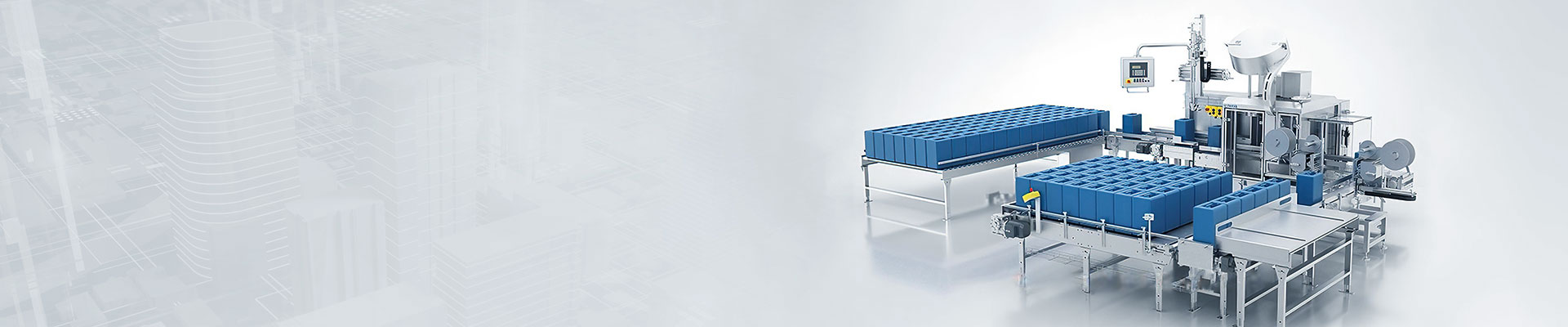
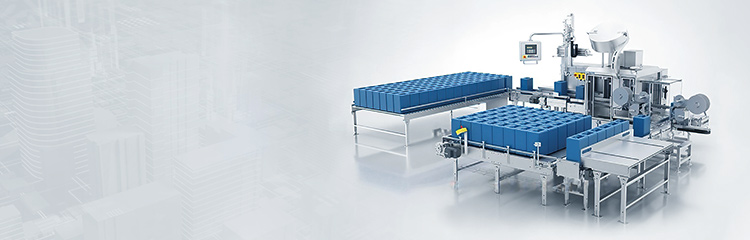
The weighing and unloading system adds the required materials into the mixing bin in turn according to a certain ratio. At the same time, PLC monitors the pulse signal sent by the material level meter to determine the position of the material in the bin, so as to control the on-off of the charging valve; After the feeding is completed, according to the preset mixing delay time, the PLC starts the mixing motor to ensure that the material is fully stirred in the mixing bin to complete the mixing operation; Then enter the discharge and pressing stage, the PLC controls the discharge valve action, the material is output from the mixing bin, pressed into the storage tank, complete a cycle of automatic batching control process.

The automatic Batching system adopts small and medium-sized distributed control, realizing "decentralized control, centralized management" and overcoming the problem of "dangerous centralization"; the upper computer and the lower computer are relatively independent. It has manual, automatic and semi-automatic switching functions. When online, it transmits information to each other according to a specific protocol. Offline, a single scale can independently realize process closed-loop process control.
The upper unit is far away from the operation site, which improves the stability of the weighing control system and the working environment of the operators; the lower unit adopts programmable controller, which is strong in anti-interference ability, simple and easy to program, and can be reliably operated for a long period of time under the bad environment; it adopts PID regulation to improve the dosage accuracy of the Dosage system, and it can be used to set up the optimal working switching sequence according to the production needs, and solve the problems of the material head and the material tail in a better way. Automatic modification of material ratio dosage.
The batching scale has three control modes: manual, semi-automatic and automatic. For manual operation, the switches of the field control box and the instrument box are set to the manual position, and the control is realized through the start-stop button, potentiometer, frequency meter, etc. on the field control box, and the weighing instrument displays the instantaneous and cumulative quantities of the materials. Emergency operation is required in case of manual maintenance and commissioning work.
For semi-automatic operation, the switches of the on-site control box and the instrument box are set to the automatic position, and the control is realized by the start-stop buttons, frequency meter, weighing and displaying instruments. Adjust the dosage quantity, display the instantaneous and accumulated quantity of materials; you can also adjust the dosage quantity by setting the recipe through the on-site operation screen. It is mainly used to realize on-site operation when no upper position control is needed.
When it is fully automatic, switch the meter box to the linkage position, the upper computer controls the start and stop of the belt, and dynamically displays the quantity of each material, the running status of the belt and all kinds of alarm indications. It can collect and process the weighing signals and switching status from each dosage control circuit, and realize the automatic control of the whole dosage system, such as the feeding of the belt scale, weighing detection, material quantity adjustment, bin selection and switching, and other dosage processes. At this time, the on-site manual control of the batching system does not work, and it is operated completely through the central control room.
Main functions of the batching system
Monitoring function: detecting and monitoring the instantaneous flow, daily accumulation, monthly accumulation, yearly accumulation and other parameters of the weighing and batching process;
Screen display: the computer monitor can display the operation status of relevant control parameters in the dosage process, as well as real-time display of dosage curves and tables;
Printing management: the composition report can be printed at any time and saved for inquiry;
Communication function: two-way data and information exchange between industrial control computer, PLC and meter;
Data processing: the collected signals can be automatically processed and output to the corresponding control quantity;
Control function: automatically control the normal operation of the equipment according to the corresponding set value before operation, including PID adjustment;
Alarm function: the upper computer alarms various parameters exceeding the limit or abnormal equipment status in the form of pictures and sound and light signals.