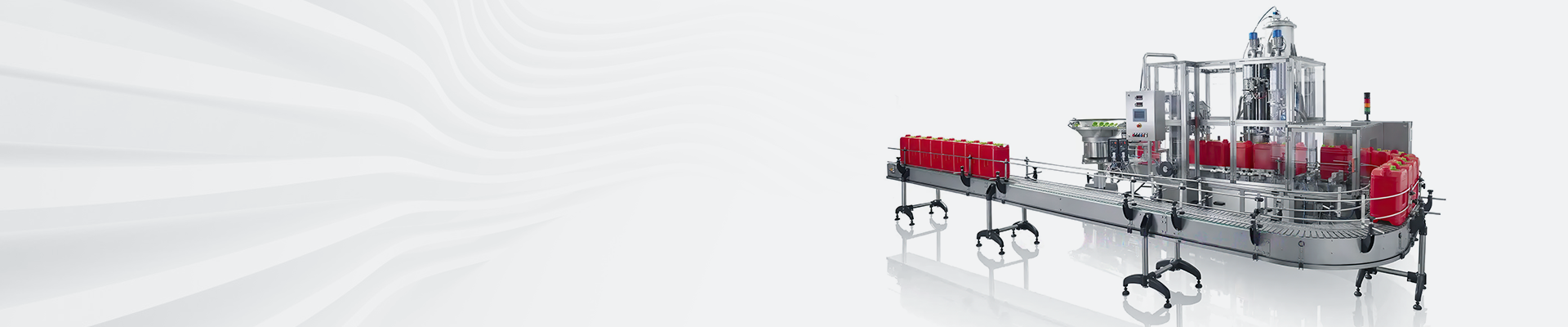
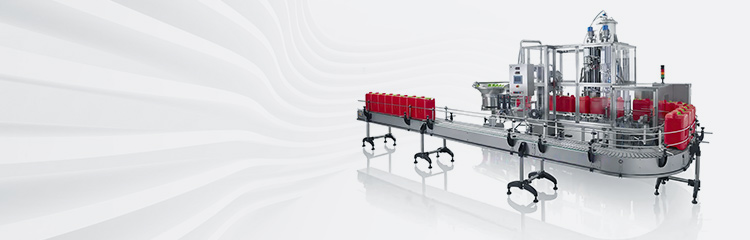

Summary:The liquid filling machine is mainly composed of a control display part, a weighing module system, a feeding system, a feeding system, a barrel clamping system, a weighing bucket, a pneumatic system and a frame structure part.
Weighing and filling machines are widely used in industries such as methanol, ink and light industry. The development of weighing and filling technology has approximately gone through several stages such as manual weighing, relay control and hard PLC control. As we all know, hard PLC is characterized by high reliability, ease of use and high resistance to harsh environments. However, with the development of computer technology, hard PLC generality and poor compatibility and other drawbacks are becoming more and more obvious. The computer's standardized communication protocols and mature LAN technology makes the network very simple, but also through the Internet and the outside world.
At present, most of the weighing and filling machine using hard PLC, when the enterprise's production scale expansion, the need to improve the filling capacity, can only use a larger capacity of hard PLC explosion-proof filling machine, so that the original hard PLC corresponding to the scrap, is bound to cause waste. The dosage system introduced in this paper only needs to modify the CoDeSys control program to improve the filling capacity, has a high value of promotion.
Liquid filling machine components and working principle
Components
The automatic filling machine is mainly composed of control and display part, weighing module system, feeding system, discharging system, clamping bucket system, weighing bucket, pneumatic system and frame structure part.
Working Principle
Urea, grease and other edible oil materials through the conveyor belt, feeding system into the weighing hopper, under the action of gravity, the weighing hopper will gravity transfer to the weighing module, so that the measurement module elastomer deformation, attached to the elastic strain beam on the strain gage bridge to lose equilibrium, the output of the weight and the value of the proportionality of the voltage signal, through the linear amplifier to amplify the signal, through the A/D converter converted to digital signals, processed by the single-chip microcomputer After processed by MCU, it displays the current material weight, various setup parameters and working process status, and sends out signals such as coarse feeding, fine feeding, weighing completion, and upper and lower limit alarms, etc. These signals are connected to the CAN bus and the computer. These signals are communicated with the industrial control machine through CAN bus, and the soft PLC (CoDeSys) in the industrial control machine outputs the switch signal according to the program. This switch signal through the I/O interface to control the electrical actuating parts, and then transformed into mechanical action, so as to realize a series of process control from the feed to the sewing mouth, such as clearing, coarse filling, fine filling, bag clamping, material release, etc. 3 Control section
The control part of the metering and filling machine program is mainly composed of the industrial control machine, intelligent weighing display part, I/O interface and other parts. The following focuses on the industrial control machine and intelligent weighing display part.
