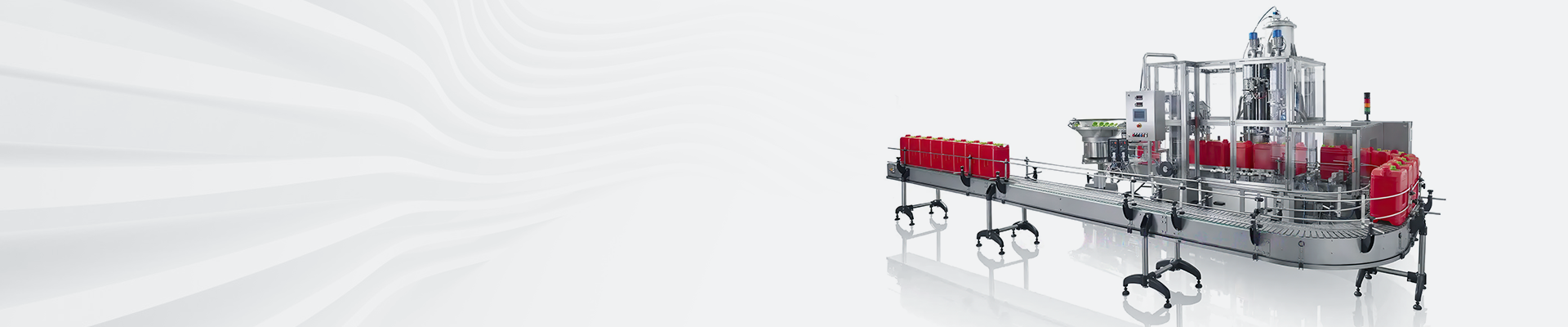
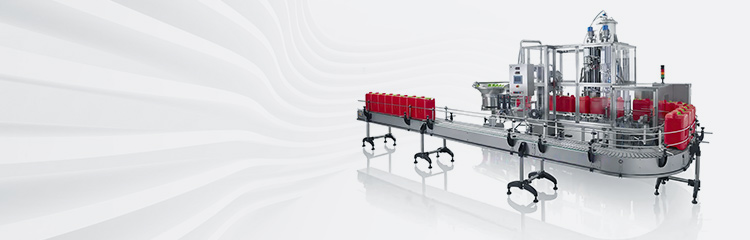
摘要:自动化配料系统通过可对生产线进行设定,管理和优化控制,实现涂料厂配料控制,混合料控制,上料铺底料控制,反应釜比例调节终点。
在油漆材料生产行业,配料通常是将原材料按某种比例均匀混合在一起,用以形成一种新的材料,因此配料是这类行业生产的重要组成部分。在生产过程中,各种原料要严格按比例进行均匀混合,就必须靠配料来完成,目前工厂一般使用两种方法,第一种方法采用人工称重,然后将成比例的各种原材料同时放入配料设备中搅拌。另一种方法是自动称重,自动搅拌。由于很多原始材料为粉状或颗粒,人工配料时,人体容易吸入粉尘等杂物,导致职业病出现,增加了生产风险和劳动力成本,同时配料品种繁多,数量巨大,因此人工配料难以现场管理,很容易出现误配,不但质量难以保证,同时也增加了管理成本。
为了保证产品质量,提高生产效率,要求采用准确、可靠的配料。基于PLC、工控机和称重仪表的配料设备在油漆材料现有的配料中,工人首先将材料运送到称重车间,称重完之后,再将材料手动送到配料设备上进行配料,称重车间使用了称重仪表进行称重,通过RS232口和工控主机相连,位于中控室的工控主机负责记录称重结果,显示称重数据,同时,控制人员可以在中控室通过控制电路手动控制配料过程的起停。这种方式效率低下,同时,主机上运行的是C语言开发的DOS程序,可扩性差,人机交互困难,不能完成自动配料的所有要求。
为了提高生产率,降低成本,需要采用全自动配料。自动配料系统采用主从式结构。以工控机为上位主机,以西门子PLC、变频器和称重仪表为下位从机。主机处于主导地位,实现对各从机的通信管理和控制,将工控机的RS-232异步通信口经电平转换后与PLC相连,形成上、下位机通信的一个物理通道;将主机的另一RS-232口和称重仪表的通信口相连,构成第二个物理通道。上位机采用轮询方式,逐个与从站通信。上位机把任务规划的结果传送给产品与应用PLC,在PLC进行控制的过程中,上位机使用上位机连接命令监视下位机的运行状态和数据区内容,PLC的内部状态以及称重仪表的实时数据,在上位机上显示。总体上讲,全自动配料系统具有如下功能:
①全自动配料,在设定好配方之后,自动配料系统自动按照配方称重配料,无需操作人员干预;
②具有报表功能,可以产生日报表,实时报表和月报表、年报表等;
③动态增加和修改报表,自动配料系统通过设定权限,赋予技术人员或操作人员修改,增加配方的权利,同时记录该次修改的日期和操作人员编号;
④断电恢复功能,自动配料系统能够在突然断电的情况下,恢复断电前的测量记录;
⑤局域网共享功能,主机在局域网内可以共享数据,方便车间主管了解工程进度和其他情况。
配料机通过可对生产线进行设定,管理和优化控制,实现涂料厂配料控制,混合料控制,上料铺底料控制,反应釜比例调节终点等等。
涂料自动配料系统组成和原理
配料设备主要由拖拉式螺旋、圆盘混合罐+伺服螺旋、溶剂搅拌器等。其主要由秤体称重模块和测速模块、称重显示器、设备调速装置、反应罐体料位检测设备,以及冗余的PLC、上位机等及其软件组成。设计用不间断电源为计算机以及PLC模块供电,以便在外电源发生故障的情况下保证系统供电。
喂料系统工作原理:
该自动喂料机硬件采用西门子S7300系列和ET200模块,软件采用西门子STEP7系列和WINCC系列。涂料原料按工艺要求按照一定的比例进行配料控制,同时根据各料反应罐的料位信息给出上料制度。配料控制可以根据原料的重量和化学成分进行配比控制。目前国内厂家配料主要按重量配比法进行。
