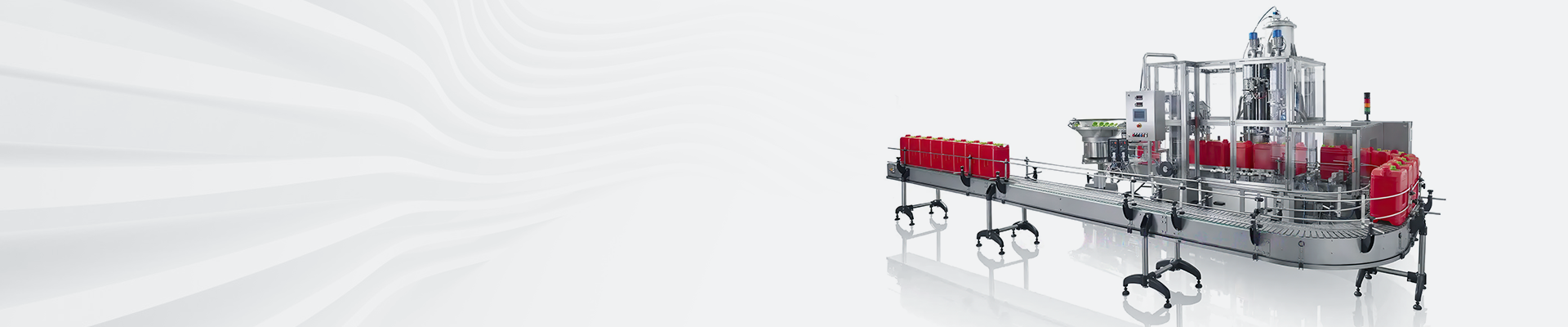
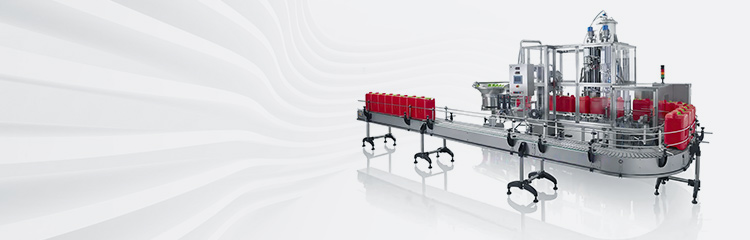

Summary:The automatic batching machine integrates feeding, weighing, and discharging. The feeding and transportation are completed in sequence to complete the transportation and control of materials.The current passing through the on-site pressure display instrument and the motor is remotely transmitted to the central control room for centralized display through the on-site display instrument.The frequency converter adjustment is equipped with an automatic switch to communicate with the main control computer.
Preface
Aseptic preparations are a class of pharmaceutical preparations that do not contain any live microbial propagules and spores in an aseptic environment using aseptic handling methods or automated dosing machines. Contamination in aseptic operation can be mainly categorized into uncontrollable active contamination (e.g. presence of microorganisms such as bacteria and viruses) and controllable inactive contamination (e.g. preparation dosing equipment, etc.). So the automatic dosing system becomes an important part of aseptic preparation. According to the requirements of GMP, container critical area, clean area, filtration area, etc., we provide a solution of dosage and CIP station system for aseptic preparation for Miyuemotochu.
The solution successfully achieves a high degree of automation of the production process with reasonable operation and maintenance processes, and is able to meet GMP specifications [2-3] and operational capabilities such as CIP [4] in the design of the equipment, as well as drainage, drying, and sterility requirements. The system is equipped with multi-channel valves and other switching operations, in order to prevent cross-infection requirements can also be easy to operate. At the same time, there is a perfect fault diagnosis and elimination mechanism to ensure that the product is protected to the greatest extent possible.
2 Requirement Objective
Freeze-drying dosing is designed to concentrate dispersed products, excipients, and solvents, which may be as simple as mixing liquids, dissolving solid active substances, or more complex operations of homogeneous emulsification or formation of liposomes. The main factors affecting dosage are warming properties, concentration of the main ingredient and excipients, pH of the finished product, dosage containers, piping, and so on. Mewon Herb requires a lyophilized dispensing system capable of completing the lyophilization process, including a configuration system and a CIP station system.
The installation and operation of the dosing system needs to meet the design requirements, the information and documents meet the GMP management requirements, the no-load and load conditions of the dispensing system meet the production requirements, the cleanliness of the production environment meets the cleanliness standards, and the microorganisms present in the production environment meets the microbiological testing standards. The equipment is used to complete the preparation of raw materials to the specified concentration of drug solution during the whole production process, which includes the preparation of standard concentration of drug solution, the adjustment of drug solution pH, the control of drug solution temperature, the sterile filtration of the filter, and the reception of the filtrate. With in-situ cleaning system, according to the process requirements of the distribution system and its pipeline in-situ cleaning, in the process of cleaning the tank without dead ends. With in-situ sterilization system, the dosage tank, filter, filtrate receiver, other connected parts of the positive pressure should be designed and manufactured according to national standards. Pure steam sterilization shall be in-line steam with the dispensing system and shall be accompanied by a manual to test the integrity and effectiveness of the filters.
