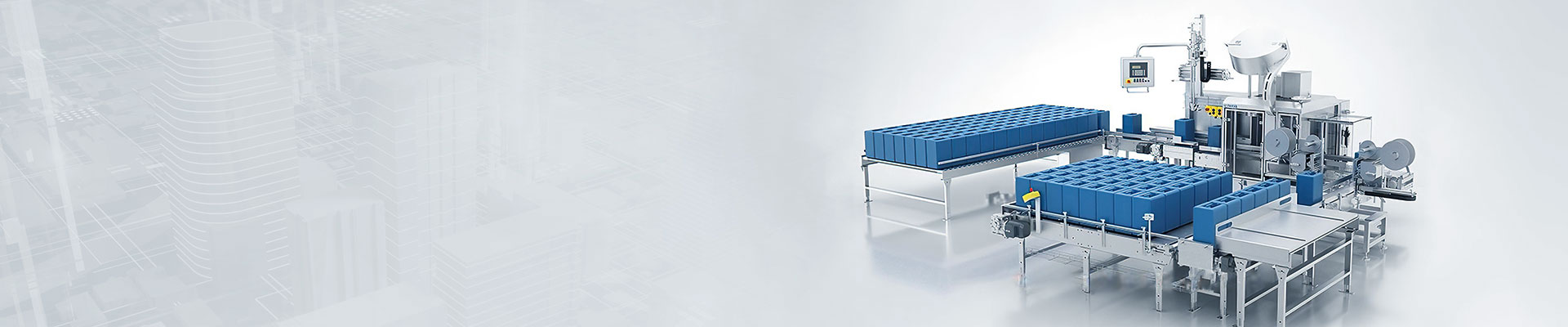
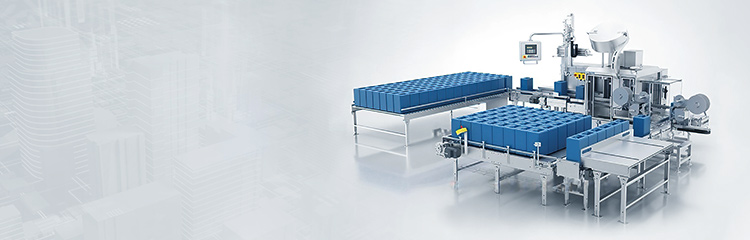
Automatic mixer to achieve material transfer, batching control, formula design, production data management and other functions. And it can realize the collective control of multiple batching systems through the network. The double helix structure is installed in an "8" shaped body, and the material in the body is moved forward by a forward thrust as the spiral rotates.

he automatic mixer is set to input the formula of the batching and allocate the required raw material quantity proportionally. The method of dynamic measurement precision control is adopted. An automated production line for the whole production process of conveying, proportioning, mixing and packaging of finished products for various types of materials. Using PLC control mode and novel variable frequency speed regulating feeding mechanism, with the batching control software package, the functions of material transfer, batching control, formula design and production data management are realized. And it can realize the collective control of multiple Batching systems through the network. The double helix structure of the conveyor, the double helix structure installed in an "8" body, with the spiral rotation, the body of the material by a forward thrust forward movement, at the same time, in this process, the material is squeezed, so that the body has a certain sealing effect, then there is a certain sealing pressure, so, This conveying structure has a good effect on conveying wet materials such as powder, paste and filter cake.
The mixing system mainly includes signal input and conditioning module, data acquisition module, batching control and calculation module, input and display module, motor drive module and discharge valve drive module. The weighing module converts the weighing signal into A voltage signal, which is amplified and adjusted by the transmitter, and converted by the data acquisition card for A/D conversion, and the generated digital quantity enters the weighing instrument for processing. These quantities can be displayed in the display, and can also feedback and adjust the motor, push device and discharge valve to coordinate the action. The preset values are entered into the weighing instrument by the keyboard.
The working process of the mixer is divided into three stages: (1) material preparation stage (2) coarse weighing stage (3) fine weighing stage. The last two stages are executed in a cycle after the machine is started until the end signal is given and the whole process is over. The operation mode is firstly put the pneumatic ball valve by the operator to the stroke 1 of the spiral, and the pneumatic ball valve is brought to the discharge port of the coarse weighing material unit by the spiral, that is, the stroke 2, and the stroke switch is touched; At the same time, the coarse weighing unit starts, when the stroke switch and the preset value of the coarse weighing meet the requirements, the coarse weighing unit will open the discharge port, and the material will fall into the pneumatic ball valve under the hopper; Delay for a certain time, so that all the materials of the coarse weighing unit fall, and then push the pneumatic ball valve to the discharge port of the fine weighing unit by the push mechanism, that is, stroke 3, and touch the stroke switch, at this time the fine weighing unit repeats the action of the coarse weighing unit, completing a coarse weighing and fine weighing process. When the push device pushes the first pneumatic ball valve to the discharge port of the fine weighing unit, the coarse weighing unit does not need to wait, and directly starts the next coarse weighing. The pneumatic ball valve accepting the blanking in the fine weighing unit will be sent to the discharge table by the push mechanism. Double core weighing material can make coarse weighing and fine weighing at the same time, with easy operation, accurate and reliable measurement, high production efficiency.