary to formulate, the liquid raw materials are pumped through the pipeline, the powdered and solid lump raw materials are distributed to the dosing ports through the conveyor belt or screw conveyor and other devices, and the AGV automatically runs between the dosing ports to receive the materials. The material from the storage tank to the completion of the batching to realize the whole line of automation, greatly improving the production efficiency.
3.Automatic weighing improves efficiency
AGV batching and weighing mode is a new application mode combined with batching production line, which provides a strong guarantee for realizing the refinement of formula, accuracy, flexibility, over-difference treatment and fault tolerance.
To sum up, the practical application of AGV in the feeding system production line greatly improves the production efficiency, reduces the labor intensity, and fully demonstrates that in the scientific combination of the production process, AGV as a flexible automation equipment can improve product quality and improve the production efficiency of the huge advantages. The successful implementation of this project also provides reference and demonstration for food, pharmaceutical, chemical and other industries with similar production processes.