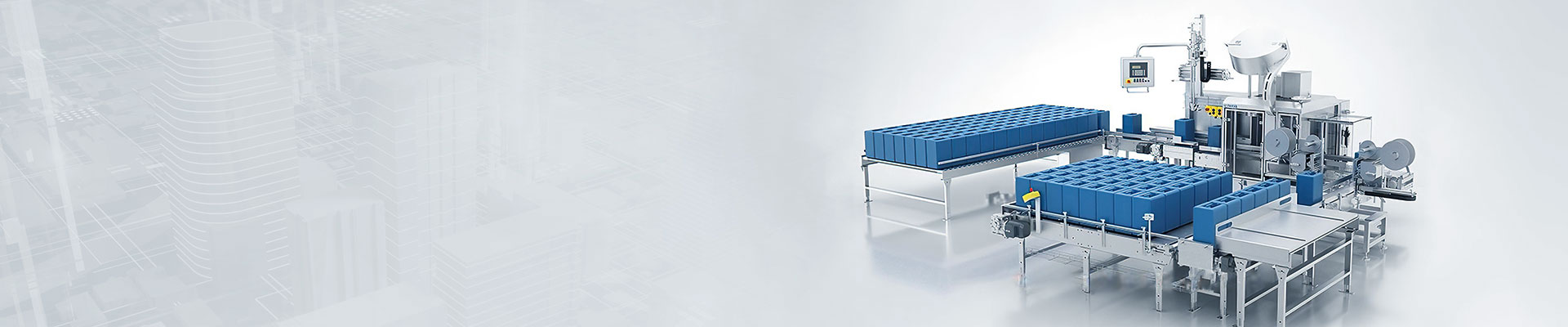
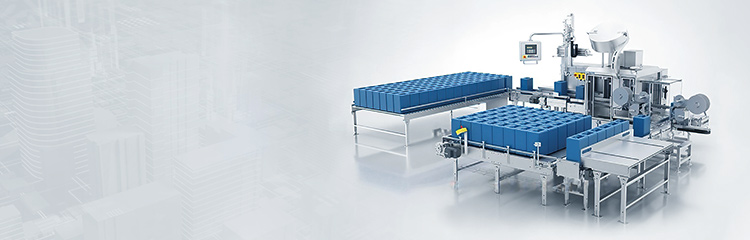
The belt scale is a measuring equipment for automatic and continuous weighing of bulk solid materials transmitted on the belt conveyor, which is mainly composed of weighing bridge, weighing sensor, velocity sensor, weighing display and so on. The load bearing device transfers the gravity of the material on the belt to the weighing sensor, which outputs the voltage (mV) signal proportional to the gravity of the material, amplifies the amplifier and then sends the analog/digital converter into A digital quantity and sends it to the arithmetic machine; After the material speed is input to the speed sensor, the output pulse number B of the speed sensor is also sent to the arithmetic machine; After the calculation of A and B, the material quantity of this measurement cycle is obtained. Each measurement cycle is accumulated to obtain the total amount of material continuously passed on the belt.

Belt scale includes information acquisition part, driving device, information processing part and measuring instrument. The drive device is composed of two parts: variable frequency motor and reducer. The speed of the belt is controlled by the variable frequency motor. The speed of the belt is changed by changing the speed of the variable frequency motor belt. Now the more common belt is the skirt belt, because it not only has a higher temperature tolerance and can prevent the material on the belt from spilling. Such a belt has a high service life and can concentrate the material to avoid unnecessary waste. The carrier can measure the material on the belt and transmit this data (the accuracy of weighing can reach 1%), with the role of load, weight and gravity transfer. The signal acquisition part is mainly responsible for collecting data, including the data transmitted by the weighing module and the velocity sensor. The data processing part is mainly responsible for processing the data transmitted by the weighing module and the velocity sensor to the computer. It includes signal sampling, signal filtering and amplification, A/D conversion, etc., which can calculate the instantaneous flow rate and cumulative flow rate of the belt scale. According to the results of data processing, the flow rate of the belt scale can be adjusted well and the parameters can be set to adapt.
The belt scale can measure the amount of coal at the end of a cycle and can also measure the cumulative amount of coal over a period of time, and the cumulative amount of coal is the result of accumulation. To measure the instantaneous coal quantity, it is necessary to measure the weight per unit length of the belt and measure the instantaneous speed of the belt. The instantaneous speed of the belt can be calculated according to the speed of the belt scale. If the measured value of raw coal transmitted on the belt in a certain unit length is q(kg/ m), then the transmission speed of the belt is v(m/s), Q=qv, 0 indicates the instantaneous coal amount. Since the coal flow rate at each moment is changing, the cumulative flow rate should be the integral value of the instantaneous flow rate over time.
Generally, the control cabinet of the belt is placed near the belt scale, so that it is convenient to carry out on-site debugging and maintenance of the belt scale and regularly calibrate the belt scale, and it is convenient to change the flow setting and parameter setting of the belt scale by moving the belt scale nearby. The electrical control system and weighing instrument are also placed in the control cabinet of the belt scale, and the operation of the on-site belt scale and the recorded data are reflected in real time to the coal injection central control room, which can change the flow setting of the belt scale or start and stop the belt scale according to the production needs or other considerations.
The belt control system mainly includes two systems: signal acquisition and signal processing. The function of the signal acquisition system is mainly to collect the motor start-stop state, belt tear and slip signals, and collect the switching and analog information of the equipment. The realization of this function is mainly completed by relays and various sensors. The function of the signal processing system is mainly responsible for the calculation and display of the signal, the system is mainly composed of PLC, man-machine interface industrial computer and so on.
The programmable controller is S7-200 controller produced by Siemens. The PLC can adapt to the harsh working face environment in the mine, has strong anti-electromagnetic interference ability to other electrical equipment in the mine, has high working reliability, and has flexible configuration. The CPU selected by PLC is CPU226. The PLC uses EM231 analog input module as the expansion module. The function of PLC is mainly to collect various signals on the site, calculate the collected signals through the program, and control the start and stop of the equipment according to the calculation results, while transmitting the signal to the upper computer, realizing the real-time monitoring of the belt conveyor. The function of the system control is mainly to achieve serial control of the coal Feeder, belt scale and vibrating screen, and the function of the system protection is mainly to alarm the slip, deviation and tear of the belt.
The control system mainly consists of two parts: control function and man-machine interface. The control function is realized through PLC programming, which is responsible for controlling the sequential start of the conveyor and the coal feeder, controlling the start and stop of the 1 conveyor and 2 conveyor, sending an alarm signal when the equipment fails and dealing with the fault. The human-machine interface is realized by WINCC6.0 configuration software, which can process the signals collected by the PLC. And in the form of sound, animation, images and other field equipment information presented to the controller.