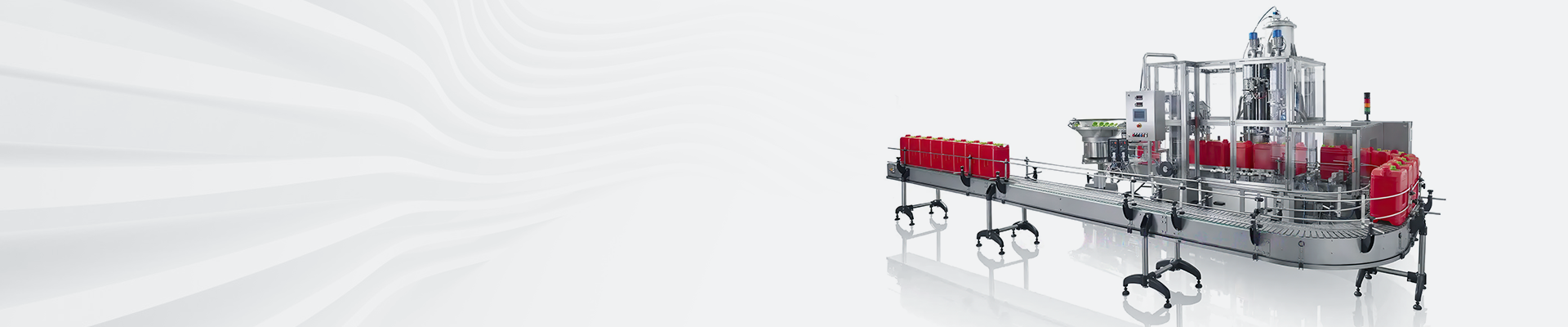
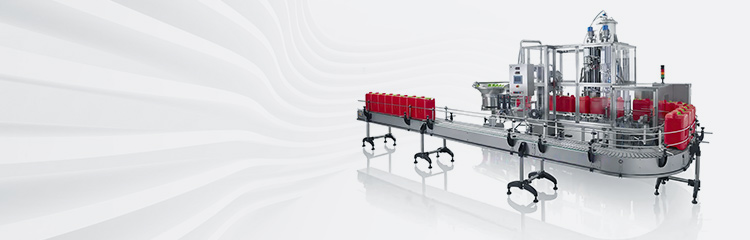
摘要:配料系统基于Profibus现场总线的交流伺服控制,传送带由交流伺服电动机驱动,可满足配料定长精度高的要求,速度在一定的范围内可进行高精度无级调速。
子午线轮胎生产过程中胎面定长配料是其关键工序之一,胶料投入挤出机后压出并经牵引拉伸、冷却及定长配料后得到轮胎胎坯。胎面配料定长检测的控制过程是一个先配料定长、后单条称重的控制过程。开发一套具有高切割精度(包括加工端面倾斜度和光洁度及定长剪切长度的精确度)、能够适应高配料速度的胎面配料设备,不管从提高产量、减少废品率还是从提高原料的利用率来说都显得极为重要。本文主要阐述一种应用现场总线和伺服控制技术来实现较高定长配料精度的配料系统。配料系统的运行指标如下:高运行速度不低于30m/min;
设定长度大于lm时,定长剪切误差小于2‰;
切割端面倾斜度和光洁度以满足下段工序的要求为标准。
一、配料设备组成及功能简介
1.配料机械部分组成
配料设备由定长输送装置、裁刀装置、压胶装置、刀架转动装置等组成。定长输送装置的结构为低台式,传送带由交流伺服电动机驱动,可满足配料定长精度高的要求,速度在一定的范围内可进行高精度无级调速。裁刀装置由裁刀刀架和刀架传动装置两部分组成,裁刀、微型气缸和电机安装在裁刀刀架上,裁刀刀片在电机带动下高速旋转,由微型气缸带动升降,裁胶时放下,回程时抬起,裁刀刀架在由伺服电机拖动的CASGOOD高精度直线运动导轨上来回移动以切割胎面。压胶装置为海绵滚筒和由气缸带动的能够抬起和压下的压刷,是为了在配料过程中压住胎面以免打滑。整个裁刀传动装置可绕一垂直心轴转动,从而调整配料角度。冷却后的胎面经反应釜进入配料定长输送皮带上,在反应釜上方装有超声波计量模块,检测胎面贮存的程度,使运输带以不同的速度运行;传送带伺服电机启动运行,同时直接装在轴上的旋转编码器开始脉冲计数,电机拖动输送皮带向前行进,当胎面长度达到预设值时,运输带经减速后停止运行;此时压胶装置压刷在气缸带动向下压紧胎面,刀架伺服电机带动刀架从初始端快速沿直线导轨向另一端行进并裁切胎面;在裁切胎面的过程中,喷水电磁阀动作并向切刀喷水,切割完毕后,压胎面装置升起、切刀抬起,直线导轨上的配料刀架退回到初始位置并停止运行、喷水电磁阀停止喷水,同时切刀放下,一切恢复到初始状态,以便再次启动。
2.电气控制部分组成
该上料系统采用Profibus现场总线传输效率最高的单主站线型网络拓朴结构。根据整条配料生产线的要求,选用了西门子S7-315-2DP为主控PLC,其中PLC作为DP主站。2台驱动电机的CASGOODDKC伺服控制器和2个绝对位移编码器接入CASGOODCLM1.4-LAP位置控制器,位置控制器本身带有DP接口,可以直接连接在PROFIBUS总线上,作为现场总线系统的从站,并且可通过主站完成远程参数配置。控制台上各种操作和显示要求较多,配料长度的设定与实际值,刀架左右移动的行程及速度,手动控制信号,以及某些系统参数的修改通过TP270来完成,TP270是西门子公司的基于Windows平台的功能强大的操作终端。
