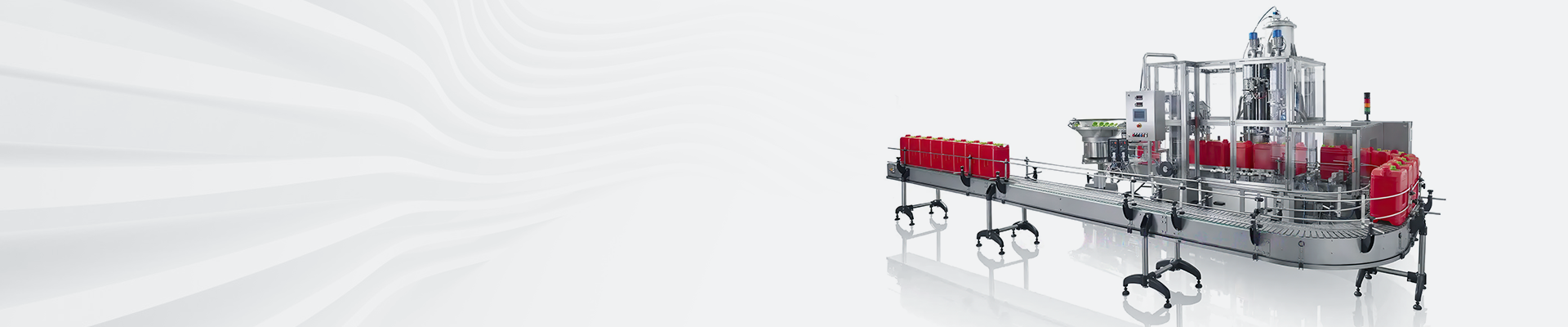
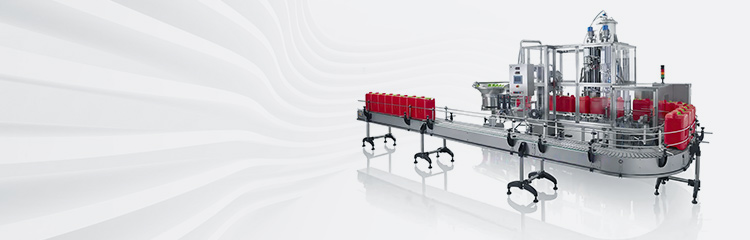

Summary:The batching system mainly completes initial data input, material tracking, process parameter setting calculation, human-computer dialogue processing, etc. The main network will be directly connected to the process control level server to complete tasks such as reactor batching parameter control, sequence control, speed control, etc.
The automation of the dosing production line consists of a two-level network, with the first level being the basic automation level (referred to as Level 1) and the second level being the process control level (referred to as Level 2).
The automatic dosage system (LEVEL 1) uses GE Fanuc's PACSystems™ RX7i series as the main controller, while the hydraulic control therein uses a dedicated hydraulic controller based on a POWER PC CPU board from MEN, Germany, and the necessary I/O modules. Metering line data acquisition, control of heated reactor parameters, sequence control, position control, speed control, strip control, temperature and profile control are among the tasks.
Process control automation level control range: starting from heating the reactor front roller conveyor to the end of resin on-line weighing in the resin transportation system. It mainly accomplishes the tasks of initial data input, material tracking, process parameter setting calculation, data recording and reporting, man-machine dialogue processing, data communication, simulation of resin modeling, historical data processing, application system startup, event monitoring and so on. The process control automation computer system reserves the communication interface with continuous casting and cold rolling computer system.
2 network structure
As the ratio requires its computer system has a "high-speed control" and "high-speed communication" of the "two high" performance, so the basic automation system design should meet the reactor control on the system. Therefore, the design of basic automation system should meet the "two high" requirements of kettle control system. Specifically, in order to meet the requirements of hydraulic system control and inter-functional communication, there should be two "1ms", i.e., the control cycle can be up to 1ms and high-speed communication with a data update cycle of less than 1ms. Therefore, the whole hybrid configuration consists of three layers of communication network.
