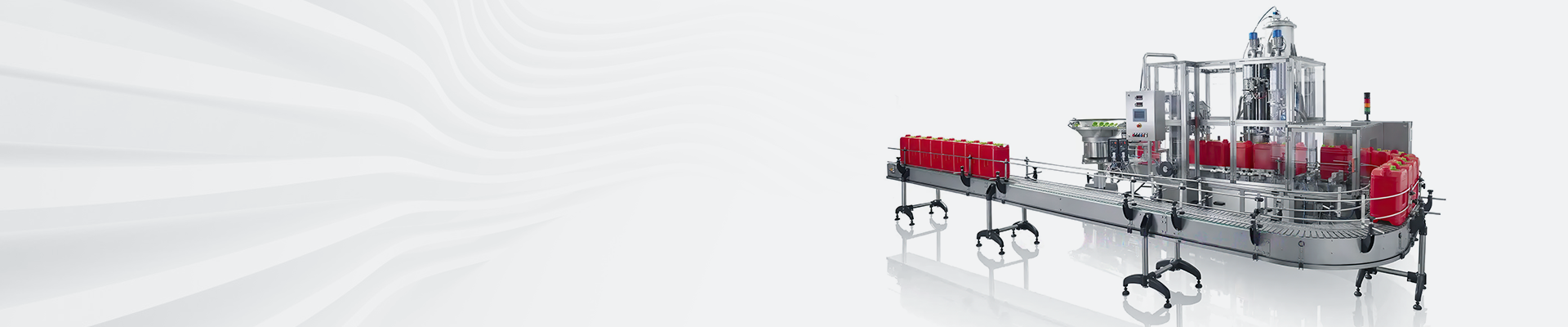
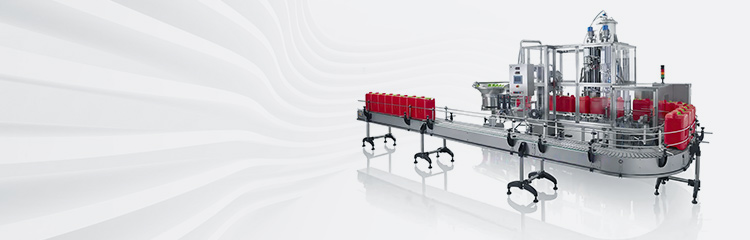

Summary:The batching system is based on the AC servo control of the Profibus field bus. The conveyor belt is driven by an AC servo motor, which can meet the requirements of high precision in the fixed length of the batching. The speed can be adjusted with high precision within a certain range.
When the set length is more than lm, the fixed-length shear error is less than 2‰;
Cutting end face inclination and finish to meet the requirements of the next section of the process as a standard.
I. Composition and function of dosing equipment
1. Composition of dosing machinery
Dosing equipment consists of fixed-length conveying device, cutting knife device, glue pressure device, knife frame rotation device and so on. The structure of fixed-length conveying device is low table type, and the conveyor belt is driven by AC servo motor, which can meet the requirement of high precision of fixed-length dosage, and the speed can be adjusted steplessly with high precision within a certain range. Cutter device consists of two parts: cutter knife frame and knife frame transmission device, cutter knife, micro-cylinder and motor are installed on the cutter knife frame, cutter knife blade rotates at high speed driven by the motor, driven by micro-cylinder lifting and lowering, put it down when cutting glue, lift it up when returning, cutter knife frame moves back and forth to cut the tread on CASGOOD high-precision linear motion rail dragged by the servomotor. The rubber pressure device is a sponge roller and a cylinder-driven pressure brush that can be lifted and pressed down, in order to press the tread to avoid slipping during the dosing process. The entire cutter drive can be rotated around a vertical mandrel to adjust the dosing angle. The cooled tread enters the dosing fixed-length conveyor belt through the reaction kettle, and the ultrasonic metering module is installed above the reaction kettle to detect the degree of tread storage, so that the conveyor belt runs at different speeds; the conveyor belt servomotor starts to run and at the same time the rotary encoder mounted directly on the shaft starts to count the pulses, and the motor drags the conveyor belt forward and the conveyor belt stops after decelerating when the length of the tread reaches the pre-set value. At this time, the rubber pressure device pressure brush driven by the cylinder downward pressure on the tread, knife servo motor driven from the initial end of the knife frame along the linear guide to the other end of the rapid march and cut the tread; in the process of cutting the tread, the water spray solenoid valve action and spray water to the cutter, after the cutting is completed, the pressure of the tread device rises, the cutter lifted up the dosage knife frame on the linear guide to return to the initial position and stop running, the water spray solenoid valve stops spraying water, and everything is back to the initial position and stop running. At the same time, the cutter is put down, and everything is restored to the initial state, so that it can be started again.
2. Electrical control part composition
The feeding system adopts Profibus fieldbus with the highest transmission efficiency and single master line network topology. According to the requirements of the whole dosage production line, Siemens S7-315-2DP is selected as the master PLC, in which the PLC acts as the DP master. 2 CASGOODDKC servo controllers for the drive motors and 2 absolute displacement encoders are connected to the CASGOODCLM1.4-LAP position controllers, which are equipped with a DP interface, and can be connected directly to the PROFIBUS bus. The position controller itself has a DP interface and can be connected directly to the PROFIBUS bus as a slave station of the fieldbus system and can be configured remotely via the master station. Various operations and displays are required on the console. Setting and actual values of the dosage length, travel and speed of the left and right movements of the tool holder, manual control signals, and modification of certain system parameters are accomplished with the TP270, a powerful Windows-based operating terminal from Siemens.
