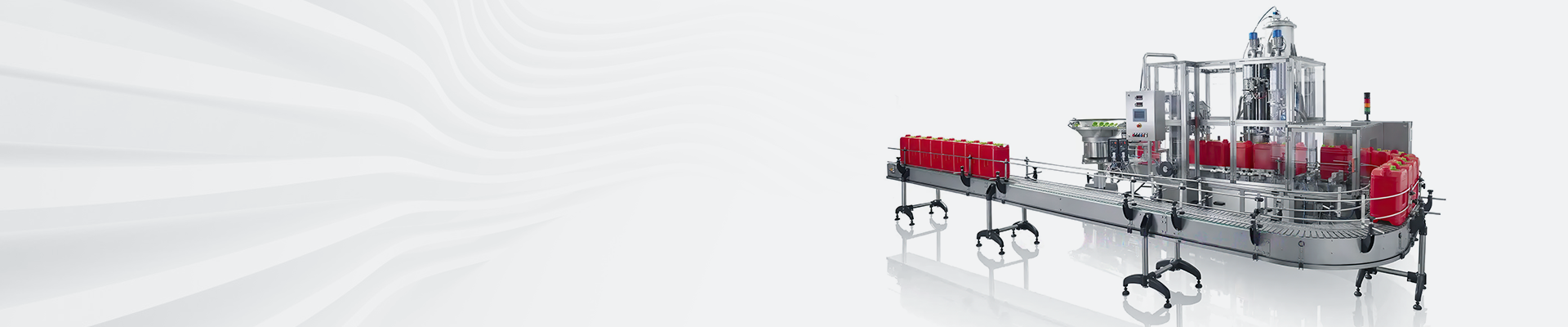
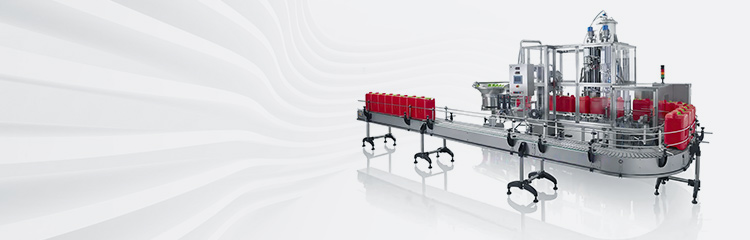
摘要:自动散料秤主要由给料、称重、螺旋、振动、输送、复检及自动采样等部分组成。由于催化裂化催化剂具有颗粒小(平均粒径75~85μm)、流动性好以及对设备的磨损强等特点,所以在该设备中采用倾斜式单悬臂双螺旋给料方式;为了达到对控制速度的要求。
中国石油兰州石化分公司催化剂厂是中国石油专属的催化裂化催化剂生产基地,主流产品年综合生产能力达5万t以上。催化裂化催化剂具有优异的流动性和的较强的磨损性,对设备的密封性和抗磨损要求很高,其传统称重和控制都采用人工方式进行,计量精度和控制速度都不能满足大批量生产的需要,而且由于无法在密封条件下作业,工作环境粉尘大,也造成催化剂跑损。在此设计自动散料秤,该称重控制系统能够满足催化裂化催化剂的准确计量与自动控制的需要,并且可以进行两种催化剂的混合控制。为了提高装料精度还应具备调节落料时间和落料冲击量的功能,给出各控制重量的平均值和误差分布。提高动力执行元件,汽动阀门、电机、电磁阀的定量秤控制速度和精度,在此着重介绍散料秤的结构及其信息架构。
1 自动散料秤的结构组成
自动散料秤主要由给料、称重、螺旋、振动、输送、复检及自动采样等部分组成。由于催化裂化催化剂具有颗粒小(平均粒径75~85μm)、流动性好以及对设备的磨损强等特点,所以在该设备中采用倾斜式单悬臂双螺旋给料方式;为了达到对控制速度的要求,散料秤采用双称重装置设计;在控制双物料时可根据配方的需要设定A、B料斗秤的重量;螺旋装置的套容器处为圆形,可保证出料口的密封;同时设计有二次卸料门和除尘器,二次卸料门可以减少直接卸料引起的容器内粉尘,并使料斗秤保持相对稳定的压力环境,减少对称重精度的影响;容器除尘器内的粉尘自动排出控制回用。
根据物料的重量按预定的重量和精度进行称量/控制的自动秤。通常由螺旋输送机,称量模块(一般由料斗秤和称重传感器等组成)、称重仪表和控气动阀门制机械组成。其形式大致包括:散料秤、多斗组合秤、累加秤和减量秤等。对于散料秤除要求称重准确性外,还需称重速度的要求,由于物料下落冲击动量等因素造成的不稳定加载时间。加载结束及卸料结束,料斗秤达到稳定状态,可以测量物料重量和空载重量的时间。
定量称重过程中对料斗的称重精度,螺旋输送机给料装置下料的均匀性,能控制下料的精度,并能满足快速给料和慢速精细给料。散料秤的称量方式分为单次称量和分量称量两类。为了提高称重速度单次称量定量秤也可有两个料斗称,两个料斗称可分别轮换称重也可上、下布置称量秤,上面斗做粗料流称重,在给料结束后,把物料卸入下面的料斗秤,再接受细料流给料直到设定重量。此时上料斗同时装料,达到提高称重速度的目的。
2工作原理
自动散料秤的电气控制系统主要由梅特勒-托利多称重控制器T600.2、S7-224、触摸式显示屏 TP177及施耐德变频器ATV31等组成。该设备具有自动和手动两种工作模式。在使用自动工作模式时,开启触摸屏的自动操作按钮,称重控制器向PLC发出快或慢加料信号,PLC控制加料门打开,快加料和慢加料电机同时运行;当达到预置慢加料值时,称重控制器停止快加料信号,PLC控制加料门关闭到中位,快加料电机停止运行;当达到预置提前量时,称重控制器停止慢加料信号,加料门关闭,慢加料电机停止运行。卸料门打开,物料通过二次料门投入到控制容器。
3运行效果
该设备经过现场的实际应用,运行稳定,其主要特点是:称重精度达到±0.2%;全密闭,环境污染小,工作现场粉尘量比传统控制方式有较大的减少,保护了工人的身体健康;操作简单,通过触摸式显示屏操作并设置参数,提高了工作效率;维护方便,系统有故障自诊断功能,结果直接显示在触摸显示屏上,缩短了检修时间;减轻了工人的劳动强度。
4结束语
目前国内市场用于粉料的定量自动控制秤已有广泛应用,但是应用于催化裂化催化剂的自动定量秤还处于试验阶段。中国石油兰州石化分公司催化剂厂设计的定量自动散料秤的成功应用,填补了国内催化裂化催化剂控制设备的一项空白,也总结出了一种用于磨损强、超微颗粒物料自动称重的成功经验。目前以上成功经验已在该厂的吨控制成功使用。