Layer 1: 2Gb/s ultra-high-speed fiber-optic memory image network. The main memory image network will be directly connected to the process control level server, which is the main network of the system, connecting the main function controllers, data storage stations, real-time simulation stations and secondary systems on the rolling line; the data (recording) storage and analysis stations are directly connected to the main memory image network in order to be able to directly access the setup, sampling and operation data.
Layer 2: 100Mb/s Ethernet based on TCP/IP protocol. It is mainly used for communication between controllers, operator stations, special function stations, rolling line instruments and secondary systems, as well as for remote programming of the controllers.
Layer 3: Fieldbus Profibus DP network. It mainly provides the communication between the controllers of each area and the main/auxiliary electric drives, remote I/O and OPU, with the maximum communication speed of 12Mb/s. All the main and auxiliary electric drives on the rolling line are connected to the controllers of the corresponding areas through Profibus DP network, with the controllers as the masters of the DP network, and the electric drive controllers as the slaves; the remote I/O of each area and the corresponding operator station are connected to the I/O of the operation box and the I/O of the OPU of the operation unit. The remote I/O of each area and the corresponding operator station and operation box I/O and the I/O unit of the operation unit OPU are connected to the main controller through Profibus DP network, and the remote I/O of the public and auxiliary systems are connected to the controller of the corresponding area through Profibus DP network. The universal adoption of fieldbus and remote I/O realizes the purpose of replacing a large number of control cables with a small number of communication cables.
According to the mixing and batching process characteristics and equipment distribution, each functional controller and OPS are basically divided into four zones, namely, heating reactor metering and batching system zone, mixing zone, batching zone and coiling zone. Each area controller mainly accomplishes the functions of logic control, man-machine dialogue, data transmission, data processing and material tracking in this area. Each controller is distributed as follows:
(1) The heating reactor area is equipped with a total of 6 PLCs. 3 sets of GE's PACSystems™ RX7i system, 3 sets of GE's PACSystems
RX7i system of GE and 3 sets of GE 90-30 PLC system. The system data of the reactor weighing and batching system area is communicated in various ways, such as Ethernet and Profibus-DP network, and the main controller transmits data with the upper computer and other areas of the rolling line by means of Ethernet. Reaction kettle dosing system area mainly transmits billet data to the upper computer, A roller conveyor with or without material signals, signals into the kettle and out of steel signals, etc., and at the same time, it obtains signals for materials from the mixing area, and sends running signals to the transmission equipment.
The basic automation in the heating reactor area has the following functions to be accomplished: logical sequence control of the roller conveyor in front of the reactor, resin centering control of the roller conveyor into the reactor, loading control of the charging machine, pumping control of the discharging machine, control of the stepping beams in the reactor, and control of the roller conveyor out of the reactor dosage system.
(2) The mixing area is equipped with a total of three PLCs, including two sets of GE's PACSystems™ RX7i system, two sets of GE's PACSystems™ RX7i system and one set of GE's PACSystems™ RX7i system.
RX7i system of GE and 1 set of GE 90-30 PLC. The task of the mixing area is to descale the resin out of the reactor dosing system with high pressure water, and then roll it back and forth 3-5 times by E/R, and finally transport it to the dosing area through the D and E roller conveyor. Specifically include: D roller conveyor, mixing machine speed control, mixing and descaling water control, mixing area inlet/outlet side guide plate APC control, vertical roll VE1 opening degree APC control, flat roll R1 mill under APC control, mixing machine speed sequence control, mixing machine vertical/flat rolls between the micro-tension control, heat preservation cover control, automatic width control (AWC).
(3) The batching area is equipped with a total of 14 PLCs, of which 12 are GE's PACSystems™ RX7i systems.