配料检测装置包括各类非接触式行程开关、超声波模块和绝对位移编码器等,用于测量机械位移、运行速度,保证了裁度伺服系统有序、安全、可靠的运行。状态检测信号接入CASGOOD位置控制器CLM开关量输入口(端子X3中的E1-E16),包括切刀、压刷的抬起与落下到位信号,刀架左右限位信号,刀架定位原点等。切刀、压刷、喷蒸汽阀的动作由开关量输出口(端子X4中的A1-A16)输出控制。超声波模块安装于定长传送带前端与前级胎面运输带后端的反应釜内,其检测到的胎面在反应釜位置高低信号(0-10V)通过模拟量输入口输入到PLC。分别检测传送皮带和刀架位置的两个位移编码器接入位置控制器CLM(端子X1、X2)。
二、软件设计及分析本配料软件设计主要包括三大部分:PLC控制程序和PLC和位置控制器CLM的通信程序的设计,其中包括配料系统Profibus-DP网络组态、系统硬件组态、控制程序设计等;
CASGOOD位置控制器配料伺服控制程序;
配料监控程序的设计,主要包括配料运行需要的监控主界面、配料控制界面、报表生成和数据查询界面等人机界面的设计。
1.PLC配料控制程序设计
配料控制系统中以西门子S7-315-2DP作为Profibus现场总线主站提供与CASGOOD位置控制器CLM直接而便利的高速循环通信服务,通讯速率高、控制适时性好、抗干扰能力强且编程简单。在PLC编程软件STEP7中导入位置控制器CLM设备数据库文件(IN2_04eb.gsd),完成硬件网络组态,为位置控制器分配网络地址,该地址必须与控制器参数中设置的相同,在组织块OB中选用SFC14“DPRD_DAT”,SFC15“DPWR_DAT”系统功能块向位置控制器接收/发送过程数据。在位置控制器参数B007中设置与主站的总线通讯率,参数B008中设置从站网络地址,并选择参数过程数据对象(PPO)类型,这样配料系统的现场设备与PLC之间通过Profibus-DP总线可以完成数据的读写和控制数据的传输,如控制字、状态字、给定值和实际值等。除过程数据外,Profibus-DP也传输传动配料系统的参数设置和诊断信号。PLC根据联动线的运行速度、操作指令及配料设备的状态对皮带、刀架进行协调控制。胎面在两条运输带之间的贮存量使称重模块产生相应模拟量输出信号,并与前段运输带的速度综合起来按照一定的算法决定配料皮带的运行速度,从而通过PLC相应地改变速度使运输带协调平稳运行。用户根据产品生产需要相应设置胎面配料长度等参数,通过总线完成PLC与位置控制器之间的数据传输。
2.位置控制器CLM的伺服程序设计