Overall System Construction Program
The system requires SIEMENS S7 1200 model PLC [5] as the host controller and SIEMENS ET 200SP distributed remote I/O system as digital and analog inputs and outputs. Under this framework, the design of the configuration system and CIP station system of the lyophilized distribution system is completed.
It enables the system to be used for the configuration and filtration of pharmaceutical liquids for different products, with functions such as stirring and in-place weighing of liquids. The loading system is mainly composed of host, tank, magnetic stirring, centrifugal pump, self-priming pump, weighing, touch screen, etc. It is equipped with CIP function, and the CIP station system is automatically controlled by the control system, which cleans and sterilizes the inner surfaces of the airtight containers and pipes.
Characteristics of the system
The feeding system features fully automatic dosing, which reduces the possibility of errors in manual operation, improves production efficiency and reduces operating costs, and has a unique automated execution program at the final stage of material delivery to ensure that filter residues can be fully utilized. Equipped with the execution program according to the characteristics of the host PLC is completely set into a modular implementation, simple and convenient, easy to debug and change the reference, high fault tolerance, modularity also provides a convenient system disassembly and assembly.
The system implements a multi-stage perfect and optimized design, adopting a phased design when designing the system according to the different needs of customers at different stages. The basic design stage provides customers with program options, customers can choose the overall design layout for the system according to the needs of different scenarios, such as work scenarios, process performance, and so on. The detailed design phase provides customers with the design of system allocation, such as piping layout, valve adoption, etc., model effect preview and the design of automatic control functions. The detail design stage improves the overall operational quality of the system according to the special needs of the scene and the specific requirements of the customer.
The system can also realize the automatic setting of multiple varieties according to the proportion, which can reduce the risk of manual error and make the production process standardized and automated. At the same time, the system is able to automatically record the running time and parameters, and can actively set up alarm messages, which meets the requirements of high-standard production.
Project Validation
The configuration system of the lyophilized color matching system and the CIP station system were designed to meet the needs of Meiyuan Herbal in sterile preparations. The overall layout of the system is shown in Fig. 3. After the system design was completed and the execution program was uploaded, the project was tested and validated.
Supplier internal testing
Self-inspection to confirm whether the design and installation of the dosage system meet the design requirements, whether the information and documents meet the GMP management requirements, whether the system operation performance meets the production requirements, whether the calibration of the measuring instruments and so on is accurate, and whether the public media are connected completely and correctly, and so on. After all the links are confirmed, the system is tested and verified. Verify the loading, mixing and discharging of the system during load operation of the distribution system, and analyze the test results and data by combining with the system's sealing inspection records, dosing tank level inspection records, and agitator operation records, etc. If there is any error other than expected with the requirements, the system will be tested. If there is an error other than expected from the requirements, further analyze and improve the system.
The system implements a multi-stage perfect and optimized design, adopting a phased design when designing the system according to the different needs of customers at different stages. The basic design stage provides customers with program options, customers can choose the overall design layout for the system according to the needs of different scenarios, such as work scenarios, process performance, and so on. The detailed design phase provides customers with the design of system allocation, such as piping layout, valve adoption, etc., model effect preview and the design of automatic control functions. The detail design stage improves the overall operational quality of the system according to the special needs of the scene and the specific requirements of the customer.
The system can also realize the automatic setting of multiple varieties according to the proportion, which can reduce the risk of manual error and make the production process standardized and automated. At the same time, the system is able to automatically record the running time and parameters, and can actively set up alarm messages, which meets the requirements of high-standard production.
Project Validation
The configuration system of the lyophilized color matching system and the CIP station system were designed to meet the needs of Meiyuan Herbal in sterile preparations. The overall layout of the system is shown in Fig. 3. After the system design was completed and the execution program was uploaded, the project was tested and validated.
Supplier internal testing
Self-inspection to confirm whether the design and installation of the dosage system meet the design requirements, whether the information and documents meet the GMP management requirements, whether the system operation performance meets the production requirements, whether the calibration of the measuring instruments and so on is accurate, and whether the public media are connected completely and correctly, and so on. After all the links are confirmed, the system is tested and verified. Verify the loading, mixing and discharging of the system during load operation of the distribution system, and analyze the test results and data by combining with the system's sealing inspection records, dosing tank level inspection records, and agitator operation records, etc. If there is any error other than expected with the requirements, the system will be tested. If there is an error other than expected from the requirements, further analyze and improve the system.