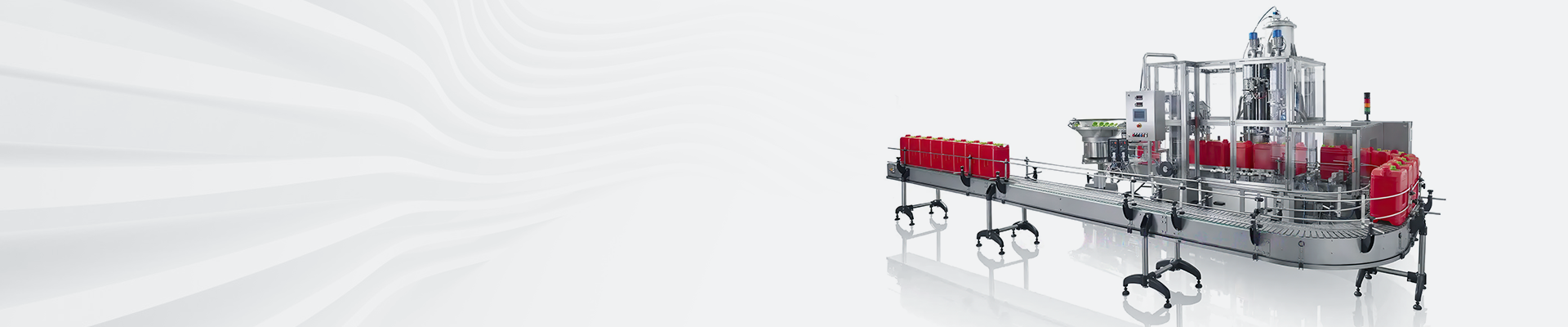
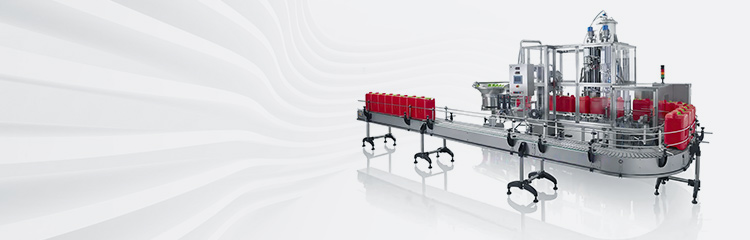

Summary:The liquid filling machine uses a programmable paint formula controller to automatically mix two liquids to achieve process data in formula control. The software provides a dynamic data exchange client module to exchange real-time and historical data with other applications.
The development of industrial computer filling machine has gone through two stages of centralized recipe control and distributed recipe control. Filling machine in the centralized recipe control mode, the computer not only has the process recipe control, real-time display conditions, data storage, report printing and other functions, filling system also completed the direct recipe control and data collection for each object. When the computer malfunctions, preventing normal lubricant formulation production. The development of microprocessor systems, network systems and communication systems for filling equipment has led to a distributed recipe control model.
To improve the reliability of automatic filling machines, i.e., in the event of a host failure of the filling hardware to back up other hosts, the backup host of the automatic filling machine will immediately take over recipe control of the heavy-duty filling machine to ensure continuous lubricant recipe production. Liquid filling machines use the popular virtual system, based on distributed recipe control, to provide primary recipe control from one of the hosts (in this case called the virtual host). If the host fails without increasing hardware costs, the virtual host will immediately take over the automatic filling machine recipe control, recipe control of all subordinate coordination tasks, to complete the material work, fully reflecting the "software that is quantitative filling machine" design concept, with a wide range of applications.
2 explosion-proof filling machine overall configuration and implementation
Liquid filling machine using programmable recipe controller to automatically mix two liquids. Weighing filling machine mainly taking into account the continuity and relevance of actions in different states, weighing filling machine for different states to perform different actions recipe control output, thus realizing the AB two liquid mixing cycle recipe control (including single cycle). Programmable recipe controller of automatic filling machine can save manpower and material resources, thus reducing costs. The rationality, comprehensiveness and reliability of the program make the liquid mixing safe and reliable.
Filling equipment has a modular structure for portability and maintainability. Filling equipment to improve the level of automation of production management of corporate lubricant formulations is greatly helpful. At the same time, it improves the efficiency, service life and quality of the automatic filling machine line and reduces the fluctuation of product quality in the enterprise. Therefore, the market outlook is bright. In order to meet the needs of the society factory was born.
