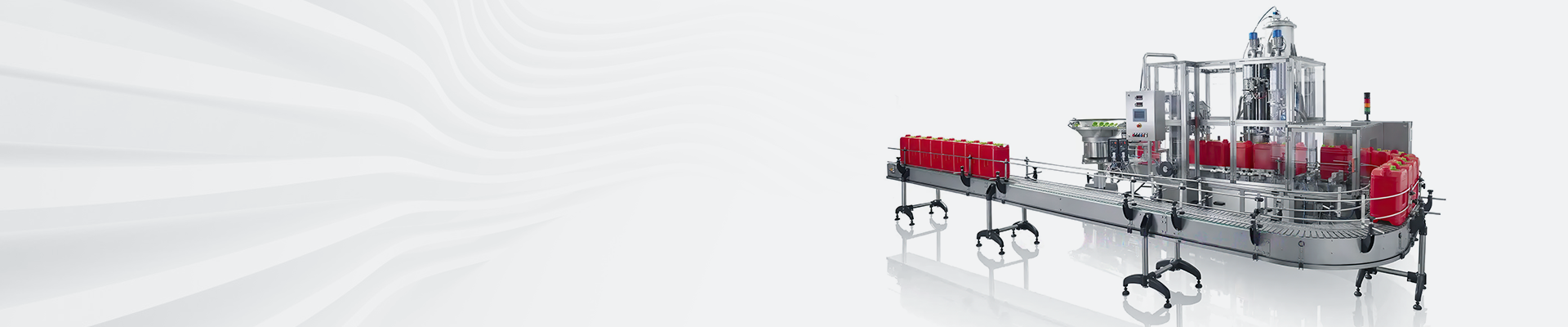
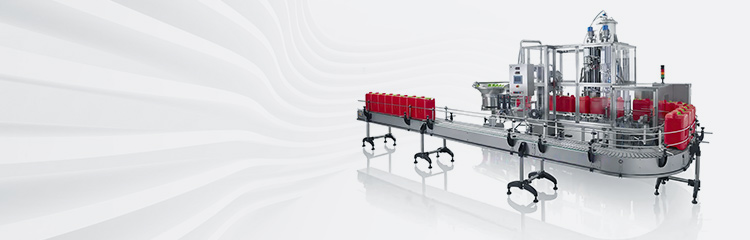

Summary:The entire automatic batching system is fed in batches to the reaction kettle of the weighing instrument. The temperature of the reaction kettle and the current of the motor are automatically batched and displayed on the PC, and the data is recorded and saved by the software.
AI-708HAI2L4S host is AI-708H Intelligent Flow Accumulator with 96×96 external dimensions. after insertion of the module, the inputs are opto-isolated digital inputs for frequency/switching type inputs, with 12VDC voltage outputs; the outputs are normally open (resistive-absorptive) outputs for relay high-capacity contacts (265VAC/2A); and with opto-isolated RS485 communication interface. interface.
Function: In practical application, after re-calibrating the load cell to get the flow range, the FDIH of the weighing instrument should be reset, the weighing instrument can accurately calculate the flow of the material according to the frequency, and close the solenoid valve at the right time according to the value set by the user, so as to achieve the accurate and automatic batching of the material.
AI-704MFJ0J4V24S host for the AI-704M multi-circuit inspector, the external shape is 96 × 48. After inserting the module, the inputs are 1 three-wire PT100 and 2 current; external isolation 24V/50mA DC voltage output can be used for the transmitter; with photoelectric isolation RS485 communication interface.
Function: Collect the temperature of the reactor and the current of the reactor motor to be uploaded to PC, displayed on the process screen and saved as history.
AI-501FSV24 mainframe single-channel measurement and display alarm meter, the external shape is 96×48, for 1 channel current input. After inserting the module, the external isolated 24V/50mA DC voltage output which can be used for transmitter; with opto-isolated RS485 communication interface.
Function: Collect the current of the reactor motor and upload it to PC, display it on the process screen and save it as a history record.
Process requirements
1. The system function of AI-708H flow totalizer can be fully operated on the computer for dosing all 14 reactors.
2. Record the temperature of the bottom of the kettle and the reaction tank in real time, and at the same time, according to the current size of the kettle motor to understand the reaction of polyurethane.
3. Record and save all data for future inquiries.
4. Real-time data provides time query, and the charging history data of the reactor provides "reaction tank number" and "batch number" query.
