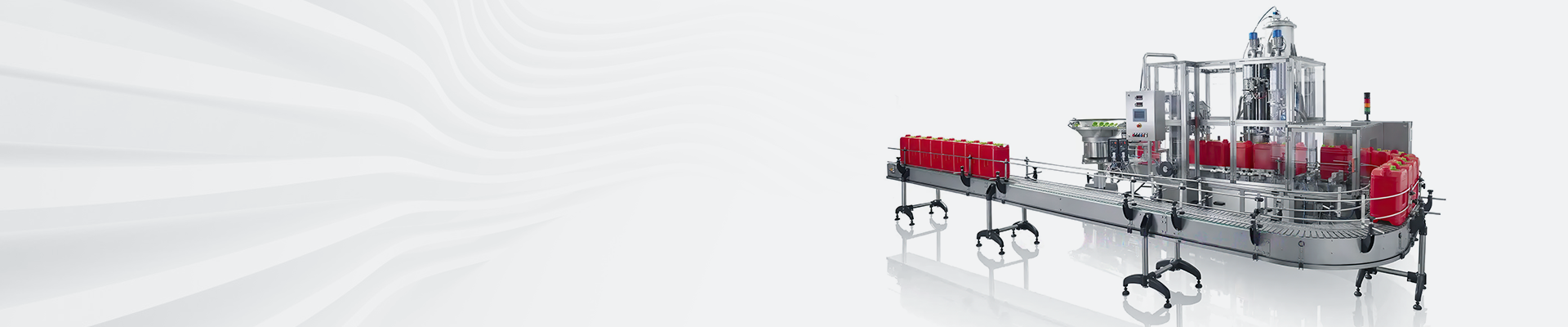
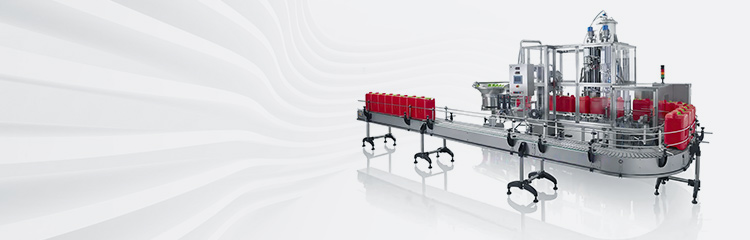

Summary:The storage tank automatic batching system is a two-level microcomputer control composed of Siemens PLC and upper computer. At the same time, AC frequency converters are used in the storage tank tilting and oxygen lance batching drive parts that require speed regulation to replace DC speed regulation and batching.
The tank weighing control system is a two-stage microcomputer control system consisting of a Siemens programmable logic controller (PLC) and an industrial computer. At the same time, AC frequency converter is used to replace DC speed regulation in the drive part of tank tilting and oxygen gun dosage which requires speed regulation. The automatic dosage system adopts safe and reliable three-place control, i.e., the operation desk, the upper machine, and the operation box beside the machine, so that the normal work of the dosage will not be affected in the event of failure of any one of the parties, and the PLC and the computer adopt the communication mode, and the upper industrial computer is equipped with the WINCC human-computer interface software. Through the description of various parameter curves and the display of equipment operation status and operability, it has advanced automation level. At the same time, under the premise of shielding isolation, filtering and error correction technology, the highest reliability of dosage operation is guaranteed.
In the storage tank tilting, oxygen gun accurate positioning and automatic dosage system adopts our company for the production of storage tanks specially developed patented products DIS-V type storage tank tilting angle display instrument and ZNLK intelligent main order controller and YSX-Ⅲ type intelligent voice alarm. It greatly improves the automation level and reliability of the storage tank.
This self-feeding system will completely realize the mixing process automation of storage tank tilting, oxygen gun lifting and transverse movement, smoke hood and flare plate control, bulk material, material material assembly material control, batching truck and thin oil station control. At the same time, the workshop adopts five-channel camera to monitor the batching system, realizing uninterrupted monitoring of the important posts in the workshop.
The weighing instrumentation system of the storage tank is all controlled by load cell into PLC automatic control system, so that all the weighing instrumentation parameters of the workshop can be seen on the computer without any doubt.
