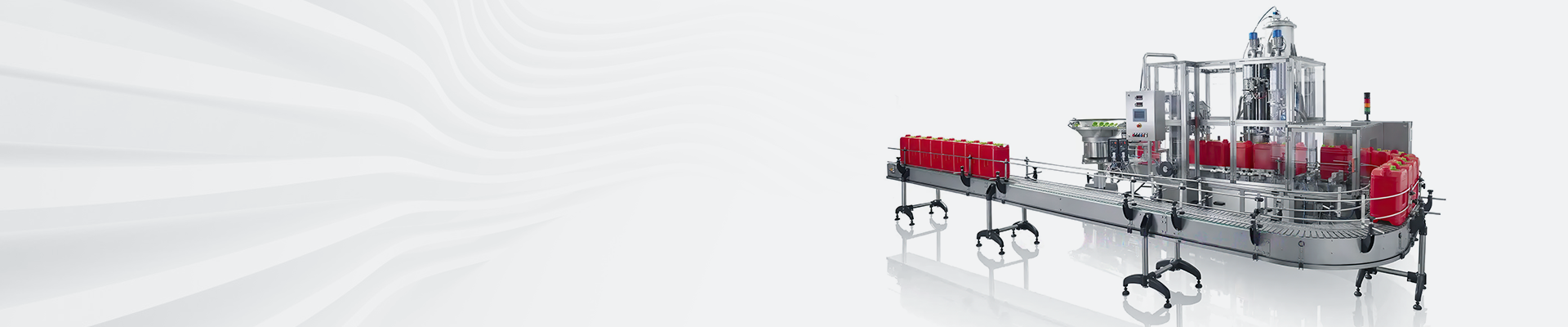
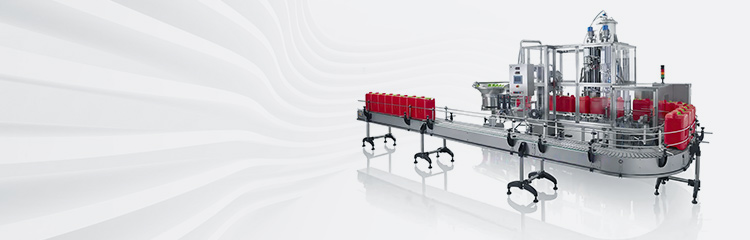

Summary:Automatic batching systems are mainly used in resin, isopropyl alcohol and other industries. Using the recipe control function of CAN bus technology, the automatic batching management needs of this industry can be easily solved.
Automatic dosage system is mainly used in resin, isopropyl alcohol and other industries, the use of CAN bus technology of the formula control function, can easily solve the industry's automatic dosage management needs, dosage PWC each functional module using CAN bus type connection, can be installed close to the equipment to reduce the field wiring, reduce the use of cost and maintenance costs, improve system reliability.CAN bus is one of the mainstream five buses. CAN bus is one of the five mainstream buses today. Using the ISO/OSI model of the physical layer, according to the link layer and the application layer, CAN communication protocol, one of the most important features is the abolition of the traditional address coding, replaced by the communication database coding.CAN bus data-oriented rather than node-oriented, the advantage is that the number of nodes within the network is not theoretically limited, to join and reduce the number of devices does not affect the work of the system. The highest rate can reach 1Mbps; transmission rate of 5kbps, the use of twisted pair, the transmission distance of up to 10km or so, and high reliability of data transmission. From the physical structure, the CAN network belongs to the bus communication network, and the general network difference is:
(1) Unlike networks for management and information processing such as Ethernet, it is a network specialized in the field of automation;
(2) Its physical characteristics and network protocol characteristics more emphasis on industrial automation bottom detection and control;
(3) With the latest technology and unique design, the reliability and performance are much higher than the already obsolete field communication technology. When using distributed control, the modules and control of electrical components can be located directly in each batching unit, so it can reduce a lot of wiring work, reduce the cable material, for large concrete plants and mobile combined concrete plant this point is particularly meaningful.
The use of CAN bus technology for the implementation of such projects is briefly described:
The implementation of such projects is mainly the use of CAN bus technology software for automatic switching and maintenance of the dosage program. The hardware composition of the current system is mainly the following two ways:
1, to board plus PC machine mode;
2, to PLC plus PC machine mode. For some small systems such as ethyl acetate, sodium sulfide solution weighing system can be used to program a hardware configuration, its system is simple, affordable, can meet the basic needs of users.