5. Provide real-time curve, real-time alarm and alarm limit modification.
6. Provide operating privileges and settings to prevent misoperation.
Operation Description
After the software is normally logged in now take "MK-12A reaction tank" as an example to describe in detail how to operate the software AI-708H type flow totalizer for the reaction tank charging quantitative dosage control system process:
In the AI-708H weighing instrument communication status and MK-12A temperature and current display value of the communication status shows "communication is normal" in the case that the weighing instrument and computer connection is normal.
Click on the "Data reset" button on the left side of the loading system table to reset the set point data of the AI-708H scale to zero, and at the same time to reset the feeding relay and initialize the scale.
Click the red valve next to "MK-12A" to activate the reaction tank, and use the switching automatic dosage system function of AI-301M module to open the high-pressure electropneumatic ball valve of the reaction tank, so that the pipeline is smooth, and make the valve turn green at the same time. Corresponding data will be displayed in the operation bar of the yellow box in the center. At the same time, the "Reaction Start" button is displayed.
After filling in the relevant information of the dosage tank, enter the amount of material to be fed in the input box under "given value", and then click "feed" that is, open the relay of the automatic dosage system, and start feeding, with the animation of pipeline feeding, and "feed amount" will be displayed in the operation bar in the center yellow box. The "feeding quantity" will be increased correspondingly, when the "batch cumulative flow" and the "given value" are the same, the feeding will stop, and the high-pressure electropneumatic ball valve of the reaction tank will be closed automatically (if there is any error in testing, we will use "FSV" to test it). (if there is any error during the test, use "FSB" to adjust).
Please click "Reaction Start" immediately after the dosage is completed, and the ACCESS database will record the current dosage data of the reactor and the start time of the reaction. The data will be displayed on the reactor at the same time, and the "Reaction End" button will appear.
If it is necessary to recharge, please click "Automatic dosage system data reset" to clear the data of automatic dosage weighing instrument (AI-708H), then click the small valve of MK-12A to open the high-pressure electropneumatic ball valve of the reactor, then set "Automatic dosage system given value", then click "Automatic dosage system given value", and then click "Automatic dosage system". "Then click "Dosing". After the dosage is completed, please click on the button "Record dosage" to record the data of dosage again.
During the reaction, if the current data is >5A, the stirrer and the liquid level are animated and the temperature and current data under the kettle are green.
When the reaction is finished, please click "End of Reaction" to record the time of the end of the reaction, so that the data curve can be queried in the future.
This is the end of the production of polyurethane resin in MK-12A reaction tank.
The software provides a large number of permissions, data processing and query functions.
User Login" allows you to log in again after logging out. (This software does not allow you to operate the weighing instruments and data without logging in.)
Report query" software database recording interval is 1 minute, can record 1 year's data. There are 5 reports, Data Report A, Data Report B, Data Report C, Data Report D and Alarm Report. (Data can be queried by time) as follows:
"Curve Query", select the corresponding reaction tank number, and the following pop-up will appear:
Input "process grade" and "batch" and click query, you can query the corresponding curve (you need to adjust the horizontal coordinate according to the actual situation, the default is 30 hours) (the temperature inside the reaction tank, the temperature at the bottom of the reaction tank and the electric current are displayed in a curve at the same time, which is convenient for you to query). (The temperature inside the reaction tank, the temperature at the bottom of the reaction tank and the current are displayed in one curve at the same time, which can be easily queried). This curve can also be used as a historical curve query data, please click the seventh button to operate.
Real-time Alarm" will pop up automatically when there is data alarm.
Alarm Answer" is used to make sure that the alarm message has been noticed.
Alarm Setting" is used to set the alarm limit of the data.
Privilege Management" is used to change the login password and add the personnel who can login.
The "Start/Stop Meter" function is used to activate the weighing instruments that need to be used, and to deactivate the ones that are not in use and that are not communicating properly. The production process and the material status can be completely monitored by the computer generating real-time curves and reports, and all the related historical data are saved in ACCESS database, with perfect historical reports and curves for future inquiries. Conclusion
The automatic batching machine has been running successfully for more than half a year, and the second set of automatic feeding system has entered the commissioning stage. The on-site operation proves that the AIFCS computer monitoring system based on AI weighing instrument and field bus is reasonable in both software and hardware design, reliable in operation, convenient in operation, and has strong anti-interference, which greatly improves the production efficiency of the polyurethane resin, and makes its industrial batching level jump to a new level.