After careful design and at the same time synthesize the experience of many years engaged in the automatic control of storage tanks believe that this design is a simple, reliable, high performance-price ratio of storage tanks production of automatic dosage control system.
Second, the dosage of software and hardware components
The core part of the automatic feeding system is Siemens PLCS7-300, weighing using integrated metering module, the upper computer with Advantech industrial control machine, tilting and oxygen gun using AC frequency converter, the operator interface using the very popular WINCC man-machine interface software.
1、PLC system
The main control system of this mixing adopts S7-300PLC of Siemens S7 series. the weighing part in the current batching, adopts Siemens module, integrated in S7-300PLC system. The electrical signals are transmitted from 3 load cells on site (each of 3 piezoelectric weighing modules connected in parallel and installed at the three corners of the plane triangle) to the weighing module, and then calculated by the weighing module and changed into weight value, which is directly transmitted to the CPU through the PLC bus, and then displayed on the upper computer. This model is the most advanced system for industrial weighing, with the millivolt signal of the load cell directly entering the PLC, eliminating intermediate links such as transmitters and weighing instruments, thus enhancing the dosage anti-interference capability. Calibration of the scale using the weighing configuration software provided by Siemens, through the computer serial interface for calibration of the scale, the process is simple, fast, if the calibration of the scale is required in the production process, the control system program can be used by the host computer to give instructions, through the S7-300PLC directly.
2、Upper computer system
The upper computer adopts Advantech IP610 industrial control computer, which is a kind of simple and reliable communication method in industry. This industrial control computer is adapted to industrial control occasions, special computers, can work 24 hours a day, anti-interference, dust, heat, running speed and other aspects better than the general computer.
Because of this mixing process requires more images, and therefore the use of two industrial control computer for real-time display, thus speeding up the data transfer speed, a display control tank work process, a display weighing instrument data. Two computers can realize data sharing, and at the same time achieve the purpose of fault dispersion, increasing the reliability of the batching system.
3、Dosing drive part
AC frequency converter is adopted for the tilting drive of storage tank and lifting drive of oxygen gun. Under the premise of meeting the requirements of production process performance, the cost of the dosage system is greatly reduced, and at the same time, it also brings a lot of advantages such as simplicity of the dosage system, convenient maintenance, easy to grasp, and easy to operate. Therefore, the use of AC inverter instead of DC drive is an optimal program.
4、Operating interface
The upper computer operation interface adopts Siemens special human-machine interface software WINCC, which is popular for its powerful function, easy to grasp, easy to use, good reliability and simple operation. All operations can be completed by the mouse, parameter display, modification, setting, and can easily create a dynamic process screen, operation screen, historical curve, real-time curve and other well-functioning screen.
All process parameters such as pressure, flow, temperature, weight, etc. can be displayed on the upper computer in the form of real-time curves, historical curves, histograms, parameter tables, etc., and alarms, statistics, printed reports and other processing. At the same time in the upper computer can be set at any time temperature, flow and other alarm values.
All equipment start and stop can be completed on the host computer, but also according to the actual situation, on the operating table or in the machine side of the operation box to complete. But each time only one side of the operation can not be carried out at the same time.
The operation status of each piece of equipment can be dynamically displayed in the process flow, and can be displayed in the status table of its running, stopping, fault, manual, automatic and other states. You can use the mouse to manually operate (according to process requirements) each piece of equipment on the computer to make it run and stop.
Real-time animation and real-time curve display production process, real-time display of steel temperature, water temperature, water flow, liquid level and other production process parameters.
5、Intelligent voice alarm
Intelligent voice alarm is a kind of high-tech product developed by our company independently, in addition to light and voice output, different alarms have different voice content output, can be recorded at any time according to the need to modify the alarm content, the sound is clear and bright.
Intelligent voice alarm in the batching machine, strengthen the alarm ability, when there is a fault, the voice can be used to point out the fault directly.
Third, the main functions accomplished
It mainly accomplishes the automatic control and weighing automatic compensation of bulk material, oxygen gun, storage tank tilting and weighing instrument.