The configuration of the dosage machine is generally as follows: industrial controller (industrial IO board) Multi-serial communication card (such as MOXA card). RS232/RS485 conversion module can also be used instead of the multi-serial port card. Dosing PWC various modules The main components of the system, currently provides eight different functional types of modules, mainly:
Main control module: integrates multi-specification software functions such as HMI, soft logic, single database, dosage algorithm software. At the same time, it is responsible for the coordination and management of various sub-modules, comparing the different types of data from various sub-modules with the values set by the user, making logical judgments according to the input and output status of each switching quantity, and outputting the action requirements through the following sub-modules, such as analog output module and switching output module, to the control equipment, which is equal to the PLC's CPU function;
Weighing module: It is mainly used for the measurement of weight and also contains 4-channel switching inputs and 4-channel switching outputs;
AIO module: the module has 4 ~ 20mA analog input and analog output of each two channels, the acquisition channel can have 4 ~ 20mA output module, equipment, etc. for the acquisition; the output channel can be used to drive the control equipment, such as frequency conversion speed control.
DIO module: contains 8-channel digital input and 8-channel digital output, mainly used for on-site switching input and output, the input node connects the passive contact (dry contact) of the equipment, such as button input, travel switch, proximity switch, etc., and the output node is a relay output, with contact capacity of AC250V5A, DC30V5A, which can drive the AC contactor, solenoid valve and so on;
AI module: with 4 analog input channels of 4~20mA, its function is the same as the input part of AIO module;
DI module: provides 24 channels of switching inputs with the same contact type as the input contact type of DIO module;
AO module: with 4-channel 4~20mA analog output;
DO module: with 24-channel switching output, contact capacity of AC250V5A, DC30V5A switching output. The software is CAN bus technology general software. This system is relatively small, the dosage process is not too complex, the main screen of system monitoring is as follows:
The dosing system is as follows:
Selection of appropriate formula;
Calculation of the actual weight;
Confirmation of the empty tare weight;
Select the automatic dosage mode;
Open the hydrogen peroxide material door, dosage additives until the additives reach the set value (i.e., additives 1 = current weight of the scale minus the empty scale tare), close the additives door switch, delay 1 second, assign the difference between the current scale weight and the empty scale tare to the actual acetone and start dosage of the next batch of material sign.
6、When the next batch of material flag is set up, the cyanohydrin nitric acid material door is opened, start to match the additives until the additives reach the set value (i.e., additives = scales) the current weight minus the tare weight of the empty scale and then minus the weight of the additives, close the additives door switch, delay for 1 second, the current scale minus the tare weight of the empty scale and then minus the weight of the additives is assigned to the actual crushed stone, and start to match the next batch of material flag. Using the powerful configuration function of CAN bus technology software, it is very simple to realize the above dosage function. When the dosage system for large neutral dimethyl sulfoxide processing plant and other large-scale dosage system, due to the complexity of the system, the use of boards and PC program obviously can not meet the control requirements.
The dosage hardware configuration for industrial control machine PLC (Mitsubishi FX series or Siemens S7-200/300 series or other series) DP communication card or other communication methods.
Software configuration for the CAN bus technology general-purpose software.
Dosing control system formula types are: phosphorus trichloride, aluminum trichloride solution, co-solvents, emulsifiers, active agents, alcohol solutions, hydrochloric acid, ethanol, water, etc., the computer according to manually set the amount of dosage, with or without the choice and pre-set timing to automatically complete the entire dosage process of various types of interlocking and control, the two types of dosage systems can achieve the following functions:
Realize automatic interlocking and control of feeding, discharging, mixing and discharging;
It can realize the functions of manual operation of measuring, feeding, discharging, mixing and discharging;
Can display the real-time working condition and various material parameters. It can call and display and print any time report and customer table at any time. With proportion pre-storage, you can input, modify or delete a certain proportion at any time.
Beautiful and practical dynamic simulation. The dynamic screen simulates the dosage valve, the weighing hopper door, and the discharge status (change of material level in the weighing hopper) during the weighing and unloading process.
Coarse weighing and fine weighing functions. (Fine weighing advance has automatic adjustment function to eliminate the effect of fallout), over-difference automatic alarm, automatic deduction function.
With operator rights management function.
With on-site management and networked remote service.
Support third-party commercial database. At present, Asian control company launched a new generation of soft logic control software (KingACT), to a certain extent, can replace the function of PLC control, KingACT software based on the fieldbus equipment (or board) to complete the monitoring of the equipment, and with CAN bus technology software seamless data exchange. It has a good price/performance ratio.