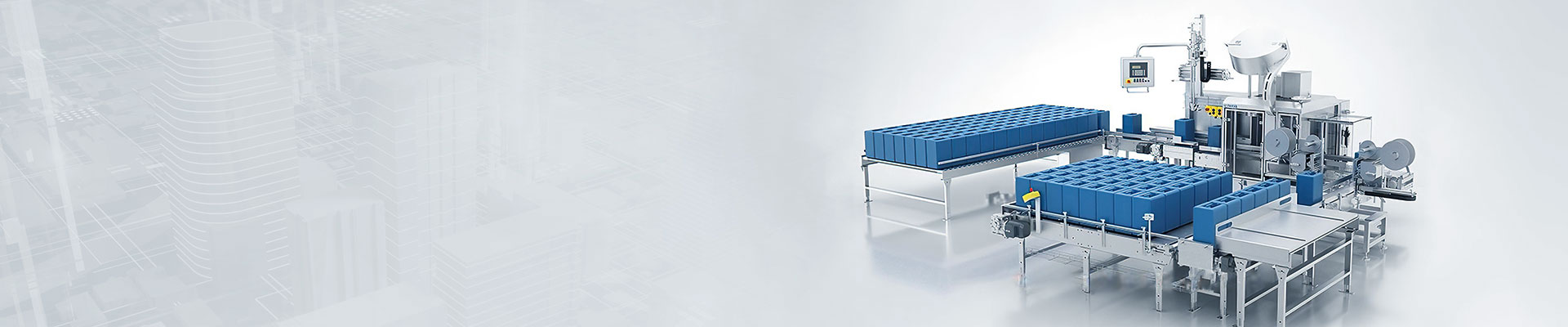
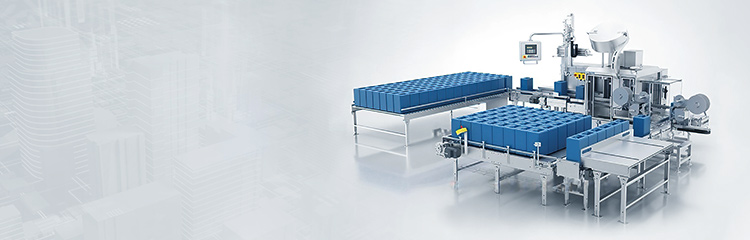
The weighing bridge of belt scale acts on the weighing sensor through a lever to send the weight of the material detected on the belt to the weighing instrument. At the same time, the speed signal of the belt conveyor by the velocity sensor is also sent to the weighing instrument. The instrument integrates the speed signal and the weighing signal to obtain the instantaneous flow and cumulative amount. The speed sensor is directly connected to the large diameter speed measuring drum and provides a series of pulses, each representing a belt movement unit, and the frequency of the pulse is proportional to the belt speed.

The automatic belt scale extracts the product from the storage hopper with a constant cross section and adjusts the extraction by changing the belt speed to maintain a constant weighing flow rate according to a set point of a fixed reference flow rate. It is composed of four parts: driving device, weighing device, belt Feeder and electric control system. The driving device is composed of a driving motor and a gear reducer. The weighing module is composed of weighing roller, Electronic scale support, weighing sensor, weighing instrument and belt speed measuring device. The belt feeder is composed of driven roller, bearing roller, receiving funnel, reversing drum, ring belt, belt tensioning device, belt inside and outside cleaning device, belt automatic deviation correction device, guide plate and feeder frame. The electronic control system is composed of control cabinet, control button, contactor and emergency stop device.
The bulk material in the storage bin flows to the ring belt of the belt scale through the discharge mechanism, and the weighing device installed on the feed scale measures the weight of the conveying material, generates a voltage signal proportional to the belt load and sends it to the weighing instrument. At the same time, the weighing instrument receives the speed pulse signal transmitted by the belt speed measurement device installed on the belt scale, and the weight signal and speed signal are integrated through the weighing instrument to show the instantaneous flow value and cumulative quantity value of the continuous output material.
Weighing instrument is the core of Weighing system, which is used to complete data acquisition, processing, operation control, display and so on. The object to be weighed transmits gravity to the weighing module in the form of pressure, and the weighing module can change the gravity acting on it into a linear voltage output. The tiny voltage output is amplified by the low-drift DC amplifier to the voltage amplitude required by the A/D converter, and then the analog voltage is converted into the corresponding digital amount through A/D conversion, which is processed by the CPU, and finally the quality of the heavy object is displayed in the LED, and some information can be input through the keyboard to intervene in the work of the CPU, such as requiring automatic zeroing.
Since the belt conveyor is the best tool for transporting continuous materials, and the belt of the belt conveyor provides a particularly favorable prerequisite for continuous weighing. By measuring the flow rate of bulk material in the conveying process, and integrating the flow rate of bulk material, the total weight of the conveying material can be obtained, which is composed of three parts: feeder, belt scale and control system. Both the feeder and the belt conveyor are driven by variable frequency motors. According to the lever principle, the belt scale is installed under the continuous operation of the belt lever device, the material above the belt through the bearing surface of the lever device, will produce a certain pressure on the bearing surface, through the lever device to transmit the pressure to the weighing module, and the control device will be the weight of the weight signal induced by the weighing module after amplification processing, in a digital way to display. At the same time, it can externally control the displayed digital signal, compare the detected bulk material flow signal with the set flow signal in the control system, adjust with PID, drive the inverter to change the speed of the feeder and the belt conveying motor, automatically change the speed of the belt according to the actual requirements of the feeding amount, and track the given feeding amount. As a result, the speed of the belt is slow when the material is long, the speed is fast when the material is small, and the slowest and even stop when the overload is the control characteristics, so as to obtain the given material flow.
Belt scale is a good continuous measurement of solid bulk material equipment, its accuracy is relatively high, the application is very convenient. Its weakness is open, dust leakage is more serious; The adhesion of dust, the tension of belt and the flatness of belt have great influence on the measurement accuracy. The maintenance workload is relatively large.
Technical parameters:
Single support accuracy: +/-1%
Multiple accuracy: +/-0.5%
Suspension accuracy: +/-0.125%~0.25%
Belt speed: 0~6m/s
Remote transmission: 1000m
Transport Angle: 0 ~ 30°
Ambient temperature: -20℃ ~ +50℃
Weighing instrument: 0℃ ~ 40℃
Power supply voltage: 220V (+10%, -15%) 50Hz±2%
Relative humidity: about 150%