The whole design process of the filling system is designed in accordance with the process flow to provide for the installation, operation, protection and maintenance of the filling system. The design is mainly based on the preparation of the filling device including: working conditions. Specific information is provided to the filling device formulation control circuit. The filling machine system is as economical and reasonably practical as possible, which ensures safety, reliability, dependability and speed, thus reducing costs. Programs and components are selected with greater consideration for filling equipment and new products. From manual recipe control to filling system recipe control, weighing and filling device from analog recipe control to computerized recipe control, filling device function realization from one to many increasingly perfect. Filling machine part of the transformation and upgrading of large-scale industrial control weighing and dosage system. Recipe control unit must be built according to the current situation of the enterprise dosage system and filling machine, metering and filling system and must use as much as possible the components of the old dosage system. The operating mode of the modified filling machine should be as similar as possible to the pre-modification mode, so that the operator can be quickly mastered. It is clear from the company's retrofit requirements that the new filling machine must handle both imitation volumes and large open and closed volumes. Automatic filling machines are highly reliable. The equipment human-machine interface is easy to use and must have data storage, analysis and summary functions.
Liquid filling machine as a whole by the master-slave industrial computer filling consists of a master-slave industrial computer through the serial bus (known as Bus I) associated with each slave (including the virtual host), the virtual host and other slaves (known as Bus u) is also associated through the serial bus, forming a dual-bus structure. The master controls the liquid filling machine via serial president 1 recipe, and the virtual master receives recipe control from the automatic filling machine and then controls the filling machine via the serial bus.
The main functions of the mainframe include process recipe control, real-time display and status alerts for weighing and filling devices, data storage library, report printing, recipe optimization and management consulting. Under host management, each system (including virtual hosts) controls its own objects according to the formula's required recipes and performs tasks such as data collection, processing, storage and display, troubleshooting and alerting, and data communication.
Pre-qualification of slave virtual hosts is performed during the setup of the liquid filling machine. If the host fails, the virtual host will take over the drawbar, recipe control each slave to coordinate and complete material operations.
3 Liquid filling machine and image processing recipe control exchange
Weighing filling machine in order to realize the liquid filling recipe control between the host and virtual host without interruption switching, an important issue is to mutually detect and determine the state of each operation between the host and virtual host. In order to solve this problem, according to the working characteristics of IPC filling, the weighing and filling machine has set up a main status timer and a cycle register in the software design. The main status timer is started and continues to work by the virtual master command. It can only be swabbed to place a cycle command. The operational status of the mainframe 3360 is determined from the contents of the cycle register and the status timer value. If a life cycle command is not received within an integer multiple of the life cycle, a primary failure is determined. The virtual host takes over recipe control and continues recipe control operations over the serial bus n each system.
The method of recovering recipe control after the liquid filling scale host returns to normal is also an issue that needs to be addressed. When the host is normal, it continues to send batch cycle commands to each slave server. After receiving the command, the virtual host first sends a scrap message to each slave server, and then the surrendered recipe control. After the host resumes recipe control, on the one hand, the recipe control lubricant formula continues to run, and on the other hand, the original data is supplemented, allowing uninterrupted switching of the lubricant formula recipe control, thus ensuring data continuity.
The liquid filling device accumulates the maximum or minimum gray level of each pixel in the odd and even frame images, respectively, based on obtaining a plurality of sequential images, filling the bucket with liquid, then subtracts the static background using a difference algorithm, and finally performs a threshold segmentation to determine the presence or absence of liquid impurities. The method does a good job of segmenting a moving object in a liquid and then detecting continuity and sloshing of the object to determine if it is a liquid impurity. However, the method does not directly distinguish between bubbles and impurities, and reduces the generation of bubbles primarily through mechanical design. As a result, the generation of bubbles can lead to erroneous judgments.
Some liquid impurities may be located at the bottom of the bucket when at rest, making it difficult to charge these impurities. It is necessary to move the liquid in the bucket, and the impurities leave the bottom of the bucket and move with the liquid, so that the presence of impurities can be observed more clearly. Also, the impurities contained in the liquid and the traces of the bed have the same characteristics in a single image and cannot be distinguished. A continuous sequence of images can be obtained when the bucket is at rest and the liquid in the bucket is moving. The traces of the bucket and the impurities in the liquid are identified by analyzing the motion of multiple frames in the sequence.
Specially designed filling machines have been used for this purpose. The filling equipment uses a filling machine capable of stopping the rotation of the injection drum at high speed and then taking a continuous sequence of images together with a mirror and a video camera without perspective deviation. First, the mechanism accelerates the rotation of the filling drum into the rotating area, the acceleration stops when the drum wants to go beyond the rotating area, and the drum rotates freely (reducing vibration-induced air bubbles). After the "bucket" has fully entered the emergency stop zone, the photodetector formula controls the filling machine that stops the bucket, and the liquid in the bucket continues to rotate due to inertia. At this point, the camera began to "through the mirror" infusion bucket of a continuous sequence of mirrors, in order to track and capture the sequence of images of the infusion bucket.
4 Conclusion
The industrial filling machine based on the virtual host system has been used normally in the production site of lubricant formulations, and has improved the reliability of the automatic filling machine without increasing the cost of hardware. It has a wide range of application prospects.