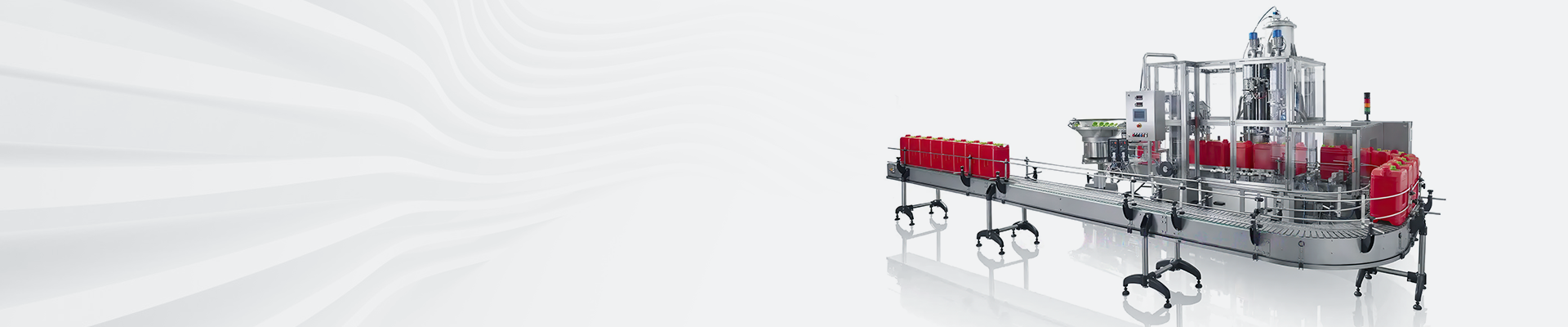
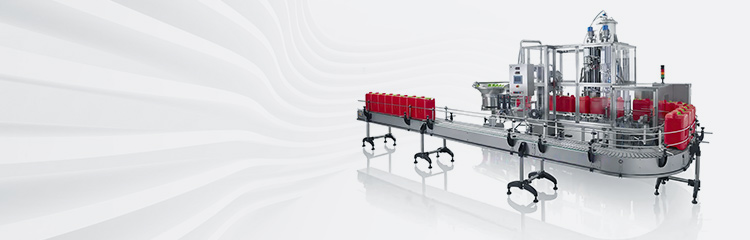

Summary:The automatic batching system can realize start, stop, frequency setting (speed setting), left turn, right turn, connection task setting, connection parameter setting, etc. The multi-motor interface allows intuitive operation and realizes human-machine dialogue.
In papermaking, textile, printing and dyeing, metallurgy and other multi-unit electrical drive system, often using multiple AC motors or DC motors as a dragging device, and multi-motor synchronous drive automatic dosage technology is the core of the dosage system, which directly affects the reliability of the system and automatic dosage precision. With the development of power electronic technology, communication technology, computer technology and modern automatic feeding system theory, the use of microcomputer automatic dosage system by the all-digital synchronous drive automatic dosage device to achieve high precision, high reliability of synchronous automatic dosage of China's industrial development is of great significance.
This paper adopts distributed feeding system based on CAS2005 to realize multi-motor synchronous drive automatic dosage. The application of field bus and communication technology, the host computer can easily realize the serial communication with any inverter on the bus: sending automatic dosage information, setting operation parameters, reading operation status, adjusting the output frequency (i.e., motor speed), etc.; fuzzy automatic dosage algorithm used to improve the dynamic performance of the system, completely solve the problem of automatic dosage brought by the transmission system, which is difficult to solve the problems caused by the field interference, as well as the large inertia of motors and the long time of lagging. The use of fuzzy automatic dosage algorithm improves the dynamic performance of the system, completely solves the automatic dosage problems brought by field interference and factors such as large motor inertia and long hysteresis time to the transmission system, and improves the system reliability.
