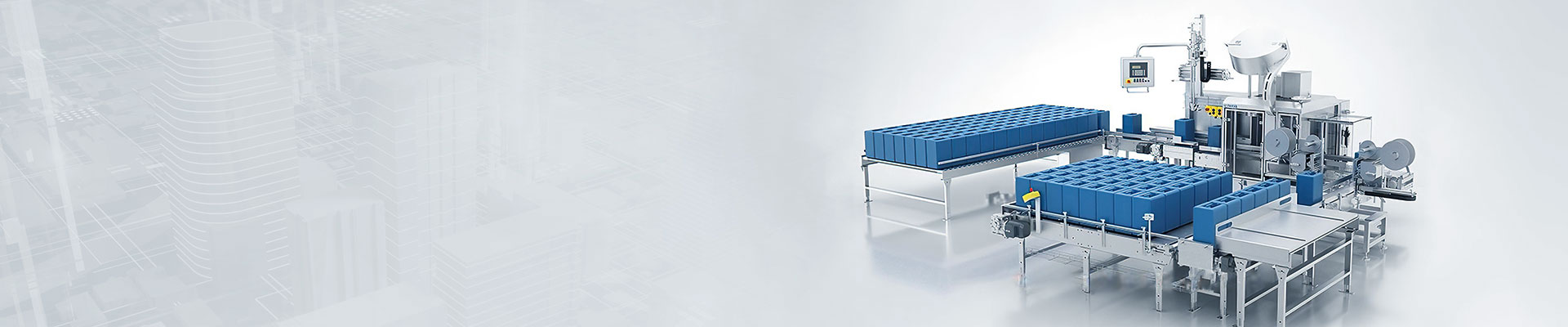
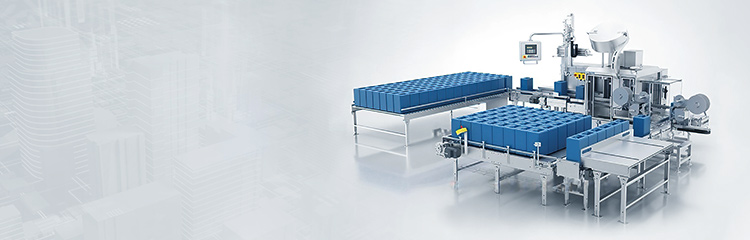
The automatic batching system is composed of industrial computer, PLC computer control system, feeding control device, etc. The weight signal is directly controlled into the corresponding weighing controller through the weighing module signal, and the weight signal is transmitted to the computer through the serial port or the Modbus protocol weighing controller. The computer controls the control valve of each raw material bin according to the batching weighing and provides power through the expansion and expansion of the hydraulic cylinder. The fine-tuning gate moves up and down the linear guide rail to adjust the distance between the gate and the round roller feeding device to achieve the desired discharge effect.

Automatic Batching system by the industrial computer, PLC computer control system, feed control device, etc., its control structure is as follows: The signal of each weighing module is directly entered into the corresponding weighing controller, and the weight signal is transmitted to the computer through the serial port or the Modbus protocol weighing controller. The computer controls the control valve of each raw material bin according to the battering weight, and provides power by using the expansion and expansion of the hydraulic cylinder. The fine-tuning gate moves up and down along the linear guide rail to adjust the distance between the gate and the round roller feeding device. Achieve the desired discharge effect.
The hopper fan-shaped main gate and feed hopper body are hinged by hinge shaft, and the opening of the main gate is adjusted by using the weighing module to adjust the up and down action of the main gate hydraulic cylinder. The fine-tuning gate is arranged on the main gate and divided into a number of fine-tuning gates in the direction of the width of the gate. Generally, the width of a fine-tuning gate is less than 1m. It can move up and down on the main gate and use the expansion of the hydraulic cylinder to provide power and realize the adjustment of the opening of the gate. The feed hopper body is loaded with mixed materials. The initial state is that the fan-shaped main gate is tightly pressed on the surface of the round roll Feeder by the weighing module. When it is necessary to feed, the round roll feeder starts, the hydraulic cylinder on the fan-shaped main valve starts, pulls up the fan-shaped main gate, adjusts the gap between the fan-shaped main gate and the round roller, and makes the material fall smoothly. In the width direction, the opening of the fine-tuning gate can be carried out according to actual needs. When there are large materials blocking the gate, the aniseed discharge device of the fine-tuning gate can be manually adjusted to restore the original position after the large materials fall, so as to complete the supply of materials.