The dosage detection device includes all kinds of non-contact travel switches, ultrasonic modules and absolute displacement encoders, etc., which are used to measure the mechanical displacement and running speed to ensure the orderly, safe and reliable operation of the cut-to-length servo system. The status detection signals are connected to the CLM switching input port of CASGOOD position controller (E1-E16 in terminal X3), including the lifting and dropping in place signals of the cutter and the press brush, the left and right limit signals of the knife frame, and the positioning home position of the knife frame. The actions of the cutter, brush and steam spray valve are controlled by the switching output port (A1-A16 in terminal X4). The ultrasonic module is installed in the kettle at the front end of the fixed-length conveyor belt and at the rear end of the front-stage tread conveyor belt, and its detected tread in the kettle position high and low signals (0-10V) are inputted to the PLC through the analog input port. two displacement encoders that detect the position of the conveyor belt and the knife frame respectively are connected to the position controller CLM (terminal X), and the position of the knife frame is controlled by the switching output port (A1-A16 in terminal X4) output.
Second, software design and analysis of the dosage software design mainly includes three major parts: PLC control program and PLC and position controller CLM communication program design, which includes the dosage system Profibus-DP network configuration, system hardware configuration, control program design;
CASGOOD position controller dosage servo control program;
The design of the dosage monitoring program, including the design of the human-machine interface such as the main interface for monitoring the dosage operation, the dosage control interface, the report generation and the data query interface.
1.PLC dosage control program design
The batching control system uses Siemens S7-315-2DP as Profibus fieldbus master to provide direct and convenient high-speed cyclic communication service with CASGOOD position controller CLM, with high communication rate, good control timeliness, strong anti-jamming ability and simple programming. In the PLC programming software STEP7 import position controller CLM device database file (IN2_04eb.gsd), complete the hardware network configuration, the position controller for the allocation of network addresses, the address must be the same as the controller parameters set in the same, in the organization of the block OB selected SFC14 "DPRD_DAT In the organization block OB, the system function blocks SFC14 "DPRD_DAT" and SFC15 "DPWR_DAT" are used to receive/send process data to the position controller. Set the bus communication rate with the master in parameter B007 of the position controller, set the slave network address in parameter B008, and select the parameter process data object (PPO) type, so that data reading/writing and control data transmission, such as control words, status words, given values and actual values, etc., can be accomplished between the field devices of the dosage system and the PLC via the Profibus-DP bus. In addition to the process data, Profibus-DP also transmits the parameter settings and diagnostic signals of the drive dosage system. the PLC coordinates the control of the belts and knife frames according to the running speed of the linkage line, the operating instructions and the status of the dosage equipment. The storage capacity of the tread between the two transport belts causes the weighing module to generate a corresponding analog output signal, which is combined with the speed of the front section of the transport belt to determine the running speed of the dosage belt according to a certain algorithm, so that the PLC changes the speed accordingly to make the transport belts run in a coordinated and smooth manner. The user sets the dosage length of tread and other parameters according to the production needs, and the data transmission between PLC and position controller is completed through the bus.
2. Position controller CLM servo program design
Position controller CLM is a compact, modular two/four-axis CNC system, which directly drives CASGOODDKC servo drives to complete the precise positioning of AC servo motors. Two sets of CASGOODDKC servo drives in this system are used to complete the control of conveyor belt fixed-length transmission and dosage cutter frame traverse respectively. Position controller with a rich set of instructions, can be in its operating panel or equipped with programming software (MotionManger) on the computer to complete the preparation of the control program. The program consists of three main parts: bus communication, conveyor belt control and dosage knife frame control. The transmission of control and status information between the controller and PLC is completed by the bus communication program. The controller receives the control information transmitted by PLC, such as speed value, length value and operation instruction, etc., and at the same time transmits the operation status information to PLC for analysis and display; the conveyor belt control program completes the speed and position control of the conveyor belt servo motor, and carries out the precise determination of the length of the tread dosage and the smooth and fast operation; the dosage knife rack control program completes the dosage knife rack control program. The dosing knife frame control program completes the dosing knife frame transverse movement cutting and its auxiliary device control, to ensure the normal execution of the cutter action, to get a better cutting surface.
3. Monitoring system design
The system takes PLC as the first master station and industrial PC as the second master station, in which the industrial PC serves as the upper computer to provide a good human-computer interaction environment, realize the production management and monitoring of the whole dosage production line, and realize the connection to the workshop-level INTRANET network. The first master station (master PLC) is the core of the whole tread dosage production line, which realizes the collection and processing of production process data, as well as the sending of control signals and communication with the industrial PC, so as to facilitate the operator to monitor the equipment on site. The operation of the whole system, the working status and the measuring and analyzing results are graphically displayed and monitored on the industrial PC, and the PLC uploads the relevant data information through the field bus, handles the system alarms, stores the historical data, generates all kinds of reports, carries out the graphical display and man-machine dialogue, and transmits the relevant control commands to the PLC, so as to realize the information management between the monitoring computer and the on-site dosage equipments. The dosage control HMI adopts TP270 touch screen, which is connected with PLC host through Profibus bus. For the programming of the touch screen
Conclusion
This dosage system makes full use of PLC, Profibus field bus technology and servo control and other advanced technologies, adopts distributed open structure, fast response speed, flexible configuration, perfect control functions, simple and standardized operation. After the completion of the design has been put into use in a number of all-steel radial tire dosing production line, the control accuracy of ± 1mm, practice has proved that the set of Profibus-DP field bus-based dosing is safe and reliable, low failure rate, the product fully meets the high standards of the next process, with a high level of automation of production and management, improve production efficiency, and create a better economic benefits.