2 design program
This feeding system is a two-level computer system, the upper level for the supervision of the dosage, for computer monitoring and operation, connected through the RS232 bus; the lower level for the CAS to the inverter dosage, for real-time automatic dosage of the scene, connected through the RS485 bus, the equipment through the acquisition of speed signals, judgment and processing to get the corresponding value of the motor running speed, and then by the RS485 bus written into the inverter. Execution.
2.1 Equipment modularization design
This system realizes automatic dosage of multi-motor synchronous drive by dosage equipment. A project is set up in the dosage software programming environment AS, which includes four task modules: motor speed feedback module, inverter communication module, host computer communication module, Profibus communication module. The modules are independent of each other and can be adjusted individually, or can be imported or exported as a module to a project.
Task 1 is responsible for completing the acquisition of field data, regulation through the look-up table, the highest real-time requirements, should have the highest priority;.
Task 2 is responsible for the communication between the device and the field system equipment, is a very important task, the real-time requirements are also very high, should be placed in a higher task level; Task 3 to complete the data display, the real-time requirements are not high, but need to run for a long time; Task 4 is responsible for the completion of the Profibus communication function to achieve communication between the CAS, the requirements of the fastest possible.
From the multi-tasking principle of the device, it can be seen that the high-priority tasks should interrupt the low-priority tasks, ensuring that the more important tasks can be completed first. After the dosage is completed, if a new task needs to be added, simply add the new task to the project.
2.2 Realization of serial communication
Weighing and batching system has been launched with a standard interface of general-purpose frequency converter, for users to design to meet the needs of the industrial field of batching has brought great convenience, but there are still a lot of companies have their own communication protocol of the frequency converter. micr.master6SE3115 frequency converter is an earlier product, it does not support the standard communication protocol, but the actual batching site requirements and the frequency converter to communicate with the ordinary PLC does not have a third-party communication protocol, but the actual batching site requirements and the frequency converter to communicate with the ordinary PLC does not have a third-party communication protocol with the frequency converter. Ordinary PLC does not have the ability to communicate with third-party products, resulting in huge difficulties in system integration, allowing developers to develop communication protocols from the bottom is a complex and considerable amount of work, and the reliability of the dosage is difficult to ensure. Based on the above problems, a 2000 series CAS products in addition to supporting the standard communication protocols, but also provides users with protocol development tools for communication with third-party products --- frame driver, users only need to understand the communication protocols of third-party products (including the composition of the information frame format, etc.), and use the frame driver to develop the communication protocols of third-party products. Users only need to understand the communication protocol of the third party product (including the composition of the information frame format, etc.), and use the frame driver to write the same communication protocol as the communication protocol of the third party product, so that the communication between CAS and the third party product can be easily realized. This system utilizes the frame driver of CAS to successfully realize the automatic dosage of CAS communication to multiple inverters. The dosing serial communication program is used to develop as a complete task module can be added to any other complex task, not only to improve the reliability of the system, but also to improve the reusability of the code and shorten the project development cycle.
The device and the inverter are connected via RS-485, and each inverter is set up with its own independent address code (0-31) to identify its own identity, so that the CAS can operate the automatic dosing system for all the inverters hooked up to the bus via the RS-485 interface.
2.3 PVI-based serial communication with the host computer
The PVI Process Visualization Interface is a software module based on the Win32 platform that manages the exchange of data between the application and the fieldbus. the PVI applications all use the PVICOM.DLL interface to achieve communication with the PVI Manager. When the PVI manager data has changed, PVICOM interface through the Windows message (or callback function) to notify the application program for data processing. PVICOM interface provides users with a large number of functions used to achieve serial communication, the use of these functions can be very easy to write RS232, RS485, CAN, PROFIBUS and other communication programs, and the program is highly portable. The portability of the program is strong, for different communication media and communication protocols, only need to modify the corresponding PVI parameters to achieve the communication task, which greatly shortens the project development cycle and improves the reusability of the application.
