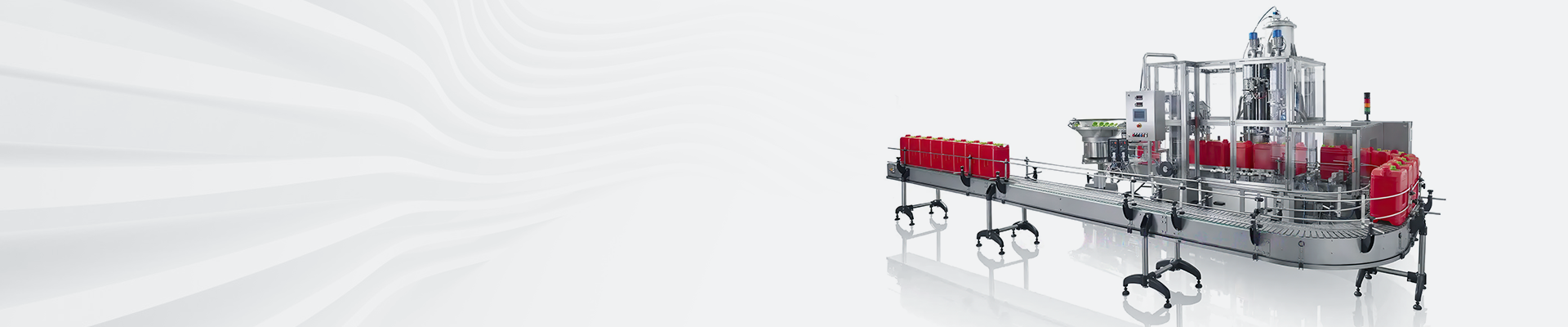
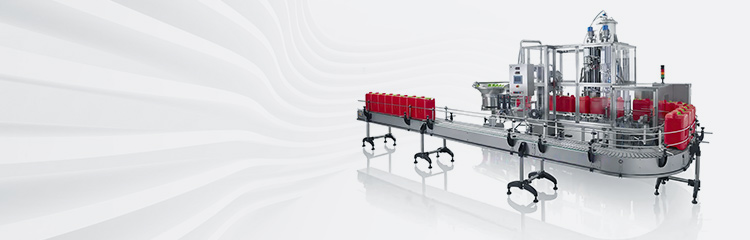

Summary:The automated batching system can set, manage and optimize the control of the production line to achieve batching control, mixture control, loading and priming material control in the paint factory, and reactor proportion adjustment end point.
In order to ensure product quality and improve production efficiency, accurate and reliable dosage is required. In the existing dosage of paint materials, the workers firstly transport the materials to the weighing workshop, and after weighing, the materials are manually sent to the dosage equipment for dosage. The weighing workshop uses the weighing instrument for weighing, which is connected to the industrial control host through RS232 port, and the industrial control host located in the central control room is responsible for recording the weighing results and displaying the weighing data. At the same time, the controller can manually control the starting and stopping of the dosage process through the control circuit in the central control room. This method is inefficient, at the same time, the host computer is running DOS program developed in C language, poor scalability, human-computer interaction is difficult, and can not complete all the requirements of automatic batching.
In order to increase productivity and reduce costs, fully automatic batching is required. The automatic batching system adopts master-slave structure. Industrial control machine as the upper host, Siemens PLC, frequency converter and weighing instrument as the lower slave. The host is in the dominant position to realize the communication management and control of the slaves. The RS-232 asynchronous communication port of the industrial computer is connected to the PLC after level conversion to form a physical channel for the communication between the upper and lower units; another RS-232 port of the host is connected to the communication port of the weighing instrument to form the second physical channel. The upper computer adopts polling method to communicate with the slaves one by one. The upper computer transmits the results of the task planning to the product and application PLCs. In the process of PLC control, the upper computer uses the upper computer connection commands to monitor the lower computer's operation status and data area contents, and the internal status of the PLCs, as well as the real-time data of the weighing instruments, are displayed on the upper computer. In general, the fully automatic batching system has the following functions:
①Full-automatic dosage, after setting the recipe, the automatic dosage system weighs and dosages according to the recipe automatically without operator intervention;
② With report function, it can produce daily report, real-time report, monthly report and yearly report;
③ Dynamic increase and modification of reports, the automatic dosage system gives the technician or operator the right to modify and increase the formula by setting the authority, and at the same time records the date and operator number of the modification;
④ Power failure recovery function, the automatic batching system can recover the measurement records before power failure in case of sudden power failure;
⑤ LAN sharing function, the host computer can share the data in the LAN, which is convenient for the workshop supervisor to know the progress of the project and other situations.
The dosage machine realizes the dosage control of coating plant, mixing material control, feeding and laying primer control, reactor proportion adjustment end point and so on through the production line that can be set, managed and optimized control.
Paint automatic dosage system composition and principle
Batching equipment mainly consists of drag-type screw, disc mixing tank + servo screw, solvent agitator and so on. It is mainly composed of scale weighing module and speed measurement module, weighing display, equipment speed control device, reaction tank level detection equipment, as well as redundant PLC, host computer and its software. The design uses an uninterruptible power supply (UPS) to power the computer and PLC modules to ensure system power supply in case of external power failure.
Feeding system working principle:
The hardware of this automatic feeder adopts Siemens S7300 series and ET200 module, and the software adopts Siemens STEP7 series and WINCC series. The raw materials of the paint are dosed and controlled according to a certain proportion according to the process requirements, and at the same time the feeding system is given according to the information of the material level of each material reaction tank. The dosage control can be based on the weight of raw materials and chemical composition of the proportion control. At present, the domestic manufacturers are mainly based on the weight proportioning method.