RX7i system 12 sets, GE 90-30 PLC 2 sets. The quality of the finished strip is closely related to the control accuracy of the batching area, so this area is a control function intensive area. Controls in this area include: intermediate rollerway (E-rollerway) control, flying shear front guide scale control, flying shear control, dosage descaling control, doser sequence control, main speed control, live sleeve height and live sleeve tension control, dosage doser bend roll, string roll control, dosage hydraulic depress APC and depress zero adjustment, dosage hydraulic AGC control, dosage final roll temperature control, and dosage doser work roll and support roll change roll control. Considering that the hydraulic transmission of the batching unit is relatively centralized, "rack controller" is adopted in the batching area, i.e., each batching machine is equipped with a rack controller, which contains a PIII CPU and two Power PC hydraulic control modules to control the hydraulic press-down, bending rollers, tampering rollers, and hydraulic live sleeve of the rack.
(4) The weighing and sorting area is equipped with a total of five PLCs, including four sets of GE's PACSystems™ RX7i system, four sets of GE's PACSystems™ RX7i system, and two sets of GE's PACSystems™ RX7i system.
RX7i system 4 sets, GE 90-30 PLC 1 set. The winding area accomplishes the following tasks: laminar cooling of polyurethane, simulation test, quality classification, output roller conveyor speed control, control of the opening degree of the guide ruler before winding, speed control of the pinch rollers, tension control and adjustment of the roll gap of the rollers assisting the winding, speed control and automatic jump control (AJC), main speed control of the reel and winding tension control, winding sequence control, and unloading control.
3 Hardware Features
The main features of GE Fanuc's PACSystems™ RX7i and related products:
(1) The PACSystems™ RX7i series adopts Intel Pentium III chips with two main frequencies of 300MHz/700MHz and 10MB of memory, which greatly improves the operation speed and applies ladder diagrams to realize sequential logic control, while at the same time completing closed-loop control. High-capacity power supply (100W and 350W) without external power supply.
(2) The CPU board integrates an Ethernet port to support 10/100M communication, which greatly improves communication capability.
(3) Open structure based on VME bus, supports 90-70 series I/O, GENIUS bus controller architecture and a wide range of third-party VME-based CPU boards and I/O modules. Supports existing 90-70 I/O and new I/O in the same rack.
(4) Integrated Development Engineering Environment for Windows Cimplicity ME provides a broad engineering development environment for all programming, configuration and diagnostics for the PACSystems™ RX7i family. With the exception of I/O points, variable names can be programmed directly without concern for their address assignments, allowing for greater design flexibility and improved engineering efficiency.
(5) The feeder adopts an open VME bus structure and can be installed with VME standard metering modules from over 300 different manufacturers. In the system configuration, in addition to its own rack I/O modules can also be connected to remote I/O modules through the field bus (such as Profibus DP), constituting a powerful and reasonably priced control platform to meet a variety of large-scale, complex high-speed control requirements.
(6) GE 90-30 PLC series with low cost and high performance can easily replace from simple relay to complex medium-sized automation system applications. Its CPU has powerful functions such as built-in PID regulation, structured programming, interrupt control, indirect addressing and a variety of function modules that can successfully complete complex operations. In addition, the 90-30 series has highly functional special modules available, such as high-speed counting modules and Profibus DP communication modules.
(7) VersaMax series PLCs provide a wide range of I/O modules for more flexible configuration. The communication module can connect VersaMax with Profibus DP network (or other industrial field bus) to realize remote control.
4 Conclusion
Polyurethane production is characterized by continuity, rapidity, real-time, and high control accuracy. This requires a computer system with high-speed control and high-speed communication capabilities to achieve high-precision control, and this design is able to meet this requirement. The system adopts the products of General Electric Company (GE) of the United States, which has a reliable guarantee in stability and maturity. This system will provide a solid guarantee for the smooth operation of the polyurethane plant, and the commissioning of the batching production line will bring great economic benefits to the donor you.