The above communication process is encapsulated, through VB, VC or Delphi software programming to provide users with automatic dosage system interface, the user only needs to operate the interface intuitively to realize the start, stop, frequency setting (speed setting), left turn, right turn, connecting task setting, connecting parameter setting, etc., so as to realize the human-computer dialogue automatic dosage system. This paper uses Delphi programming, its user interface.
3 speed feedback automatic dosage circuit design
In papermaking, printing and dyeing industry, due to the non-extensibility of the product, so in order to prevent it from breaking, curling, indentation, it is necessary to carry out automatic dosage on the speed of each transmission part. The principle of this system on the speed of the automatic dosage is the use of photoelectric encoder feedback speed signal, by the equipment of the NC150 module counts the number of pulses, forming a closed-loop automatic dosage circuit. The actual value of the speed is compared with the set value of the speed and fed back to the execution structure through the fuzzy automatic dosage algorithm. In order to overcome the time prolongation caused by the large inertia of the motor, the long lag time of the input regulation and the large amount of overshooting, an intelligent automatic dosage method is selected in the experimental process through the combination of hardware and software. Experiments have proved that the use of fuzzy automatic dosage algorithm can play a precise and quick role in regulating the speed fluctuation of the motor caused by load change, voltage fluctuation, external interference, etc., and at the same time, it can reduce the start-up time of the motor, and improve the accuracy of automatic dosage for synchronous transmission of multiple motors.
4 Intelligent dosage principle
Due to the object model is difficult to be precise, the system is nonlinear, at the same time, inertia, long lag time and other factors exist, making it difficult to meet the requirements of the traditional PID automatic dosage, decided to use fuzzy automatic dosage system. To improve the accuracy and tracking performance of the fuzzy automatic dosage system, it is necessary to take more linguistic values for the linguistic variables, and the finer the grading, the better the performance. The fuzzy automatic dosage system applied in this paper is a typical dual-input single-output two-dimensional fuzzy automatic dosage with three variables, i.e., deviation E, deviation change EC and automatic dosage amount f.
4.1 Fuzzification process
Fuzzification refers to the transformation of the exact values of the input variables into the values of linguistic variables (fuzzy input values) on the appropriate thesis domain, for the characteristics of the motor speed deviation range is large and the accuracy requirement is high, the quantization level of the three linguistic variables is taken to be 15, i.e., {-7, -6, -5, -4, -3, -2, -1, +1, +2, +3, +4, +5, +6, +7} for the convenience of designing and calculating the The affiliation function of the input and output fuzzy subsets uses triangular curves, and the linguistic variables take seven values, namely, "Positive Big" (PB), "Positive Medium" (PM), "Positive Small" (PS), "Positive Small" (PS), "Zero" (PS), and "Positive Big" (PB). (PB), "positive medium" (PM), "positive small" (PS), "zero" (ZE), "negative small" (NS), "negative medium" (NM), "negative large" (NB). ).
4.2 Determination and reasoning of fuzzy automatic dosage rules
The fuzzy automatic dosage rule for a weighing and feeding system is a collection of fuzzy conditional statements summarized from the experience of the expert and the skill of the operator. Determination of the fuzzy automatic dosage rule must ensure that the output of the automatic doser can optimize the dynamic and static characteristics of the system. Here the manual dosage experience is used to derive the fuzzy automatic dosage rule table.
5 Conclusion
Through the theoretical analysis and experimental study of multi-motor synchronous drive feeding system, the application of field bus and communication technology in multi-motor synchronous drive greatly improves the accuracy of the system's automatic dosage system; fuzzy automatic dosage system algorithms, which show a strong superiority in the actual debugging process, so that the system has a good intelligent automatic dosage effect. Experimental results show that the system has the advantages of high reliability, scalability, short adjustment time, good synchronization effect, easy maintenance and so on. The automatic dosage system scheme is advanced, and combining it with specific controlled objects (such as textile, printing and dyeing, steel rolling, etc.), it can be applied to any dosage that needs to realize synchronous transmission.