1、Bulk material part:
① The weight value of each weighing hopper can be set on the upper computer at any time according to the requirements of mixing, displaying the weighing value, error value, class accumulation and total accumulation of each time, automatically calculating the next set value and making history curve, and the class accumulation can be cleared to zero at the time of shift handover, and the report can be printed at any time.
②Weighing process, due to the program has a set amount of advance, and automatic error compensation function, the batching system will be based on the weight of each vibration material and the last error and the amount of advance and other parameters automatically calculate the weight of the next vibration material, so as to accurately stop vibration material machine. It realizes automatic and accurate weighing of lime, ore and materials, automatic compensation between each batch of materials, alarm for over difference and automatic correction of compensation amount, and automatic tracking of zero point.
③After the automatic compensation of error, after a long time of production, the cumulative error is less than 5Kg, (except for human factors and equipment failure).
Weighing time is not more than 60 seconds, mixing time is not more than 50 seconds, and it has the functions of no stoppage for jammed material, automatic lifting of alarm and automatic time-delayed dosage.
2、Storage tank tilting part
①In order to improve the synchronization performance of the motor, in the storage tank tilting choose a single frequency converter for multiple motors, thus reducing the synchronization communication brought about by the asynchrony.
②The left and right tilting of the storage tank is controlled by manual command. As the tank mixing process of each tank steel uncertainties
Because there are many uncertainties in the mixing process of each tank, automatic control will undoubtedly increase the failure rate of the whole dosage system. The whole tank tilting process we will realize multi-step speed control, low-speed start, low-speed stop. Through the manual master order on and off to the host computer and PLC to send signals, PLC receives the master order signal, processing and analysis, PLC's output point control frequency converter, different output points correspond to different frequency converter output frequency, so that the motor to achieve the purpose of the multi-segment speed operation. When it is necessary to adjust the motor speed only need to modify the internal parameters of the frequency converter on the operation panel of the frequency converter, without adjusting the whole control.
Through the DIS-V type storage tank tilting angle display instrument specially developed for storage tanks by our company to dynamically display the tilting angle of storage tanks, the operator can know the current angle of storage tanks more clearly by observing the angle display instrument, thus reducing the incidence of accidents.
3、Oxygen gun lifting part
The precise control of the main and reserve oxygen guns adopts the intelligent main order controller, which is the replacement product of the old main order, and the accuracy of its positioning can reach millimeter level. Through the high-precision electronic encoder connected with the winch, the on-site data signal is collected, processed and analyzed inside the S7-200PLC and output, the output point of the intelligent master order controller enters the main control dosing system, and the output point of the main control dosing controls the operation of the frequency converter, so as to achieve the precise positioning of the upper limit point, the upper variable-speed point, the point to be blown, the lower variable-speed point (the oxygen opening point), the blowing point, and the lower limit point. Through the Siemens Chinese operation panel TD-200, the number of points corresponding to each output point can be adjusted on the operation panel to achieve the purpose of precise positioning.
4、Weighing instrument part
The weighing instrument enters into PLC, canceling the original secondary weighing instrument in the dosage, and all the data are displayed in the upper computer and printed by the printer after being processed by PLC. As the signal collected by the sensor directly enters the PLC without secondary weighing instrument processing, it reduces the distortion factor and uncertainty factor in the signal transmission process, making the signal more stable and the batching system more reliable. It makes the signal more stable and the batching system more safe and reliable.
5、Camera monitoring dosage system
In order to improve the safety and reliability of the whole dosage, the camera monitoring system is adopted, which is mainly composed of PTZ, zoom lens, color camera, electronic temperature-regulating outdoor shield, PTZ and lens controller, screen separator, and other equipment.
Zoom lens and color camera connection, installed into the outdoor electronic temperature control enclosure, and then the whole fixed in the PTZ. Through the four screen separator to the multi-channel sampling lens into the industrial color monitor, while the operator can also choose the screen according to the situation want to observe the screen, zoom in or zoom out on the screen.
The operator is placed in the main control room through the PTZ and lens controller to operate the PTZ left and right and up and down movement, to realize 360 degrees of rotation and control, thus expanding the field of view to increase the scope of the whole monitoring.