Weight proportioning is to control the raw material reaction tank under the spiral and feeding device, according to the theoretical flow rate of the weighing spiral and feeding device, PLC set up the proportion of raw materials and the total amount of feeding, and at the same time, we should take into account the relationship between the raw material reaction tanks arranged in the order. Through the communication of the upper computer, the flow rate of the equipment under each reaction tank is set. After the system is started, the weight signal and speed signal are sent to the secondary weighing instrument, and the instantaneous flow rate and cumulative amount are calculated through the amplified A/D conversion and displayed on the on-site weighing instrument. The indicator uploads the signals to the PLC metering module, the PLC analog input module collects the weight and speed signals from the weighing screw and feeding device, and carries out the self-tuning operation according to the parameters set by the user, and if there is a deviation between the set value and the current value, then the PLC analog module outputs a standard signal (4-20mA) to the frequency converter for the device to be adjusted, and the frequency converter will change the rotational speed of the device in real time when it receives the signal from the PLC. After receiving the signal from PLC, the frequency converter will change the rotational speed of the equipment in real time, which will reduce or increase the feeding for the disk and reduce or increase the material flow for each speed control. Thus the dosage has a stable state. When normal operation for a certain period of time, mixed reaction tank material level will fluctuate because of the paint arrangement, when the thickness of the material layer with the car is stabilized, the PLC according to the weight of the material in the tank measured by the mixed reaction tank weighing module to the dosage reaction tank of each downstream port for flow adjustment, to ensure that the mixing of storage tanks in and out of the balance of the material. Mixed material automation is mainly for the two mixing with solvent control and electrical interlocking. Because the purpose of a mix is to mix, so according to a mix of the total amount of mixed material and a mix of pre-moisture detector moisture value at the right time by a certain percentage of solvent calculation, through the control of a mix of water pipes on the electric valve to regulate the flow of incoming water. The current value of the dosage reaction tank under the mouth of the material flow calculated cumulative and shared to the feeding system, according to the total amount of material and material into a mix before the percentage of water content to calculate the need to add how much solvent to a mix, for a mix of automatic solvent to provide solvent benchmarks.
Weighing mixer features
Intelligent weighing and mixing machine is specially designed for screw, reamer, disc, etc., is a high-performance set of measurement, control, display in one of the dosage equipment, industrial-grade components design, the display adopts the VFD high-brightness deluxe fluorescent Chinese characters, SMD process production, a variety of anti-jamming measures and single-chip microcomputer the latest research results, has a powerful, small size, high reliability and adaptability, etc. Features. Can be applied to various forms and various ranges of spiral control. It has many outstanding advantages such as reliable quality, accurate measurement, high control accuracy, flexible use and convenient operation.
The functions and features of weighing and batching system are as follows:
Adopting field bus technology, fast communication speed, long communication distance and high reliability.
Dual CPU hardware structure, good real-time and high control accuracy.
High-brightness color fluorescent tube character display, can display 2 rows of 40 dot matrix characters. Display information is rich, intuitive, easy to operate.
Input and output interfaces adopt various hardware anti-interference technologies.
The instrument can be operated by keyboard, external signal (port), remote terminal and upper computer.
Can be weight calibration, chain code calibration, real material calibration and other calibration methods to meet different user requirements.
Intelligent PID adjustment, optional parameter self-tuning function.
It can be connected with upper computer, PLC or DCS through instrument interface, remote expansion module and communication interface.
Maximum and minimum values of analog input/output signals can be set.
Standby or running status display parameters can be customized by the user.
Two control modes: flow control and totalization control.
Two working modes: speed control and constant speed.
Various alarm outputs can be set.
All parameters are set with upper and lower limits and default values, which are set according to the default values at the factory, and all parameters are automatically restored to the default values when the factory setting function is executed.
There is a totalization pulse output, the pulse width and equivalent (the weight of material represented by each pulse) can be set through the parameter.
The "flow rate setting mode" and "start-up mode" can be parameterized as "instrument keypad", "external interface", and "external interface". "External interface" and "Communication".
The PLC control system is characterized as follows:
Adopting field bus technology, fast communication speed, long communication distance and high reliability.
CPU hardware structure, good real-time, high control accuracy.
According to the material reaction tank level information to prompt the raw material feeding.
Input and output interfaces use a variety of hardware anti-interference technology.
Intelligent PID adjustment, can be self-tuning.
It can collect, process, record and monitor the data in the production process in real time.
It can realize the adjustment of the proportion of each ingredient online according to the production needs.
It has the functions of class production, daily production and monthly production totalization.
On-site weighing reaction tank instrumentation display all in and out of PLC control, to realize the two-location display.
The whole process of automatic dosage, for independent closed-loop control, can realize manual dosage.
The upper computer adopts industrial control machine, simulation screen display. It is easy and convenient to operate with mouse for total setting, proportion setting, start/stop, parameter setting, and so on.
It has 485 interface communication function, data processing and control function.
The microcomputer automatically records the running and operating conditions, which can be consulted at any time.
Emergency stop operation box is set up at the site, which can operate and fault emergency stop for each circuit equipment at the site.
In summary, the PLC plus intelligent weighing instrument weighing and feeding system is more reliable, usually mainly for PLC centralized control, PLC failure intelligent instrument can also complete the dosage work. At the same time, the maintenance and operation of the dosage is also more simple.