This weighing and filling machine adopts industrial control machine as the upper computer, can use windows or Linux operating system, using touch screen technology.
At present, the soft PLC products on the market are mainly 3S CoDeSys, SIEMENS SIMATICWinAC, SOFTPLC SoftPLC and CJIntemationl ISaGRAF. Among them, CoDeSys of 3S company is gradually recognized by domestic and foreign users for its powerful functions, high reliability, easy secondary development, integrated visualization, etc. CoDeSys consists of three parts: controller application code development editor, integrated compiler for generating controller application code, and digital diagnosis and test run functions. 3 standard, which supports the standard's five programming languages, namely Sequential Function Chart (SFC), Function Block Diagram (FBD), Ladder Diagram (LD), Instruction List (IL) and Structured Text (ST). In addition, it provides a sixth editor language called Sequential Function Chart, which is a variation of Function Block Diagram. Users can program in one of these languages or in a mixture of several languages, which greatly improves the efficiency of programming and development.CoDeSys provides a large number of important feature tables to help developers debug and test their applications quickly and efficiently. The current value of each variable can be displayed directly in the program code. These values can be written to at any time and type-compulsory conversions can be performed. Errors can be easily detected by setting breakpoints and then running the code in a single step. in June 2004, the company set up the CoDeSys Product Promotion and Training Center at the Beijing Institute of Technology, which is able to provide strong technical support. Therefore, the system control software adopts CoDeSys software from 3S, which supports SERCOS bus and CAN bus.
CAN (ControllerAreaNetwork) that is, Controller Area Network, mainly used for various equipment monitoring and control of a field bus. It has a simple structure, flexible communication mode, long communication distance, non-destructive bus arbitration technology, etc. CAN bus provides a new solution for highly reliable data transmission in industrial quantitative filling machines, which has been widely used in foreign industrial measurement and control fields, therefore, this program adopts the CAN bus interface, and selects ADLINK's dual-port isolation and non-intelligent CAN adapters PCI-7841. PCI-7841, the card supports CANopen, DeviceNet and other CAN bus application layer protocols; and provides programming functions under VB and VC. Through the human-computer interface, the operator's control instructions are transmitted to the intelligent weighing and display control part, and at the same time, the signals and data from the intelligent weighing and display control part are accepted, analyzed and processed, and displayed.
At present, there is no special controller with CAN communication interface for automatic filling machine in the market, so the intelligent weighing display control part needs to be developed independently. In order to shorten the development cycle, the CAN communication part is added by technical improvement of the existing controller. The part of Intel's microprocessor 89C51 as the core, through the weighing module, A/D conversion to collect weighing signals, after processing, according to the need to send these information through the SJA1000 and CAN interface circuit (mainly composed of PCA82C250) to the CAN bus, and the upper level of the industrial control machine for communication. SJA1000 is an independent CAN controller produced by PHILIP company, which conforms to CAN2.0B protocol, and has all the necessary functions required to complete the high-performance communication protocol, and can complete all the functions of physical layer and data link layer of the CAN bus protocol. PCA82C250 is the interface between the CAN controller and the physical bus, which can improve the differential sending ability to the bus and differential receiving ability to the CAN controller, and can improve the resistance of the bus. and can improve the anti-jamming ability of the bus.
Conclusion
This automatic filling machine adopts CoDeSys and CAN bus technology, simplifies the hardware structure, fully meets the requirements of open architecture, can meet the requirements of industrial automation field on the openness and flexibility of the quantitative filling machine, for the future of industrial automation to a higher level of integration provides a reliable technical guarantee. After simulation test, this control program has achieved the expected results, has a very broad application prospects, and can produce good social and economic benefits.