位置控制器CLM是一种紧凑型、模块化二/四轴数控系统,直接驱动CASGOODDKC伺服驱动器完成交流伺服电机的精确定位运行,本系统中二套CASGOODDKC伺服驱动器分别完成传送带定长传送和配料刀架横移的控制。位置控制器带有丰富的指令集,可在其操作面板或装有编程软件(MotionManger)的计算机上完成控制程序的编写。程序主要由总线通讯、传送皮带控制和配料刀架控制三部分组成。控制器与PLC之间控制和状态信息的传送由总线通讯程序完成,控制器接收PLC传送的控制信息如速度值、长度值和操作指令等,同时将运行状态信息传送给PLC进行分析、显示;传送带控制程序完成传送带伺服电机运行的速度和位置控制,进行胎面配料的精确定长和平稳快速运行;配料刀架控制程序完成配料刀架横向移动切割和其辅助装置的控制,保证裁刀动作的正常执行,得到较好的切割端面。
3.监控系统设计
系统以PLC为第一主站和以工业PC为第二主站,其中工业PC作为上位机,提供良好的人机交互环境,实现对整条配料生产线的生产管理和监控,并实现连接到车间级INTRANET网络。第一主站(主控PLC)是整个胎面配料生产线的核心,实现生产过程数据的采集和处理,以及控制信号的发送与工业PC的通讯,以便于操作人员监控现场的设备。整个系统的操作、工作状态及测量分析结果在工业PC上进行图形显示监控,通过现场总线由PLC上传相关数据信息,处理系统报警,存储历史数据,生成各类报表,并进行图形显示及人机对话,向PLC下传相关控制命令,从而实现监控计算机与现场配料设备之间的信息管理。配料控制人机界面采用TP270触摸屏,通过Profibus总线与PLC主机连接。对于触摸屏的编程,采用西门子公司提供的ProTool/ProCS组态软件进行编程组态。ProTool/ProCS完整的图形用户界面加上软件本身自带的项目组态向导允许用户方便地创建面向对象、基于符号的各种项目。在ProTool/ProCS中界面上的操作单元与执行器之间通过PLC利用变量进行通讯,即在HMI可以直接读或写的PLC上的存储地址。软件设计思想是在完成基本人机交互功能的基础上,设计了一套让操作者能够自学习操作规程的软件系统。通过人机界面,操作者即能设置一些基本的参数,如定长值、误差调整、配料次数等,也可以监测系统的报警状态,操作规范以及密码设置等。自动运行按照设备设计的动作流程进行自动运行控制时,一些需要调整的参数,如速度、位置等可以方便的在触摸屏上进行调整、修定。异常停止当定位模块、伺服驱动器、行程开关以及机器异常时伺服马达都应该立即停止运转,并产生异常码显示在触摸屏上,以便维修人员及时了解发生的问题。
三、结语
本配料系统充分利用了PLC、Profibus现场总线技术和伺服控制等先进技术,采用分布式开放结构,响应速度快,组态灵活,控制功能完善,操作简单规范。设计完成后已在多家全钢子午轮胎配料生产线中投入使用,控制精度达到±1mm,实践证明该套基于Profibus-DP现场总线的配料安全可靠,故障率低,产品完全满足下道工序的高标准要求,具有较高的生产和管理自动化水平,提高了生产效率,创造了较好的经济效益。