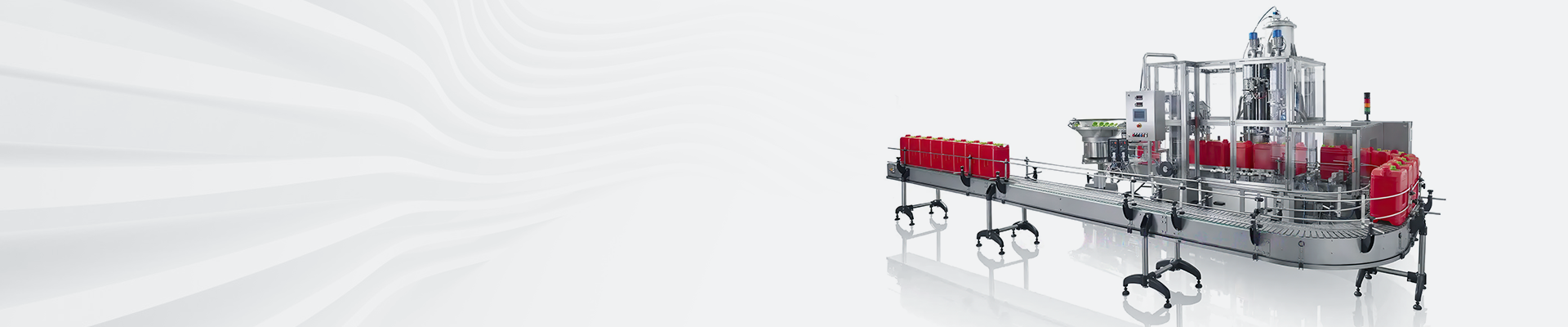
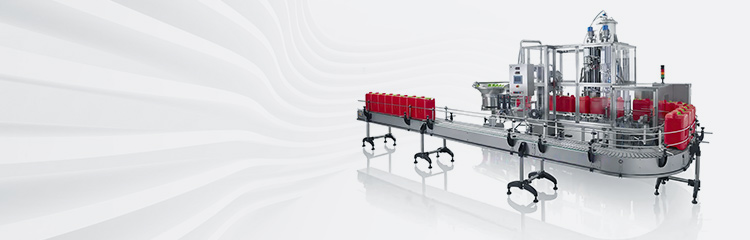

Summary:The automatic bulk scale is mainly composed of feeding, weighing, screwing, vibrating, conveying, rechecking and automatic sampling. Since FCC catalyst has the characteristics of small particle size (average particle size 75~85μm), good fluidity and strong abrasion to the equipment, the inclined single-cantilever double-screw feeding method is adopted in this equipment; in order to meet the requirement of controlling speed.
The Catalyst Plant of PetroChina Lanzhou Petrochemical Company is the exclusive FCC catalyst production base of PetroChina, with an annual comprehensive production capacity of more than 50,000t of mainstream products. FCC catalyst has excellent fluidity and strong abrasiveness, which requires high sealing and anti-wear requirements for the equipment. Its traditional weighing and control are carried out manually, and the metering accuracy and control speed can not meet the needs of mass production, and because it can not operate under sealed conditions, the working environment is dusty, which also causes catalyst runout loss. The automatic bulk scale is designed here, and the weighing control system can meet the needs of accurate measurement and automatic control of catalytic cracking catalyst, and can control the mixing of two kinds of catalysts. In order to improve the loading accuracy should also have the function of adjusting the drop time and drop impact volume, giving the average value and error distribution of each control weight. Improve the power execution element, steam valve, motor, solenoid valve quantitative scale control speed and accuracy, here focus on the structure of the bulk scale and its information architecture.