重量配比是对原料反应罐下螺旋和给料装置进行控制,根据称重螺旋和给料装置的理论流量,PLC设定好原料的配比和总给料量,同时要考虑原料反应罐排列顺序的关系。通过上位机通讯设定每个反应罐下设备的流量,待系统启动后重量信号和速度信号送到二次称重仪表,通过放大A/D转换,计算出瞬时流量和累积量,并显示于现场称重仪表。称重显示器在将信号上传给PLC计量模块。PLC模拟量输入模块采集称重螺旋和给料装置的重量信号和速度信号,根据用户设定的参数进行自整定运算,如果设定值与现行值有偏差则PLC模拟量模块将针对需调节的设备输出一个标准信号(4~20mA)给变频器,变频器接受到PLC的信号后将实时改变设备的转速,对于圆盘则使给料减少或增多,对于各调速称则使物料流量减少或增多。从而使配料有一个稳定状态。当正常运作一定时间后,混合反应罐料位会因为涂料布置情况出现波动,当带车料层厚度稳定后,PLC根据混合反应罐称量模块测出的罐内物料的重量对配料反应罐各下料口进行流量调节,保证混合储料罐进出料平衡。混合料自动化主要是对两次混合进行加溶剂控制和电气连锁。由于一次混合的目的在于混匀,所以根据一混前混合料的总量和一混前水分检测仪的适时水分值按一定百分比进行加溶剂计算,通过控制一次混合家水管上电动调节阀来调节进水流量。将配料反应罐各下料口现行值累加计算出物料流量并共享给上料系统,根据物料的总量和物料进入一混前的含水百分比计算出需要给一混加多少溶剂,为一混自动加溶剂提供加溶剂基准。
称量混合机特点
智能称重混料机是专门针对螺、绞刀、圆盘等设计的,是一种高性能集计量、控制、显示于一体的配料设备,采用工业级元件设计、显示器采用VFD高亮度豪华荧光汉字、贴片工艺生产、多种抗干扰措施和单片机最新研究成果、具有功能强大、体积小、可靠性高和适应性强等特点。可适用各种形式和各种量程的螺旋控制。具有质量可靠、计量准确、控制精度高、使用灵活、操作方便等很多突出优点。
称重配料系统功能及特点如下:
采用现场总线技术,通讯速度快,通讯距离远,可靠性高。
双CPU硬件结构,实时性好、控制精度高。
高亮度彩色荧光管字符显示,可显示2排共40个点阵字符。显示信息丰富、直观、操作方便。
输入输出接口采用多种硬件抗干扰技术。
可通过键盘、外部信号(端口)、远程终端和上位机等对仪表进行操作。
可以砝码标定、链码标定、实料标定等多种标定方法,以满足不同用户要求。
智能PID调节,可选参数自整定功能。
可以通过仪表接口、远程扩展模块和通讯接口等方式与上位机、PLC或DCS相连接。
可以设定模拟输入/输出信号的最大值和最小值。
待机或运行状态显示参数可由用户自定义。
具有流量控制和累计控制两种控制方式。
具有调速和恒速两种工作模式。
可设置多种报警输出。
所有参数都设置上下限和省确值,出厂时按省确值设置,执行出厂设置功能时,所有参数自动恢复为省确值。
设有累计脉冲输出,脉冲的宽度和当量(每个脉冲代表的物料重量)可通过参数设定。
仪表“流量设定方式”和“启动方式”可通过参数分别设定为“仪表键盘”、“外部接口”、和“通讯”三种方式。
PLC控制系统特点如下:
采用现场总线技术,通讯速度快,通讯距离远,可靠性高。
CPU硬件结构,实时性好、控制精度高。
根据料反应罐料位信息提示原料上料。
输入输出接口采用多种硬件抗干扰技术。
智能PID调节,可自整定。
可对生产过程中的数据实时采集、处理、记录和监测。
可以根据生产需要在线实现调节各配料的配比。
具有班产量和日产量、月产量累计功能。
现场称重反应罐仪表显示全部进出PLC控制,实现两地显示。
全过程自动配料,为独立的闭环控制,可实现手动配料。
上位机采用工控机,仿真画面显示。总给定设定、配比设定、开停机、参数设定等用鼠标操作,简单方便。
具有485接口通讯功能、数据处理及控制功能,
微机自动记录运行、操作情况,可随时查阅。
现场设急停操作盒,可在现场对各路设备进行操作和故障急停。
综上所述,采用PLC加智能称重仪表的称量投料系统可靠性更高,平时主要为PLC集中控制,PLC故障时智能仪表也可以完成配料工作。同时配料的维护及操作也更加简单。