1 The structure of the automatic bulk scale composition
Automatic bulk scale is mainly composed of feeding, weighing, spiral, vibration, conveying, review and automatic sampling and other parts. Since the catalytic cracking catalyst has the characteristics of small particle size (average particle size of 75~85μm), good fluidity and strong abrasion to the equipment, the inclined single-cantilever double screw feeding method is adopted in this equipment; in order to meet the requirements of the control speed, the bulk scale adopts the design of double weighing device; the weights of the hopper scales of A and B can be set according to the needs of the formula when the double materials are controlled; the casing vessel of the screw device is round, which can ensure the discharge of the material. The spiral device of the sleeve container is round, which can ensure the sealing of the discharge port; at the same time, it is designed with a secondary discharge door and a dust collector, the secondary discharge door can reduce the dust in the container caused by the direct discharge, and make the hopper scale maintain a relatively stable pressure environment to reduce the impact on the weighing accuracy; the dust in the dust collector of the container is automatically discharged to control and reuse.
An automatic scale that weighs/controls materials according to their weight at a predetermined weight and accuracy. Usually consists of screw conveyor, weighing module (generally composed of hopper scale and load cell, etc.), weighing instrument and control pneumatic valve system machinery. Its forms include: bulk scales, multi-bucket combination scales, totalization scales and reduction scales. For bulk scales in addition to the requirements of weighing accuracy, but also the requirements of weighing speed, due to the impact of the material falling momentum and other factors caused by the instability of the loading time. The end of loading and unloading end, the hopper scale to reach a stable state, you can measure the weight of the material and the time of the unloaded weight.
Quantitative weighing process of the weighing accuracy of the hopper, the uniformity of the screw conveyor feeding device under the material, can control the accuracy of the material under the material, and can meet the fast feeding and slow fine feeding. Bulk weigher weighing method is divided into two categories: single weighing and portion weighing. In order to improve the weighing speed of single weighing quantitative scales can also have two hopper weighing, two hopper weighing can be rotated weighing can also be arranged on the upper and lower weighing scales, the upper hopper to do the coarse material flow weighing, in the end of the feed, the material is unloaded into the hopper below the scales, and then accept the fine material flow to feed until the set weight. At this time, the upper hopper is loaded at the same time to achieve the purpose of improving the weighing speed.
2 working principle
The electrical control system of automatic bulk scale is mainly composed of mettler toledo weighing controllers T600.2, S7-224, touch screen TP177 and schneider inverter ATV31. The equipment has two working modes: automatic and manual. When using the automatic working mode, the automatic operation button of the touch screen is turned on, and the weighing controller sends a fast or slow feeding signal to the PLC, and the PLC controls the feeding door to open, so that the fast feeding motor and the slow feeding motor run simultaneously; When the preset slow feeding value is reached, the weighing controller stops the fast feeding signal, the PLC controls the feeding door to close to the neutral position, and the fast feeding motor stops running; When the preset advance is reached, the weighing controller stops the slow feeding signal, the feeding door closes and the slow feeding motor stops running. The discharge door is opened, and the material is put into the control container through the secondary door.
3 Operation effect
After practical application in the field, the equipment runs stably, and its main characteristics are: the weighing accuracy reaches 0.2%; Fully enclosed, with little environmental pollution, the dust on the work site is greatly reduced compared with the traditional control method, which protects the health of workers; The operation is simple, and the working efficiency is improved by operating and setting parameters through the touch screen; Convenient maintenance, the system has fault self-diagnosis function, and the results are directly displayed on the touch screen, which shortens the maintenance time; And the labor intensity of workers is reduced.
4 Conclusion
At present, the automatic quantitative control scale for powder has been widely used in the domestic market, but the automatic quantitative scale for catalytic cracking catalyst is still in the experimental stage. The successful application of the quantitative automatic bulk balance designed by the catalyst factory of China Petroleum Lanzhou Petrochemical Company fills a gap in the control equipment of FCC catalyst in China, and also summarizes a successful experience for automatic weighing of ultra-fine particles with strong wear. At present, the above successful experience has been successfully used in the ton control of this factory.